Future-proof with the IoT miniseries – ep. 1 Transcript
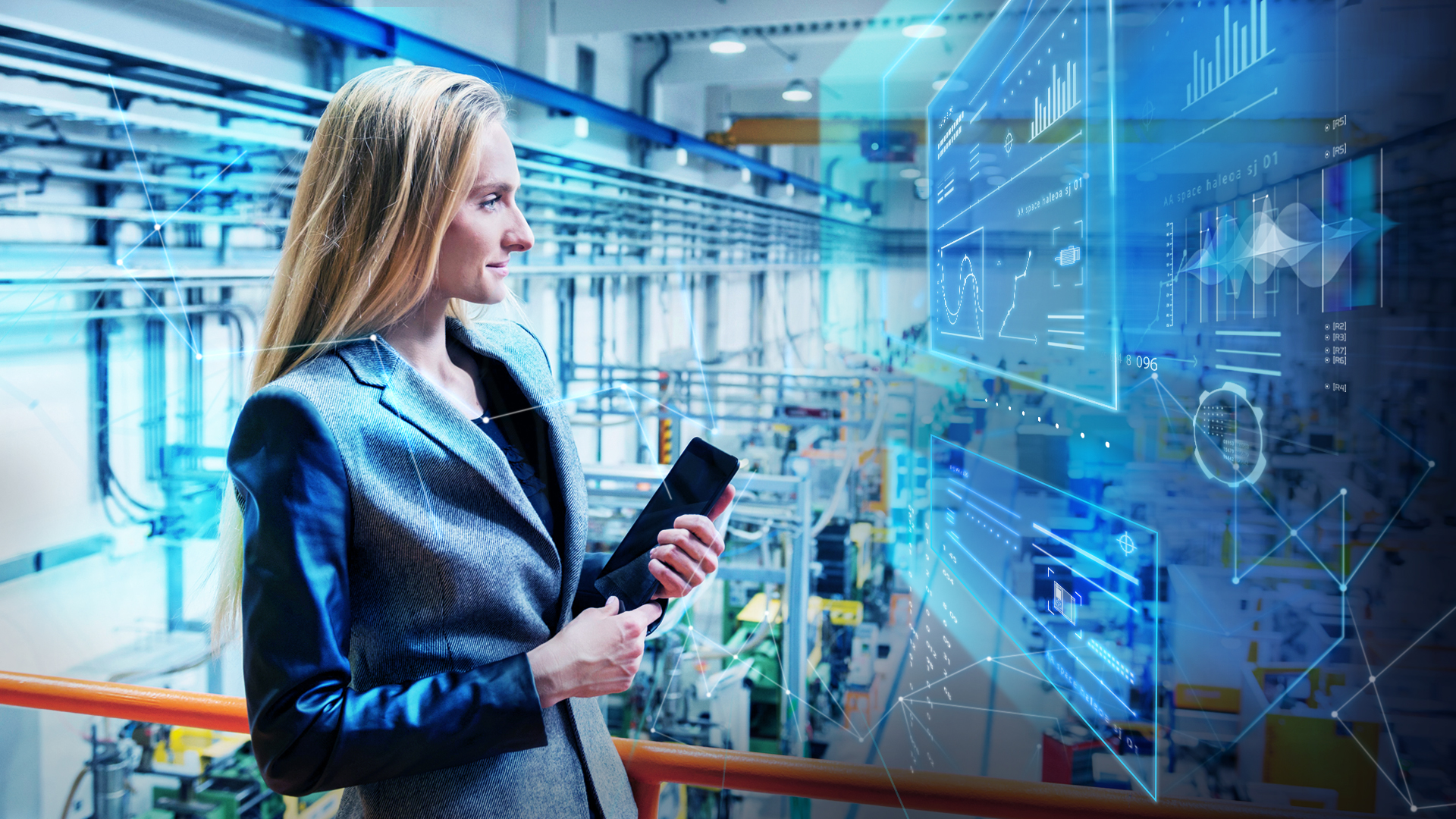
Taking a break from the usual host, Bill Butcher, this miniseries Future-proof with the IoT brings the guest host Jörg Ludwig into an in-depth conversation with Internet of Things (IoT) experts to examine the current trends for the industry’s adoption of the technology. In this first episode Jörg, along with his guests Heiko Dickas, Sebastian Oeder, Colm Gavin and Matthias Lutz dive into two of the largest trends changing industrial machinery – new business models and hyperautomation.
