The Digital Enterprise empowers advanced product design
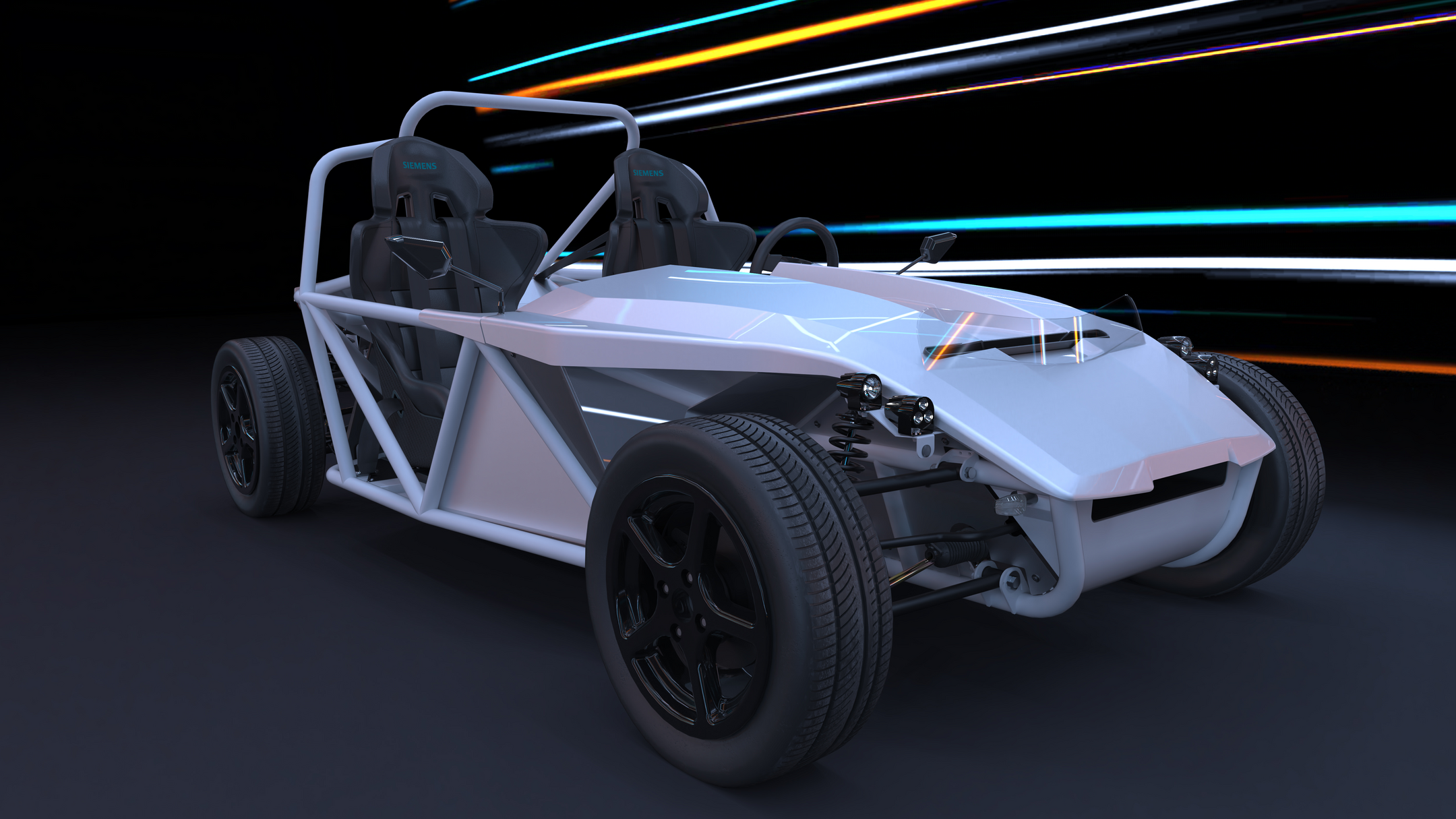
Companies of all sizes and in all industries are facing a future of disruption, uncertainty, and challenge. Product complexity is growing rapidly, due to increased demand for connectivity, customizability, and integrated intelligence. Sustainability is a primary concern for companies around the world as new regulations come into effect and companies seek to reduce their environmental impact.
These trends have implications across the product and production lifecycle, and will drive changes in how companies design, test, manufacture, and recycle the products of the future.
So, how do companies overcome these challenges and prepare for the future of more agile, intelligent, and sustainable industries? The answer lies in digital transformation. Through digital transformation, companies can combine the real and digital worlds, managing the product and production lifecycles in both the real and virtual worlds.
