Future-proof with the IoT miniseries – ep. 3 Transcript
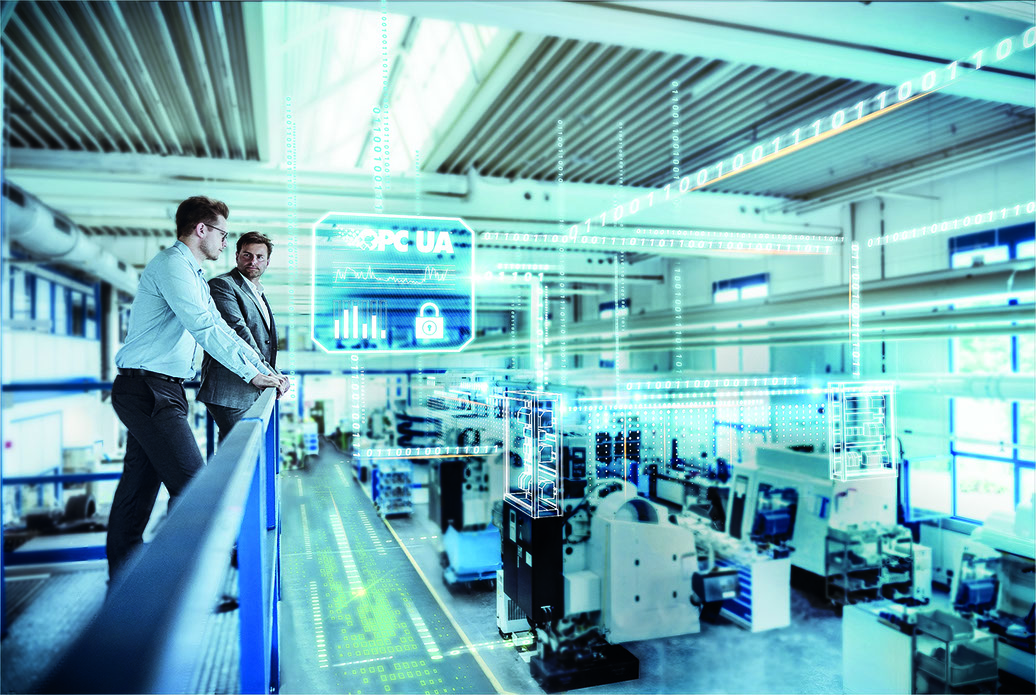
Episode three is out for the miniseries Future-proof with the IoT, our experts have covered the trends impacting the industrial machinery industry in episodes one and two – how they were already growing challenges and how many were exacerbated by the COVID-19 pandemic and the ensuing supply chain disruptions. This third episode covers where to start when adopting the industrial internet of things as well as the options of how to build it.
You can read along as you listen, below through Acast or just listen through your favorite podcast platform:
Jörg Ludwig: Hello! This is “Future-proof with the IoT”. A podcast mini-series for the IM industry, learning how to leverage digitalization to overcome manufacturing disruptions and bounce back stronger. I’m your special host, Jörg Ludwig.
If this is your first time joining, our first two episodes covered the challenges of IM and how four major trends were impacting the industry even before the pandemic started – new business models, hyperautomation, low-cost competition and a new generation in the workforce. The episodes are available on all your favorite platforms, and we’ll include a link in the description.
But today, we’ll be talking about how the Internet of Things (IoT) can help with these challenges in manufacturing.
Joining us again today are Colm Gavin, Portfolio Development Manager at Siemens Digital Industries Software, Matthias Lutz, Head of PreSales and Solution Design at DI SW, and Heiko Dickas and Sebastian Oeder from Siemens Bad Neustadt, leader of the digitalization team and head of the production unit main motors at the electric motor factory, respectively.
IoT has become crucial to IM in recent years. By connecting devices to collect and share data, IoT is one of the strongest enablers to accelerate digital transformation. So, whether you, my dear listeners, are considering improving your factory’s production capacity, the maintenance of your machines, or reducing the energy consumption, the adoption of IoT technology will provide tremendous benefits for your business.
Adoption is expected to flourish, based on the “IoT Commercial Adoption survey” published by Eclipse Foundation in March 2020: 40% of organizations plan to increase IoT spending in the next fiscal year.
So, Colm, first question, what will be your recommendations to start with digitalization?
Colm Gavin: I think a simple thing, start simple. Start small, then roll it out gradually where you see a value, some low hanging fruit where you think you can get some value quickly. It’s very important that you already have a clear vision laid out of a goal of what you’re actually trying to pursue. Just doing digitalization because everyone’s doing it, that doesn’t make sense. So, you need to have a clear business value, business idea behind it: what is it you’re trying to do? What’s the goal? Whether it’s improved production, reduced downtime, plan the maintenance segments, or make product smarter in order to be able to offer customers that added value. The simplest thing you can do to start is around the topic of connections: how are you going to connect your devices, your components, your machines to collect the data? What considerations and requirements do you need to put into the switches or the communication protocols because all of that matters because, data is the new gold. So, you’re going to need a powerful communications network to handle some of the data quantities that will be generated. And critical will be, your communications network and components, can they handle the speed, the high data volume capacity, as well as ensuring the security.
