Additive manufacturing reduces complexity in A&D
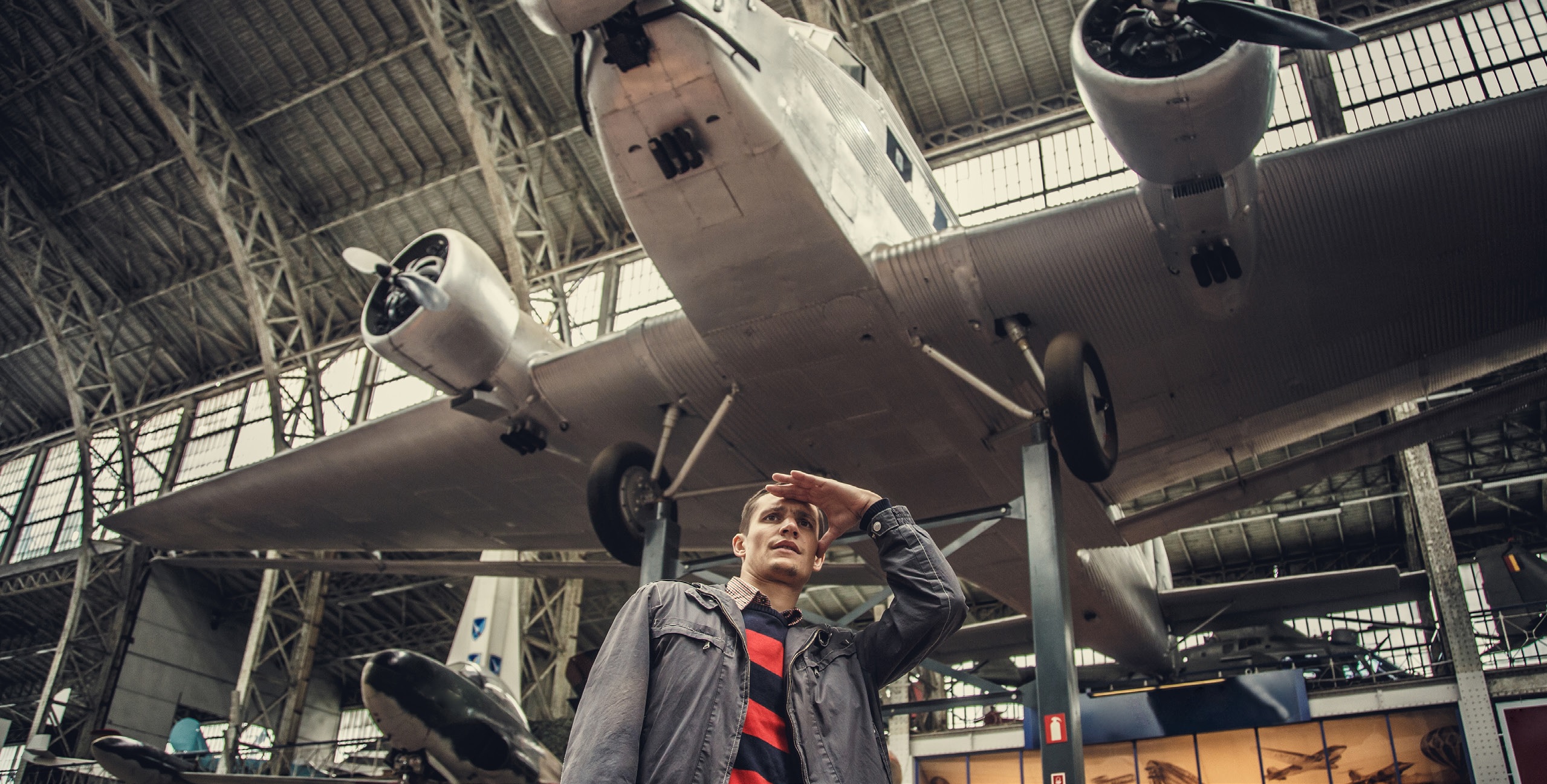
The aerospace and defense (A&D) industry was one of the earliest adopters of additive manufacturing (AM) technology, with companies using it as far back as the 1990s to print nonstructural components. Its use has been steadily increasing throughout A&D companies, and it is easy to see why. AM offers many advantages that conventional manufacturing methods lack, including reduced manufacturing costs at low volumes, highly functional part optimizations, and a much faster time-to-market. While there are barriers to its adoption, those challenges can be broken down with the assistance of the digital twin.