The Digital Transformation is pushing the entire industry into the future and the data produced by IoT devices is becoming the new gold of the industry. Capturing that stream of bits and utilizing it to the fullest potential will become a key differentiator in delivering quality products on time and more efficiently.
And for those inclined to read along, the full transcript of the first episode can be found below the podcast player. Thank you and happy listening!
Jörg Ludwig: Hello! This is “Future-proof with the IoT”, a podcast series that is part of “The Digital Transformation: Solutions for Industrial Machinery Podcast”. This particular miniseries is focused on how to leverage digitalization to overcome manufacturing disruptions and bounce back stronger. I’m Jörg Ludwig, and I will be your special host for this miniseries. Bill Butcher will be back to the podcast after this miniseries.
Today, in our first podcast, we will be talking about the challenges that manufacturing faces in a normal state, and how those escalate when the situation gets worse with an economic downturn, such as the pandemic we see, actually, natural disasters, and so on. We’ll discuss the general trends that were hampering productivity even before COVID arrived.
So, I’m pleased to introduce my first guests, and they are from Siemens Bad Neustadt, an electric motor factory in Bad Neustadt an der Saale, in Germany, that is being developed as a showcase factory for digital applications in metalworking. Welcome, Heiko Dickas and Sebastian Oeder! Can you both, please, explain to our listeners about the factory and your role at it?
Heiko Dickas: Hello, Jörg. My name is Heiko Dickas, and I am the team leader of the digitalization team since the beginning of 2017. Our scope is being an enabler for our production unit in terms of digitalization. I’m with Siemens for more than 30 years in different functions.
Sebastian Oeder: Hello, everybody. My name is Sebastian Oeder. I am head of the production unit main motors in the Bad Neustadt motor factory. I have a background as a production manager at Siemens Energy. And before, I was working for five years as a consultant at Siemens Corporate Technology.
Jörg Ludwig: Thank you both. In the words of Klaus Helmrich, member of the Managing Board of Siemens AG and previous CEO from Siemens Digital Industries, he said, “Bad Neustadt was on a very difficult course 10 years ago and, together, we have succeeded in finding an innovative way that has given the future security. And today everyone can look back with pride on what has changed over the past ten years.” What have been the biggest challenges on this journey?
Heiko Dickas: Indeed, it was a difficult time 10 years ago. From an economical point of view, a lot of employees should have dismissed and so on, and in summary, not the best situation. We were at the point where we had to change some things and had to start different things, completely new. A lot of processes had to be improved, optimized, and maybe also more automized. But first, we had to start with lean shop flow management to kick out waste of our processes because it makes no sense; if you want to digitalize, first, you should have optimized these things, otherwise, you will digitalize waste also. So, in parallel, we look forward, also, where it could help to automate things where possible environments where robots also could support. Therefore, we had to develop a clear vision for the next years: what are our goals in digitalization and automation, but all based on the factory needs. What’s very important is don’t forget the people, you have to involve the people who are impacted by these measures and involved in these measures. And I can have very good ideas for my office view but it could be completely wrong if I want to improve a specific shop floor process, and therefore, involving the people, use their experience, and listen to their needs. The last thing is more a cultural topic as well. In the digitalization world, not everything is clear, from the very first beginning must be allowed also to fail, especially in Germany, sometimes a problem. Here, our former CEO also set up the phrase: “Deliver fast to learn fast.” Start with simple and small use cases. Look whether we had a good result or not, redefine, try again, and so on. But also don’t hesitate to stop things if you see there’s no success.
