Scaling battery manufacturing sustainably
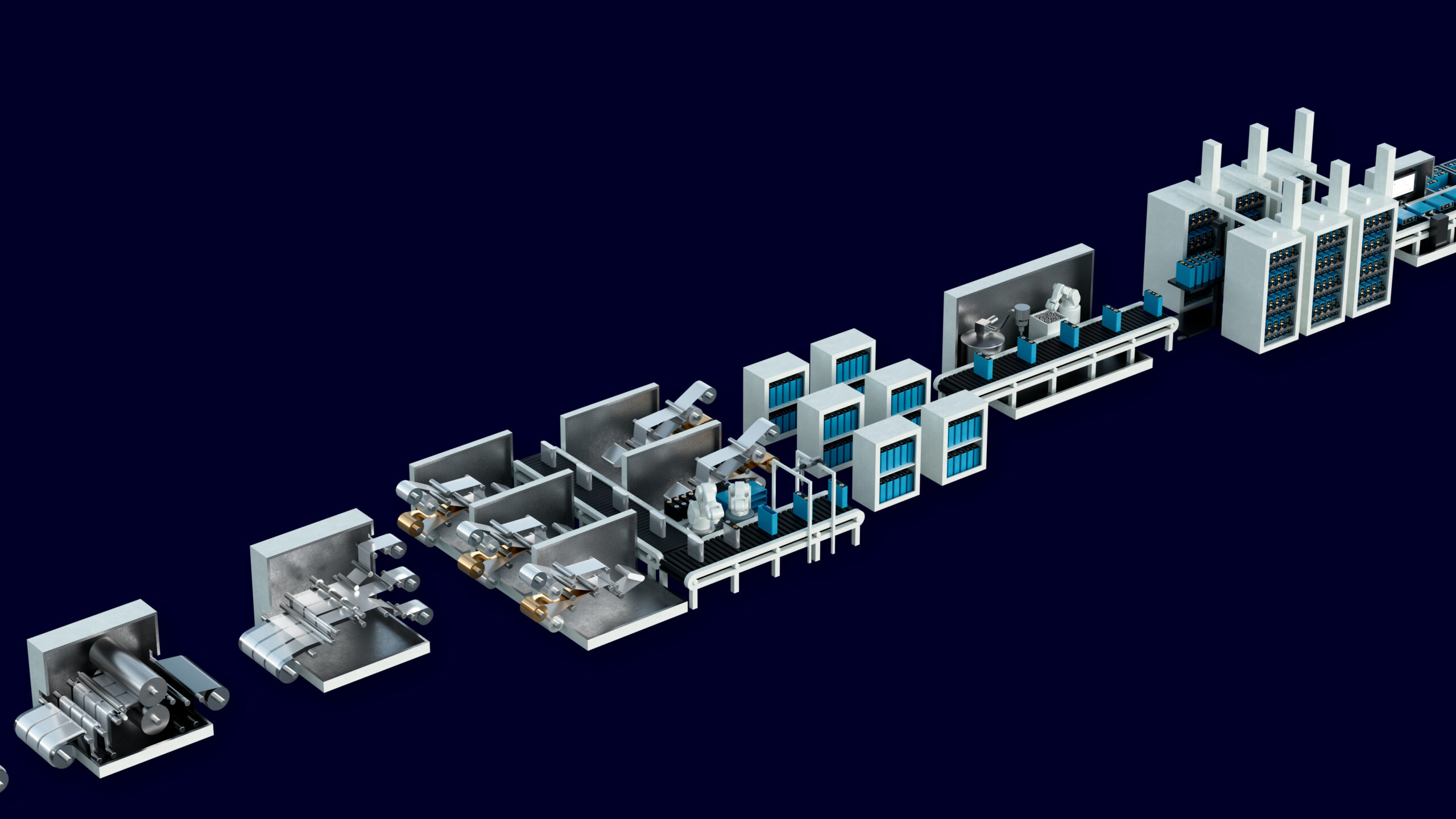
Many markets and industries around the world are marching towards sustainability. Some to become market leaders, more to meet growing regulatory demands, and others still looking at the profit potential of more sustainable operations. In almost all cases that means adopting further electrification to manufacturing and operations. The challenge arises that many industries require mobility and cannot rely on simply plugging into the electrical grid. And even those that can need to contend with the increased load and renewable energy generation patterns – often called the duck curve to grid operators.
