Sustainability and the digital twin energy resource impact – Transcript
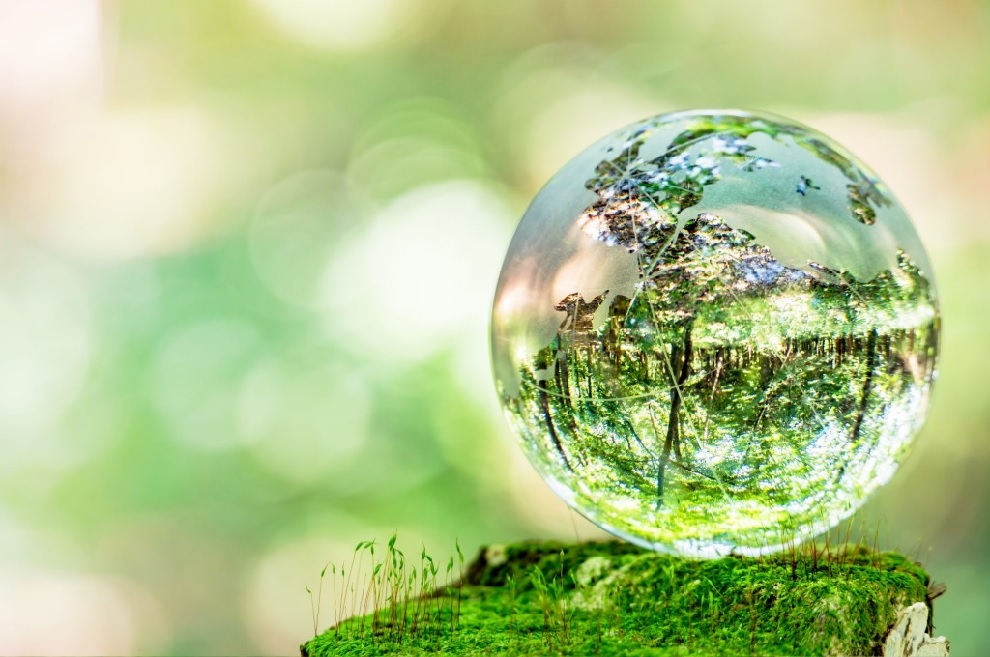
Below is my continuing conversation with Eryn Devola, Head of Sustainability at Siemens Digital Industries Software, and Rahul Garg, VP Industrial Machinery and SMB Business Program at Siemens Digital Industries Software, about the impact of sustainability on the industrial machinery industry in part 4 of our podcast series. Check out the podcast here, or read the full transcript.
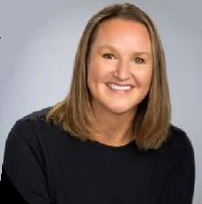
Read the transcript
Blake: Welcome to our fourth podcast in the Sustainability series, and the second half of our conversation with our special guests Eryn Devola and Rahul Garg. Eryn is Head of Sustainability at Siemens Digital Industries Software. Eryn is a mechanical engineer by training and has spent the last 20 plus years working in the industry. Rahul Garg’s background is in electrical computer engineering, being involved with the design and development of software and other activities for the last 20 to 30 years. So, welcome to you both. When we left off in our previous podcast, we were discussing machine design and sustainability, so let’s continue with that theme.
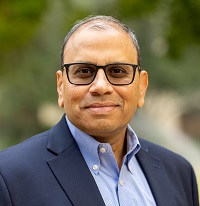
When we look at machine operation and sustainability, what is the impact that it’s having on factories and machines today?
Rahul: Yeah, you know that’s a very important thing. There’s one interesting statistic I have read somewhere which goes to the fact of a one percent reduction in the industrial carbon footprint or production. That could mean 70 million tons of less CO2 emissions per year. And so that impact is huge, right?
And all that impact can be driven by making the machines more efficient in terms of how they are using energy and the CO2 impact that they can have.
So, to me the machine operation is significant for the overall drive for sustainability for our planet.
Eryn: And I think one of the ways that we’re able to help better manage that is getting the IT/OT convergence to control and predict what’s going on in your production floor and then manage the energy use of your equipment or optimize based on looking at minimizing, for example, startups and shutdowns, looking at making sure that we don’t have a line that’s going down for our material problem because then we get the best conversion of those resources.
In durable products along the way, it’s using that intelligence we’re collecting by running the machinery, understanding what the use profiles are, understanding what the energy profiles are, and then optimizing them along the way. This is a clear way that we’re able to drive sustainability through industrial machinery.
Rahul: Yes, and I think along with the carbon footprint, I would imagine, Eryn, the whole recyclability of waste has a significant impact as well.
Especially when you start thinking of resources that are used in the production of whatever that machine is trying to do, plus what’s used in terms of trying to run the machine and trying to cool the machine trying to cool the parts that you’re trying to machine itself.
So all those things have a significant impact on the overall sustainability impacts of how the production is running.
Eryn: Part of this is where we use 1.7 of earth’s worth of natural resources per year. Overall, we would need to decrease that by 59 percent to get to the point where the Earth can renew the resources that we’re currently taking from it. And the challenge with that is we can’t just look at CO2, which is extraordinarily important. But we have a lot of other considerations. Water, for example, is one of those that fall right behind there.
In looking at how we can maybe recapture some of the things that we waste, heat is a huge waste in some places where we generate a lot of heat, we don’t have a way to turn that heat into energy and a way to then reuse that for another purpose.