Jörg Ludwig: Thank you very much for that answer. Our next guest is Colm Gavin. He is Portfolio Development Manager at Siemens Digital Industries. Colm, thanks for taking the time to talk about leveraging digitalization to overcome manufacturing disruptions. With over 20 years of experience in the Siemens Digital Factory, do you think that the challenges that Heiko just explained are something that can be generalized to Industrial Machinery? Do you have any other insights from your career experience?
Colm Gavin: yes, I absolutely agree with the comments from Heiko, that as companies try to improve their automation and optimize their processes that they have to really look to see what’s possible, interesting. Heiko mentioned including people in the process. Absolutely. How do we collaborate with people to bring them on board? Because it’s a journey to innovate with new technology, bring people on board, and find what works as far as approaching this Industry 4.0, everything around that, the new technologies – how do you embrace those new technologies? Finding value and incorporating people at the same time.
Jörg Ludwig: It sounds like there are a few trends that underscore the challenges facing machinery customers; for example, new business models, hyperautomation, low-cost competition, and new generation in the workforce. Machinery has always been about automating manual processes, but now customers are expecting more connected, adaptable, predictable, and extendable machinery. To understand that impact, we should delve a bit deeper into each of those trends that are shaping Industrial Machinery. Before we move on to these industry trends, we still have one more guest to introduce, Matthias Lutz. Could you please explain your role and background at Siemens to our listeners?
Matthias Lutz: I started many years ago within Siemens in supply chain and procurement. And in 2015, I moved on to our industrial customer service organization. It was pretty clear for us that data is the new source of innovation and services. And then, we started to build up our industrial IoT offering today called MindSphere. Since then, I’ve talked to more than 300 customers regarding IoT and use cases. And one thing I want to share with you about my learnings, it’s not about technology on the first hand. It’s more about waste, how to interact with data, and how to enable your organization to come up with new business models and new ways how to interact with your factory.
Jörg Ludwig: Okay, thank you, Matthias. So, it seems to me that data is the new gold. And with your experience helping customers start new business models, in the sense of new IoT business models. Can you explain what they look like, and how are they changing the industry?
Matthias Lutz: What we see currently with Industrial Machinery customers that more and more of their end customers want to buy outcomes, and they want to have new purchasing options, and machine builders need new revenue streams, which, for example, translate into being able to offer anything as a service options. For example, maintenance as a service, or machine optimization as a service. Or you could as well look into use cases around pay-per-use, so why don’t selling, for example, the outcome of the machine and not the hardware by itself, or new leasing options? So, a lot of our customers are telling us: “with IoT, I’m now able to introduce new dynamic warranties, for example, or maybe as well pricing or extensions based on the machine use.” When using data and using platforms to exchange with your customer certain information, certain values, you’re actually able to provide much more differentiated value to the manufacturers, and an ongoing value add to customers that provides a leg up. You cannot start to introduce new business models without doing the extra groundwork, meaning, learning how to connect machines, collect and structure data, and learning how to use this data with actual IoT tools. You have to lay the foundation now.
Jörg Ludwig: So, Colm, have you seen a significant implementation of these new IoT business models in the last years?
Colm Gavin: Yes, and we’ve seen a variety of machine builders of different sizes, try to onboard these new technologies. And I think one of the key things to pick up what Matthias had mentioned is they’re trying to increase their revenues from service. In some cases, the revenues from service will exceed what they actually will get from the basic selling of the machine. But I think what we’re finding is many companies are still trying to figure out the business model for what they would offer for their customers – the service – how to offer it in a way that brings value and also is profitable for them? We’re working with the company Anguil Environmental Systems in Wisconsin – a mid-sized OEM machine builder – and they make very innovative pollution control technologies for water and air cleaning, and so on. One of their goals is they would like to significantly increase their current service base revenues. But they recognize the only way that they’re going to be able to do that is by leveraging IoT technologies to pick up what Matthias said earlier, because without that kind of remote monitoring and predictive maintenance, they’re not going to be able to grow those service-based revenues beyond what they already have. And of course, they have the industry knowledge for their machines, their pollution control machines, they know the valuable data that can be extracted from their machine. So, they have the know-how required. But their IT department doesn’t want to have to reinvent the whole IoT cloud-based system by themselves. So, that’s why they’re partnering with Siemens to help them on that journey. And that’s one thing that’s important is – I’m sure we’ll talk about it in the rest of the podcast as well – what companies are willing to invest in? And how much can Siemens take the load off of their IT departments? So, they just focus on the data from their machines, and how to turn that into value for their customers.