By doing so, companies can become Digital Enterprises, able to gather and exchange data and information quickly between product and production development, testing, maintenance, and operation.
This ability to collect, understand, and use data throughout the organization is what defines a Digital Enterprise. It gives them the capability to react quickly to market demands, develop innovative products and production solutions, overcome complexity, and become more sustainable in the process.
The Digital Enterprise in practice
To demonstrate how this can work in practice, Siemens uses a technology carrier, a small, light, all-electric roadster, called the SimRod. The SimRod, however, is more than just a small roadster; it validates and demonstrates the capabilities of the Digital Enterprise utilizing the cutting-edge technology found in Xcelerator, Siemens’ engineering software and automation portfolio.
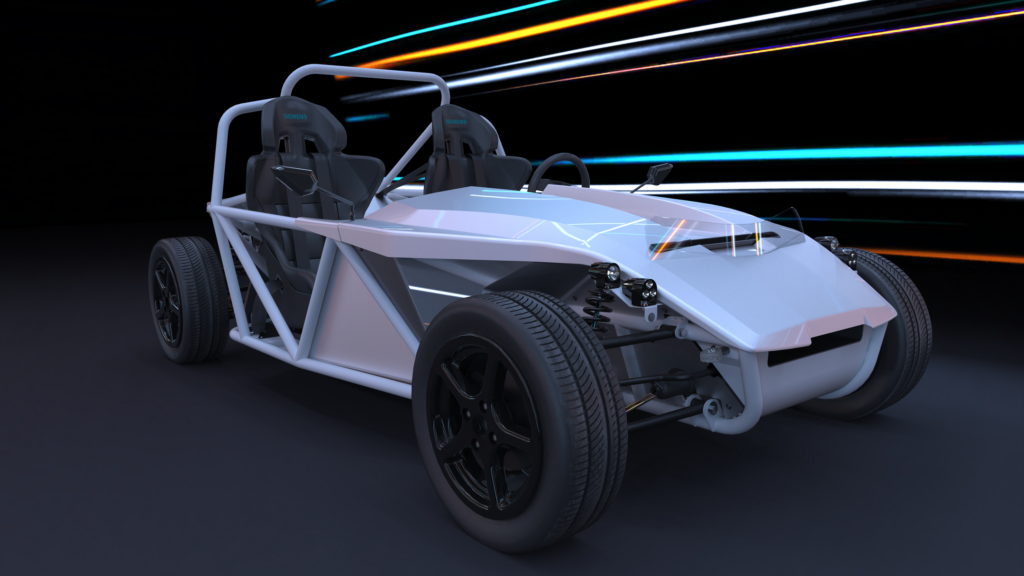
The SimRod, therefore, acts as a representative for any modern product and the production processes involved. By looking at the SimRod, we can understand how becoming a Digital Enterprise can empower companies to build the products of the future.
Leveraging the Digital Twin to design an all-electric roadster
Let’s start with the key performance characteristics for our all-electric roadster.
- First, a modern EV should be able to drive several hundred miles in between charges.
- Second, our EV roadster should also be fun and engaging to drive, with enough power to make it exciting from behind the wheel
- All without sacrificing efficiency and battery capacity.
With these key characteristics in mind, we can begin to design, test, and improve the SimRod. In a traditional development cycle, this would involve a lengthy process of designing the vehicle before producing several physical models and prototypes to test the design. The results of these real-world tests then drive re-design and optimization cycles before another round of physical models and prototypes are created for testing.