Reducing costs and adding functionality
One of the clearest benefits of using AM is the reduction material waste. With conventional manufacturing methods, parts are often made by removing portions of material in a machining operation, resulting in scrap that must be disposed of properly. Not only does this have a financial cost, but it can also impact the environmental sustainability of production. Alternatively, molds are created to shape material, but those molds also have a cost in capital and resources. With AM, however, parts are made by adding material without the assistance of molds, resulting in little to no scrap and few extra costs for extraneous materials. With AM, the manufacturing process can be cheaper without sacrificing the quality of the product.
The optimization of parts and components printed with AM is another great advantage of the technology. AM has introduced new ways to manufacture parts that allow engineers to get the most functionality from components while using minimal amounts of material. By adding material instead of subtracting material, engineers can more readily create complex structures that would be exceedingly difficult using conventional manufacturing methods. Parts made with AM can fulfill the same functions as those made conventionally while weighing significantly less. This is a boon for aerospace considering weight reductions are highly beneficial for any product. When manufactured, these optimized parts made with AM combine to form a stronger, more efficient whole.
Lastly, AM accelerates the time-to-market and overall innovation. Creating parts additively takes much less time than conventional manufacturing methods at low volumes, so they can be released much sooner. Not only does this get new products in the air faster, but it also allows faster repairs in the field thanks to an increased availability of parts, thereby increasing the lifespan of aircraft. Innovation also speeds up thanks to this rapid deployment environment. It gives engineers more operational data quicker, allowing them to iterate on their designs and release those sooner as well. In short, AM has the potential to help optimize and innovate aerospace designs in record times.
Why the digital twin?
Of course, there are still barriers to the adoption of AM, most notably from a software perspective. Companies often use five to eight different products to enable a full AM workflow from initial computer-aided design (CAD) to finished product inspection. These products cannot transfer data between each other easily. Each additional step from design to assembly adds risk of failure, whether that is due to ease of transfer, a slight value change, or simply the added time of multiple steps. Discontinuity disrupts the workflow and prevents the rapid innovation that AM can provide at its full potential with a digital twin workflow.
Companies can construct a digital twin of their whole operation from their products to their production lines to create a single end-to-end virtual representation of their AM processes. Furthermore, using technologies like IoT sensors they can gather data from the physical versions of products to optimize their virtual counterparts. In turn, this data is used to optimize the physical versions further. That data can be accessed from the digital twin at any point in the product lifecycle without disrupting any stage of the process, allowing companies to leverage as much innovation as they can.
The benefits of additive manufacturing are many and can improve aerospace products across the product lifecycle. That said, if companies are not careful, their AM processes can be stymied by inefficient uses of disparate software tools. By utilizing digital technologies like the digital twin to create end-to-end processes, though, companies can navigate those traps and unleash the full potential of AM into their manufacturing processes.
To learn more about the role of additive manufacturing in A&D, check out this this white paper.
Siemens Digital Industries Software helps organizations of all sizes digitally transform using software, hardware and services from the Siemens Xcelerator business platform. Siemens’ software and the comprehensive digital twin enable companies to optimize their design, engineering and manufacturing processes to turn today’s ideas into the sustainable products of the future. From chips to entire systems, from product to process, across all industries. Siemens Digital Industries Software – Accelerating transformation.