Jörg Ludwig: What about hyperautomation? In Siemens Advanta’s January 2021 list – “What are the expected IoT Trends in 2021?” – it takes the 6th spot, what is it exactly?
Colm Gavin: So, hyperautomation is what we refer to as islands of automation and bringing machines together that may have been separate on their own. How do we leverage the improved connectivity that’s happening between machines to leverage the evolving integration capabilities and open standards? That’s part of it to kind of onboard some of this new technology to push machines and rather than having a fixed production line very rigid, where if you want to embrace flexibility, then the machinery needs to be smart; they need to be able to talk to each other and understand each other. And so leveraging the advanced technologies on communication, so there’s this idea of a smart factory. And one example there would be leveraging AI and Machine Learning so that the machines are able to adapt accordingly.
One quick example of this kind of hyperautomation using AI is AI and vision systems where you have a quality inspection system and you want to verify good or bad on parts as they travel through the system. But in many cases, I’ve been on-site with companies where I’ve seen operators – they will actually turn off the vision system because it’s getting too many false negatives, and too many shutdowns. And what they’re looking for is a way if the vision system through AI can learn, can adapt, and recognize “Well, actually, this is a good part,” and learn from that – so, this being able to teach and adapt machine learning, AI is like an extra muscle, if you like, can help bring the machine beyond its current capabilities without a complete rehaul of the design.
The other common way we see AI/ Machine Learning as part of, say, hyperautomation, another example would be cameras at the end of robot arms for pick and place. And this is where we see a convergence of the different technologies, ERP systems, MES systems, and automation coming together. So, in many cases, when you program a robot, it will have a fixed path that it’s doing the same thing all the time. But being able to teach a robot that it has to recognize “Well, you need to pick up these different parts at this time or that time, different sizes, how do you grab them?” That’s combining cameras with AI so the robot can dynamically grasp different parts and maybe have different paths that needs to place the parts based on what it’s picking. That is a whole other level of automation, where the robot is basically changing its path on the fly, and AI is telling it what to do. Those are, for me, some of the best examples for this hyperautomation; bringing systems beyond what they’re already able to do.
Matthias Lutz: But based on my experience, IoT is not all about the next level of automation. Of course, it leads to better automation, but for this trend, it’s about getting accurate transparency into machines and monitoring their health – to improve run-rates, decrease downtime, improve revenue by decreasing scrap, and much more than this. I think it’s as well about to build a system of systems, so, making machines able to talk to each other. Hyperautomation responds to the continuous advances in technology and customer demand for customization. It means to deliver a much more personalized experience with flexible machine lines, and eventually optimize the user productivity. Much more than that, as well, to get products to market faster by reducing costs and improve quality. I had a pretty interesting customer conversation, and they said to me: “I’m designing my machine with the best in class design tools. But once my machine is out there in the field, I’m not able to use this data unless I’m getting some service request with hyperautomation.” So, meaning the connection between different systems in the automation chain, these customers will be in future able to use IoT to actually funnel in the real-life data from the Internet of Things system into their design systems and to iterate their product in a much more efficient and faster way.
Jörg Ludwig: And that completes the digital twin, by the way. Heiko or Sebastian, Siemens Bad Neustadt is in the process of getting fully digitalized starting the journey ten years ago. Can it be labeled as a pioneer, a trend-setter in hyperautomation? How and when did it start? And how has it ramped up to get there?
