The power of simulation to AV design and development – Transcript
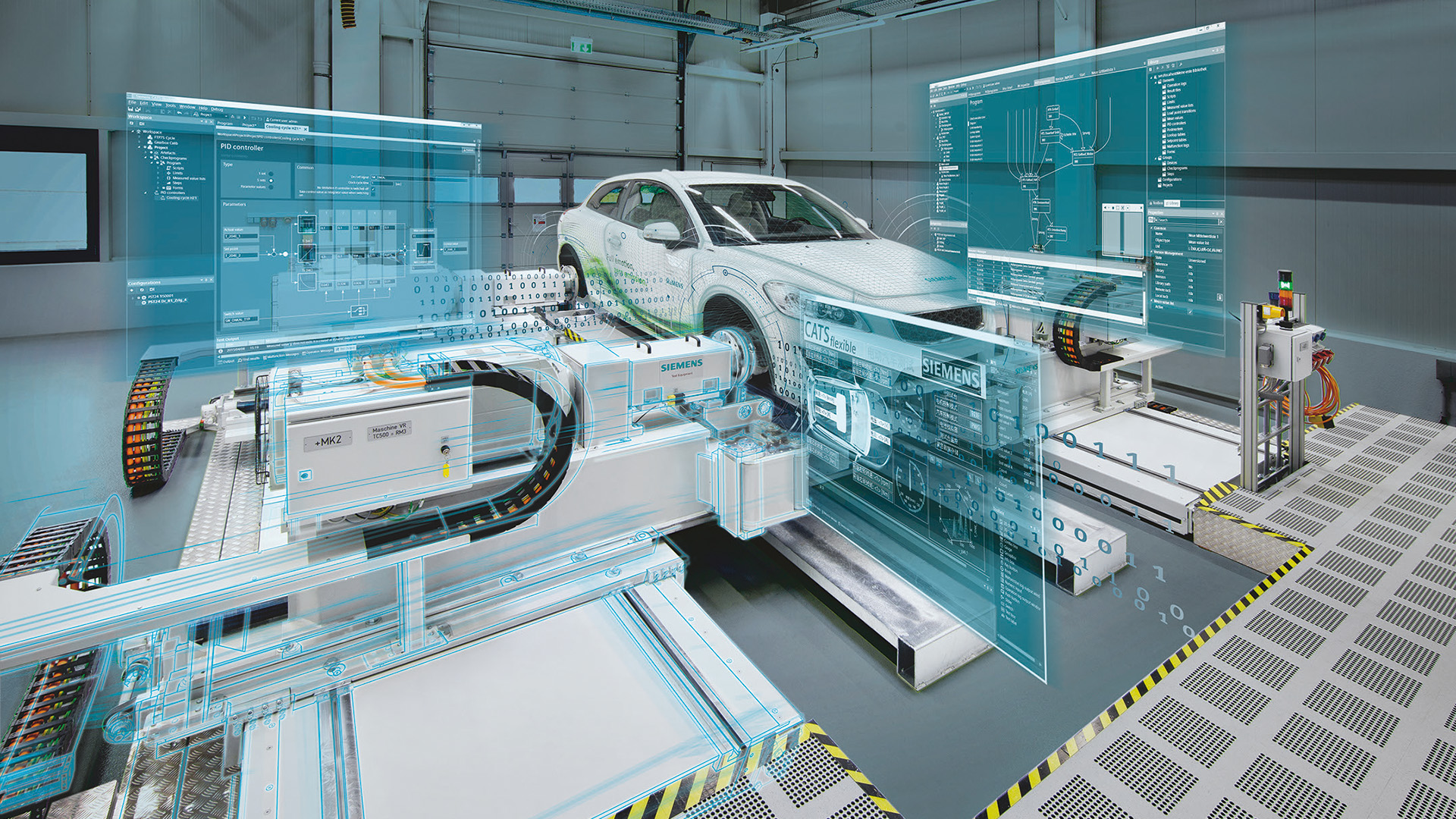
In this episode of the Future Car Podcast, Nand Kochhar, VP of Automotive and Transportation Industries, and I, Conor Peick, Thought Leadership team writer, continue a series of conversations on autonomous vehicles and how they will shape the future of mobility.