Jörg Ludwig: Got it. Matthias, what is your recommendation?
Matthias Lutz: So, it’s very important to stay realistic during this process. I’m sure many of our listeners keep hearing that the IoT is the answer to all their problems. And what you typically hear is that you need to get predictive maintenance going to start with artificial intelligence and machine learning to advance automation. But that’s wrong. It is out of reach right now, expensive, and time-consuming. And while there is value in that higher-level implementation, of course, that’s something you build to over time. But you get immediate, real value from getting started with condition monitoring. So, getting your things connected, start to learn to interpret this data, and to monitor the condition of your machinery. You don’t need fancy analytics, in the first place; you just need connected machines and a way to intelligently see them. It’s not cost-prohibitive; it doesn’t take months to set up. In general, a maturity curve looks for me like, first, to get your things connected, start to understand the value of IoT and your data, gain experience in implementing first IoT use cases with a clear value add to your organization or your end customer, then get the transparency about what all the things out there are doing; how you can use data to build a system of systems to interconnect different, let’s say, data silos, and this will help you gain new insights and to improve your products, production, or your services. And after having achieved that, which is quite challenging, you will be able to win new customer groups and stay more competitive. And last but not least, I think it’s not only about the sole IoT technology; it helps you to generate value through network effects based on your own ecosystem. Because this will eventually enable a new way of doing your business, doing your service, and getting access to new customer groups. Get started now, use out-of-the-box IoT technologies, IoT as a service and applications, gain immediate value out of your data, and then think about how to evolve along this, let’s say, maturity curve.
Jörg Ludwig: So, you mean the minimum to start should be condition monitoring? Colm, what are the differences between an edge implementation and doing so on the cloud?
Colm Gavin: The fundamental difference between edge and cloud, I mean, as the name implies, you’re processing and working with the data local besides the machine. And while the edge systems including the new one from Siemens, our Simatic Industrial Edge Solution, of course, it’s possible to send the data to the cloud, or to other on-premise systems if you want, but fundamentally, the application is running on an edge device local to the machine as opposed to an application running in the cloud, and you’re communicating to the system. In many cases, it’s just not practical to send data to the cloud, so you need that local processing, for example, high frequency of data. In some cases where the latency is really important, you can’t send it to the cloud, upgrade it, and send it back, that’s going to take too long if you need to react quickly. In other cases, purely physical, I think an extreme example, but I think it’s a great one, is a ship in the middle of the ocean; they want to do analysis on their subsystems on the ship, and so on but there’s no way that they’re going to rely on making a connection to the cloud system out in the ocean. But the reasons to drive you to an edge such as the physical or the latency, we need to be able to manage the applications that are running on the edge device. And that’s a whole topic in itself that I think Siemens can bring a lot of value with our, say, edge computing solution as well.
Jörg Ludwig: IBM has published an article explaining that one production line at a modern plant might have 2,000 different pieces of equipment. Each piece could have 100 to 200 sensors that collect data continuously, generating 2,200 terabytes of data each month; that is a lot of wealthy data that needs to be handled securely. So, Colm, is edge more secure than the cloud? What cybersecurity options do each offer?
Colm Gavin: I think the edge is definitely a very secure option. We have comprehensive security mechanisms on all the layers. Of course, the edge software running on an edge device lives down beside the machine, but it does have, of course, a connection to the cloud as far as the deployment of the apps. But from a security standpoint, if we think of the beginning from top-down and from the cloud area where we would deploy the edge application to the edge device, we offer a multi-layered security model with data center security, application security, and secure access authentication, role-based access control, and a multi-factor authentication; we comply with the secure data storage according to ISO 27001. So, from a cloud perspective, moving down to the edge to communicate it, it’s quite secure. The actual communication mechanism we use when we go from the cloud down to the corporate firewall before we get into the actual edge device, that communication is encrypted. Once we’re inside the facility on the edge device itself, of course, the physical storage of the data is inside the manufacturing in a facility. And within the edge device itself, the edge application is encapsulated, and they secure the edge application by a secure application based on an up-to-date runtime environment. And then on the actual edge device, multilayered access control – again, with authentication – user rights, port restrictions, and a secured managed Linux. So, I think it’s very well supported in regard to security for the edge device.