Heiko Dickas: For me, it’s unclear whether we are a trendsetter in this way, maybe this can be ready to throw somebody out of the factory even better. But we are working constantly on infrastructure and use cases for many years. We set up the environment and the frame where we think we can progress very fast; therefore, we have a clear vision, strategy, roadmap also pushed by our former CEO, Dr Heuring, he always said and it’s a quotation from him, “Patience is not required at digitalization.” This means, again, also, deliver fast to learn fast. Try something new even if it fails. So, we started with a few split heads years ago, where we met once a week to discuss digitalization topics but the progress was not very fast; therefore, maybe half a year later we decided to found a specific department which takes care of the requirements coming up with digitalization. Now, more or less 10 to 15 persons are working on digitalization, automation use cases in Bad Neustadt constantly. With this structure, we increase the contribution on our yearly productivity goals at the shop floor. And one part is also to automate more and more in different areas. But, Sebastian, what is your view on this thing?
Sebastian Oeder: Yeah, if we talk about the shop floor, that’s where I step in. Honestly speaking, we did not use the term hyperautomation so far. But as I understand the meaning behind the trend, I can state that we have our hyperautomated systems in place, I just would like to give you some examples. In the production of main motors, we have automated several production steps by using assembly robots. We also automated final test systems for electrical and mechanical tests. For this test, we are using an AI that continuously analyzes test results and reduces test steps based on an algorithm for our automated systems as well as for our conventional machines. We use condition monitoring to analyze and reduce downtimes. Performance management is in place for logistic data like output and lead time. We also use it for detailed process analysis, for example, to monitor the joining forces of our stator and the winding. The sequence of orders is system-based to optimize setup efforts, and a big portion of our material is delivered from or to the production line by an AGV. Another example from our pre-production is a fully automated machine tool that performs the entire setup autonomously by using a camera system, Edge, and AI. So, I don’t know if we are a trendsetter, but for sure we have some really cool use cases in place.
Jörg Ludwig: This really has been cool is to have you all in this first episode of the special mini-series “Future-proof with the IoT”! Unfortunately, we are out of time today! But in the next episode we will keep talking about the challenges in manufacturing and, especially, about the trends of low-cost competition and new generation workforce. Take care and we hope to have you again!
About the Host and Guests
Jörg Ludwig – Since 2018, Jörg has been in the sales enablement team for MindSphere and since October 2020 also for Mendix, globally responsible for the creation of learning paths, enablement sessions, and value selling trainings and workshops. Prior to Siemens, Jörg ran his own business as a Value Selling trainer and coach for more than 7 years. He gained Sales experience and expertise from over 16 years in global Software Sales organizations.
Heiko Dickas – Heiko is the Team Leader of the digitalization team since the beginning of 2017 in the Bad Neustadt motor factory. His scope is being an enabler for the production unit in terms of digitalization. Heiko has been with Siemens for more than 30 years in different functions.
Colm Gavin – With over 20 years of experience in the Siemens Digital Factory, Colm works on business development for digitalization topics as they pertain to Siemens SW and Factory Automation, specifically virtual commissioning, Industrial IoT, Industrial Edge and AI topics.
Matthias Lutz – Matthias joined Siemens 14 years ago, starting in supply chain and procurement department. In 2015, he moved to the industrial customer service organization, focusing on industrial IoT and digital services.
Sebastian Oeder – Sebastian is Head of the production unit main motors in the Bad Neustadt motor factory. He has a background as a production manager at Siemens Energy and as a consultant at Siemens Corporate Technology.
Siemens Digital Industries Software drives the transformation to enable a digital enterprise where engineering, manufacturing and electronics design meet tomorrow. Xcelerator, the comprehensive and integrated portfolio of software and services from Siemens Digital Industries Software, helps companies of all sizes create and leverage a comprehensive digital twin that provides organizations with new insights, opportunities and automation levels to drive innovation.
For more information on Siemens Digital Industries Software products and services, visit siemens.com/software or follow us on LinkedIn, Twitter, Facebook and Instagram.
Siemens Digital Industries Software – where today meets tomorrow