Hydrogen-powered aircraft design can take off with digitalization
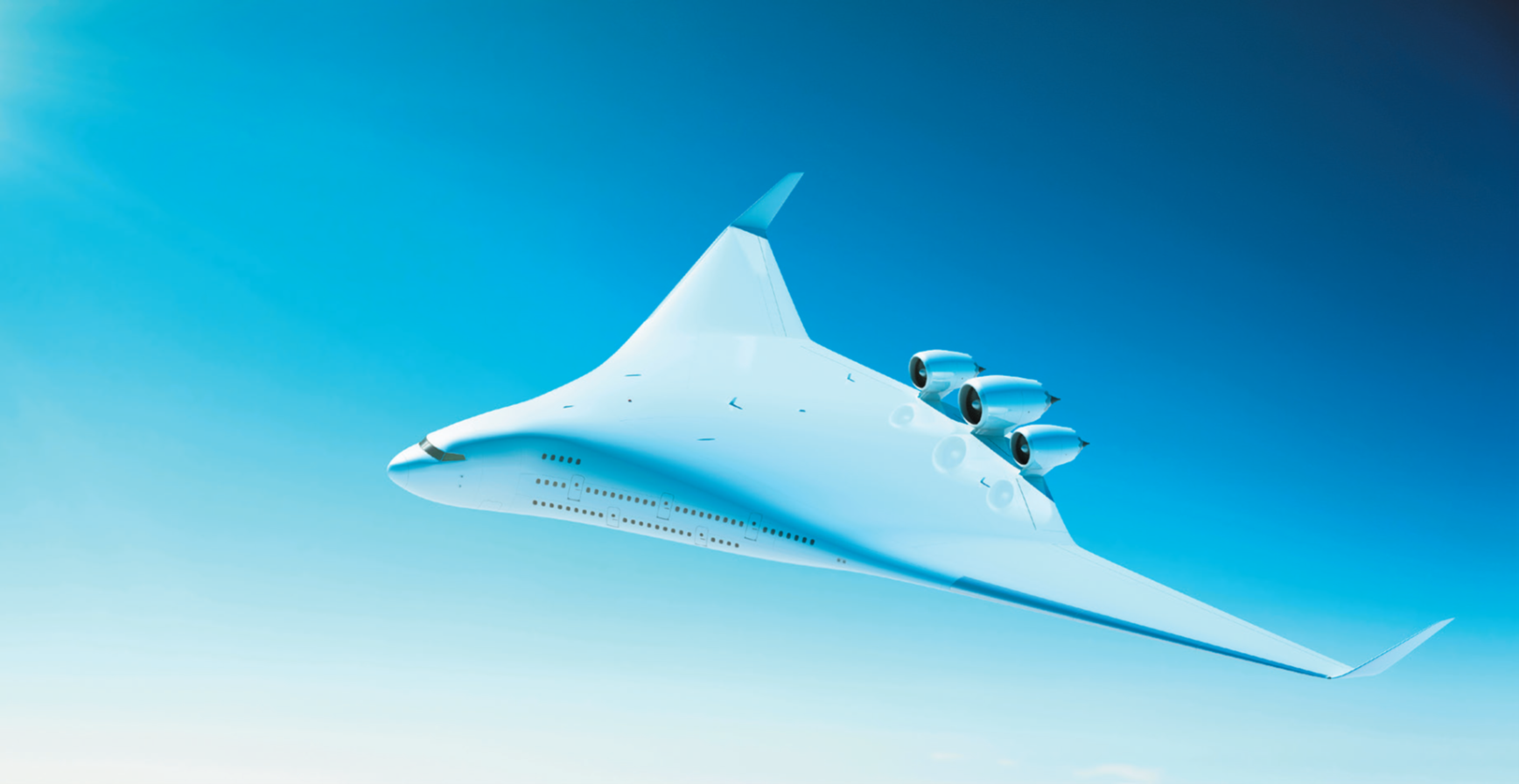
With climate change increasing in intensity across the world, the push for sustainability in the aviation industry has never been stronger. A significant part of that push is exploring new carbon neutral propulsion methods to limit emissions. One method gaining particular attention is hydrogen, as its high energy density is favorable for large-scale aircraft, and by extension, the increasing activity of commercial aviation. That said, hydrogen is very different from the kerosene used today, and will require engineers to design new aircraft configurations to store and use it, as well as the ground infrastructure to support them. Here, the virtual testing and integration capabilities of digitalization will be crucial in designing a functioning hydrogen-powered aircraft in time to meet sustainability goals.
