Smart Manufacturing and OT/IT convergence drive optimum utilization
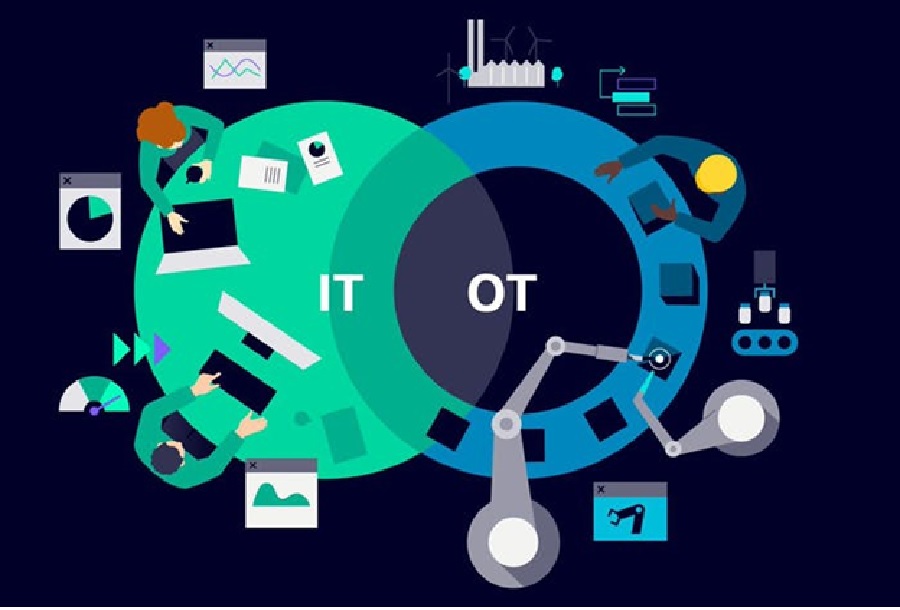
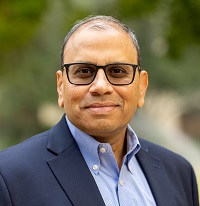
In a Machine Design article by Rahul Garg, VP for Industrial Machinery & SMB Programs at Siemens Digital Industries Software, he addresses how smart manufacturing enables industrial companies to tackle the challenges associated with global competition, sustainability, supply chain mishaps and labor shortages.
The objective is efficiency – driving optimum factory utilization. Digitalization is the equalizer to achieving innovative levels of smart manufacturing. Previously, automation was used to reduce costs; however, now digitalization takes the manufacturing process to a new level.
“The foundation for achieving higher operation efficiencies is the convergence of OT and IT to uncover actionable insights,” says Rahul. “Using the wealth of data generated by factory operations technology (OT) from edge sensors and smart equipment, information technology (IT) can then store, retrieve, process, analyze and recommend action based on that digital data.”
And this data leads to a closed-loop manufacturing process that is continually optimized via closed-loop product quality, thus supporting a comprehensive digital twin of the manufacturing environment to maximize throughput.
IT/OT provides new information
IT/OT convergence is essential for reaching smart manufacturing. Operation technology (OT) helps run a factory. This includes software for the physical equipment, the technology driving machines, and the programmable logic controllers (PLCs). Information technology (IT) is the computer information technology it stores, processes, and analyzes – responding to this data from operations. In turn, this data helps make decisions while operation technology drives actions.
Most factories are a combination of both older and newer equipment. Newer smart machines can share data with a network, while older machines are silos of data.
“A network of sensors is added to the factory to connect those islands to ensure robust data across all manufacturing operations, bringing operational data together for IT to analyze. These edge sensors can stream data to an entire range of measurements to provide a solid sense of the equipment’s performance. As a result, in almost every factory today, data is collected by various physical sensing technologies, including PLCs, sensors and gauges, and IoT devices,” says Garg.
IT/OT is the foundation for implementing a robust digital twin
Currently, OT and IT are interacting to provide exceptional operational efficiencies, whereas, in the past, they were two distinct areas. However, the search for greater operational productivity joins the boundaries between information management in server rooms, office buildings and operations management in the factory to provide necessary data to improve processes.
“OT and IT converge when information technology is captured as the factory floor is running, fed into IT systems that digitally optimize business decisions, looking at this data from edge sensors in smart machines,” says Rahul.
Now it is easier to comprehend the equipment runs to make real-time decisions that further optimize and maximize throughput from factories. Cohesively, they help make essential decisions, uncovering a particular machine part that may be failing, running out of stock, or having issues that impede factory production.
Learn more in Rahul’s article.
Siemens Digital Industries Software helps organizations of all sizes digitally transform using software, hardware and services from the Siemens Xcelerator business platform. Siemens’ software and the comprehensive digital twin enable companies to optimize their design, engineering and manufacturing processes to turn today’s ideas into the sustainable products of the future. From chips to entire systems, from product to process, across all industries. Siemens Digital Industries Software – Accelerating transformation.
Rahul Garg is the vice president for Industrial Machinery & SMB Programs at Siemens Digital Industries Software, responsible for defining and delivering key strategic initiatives and solutions, and global business development. More information on Siemens Xcelerator, a comprehensive and integrated portfolio of software and services that can help companies realize digital twins, can be found here.