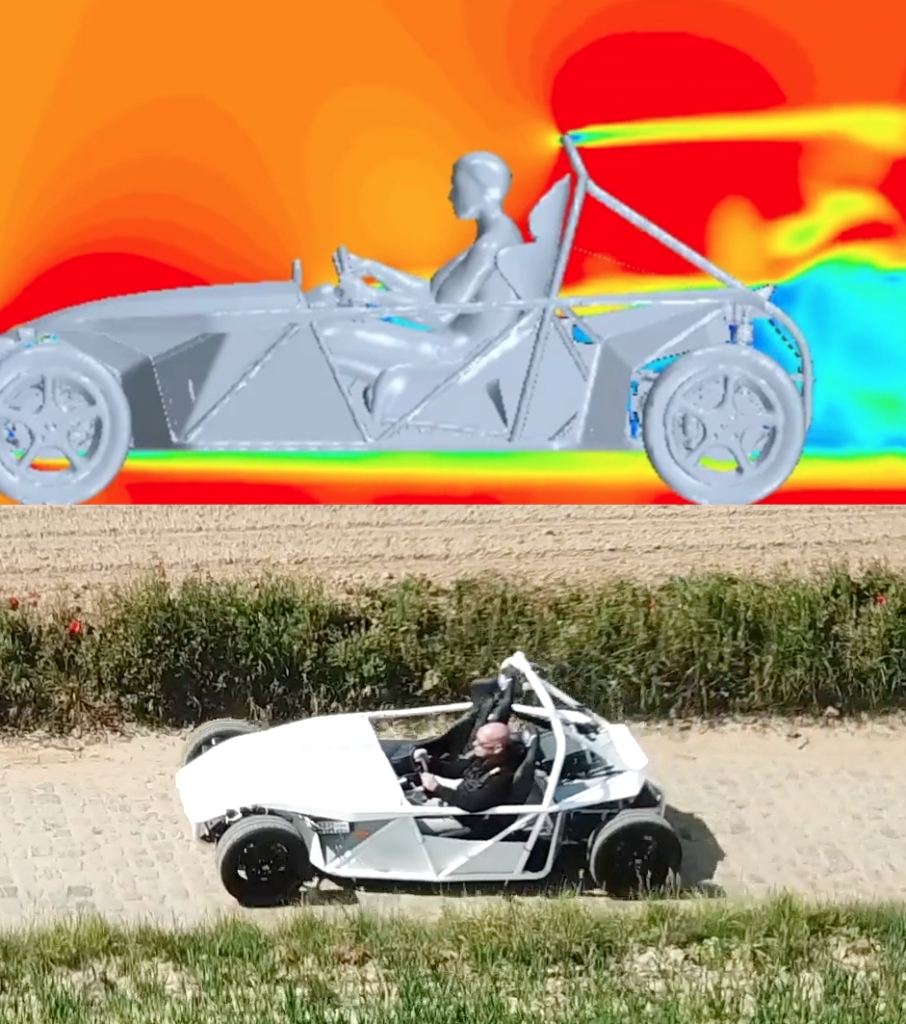
A Digital Enterprise can merge the real and virtual worlds through the Digital Twin of the vehicle to accomplish the same task much faster and with fewer prototypes, cutting down on the resources used during testing. As the designers refine and mature the Digital Twin of the product (the SimRod in this case), other engineering teams can leverage this Digital Twin in various simulation environments to test and improve every aspect of the vehicle:
- mechanical systems
- electrical and electronic systems
- software
- chassis and handling
- powertrain
- autonomous driving
- and more
For a modern EV, this allows design and engineering teams to not only accelerate their design processes, but also verify, validate, and optimize these designs all within the digital realm.
Merging the real and virtual worlds through data
Eventually, some real-world testing is still necessary to achieve the final verification and validation of the SimRod’s functionality, performance, and driving characteristics. Even though this testing occurs in the real world, the Digital Twin still has an important role to play. The SimRod is outfitted with dozens of sensors to collect data from every vehicle system during testing sessions. By folding this data back into the Digital Twin of the vehicle, engineers can identify opportunities for optimizations and rapidly develop solutions – collecting, understanding, and using data for continuous optimization.
Indeed, a short drive on a cobblestone road outside Leuven, in Belgium, revealed such an opportunity in the SimRod. The data gathered during that drive indicated that the steering knuckle, which transfers the motions of the steering wheel to the front wheel of the vehicle, could be made lighter while preserving its structural rigidity and strength. To develop a lighter steering knuckle, Siemens engineers scanned the original part into NX. Next, the team used generative design to optimize the steering knuckle’s topology, resulting in a steering knuckle that weighed 30% less than the original while maintaining its strength. The new design was also tested by use of the data previously collected on the cobblestone road in Leuven.
In part two, we will move into the world of production, examining how the Digital Enterprise and the Digital Twin can enhance the production environment through advanced technologies and digitalized production planning and design. In the meantime, you can visit us at www.siemens.com/digital-enterprise to learn more about digital transformation, the Digital Enterprise, and how Siemens’ Xcelerator can help you on this journey!
Siemens Xcelerator, the comprehensive and integrated portfolio of software and services from Siemens Digital Industries Software, helps companies of all sizes create and leverage a comprehensive digital twin that provides organizations with new insights, opportunities and levels of automation to drive innovation.
For more information on Siemens Digital Industries Software products and services, visit siemens.com/software or follow us on LinkedIn, Twitter, Facebook and Instagram. Siemens Digital Industries Software – where today meets tomorrow.