More sustainable manufacturing with additive
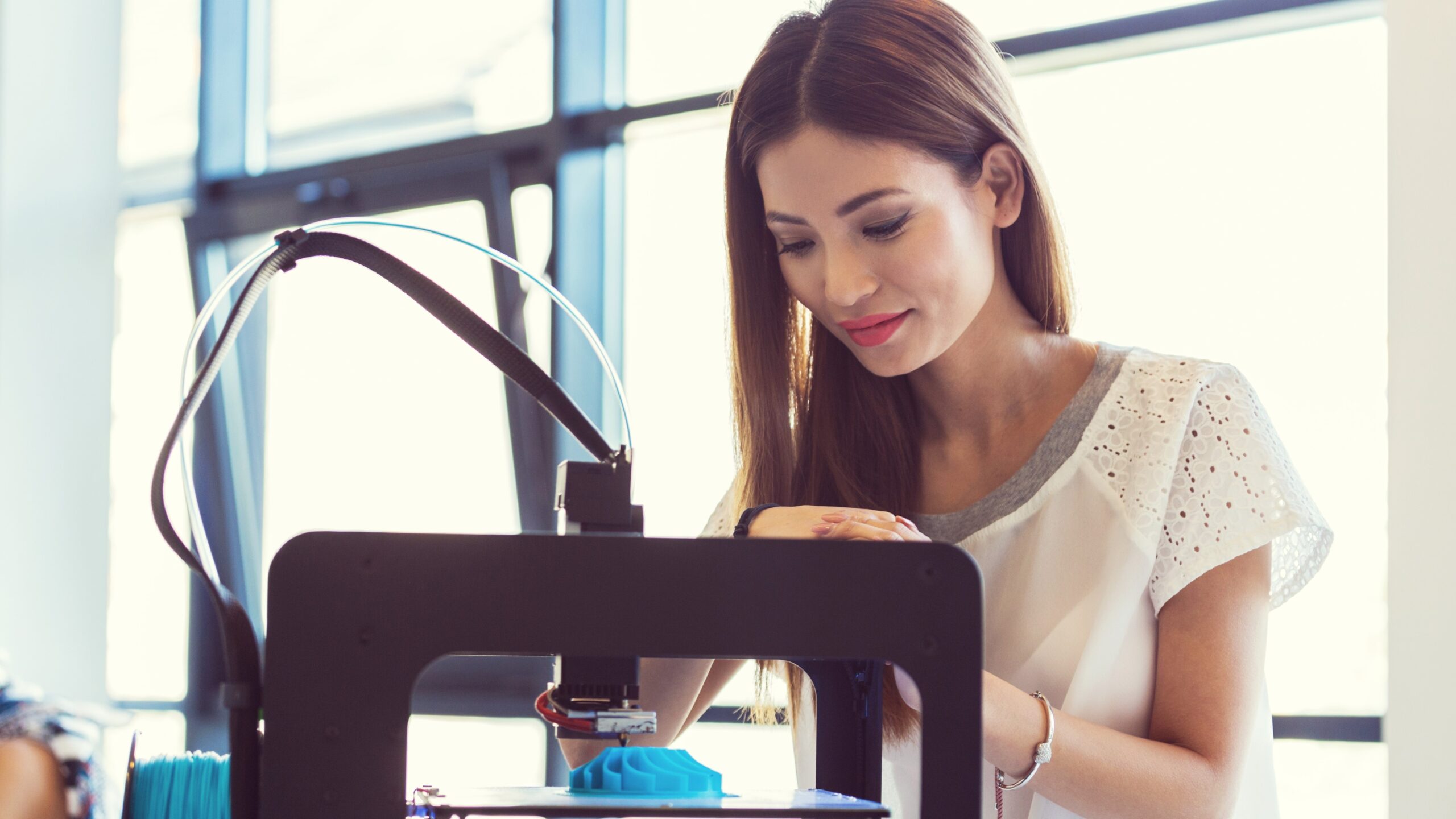
Localized manufacturing has long played second fiddle to the efficiency of centralized manufacturing processes. Centralization enables process optimizations to have a much greater impact on production due to the shear volume of product running through a single site, it also streamlines the supply chain such that there are fewer parties that need to coordinate for business efficiency. But those efficiency gains are not free, they come at the cost of flexibility and to some extend adaptability. In the event of a supply chain disruption, manufacturing can be halted by lack of an individual material or component. Localized manufacturing, aided by additive manufacturing (AM) technologies and software, creates a path to reduce the stresses on manufacturing induced by unaccounted for disruption avenues. AM makes manufacturing more sustainable and not just in surviving the unexpected.
