Lightning fast and durable printed parts
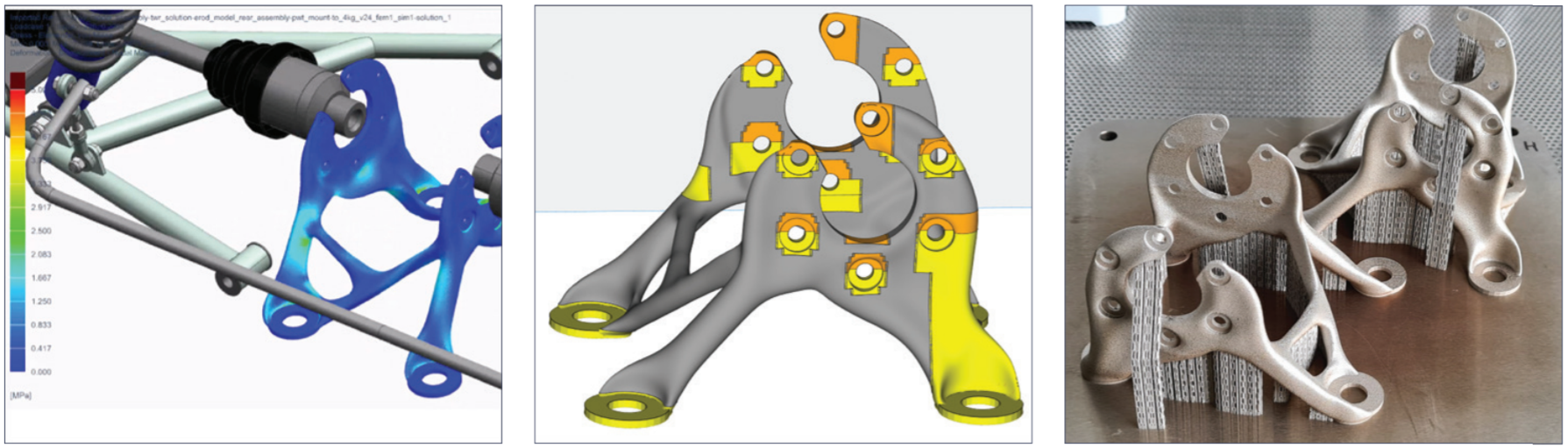
Getting a component quickly is paramount to many businesses and the global supply chain in general, as lost time waiting ripples through development increasing the overall costs of production. Capturing this need was one of the first goals for additive manufacturing (AM) technologies with the emergence of rapid prototyping machines. And while it is still a major feature of the printed products today, the components are being deployed in working environments. No longer used to understand the physical dimensions of an idea, printed parts need to be durable for applications in aerospace, energy generation, industrial machinery, and much more. Without the experience afforded to more traditional manufacturing methods, however, engineering strength into AM components is a non-trivial task. Simulation is quickly becoming the only way to keep up with the lightning-fast development times required of AM components.
Material differences
Possibly the greatest hurdle to perfect prints is that 3D printing, regardless of technology, creates a heterogeneous component with variation throughout due to asynchronous cooling. That is not inherently disadvantageous, in fact some best-of-class products rely on differences in a material, the challenge comes from our collective inexperience with the material processes. It is extremely difficult to predict the grain structures that form within the parts because there are so many variables in the process. Compare that with forged steel, there are a high number of defined material properties using the same set of inputs, but the cause and effect have been defined over centuries of metallurgy advancements. This near randomness of AM material properties extends to other factors, like porosity, which contribute to the difficulty in defining durable components and creating them consistently without advanced tools.
Process influences
Not all printing techniques are equal in their final durability, however, the process has a dramatic impact on the durability results. Possibly the best example of a process’ influence on durability characteristics is in the orientation of a part within the build volume. The same part printed on the same machine can have drastically different strength characteristics just by reorienting the part. This comes about from a variety of factors. The cross section of the part changes dramatically with this action, requiring a new tooling path simulation to check for overheating spots. And with planar printing, failure from reorientation can emerge from printed layers coinciding with a stress concentrating structure – allowing stress fractures to for and expand with usage. Fortunately, as the application of AM has expanded so too has the toolset for the technology and simulation plays a major role in creating durable components.
The simulation solution
Simulation helps sift through the massive amount of information needed to successfully print a durable part with additive technologies. But on it’s own the tools are analogous to a Monte Carlo simulation, checking each variable to see if the result is favorable. This can be effective, but it is far rom fast, which is why machine learning (ML) is making its way in to simulation technologies for fatigue and durability. How you might ask? For an in-depth understanding, my colleague has a great explanation coming out soon, but quick-and-dirty it is using physical tests and simulations to create empirical solutions to the durability problem. By simulating the behavior of a material or process and validating the results against physical tests, the ML algorithm is learning how to make better guesses in the simulated environment. It is essentially an artificial intuition as a smith would employ for their own craft.
It is amazing what can be achieved with the right tools and processes, and I’m very interested in how this specific solution progresses. How much time can be cut from development because of additional process knowledge? And how much better will parts become as we collectively push the limits of these materials? But I’ve only scratched the surface of this technology, if you’d like some more information of the material hurdles of AM, how the simulation environment is refined with machine learning, or read about a real-world application of the technology, the whitepaper is a great read.
Siemens Digital Industries Software is driving transformation to enable a digital enterprise where engineering, manufacturing and electronics design meet tomorrow. Xcelerator, the comprehensive and integrated portfolio of software and services from Siemens Digital Industries Software, helps companies of all sizes create and leverage a comprehensive digital twin that provides organizations with new insights, opportunities and levels of automation to drive innovation.
For more information on Siemens Digital Industries Software products and services, visit siemens.com/software or follow us on LinkedIn, Twitter, Facebook and Instagram.
Siemens Digital Industries Software – Where today meets tomorrow