Why hydrogen?
Hydrogen has multiple advantages for large aircraft over other sustainable propulsion systems like electric batteries and synthetic ultra-efficient fuels. Batteries may lack emissions, but their weight is too heavy for the low energy density they produce and are thus more suited to smaller aircraft. Synthetic fuels, meanwhile, can match the energy density of kerosene, but while their emissions may be lower than kerosene, the fact remains they still produce emissions. Hydrogen has the benefits of both options and none of their flaws. Its energy density is nearly triple that of kerosene, and its main byproduct is environmentally friendly water. With a high energy density and no carbon footprint, hydrogen is a prime candidate for powering large aircraft.
There are also different ways to utilize hydrogen to power aircraft, namely hydrogen-powered gas turbines, hydrogen fuel cells, and hybrid systems that combine the two. Gas turbines are not so functionally different from turbines used for fossil fuels today, so with some design adjustments, new turbines can easily be made to utilize hydrogen. Fuel cells, meanwhile, pass hydrogen and oxygen through an anode and cathode, respectively, to power electric motors and other systems. The diversity of applications gives engineers plenty of room to explore different aircraft designs.
Integrating hydrogen
Of course, hydrogen has a completely different set of qualities than kerosene and will impose new design requirements for aircraft, namely new storage systems. Hydrogen burns much hotter and faster than kerosene and is highly flammable, so turbines and storage tanks will need to have additional precautions to reduce risks of failure. Additionally, hydrogen takes up four times the volume of kerosene to achieve the same result. If hydrogen is stored as a gas, storage tanks will need to be large and significantly pressurized. If it is stored as a liquid, the tanks will require cryogenic temperatures to keep the hydrogen from boiling. All these additional storage requirements will have ramifications on the rest of the aircraft that engineers will need to consider.
Additionally, any application of hydrogen will impose new requirements on aircraft configurations. For decades, commercial aircraft have been built with the tube-and-wings configuration, with passengers carried along the central tubular body and fuel stored along the wings. No matter the approach, hydrogen will likely need to be stored in the body to achieve the right conditions, which will require adjustments to the body’s internal and external configuration.
Ideas for alternate configurations exist, but have their own drawbacks. The blended wing aircraft, for example, combines the body and wings into one structure to add more fuselage for hydrogen storage, but this idea raises more design questions, like how to account for passengers. Will passengers still be seated by windows? If so, how can the effects of the increased torque and motion they will experience from the wider body be mitigated? Engineers will need to answer these questions and more when they design new hydrogen-friendly aircraft configurations.
The digitalization of hydrogen
The challenges in designing hydrogen-powered aircraft will impact nearly every aircraft system, but digitalization can be vital to address them effectively. Technologies like the digital twin can be used to create a virtual representation of an aircraft that engineers can test their ideas on, optimizing their design choices and reducing reliance on expensive, time-consuming physical prototypes. Another crucial component of digitalization is the integration of design domains, allowing engineers to develop interfacing aircraft systems, such as thermal and mechanical, simultaneously and efficiently. By connecting these disciplines through a virtual testbed, digitalization can help engineers design safe hydrogen-powered aircraft that meet sustainability goals.
A hydrogen-powered future?
Hydrogen has enormous potential to create a sustainable form of commercial aviation that keeps up with industry trends, but its use creates new challenges engineers must consider when designing new aircraft. Alternative aircraft configurations offer ways to efficiently utilize hydrogen, but impose their own new design requirements. With digitalization, however, aviation companies can accelerate and optimize the design of hydrogen-powered aircraft and give rise to a new generation of sustainable aviation.
For more information on hydrogen-powered aircraft design and other forms of sustainable aviation, check out the resources below.
- White paper | Hydrogen-powered aircraft design
- White paper | Paving the way to sustainable aircraft with the Clean Aviation Joint Undertaking
- Webinar | Future of sustainable aviation
- White paper | Shaping sustainable aviation with a digital twin
Siemens Digital Industries Software helps organizations of all sizes digitally transform using software, hardware and services from the Siemens Xcelerator business platform. Siemens’ software and the comprehensive digital twin enable companies to optimize their design, engineering and manufacturing processes to turn today’s ideas into the sustainable products of the future. From chips to entire systems, from product to process, across all industries, Siemens Digital Industries Software is where today meets tomorrow.