If you are unsure of what 3D printing or AM are, Brian Neff of Sintavia gives a great primer on the technology in episode 22 of Barbara Humpton’s Optimistic Outlook podcast, as part of their discussion of how it is changing the world today and tomorrow. But to get to the interesting points of conversation, AM is essentially adding thin layers together until the 3D object is completed. Functioning much like an office printer, AM works one sheet or layer at a time. Each sheet contains the cross-section of the 3D object and with a great enough density of layers the process approximates exact curves and surfaces in all three directions. The important takeaway from the technology is that this layering process enables internal cavities and geometries that are almost impossible to create with other methods, all while only using the material needs to complete the part.
Localization
Supply chain shortages during the pandemic are a prime example of the value in localized manufacturing and even hyper-localization with 3D printing. When faced with ventilator shortages, many engineers, doctors and manufacturing groups working together to 3D print critical parts for the machines. Some even tried to increase the effective number of ventilators by optimizing the designs to work for to patients simultaneously. Even more localized was the need from hospitals for face shields while larger manufacturers ramped up production with more traditional manufacturing methods. The most efficient method for making face shields is injection molding, but the molds take time to design, test and calibrate. 3D printers can simply take a 3D component file and start right away. This short-term capacity was invaluable to many hospitals, with small groups of ‘makers’ setting up networks of home printers and unused industrial printers to make supply as a stopgap solution.
But as Barbara explains in episode 22, this is a valuable proposition manufacturing in general, not only in additive manufacturing but definitively with the technology making the process an easier goal to reach. By keeping local supply chains intact, products delivery can be ensured even if not at the same volume that would be available under normal operations in a globalized supply chain. This is exemplified by the water shortages that have hampered silicon production, business efficiency dictated that a single location was preferable to production to minimize the already exorbitant investment costs but that also created a single source of failure that has created ripples across multiple industries. AM provides a path to enable small factories around the globe serving locally and globally when the next supply chain disruption occurs.
Minimization
The other sustainability improvement additive manufacturing brings to the table is most notable in the aerospace industry. In an airplane, every gram is important because every bit of mass from the structure of the plane is effectively more mass that is removed from the maximum load. Mass also contributes to the total fuel efficiency of the aircraft, moving more weight requires more energy. Additive manufacturing provides new techniques to minimize the weight of parts when combined with comprehensive software and simulation solutions. Traditionally parts are cut from billet, which itself is a wasteful process creating large amounts of scrap metal but it also means the inside of the part is solid. That can add a lot of extra weight when a part may not even approach the strength limits of a solid piece of titanium or even aluminum.
Instead, a printing part can contain an internal lattice that supports the structure while minimizing the total mass of the component. Doing this once still helps the overall efficiency of the aircraft, but doing it repeatedly wherever it can be can drastically reduce the weight of the airplane – and with a direct relation between total weight a fuel consumption it is a valuable workflow for aerospace companies looking to make air travel sustainable. Beyond the lattices for lightweight materials, the geometries of components can be matched more readily to their functions, to reduce overhead and possibly remove now unnecessary connections from a design by printing a system as one piece.
A more sustainable world
Whatever your business is doing to make manufacturing a more sustainable endeavor, it is important to understand that additive manufacturing is a powerful tool in your toolbox. But it is just as important to remember that it is not a matter replicator like one would find aboard Star Trek’s USS Enterprise. The technology has limits, but understanding them with a comprehensive software solution will help your team provide something once impossible with traditional manufacturing methods. For more details on how AM is shaping the future, I would highly recommend listening to all of episode 22 of The Optimistic Outlook on your favorite podcast platform or watching it on YouTube.
Siemens Digital Industries Software is driving transformation to enable a digital enterprise where engineering, manufacturing and electronics design meet tomorrow. Xcelerator, the comprehensive and integrated portfolio of software and services from Siemens Digital Industries Software, helps companies of all sizes create and leverage a comprehensive digital twin that provides organizations with new insights, opportunities and levels of automation to drive innovation.
For more information on Siemens Digital Industries Software products and services, visit siemens.com/software or follow us on LinkedIn, Twitter, Facebook and Instagram.
Siemens Digital Industries Software – Where today meets tomorrow