As the automotive industry moves into the future, automotive companies are faced with the challenge of designing increasingly complex vehicles to satisfy consumer demands for greater automation, convenience and connectivity—and AVs are only expected to exacerbate this trend of growing vehicle complexity. To dive into the topic of vehicle simulation and testing, Nand and I are joined by Robbert Lohmann, Business Development Director of AVs at Siemens Digital Industries Software.
Conor Peick: In this episode of the Future Car podcast, Nan Kochhar, VP of Automotive and Transportation Industries, and I Connor Pike, a thought leadership team writer, continue with series of conversations on autonomous vehicles and how they will shape the future of mobility. As the automotive industry moves into the future, automotive companies are faced with the challenge of designing increasingly complex vehicles to satisfy consumer demands for greater automation, convenience, and connectivity.
AVs are only expected to exacerbate this trend of growing vehicle complexity. This complexity becomes particularly challenging as the lifecycle moves into the verification and validation phase. How do companies test and ensure that autonomous vehicles are safe and effective?
To discuss the vehicle simulation and testing, Nand and I are joined by Robbert Lohmann, Business Development director of AVs at Siemens Digital Industries Software. So welcome, Robbert, and thanks for joining Nand and I today. We’re really excited to have you on. Just to get started. I’m hoping you can give us and the listeners a brief summary of your experience with simulation and autonomous vehicles and ADAS systems.
Robbert Lohmann: Thanks for having me today. My history with autonomous vehicles goes back to I guess 1999 when I started at a company called Frog doing automated guided vehicles in factories. That quickly became the same technology applied for automated vehicles outdoors and where we thought that time, they were called automated people movers. People in that industry were looking at us very oddly because they said, “what you’re doing is not a people mover because that’s guided by some form of rail.” And it was only until the Society of Automotive Engineers came with levels 1 through 5 that people all of a sudden said you’re a level 4 autonomous vehicle. So that’s where my history is at.
It became a separate company called 2getthere in 2007. We went with 2 founders of the company to ultimately 70 people, multiple vehicles deployed in multiple projects around the world, and selling the company to ZF. And at that time, I decided I was ready for a new challenge. I came to Siemens to apply everything I had learned in deploying these types of vehicles in projects around the world into tools that could assist other companies in doing exactly the same thing.
Conor Peick: Excellent. Nand, to kick off our discussion today it seems that virtual methods of vehicle testing and verification by way of simulation have really grown in usage in recent years in the auto industry. So, I’m curious from your perspective, what is driving this growth and what implication will it have on the verification and validation process for an autonomous vehicle?
Nand Kochhar: Thank you Conor, for having me back on the podcast. As you know, there’s tremendous innovation going on in the automotive and transportation industry and one of the key drivers is the cycle time reduction for end-to-end and the virtual methods of doing product development and verification and testing is really the only game in town in my mind from the perspective of continuing to shrink the timing as well as reducing the cost it takes and to improve the quality.
Now, having said that, to answer your question, there are several factors of that simulation. So today simulation is enabled by all the computing technologies available and the type of simulation and the type of physics, which can be solved and continues to increase the accuracy of that. I think those are some of the reasons the usage of simulation has become real because all you need now is a physical testing for correlation purposes.
Then you can leverage the simulation technologies to make real decisions, whether it’s a product decision or manufacturing decisions in light of the digital twin of the of the product in the manufacturing. Now when it comes to implication on verification validation process for AV. As you know, to certify autonomous vehicle or a dash feature on a vehicle, you would need millions of miles of physical testing, which we know is not possible from a timing perspective. Also, some of the scenarios can’t be produced in a physical testing environment. So, simulation plays the most important role because now you can create those scenarios and validate some of the things which are not even possible. You can also create different variations of those scenarios and that’s why it does become critical especially in the ADAS features of the AV development.
Robbert Lohmann: I agree completely. I can echo the sentiment about millions of kilometers that you need to drive. The crucial part there becomes that if at some point you encounter a scenario that the software can’t handle and you may need to make changes to what you’ve set up, that you need to start at zero again with the driving of the 1,000,000 kilometers.
So, whether it’s a million miles or kilometers, miles are even worse than kilometers, right? But then it means that if you do virtual testing and you’re able to avoid running into a scenario which you couldn’t have anticipated that you would encounter in the testing on public roads, that you’re actually able to get through that process much quicker. So, the virtual testing and actual testing go hand in hand, and you can see one separate from the other.