Matthias Lutz: Somehow like your question: if edge is more secure than cloud, and I think there’s no clear answer, a lot of our customers do see the benefit in using best of two worlds. When it comes to industrial IoT, it’s very important to talk about security, of course, and as Colm mentioned, we have done everything state of the art to ensure security on all layers. But when talking about security, a lot of our customers actually mean confidentiality. And I think that’s a very important topic to talk about. With our industrial IoT offering, we offer our customers as well a way to share in a confident way data between different entities, between different customers, and among other partners such as the app developers. What I do see with a lot of customers is that they really see this value of a tightly connected edge and cloud system where they can move easily data loads between both worlds. When starting the whole IoT journey, many of our customers said, “Okay, we don’t want to talk about cloud; that’s not secure.” But I think this has changed dramatically over the last years. So, I think each and every customer, in traditional industries, clearly see the benefit of cloud, and they even have a clear cloud-first strategy. And combined with edge, that’s, for me, the winning combination in industrial IoT.
Heiko Dickas: And how we are doing this in Bad Neustadt? So, in Bad Neustadt we’re using several options to collect and monitor data. When we started the digitalization push, we used our inline system, SINUMERIK Integrate, where we can collect and visualize data from the whole shop floor. We are using the performance monitoring very much and it’s still in use. But getting the new option, MindSphere, then we started using MindConnect nano boxes, SIMATIC S7s; this is also the most used option in our factory at the moment. Especially for machine tools, with SINUMERIK clients, we can also collect the data with the SINUMERIK Integrate gateway. For applications, which are very close to the machine where high-frequency data has to be evaluated, then we use as well the SINUMERIK Edge. But not only machine data we connected to MindSphere, even databases like SAP or other local used databases: Oracle databases, SQL databases; we have connected to MindSphere. And we use here also the MindSphere Integrated Data Lake’s APIs, or even the Mendix app which is developed and operated by our IT department. But always supported by our infosec guys, because it’s very important for us to save our information as good as we can. And in general, we created a clear architecture from which sources we want to collect data from different systems, and where and how the data should be visualized. And our common solution for this is MindSphere. For monitoring the data, we look extremely to the needs of our software guys. If there’s a native app available which fulfills the demands, then we use this.
Jörg Ludwig: Thank you, Heiko, for that great insight. Sebastian, can you elaborate a little bit how that digitalization journey went on after these initial steps in condition monitoring at Siemens Bad Neustadt? I really like to hear about those use cases and experiences before taking a decision. How has IoT improved your factory?
Sebastian Oeder: Automation and digitalization are clearly set in our vision as a main driver to increase our competitiveness. The required boundary conditions to realize digital use cases have been set and further developed since years. This includes the technical side with IoT infrastructure, as well as the personal side with the required experts. On the technical side, we started with performance management. I’m convinced that it is quite irrelevant with which topic you start, as long as you do start. After the first use cases which have been a push to a certain degree, new ideas from the production units came up: what else could be done with the data from the machines. The rest is an ongoing cycle in further gathering data: use the latest technology and software, rollout successful use cases to the entire factory, and connect digitalization and automation use cases. Our latest use case in my department is an assembly line with automated testing, where the decision “which tests need to be performed,” is determined by AI. My personal feeling is that, technically, everything is possible, but we need to select wisely which topic is the most efficient.
Jörg Ludwig: Thank you, Sebastian! That’s a great example of how things can go! And what really goes by very quick is time. Unfortunately, we ran out of time again! In our next episode we will continue talking about how IoT can help solve industry challenges. Take care and we hope to have you again!
About the Host and Guests
Jörg Ludwig – Since 2018, Jörg has been in the sales enablement team for MindSphere and since October 2020 also for Mendix, globally responsible for the creation of learning paths, enablement sessions, and value selling trainings and workshops. Prior to Siemens, Jörg ran his own business as a Value Selling trainer and coach for more than 7 years. He gained Sales experience and expertise from over 16 years in global Software Sales organizations.
Heiko Dickas – Heiko is the Team Leader of the digitalization team since the beginning of 2017 in the Bad Neustadt motor factory. His scope is being an enabler for the production unit in terms of digitalization. Heiko has been with Siemens for more than 30 years in different functions.
Colm Gavin – With over 20 years of experience in the Siemens Digital Factory, Colm works on business development for digitalization topics as they pertain to Siemens SW and Factory Automation, specifically virtual commissioning, Industrial IoT, Industrial Edge and AI topics.
Matthias Lutz – Matthias joined Siemens 14 years ago, starting in supply chain and procurement department. In 2015, he moved to the industrial customer service organization, focusing on industrial IoT and digital services.
Sebastian Oeder – Sebastian is Head of the production unit main motors in the Bad Neustadt motor factory. He has a background as a production manager at Siemens Energy and as a consultant at Siemens Corporate Technology.
Siemens Digital Industries Software drives the transformation to enable a digital enterprise where engineering, manufacturing and electronics design meet tomorrow. Xcelerator, the comprehensive and integrated portfolio of software and services from Siemens Digital Industries Software, helps companies of all sizes create and leverage a comprehensive digital twin that provides organizations with new insights, opportunities and automation levels to drive innovation.
For more information on Siemens Digital Industries Software products and services, visit siemens.com/software or follow us on LinkedIn, Twitter, Facebook and Instagram.
Siemens Digital Industries Software – where today meets tomorrow