But for both of these instances, designer, engineers, manufacturers, and whole enterprises are looking to batteries for there solutions. And meeting this demand has accelerated the field quite rapidly and next steps need to be in motion today to keep the momentum going for the increasing growth the industry expects.
As part of The Battery Podcast from Siemens Digital Industries, our resident host Marc Deyda took some time on the showfloor at Battery Show Europe to talk with experts in the field – Dr. Christian Offermanns (Chair of Production Engineering of E-Mobility Components at RWTH Aachen University),
Dr. Markus Gräf (Chief Operations Officer at Cellforce Group GmbH), and Dr. Hannes Schmüser (CEO Division Clean Technology Systems at Dürr). To listen to the full conversation, hit the play button below, but you can continue reading to just get the highlights.
Listen to the full episode on Siemens.fm
When planning a production site, Dr. Offermanns explained that “you have to have in mind what are the costs in the end, so OpEx as well as CapEx.” And a major example of this for battery manufacturing “is to reduce the energy that you need to produce the batteries.” Energy consumption is a massive driver of costs and carbon emissions in the manufacturing process, during the drying process and during formation. Understanding the impact of these processes on energy consumption is critical in reducing costs and scaling production.
In addition to optimizations on the factory floor, scaling the battery industry requires continued partnership with research institutions, factories, and suppliers. Whether it is pilot lines or something else, “you have to transfer that [innovation] to the industry” – Dr. Offermanns. The fundamental research often being funded with government help needs to be progressed in industrial environments to ever make it to deployment at scale.
Dr. Schmüser readily agreed to the role of innovation for a successful battery industry, and stating that businesses have to “innovate in terms of finding the right customer benefits.” At Dürr, they are working on laser drying to reduce the energy consumption of the process as well as closed loop controls to track, analyze, and optimize the coating quality during production. Elaborating, “we can detect failures, we generate all the data based on camera system and sensors, put an artificial intelligence system on top of it in order to detect and identify the right failure [locations and modes].”
Quality and yield rates are an important area of growth for the industry in the years to come, in terms of sustainability and profitability, “because raw materials are extremely expensive” concluded Dr. Schmüser. When the cost of your materials is a large part of overall costs, there is a huge incentive to minimize waste and find sustainable supply networks for them – which is why circularity will be so important into the future. Circularity will improve the environmental friendliness of batteries while making the business more profitable in the long-term.
Marc’s last guest, Dr. Gräf continued the thread of quality and resource preservation, but took a more predictive look with how to detect faults before investing the long lead times into cell manufacture. After coating, cell formation takes a week and a half. Waiting that long for a cell that could be determined faulty beforehand is a big hit to OpEx, it is almost like throwing money in the bin. Dr. Gräf explained, “the collaboration we are doing here with Dürr and Siemens, [is] how to [really] get the coating process more stable and more predictable with less waste.”
For more details on what these guests are dealing with as there innovate in the battery field, I would highly recommend listening to the complete episode above. But for more information on how Siemens is partnering with companies across the industry, check out our website siemens.com/battery.
Siemens Digital Industries (DI) is a leading innovator in automation and digitalization. In close cooperation with its partners and customers, DI is the driving force for the digital transformation in the process and manufacturing industries. With its Digital Enterprise portfolio, Siemens provides companies of all sizes with all the necessary products, along with consistent solutions and services for the integration and digitalization of the entire value chain. Optimized for the specific requirements of individual industries, this unique portfolio enables customers to enhance their productivity and flexibility. DI continuously extends its portfolio to include innovations and the integration of future-oriented technologies. Siemens Digital Industries, with its headquarters in Nuremberg, has a workforce of around 72,000 people worldwide.
For more information on Siemens Digital Industries products and services, follow us on LinkedIn, Facebook, Twitter, and YouTube.