Nand Kochhar: Can you talk about where the virtual scenarios that drive these simulations come from? It’s fascinating for me to experience these things now. How are those created and how do you ensure that these scenarios are representative of the real world? Is artificial intelligence involved in these processes today?
Robbert Lohmann: That’s one way to approach it, right? But even if you use artificial intelligence to generate scenarios, it’s to a degree, still limited by the imagination of the engineers that designed the software that allows for these scenarios to be created. I think that as human beings, we have one unique ability and that’s our creativity and the creativity sometimes mean that when we’re driving down the road, we do something that is very smart and avoids an accident. And in other circumstances, the creativity also leads us to do something very stupid and, causes a situation on the roads that you’ve never seen before, and I think anybody that’s ever driven a car may see something on the road that they haven’t seen before. I think that’s the main difficulty when you’re trying to roll out these systems to the world is that the likelihood of you encountering a scenario that you haven’t seen before is very large.
If you deploy it over a whole fleet and it’s very small, if it’s just on a single vehicle running around one particular town on a typical section of streets. So, trying to solve that puzzle is one of the main challenges of the industry, and there’s different thoughts about how to go about it. Whether it’s synthetic, whether it’s using AI, whether it’s through massive data recording with all the vehicles that are deployed on the road. But yeah, the industry creates all the data because the data is ultimately what is going to drive the development.
Conor Peick: On a similar front, how do you think the development of industry standards will play into the future of virtual vehicle testing and simulation technology? Does that have a role to play in like scenario generation or those things?
Nand Kochhar: Yeah. In fact, the industry standards will play a very important role because, as you know, at the end of the day, vehicles need to be certified. If we are talking about ADAS features or autonomous vehicles, there needs to be subset standards since we have a vast variety of producers. Of these features all over the globe. Now the standards will help streamline, consistency and acceptance of the vehicle certification based on the virtual methods versus a having to run the physical testing all the time.
So, I can speak from my safety experience that standards play an important role when they’re initially developing and maturing. For example, if you look at the crash safety today, North America has developed all over the globe, euro and cap those standards were developed for certification with the level of maturity building confidence in those.
So today there’s very few things you can take all the way into certification in the safety arena purely on the simulation methods, but that’s where you have to continue to evolve to prove the correlation between the physical testing and the virtual testing, let the authorities who have to approve of those standards, and then ultimately get to it. Pure virtual testing environment, which we also call all the way up to a virtual homologation that the authorities all over the globe can stick to those standards so that plays very important role. I think Robbert touched on bringing the physical and virtual data together over a period of time, you grow that correlation, and you rely on the virtual analysis more and more.
Robbert Lohmann: To add to that, if you look at all the research that has been done into when autonomous vehicles will be deployed in a large scale and whether it’s autonomous vehicles or ADAS features and there’s three pillars that are crucially important to them being introduced successfully: public acceptance, the technology itself, and the regulations. In the automotive industry you sometimes still see a little bit of tension between technology and regulations with the people that are producing the technology saying that the, the regular regulatory framework is not in place yet and at the same time, seeing the regulations that there is the technology perhaps not being able to completely comply with it yet.
So, it’s still a challenging task or a challenging target to accomplish and you notice a little bit of tension and I think older industries where you look at rail and air aviation, there’s less tension between regulations and technology because there’s no competition on safety. And when it comes to ADAS and AV’s, it feels like these features are distinguishing marks that could be purchasing reasons for customers for a certain brand of automobile. So there still is a little bit more attention to what you don’t want is that tension to become so high that you break the relationship between technology and regulations and both of them break the relationship with public acceptance because it means that inevitably the introduction to the market will be delayed.
The standards should help balance out the tension that there is between technology and regulations, and those standards play a guiding role for companies like Siemens that are developing tools to accommodate processes within the developers that ensure that the standards are in alignment with the technology that they’re developing and the other way around. So yeah, I think standards are perhaps even driving the speed with which we will see all these technologies coming to the road.
Conor Peick: Fascinating. Well, so then let’s assume that you have a robust set of scenarios that you’re going to use to test your vehicle design and I think the next step is how can companies take those scenarios and represent their vehicle in a virtual environment with sufficient detail to test, and verify, and validate the vehicle.
