Smart manufacturing addresses product complexity and sustainability
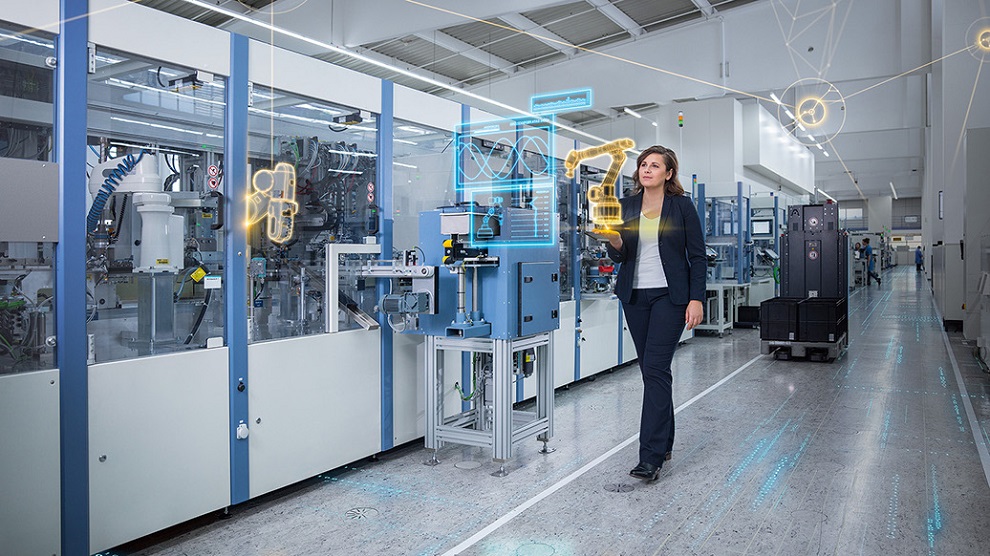
In a recent Industrial Machinery article, Rahul Garg discusses how manufacturers are looking for new ways to address many challenges, including product complexity, sustainability goals, and consumer demands for customization. In addition, there are looming issues with global competition, supply chain problems and labor shortages.
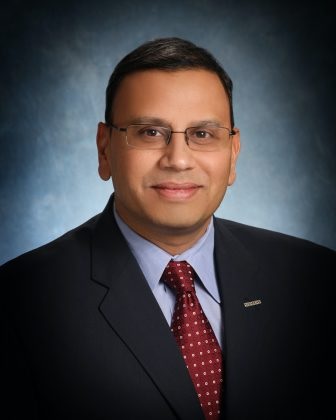
However, we are discovering that digitalization is a counterbalance to achieving a new smart manufacturing level. In the past, the focus of automation was on reducing costs. Today digitalization takes manufacturing processes to an entirely new level. Digitalization delivers improved data and more of it—vital to operational efficiencies of high availability, maximizing factory utilization, real-time management of supply chains, and improving time to market.
Digitalization supports three capabilities that lead to smart manufacturing.
- Information technology (IT) with operational technology (OT) convergence extracts and analyzes all the data generated during operations to uncover actionable insights.
- Closed-loop manufacturing and execution create and optimize the process and expedite customer orders.
- Closed-loop quality ensures products are delivered right the first time, regardless of the lot size.
IT/OT fusion delivers
OT/IT convergence is the first step to achieving smart manufacturing. OT governs the operation of the physical equipment, controls and technology driving the machines. Software instructs the machine and ensures that the hardware executes those instructions. IT is the organization’s computer technology that stores, retrieves, processes analyze and recommends action on data extracted during operations. Subsequently, IT helps management make decisions, and operation technology helps the factories drive actions.
Today’s factories are a combination of old and new equipment. New machines share data with a network; conversely, older machines are data islands. When network sensors are added to a factory, they connect those islands to guarantee healthy data across all manufacturing operations to provide operational data combined for IT analysis. Consequently, data is collected by various physical sensing technologies: programmable logic controllers (PLCs), sensors and gauges, IoT devices, and more.
OT/IT fusion leads to flexibility and operations visibility. In turn, manufacturers can make better, integrated decisions, making real-time process monitoring on the shop floor possible. This supports and encourages collaboration across planning, scheduling, and factory performance, leading to superior efficiency. Then artificial intelligence and machine learning can be applied to large data sets, uncovering non-conformance and non-regular data to make decisions based on that information quickly.
Closed-loop manufacturing provides operational improvement
Closed-loop manufacturing (CLM) and execution are accomplished through the data delivered via IT/OT fusion. It synchronizes and optimizes production around product design, production planning, manufacturing execution, automation, and intelligence from consumer use. This results in a collaborative, connected loop of information to continually improve the manufacturing process’s cost, time and quality to accelerate product delivery. In addition, it strengthens the alignment of the as-planned product with the as-built and as-used product in a continuous, iterative process.
CLM confirms that all teams have real-time information at each step in the manufacturing process, including product planning and engineering, through enterprise resource planning (ERP), the supply chain, and manufacturing operations management (MOM). Using MOM on the factory floor enables manufacturers to collect and maintain large amounts of data on the production and the physical products. This process now includes quality management, advanced planning and scheduling, manufacturing execution systems, enterprise manufacturing intelligence and more.
Then engineering teams receive well-timed manufacturing feedback to expedite problem resolution and confirm optimal product evolution. This process allows tracking of what was built with the data, how it was built, and the materials and parts. It also accelerates new product introduction to expedite time to market while maintaining fidelity to quality and compliance requirements.
Benefits of IT/OT fusion
When real-time data from IT/OT fusion is shared in an iterative process in closed-loop manufacturing, it identifies issues in assembly production that might require a change in work instruction during volume production to optimize process planning. This includes a situation when a machine goes down – a manufacturer can assess the impact on mid- to long-term planning, immediately identifying alternate resource capacity, order prioritization, sequencing, and synchronization, and quickly making the appropriate production changes.
Learn more benefits in Rahul’s article.
Siemens Xcelerator, the comprehensive and integrated portfolio of software and services from Siemens Digital Industries Software, helps companies of all sizes create and leverage a comprehensive digital twin that provides organizations with new insights, opportunities and levels of automation to drive innovation.
For more information on Siemens Digital Industries Software products and services, visit siemens.com/software or follow us on LinkedIn, Twitter, Facebook and Instagram. Siemens Digital Industries Software – where today meets tomorrow.
Stay up to date with the Siemens Software news you need the most.
About the author
Rahul Garg, Vice President of Industrial Machinery, Siemens Digital Industries Software, responsible for defining and delivering key strategic initiatives and solutions, and global business development. He and his team are responsible for identifying key initiatives and developing solutions for the industry while working closely with industry-leading customers and providing thought leadership on new and emerging issues faced by the machinery industry. Rahul’s experience and insight are derived from a 25-year career delivering software-based solutions for product engineering and manufacturing innovation for the global manufacturing industry, spanning a career in R&D to program management, sales and P&L management and having focused exclusively on the industrial machinery and heavy equipment industry since 2007.