And I think that those are the circularity models. We’re industrial machinery, and it could really play a big role in solving some of those problems.
Rahul: Yes, that’s a good point. I think the whole energy resource efficiency is going to have a big impact in terms of how we are all impacting the planet.
Blake: Yeah, very interesting statistics there. When we’re looking at machine design, how would we perform machine design for overall sustainability?
Rahul: Yeah, this is right up our wheelhouse. You know when I go back a bit, from a design perspective, most companies were trying to see how to improve the overall performance of the machine. But how do you change the throughput so you can maximize the utilization of how the machine is getting used? You got to play a balancing act to maximize it. Plus, how do you optimize it for sustainability as well?
These two factors must be put into a balancing scale, to make sure that you are doing the right things and that’s where you use digital twins to simulate hundreds of different variations. So, this becomes critical to help ensure that you’re making the right choices in terms of creating the designs.
This process pertains to the materials you’re using, ensuring that you optimize them for water, energy efficiency, and waste and placing sensors on the machines to deliver optimum data metrics.
It’s important to design the machine for end of life recycling disassembly.
How do you change parts in there? How do you optimize it for?
So, these are all important things that have to be thought through and I really think there is no other way to do that process without leveraging a comprehensive digital technology and a complete digitalization solution that can bring all these things together better because you cannot try and optimize one part. You must optimize for all these variables together.
It becomes a multi-part variable equation that you must solve, and the only way to do that is by leveraging digitalization technologies right up front during the design process.
Blake: So, when you’re looking at all these variables of optimizing for sustainability, how do you ensure peak machine performance is sustainable?
Rahul: So, first, go back to the whole design process, there was another statistic of 80 percent of all products related to environmental impacts are determined during the product design phase.
So if 80 percent of the performance and environmental impacts are all going to be determined at the product design phase, you have to obviously make sure that you are trying to optimize that whole process to the maximum. To help you optimize the process you optimize your performance, and to help you optimize your sustainability requirements.
There are various technologies that are available. One of them is around the whole concept of virtual commissioning, which allows you to bring all of the capabilities in a virtual format without actually having to build or construct even a single part.
And if something goes wrong, you’re in the virtual world, so you can start from scratch again and it makes it very easy to bring in and take advantage of the benefits of a digital twin, leveraging a digital twin, reducing your times and cost, making use of a digital twin to test out all of the different operations, optimizing operations, making production more flexible and predictive.
So all that can be done using virtual commissioning and digital twins. It will help you understand even the carbon impact, so it’s very much possible. You are not merely optimizing it for peak performance, but understanding the sustainability impact, and the carbon impact of how that machine will be running.
I don’t know if you have any thoughts to comment on that, Eryn. Anything else to add in there?
Eryn: Yes, I think one of the big shifts is that peak machine performance in the future will include its impact on the environment. So, Rahul, you hit on this earlier that you know these factors – there are numbers of variables that you need to solve and need to optimize for continue to grow.
And I think that that’s a big part of it. The other part of it is don’t make these design jobs any easier, but look at that over time and the entire lifetime of the product, which is one of the big things that I think will continue to be something that we will work to solve, getting not just the virtual commissioning, but virtual maintenance and being able to repair or upgrade the equipment.
I’m with as little human interaction as possible, and we talked to some customers attempting to run dark factories. This is one of their biggest concerns as how do I maintain the equipment moving forward? And I think that is a solution or problem that we still need to drive through to solve.
Rahul: Ok, Eryn, since we are talking about multiple equations and variables, even on the topic of sustainability, it is not merely one variable by itself? That’s another multipart equation – all the way from water usage radiations, and all these things are another set of variables that need to be solved under the topic of sustainability. And I would imagine there’s probably many more.
Eryn: I know you mentioned at the beginning of this podcast that one of the biggest pieces of legislation in the broadest sense is the corporate Sustainability Reporting Directive coming out of the EU, with effectivity as a requirement for reporting in fiscal 2025.
So that is not very far away, and that requires entities that either manufacture or sell in the EU to report 400 different environmental related KPIs. So, to your point, it’s not just a couple of things. What this does is push legislation, which gives us the transparency we need to be able to give the information into these design processes, whereas you mentioned so many of those impacts can be minimized and understood.
So yeah, one of the things around sustainability is the truth of the technology. We need it available, and I think we’re getting to see the tipping point where people are really putting a priority on applying that wonderful technology and solving problems. The other things you mentioned is that governments aren’t only writing legislation, they’re also providing incentives in funding to help solve some of these problems. Therefore, we’ve got some motivation, some funding, and we have the technology and the industry. We also have the momentum and the size to really make a big difference.
So, as depressing as it sometimes feels, I think there’s so much opportunity. If we talk again in six months, we’re going to see that this is really moving along and furthering our ability to positively impact the environment.
Blake: Those are great points, Eryn and Rahul. Unfortunately, we are out of time for this episode, but we will pick up on this compelling conversation in the last part of our conversation with Eryn Devola and Rahul Garg, continuing to discuss the impact of sustainability in the industrial machinery industry. We hope you can join us. Bye for now.
Siemens Digital Industries Software helps organizations of all sizes digitally transform using software, hardware and services from the Siemens Xcelerator business platform. Siemens’ software and the comprehensive digital twin enable companies to optimize their design, engineering and manufacturing processes to turn today’s ideas into the sustainable products of the future. From chips to entire systems, from product to process, across all industries. Siemens Digital Industries Software – Accelerating transformation.