Nand Kochhar: Yeah, I’ll start with that. Good question. Today, companies are doing virtual vehicle development. Let’s say a vehicle dynamics model which is built up on elements of the physical vehicle or the design part of it, and then combine that with the software and the controls for running the vehicle dynamics of that vehicle. Now, when you have created a scenario model as you mentioned, now you need to integrate these two things. The detailed vehicle models playing in that scenario models and you will be running these virtual vehicles in those scenarios, obviously to increase you have to continue to increase the fidelity of these models based on what scenarios you are playing. For example, for autonomous vehicles you must do the lane merging feature part of it.
That’s a combination of your steering operations and the handling operations of the vehicle being played in a scenario which you have generated, let’s say the coming off ramp from a freeway and then merging into the traffic, and obviously, the critical part there is also creating those critical scenarios. What we call unknown, unsafe scenarios through the virtual simulations in bringing these two things, the vehicle models and the scenario models together to make the final assessment that whether it’s a safe operation or not. So, I think this is how these two things will come together. These two environments will come together to give the ultimate certification or validity of the operations of the vehicle.
Robbert Lohmann: In addition to that, it also depends on the intent of the simulation. So, there’s different things that you can use the simulation for. A sufficient detail depends on whether you’re validating sensory systems or whether you’re verifying path. For the latter, which is think if you will, the accuracy is less relevant as you are assuming that your sensor and sensory systems are working perfectly and this is very achievable today when you are looking at validation of the perception algorithm, it’s much more difficult. That’s the sense part. Fist-based sensors also in simulation with validation of the measurements are essential to make sure that there’s a good correlation between what you’re seeing in the real world and what you’re seeing in your simulation program.
That’s why we also do test to see that what we’re trying to replicate in the physics-based environment matches with the real-world measurements. This is increasingly complex, but eventually you have to be able to do that to also do the physics-based sensors validation in a simulated environment. It’s not as easy as perhaps verifying the path planning, and for sensing simulation we’ll be supporting the real-world testing for the path planning.
Conor Peick: Robbert and Nand, thank you guys so much for your time today. As we’re wrapping up, I want to give you guys a chance to share any final thoughts or takeaways you’d like to listener to leave this episode with.
Robbert Lohmann: Well, thanks for having us and thanks for the interesting discussion. And one aspect that we perhaps touched on a little, but we didn’t go into a lot of detail, but if there are people listening that are interested in more about the unknown unsafe scenarios towards which Nand mentioned, I think the methodology that Siemens now has which is patent that has a lot of promise towards the future and actually discovering these unknown unsafe scenarios and making sure that in the real-life deployments that developers are doing, they’re less likely to run into an unknown unsafe scenario that they weren’t expecting, making that testing a lot easier. I would recommend anybody listening in to reach out, find out more about critical scenario creation, because I believe that what it’s bringing to the market is truly unique.
Nand Kochhar: Yeah, I’ll add to that. I think Conor, from my perspective, simulation is the only way going forward for the companies to continue to innovate because when we are offering these advanced features and functions and autonomy in the vehicle, there’s many scenarios to be delivered from a business perspective in a wake of the woman.
So the speed at which we can leverage simulation do play those business cases is absolutely the only way in my mind, of delivering innovations on an ongoing basis. Now, having said that, of course it is equally important when you bring any new features, it needs to be proven with correlation, and that’s where the physical testing and the real-world comes together. And as Robbert mentioned, we are in a unique position from Siemens, bringing real and virtual together. The build confidence in the eight Dash features development as well as the full autonomy delivery, whether it’s automated guided vehicles in the factories Robbert talked about in the in the beginning or the timeless vehicles. So that’s critical, and we are in a good position to move the industry in that direction. Thank you for your time.
Conor Peick: I’d like to thank the listeners for tuning in once again to the Future Car podcast. We hope that you’ll come back and hang out with us soon.
Siemens Digital Industries Software helps organizations of all sizes digitally transform using software, hardware and services from the Siemens Xcelerator business platform. Siemens’ software and the comprehensive digital twin enable companies to optimize their design, engineering and manufacturing processes to turn today’s ideas into the sustainable products of the future. From chips to entire systems, from product to process, across all industries. Siemens Digital Industries Software – Accelerating transformation.