Integrated design and simulation enable the industrial machine’s digital twin
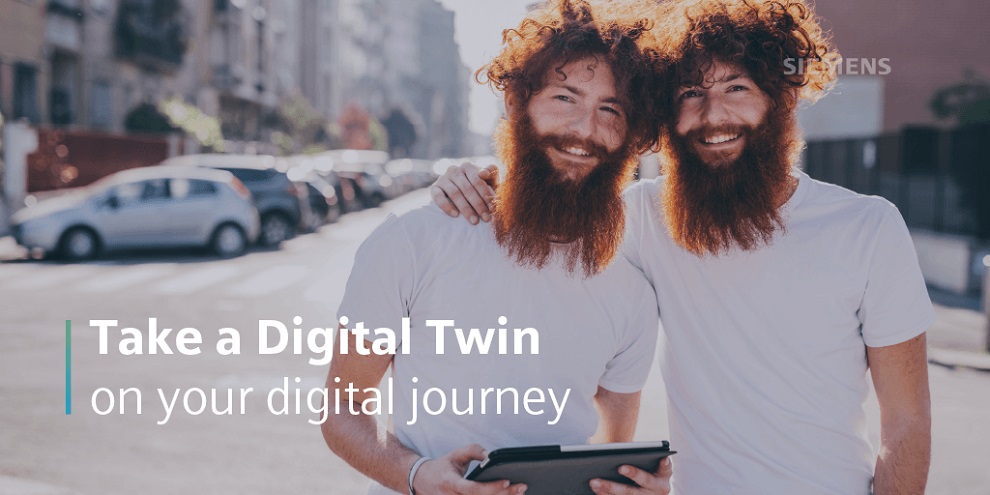
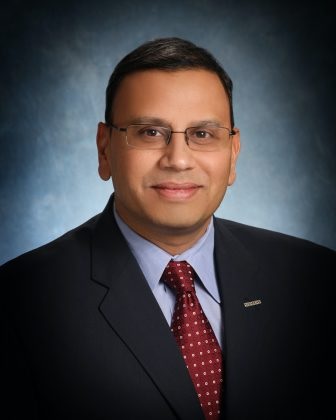
If you want smart manufacturing, it is essential to have smart tools. Companies can no longer rely on conventional, outdated methods of product engineering. The development of industrial machinery is becoming highly intelligent and complex, needing a new approach – a digital twin. An integrated design and simulation enable the creation of the industrial machine’s digital twin, assisting in comprehending and predicting the physical machine’s performance under various conditions without needing a physical prototype.
>Read the eBook.
This recent eBook teaches about boosting productivity and driving innovation through simulation with Intelligent Performance Engineering (IPE).
A machine’s digital twin provides shorter commissioning times, predicts maintenance needs and reduces machine downtime in the field.
A comprehensive digital twin captures simulation and validates the results in a central repository. Designers can now incorporate changes based on these results, closing the loop between testing and design. Subsequently, a digital twin can increase design flexibility, boost productivity, improve innovation processes and promote next-generation smart industrial machines.
When you run the simulation parallel to the design, it reduces the product lifecycle and allows fully validated products to be out the door faster. Furthermore, it maintains reliability and safety while integrating tests and simulation in the same environment, thus automating information sharing and enhancing interdisciplinary collaboration to provide time and resource-saving efficiencies.
There is an ever-increasing need to develop industrial machines faster, with better flexibility to meet changing customer demands. Integrating simulation data and designs saves time and money in the product life cycle and stays ahead of the competition.
Learn how to drive innovation through simulation. Think of the possibilities and imagine, simulate and validate them under real-world conditions with Integrated Design and Simulation, a part of Siemens’ Intelligent Performance Engineering solution.
Siemens Digital Industries Software drives the transformation to enable a digital enterprise where engineering, manufacturing, and electronics design meet tomorrow with the Xcelerator portfolio.
Xcelerator is a comprehensive, integrated portfolio of software, services and an application development platform, accelerating businesses’ transformation into digital enterprises. It unlocks a powerful industrial network effect – essential requirements to leverage complexity as a competitive advantage, no matter the industry or company, to seamlessly create tomorrow’s complex machines.
Related links:
Listen to the IPE Integrated Design and Simulation Podcast.
Listen to the IPE Podcast on leveraging machine complexity.
Learn more about Intelligent Performance Engineering.
About our expert
Rahul Garg is the Vice President for Industrial Machinery & SMB Program, responsible for defining and delivering key strategic initiatives and solutions and global business development. He and his team are responsible for identifying key initiatives and developing solutions for the industry while working closely with industry leading customers and providing thought leadership on new and emerging issues faced by the machinery industry. Rahul’s experience and insight are derived from 25 year career delivering software-based solutions for product engineering and manufacturing innovation for the global manufacturing industry, spanning a career in R&D to program management, sales and P&L management and having focused exclusively on the industrial machinery and heavy equipment industry since 2007.