Additive Manufacturing – first time-right printing solutions – webinar
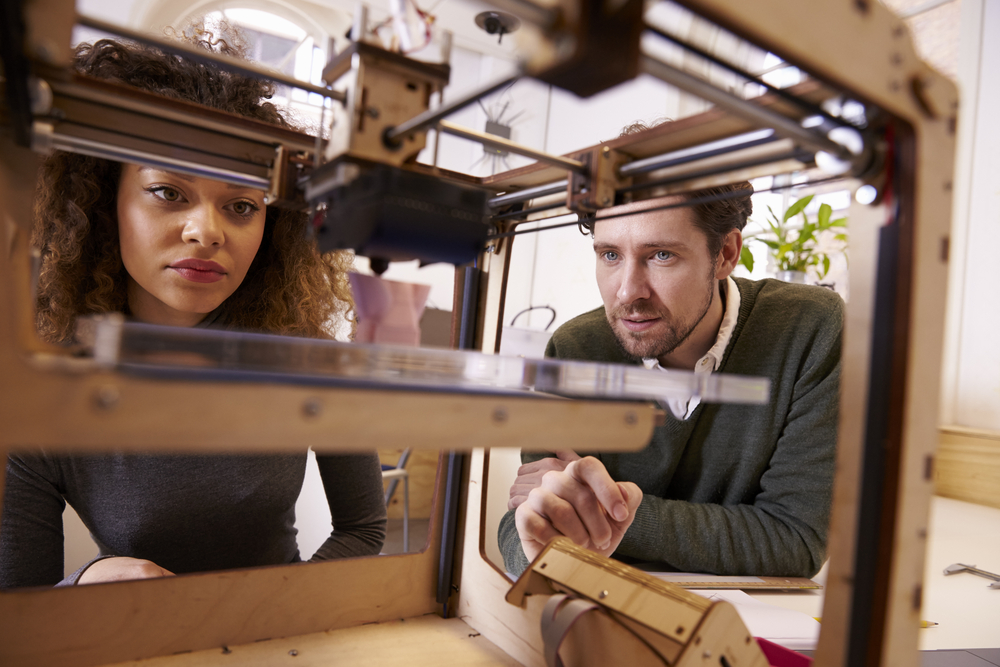
Companies are producing parts using additive manufacturing or 3d printing, which can accompany challenges across the digital thread. These organizations need to understand how to assess designs for printability while avoiding print failures. Also, they must detect and mitigate issues during production. All these factors feed into the ability to produce quality parts on time and at scale using Digital Part Production and adopting additive manufacturing technologies.
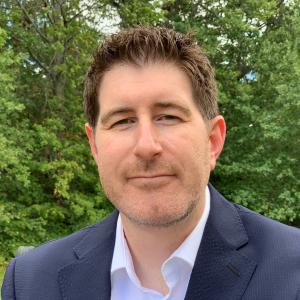
Joining us in this webinar is Ashley Eckhoff, Marketing Manager for the Manufacturing Engineering Group at Siemens Digital Industries Software, with over 20 years in various capacities. He has spent the past several years deep-diving into additive manufacturing in both product design and marketing roles.
> Listen to the webinar.
Additive manufacturing – adopting innovative software
In the last decade, additive manufacturing is one of the most talked-about innovative technologies to come to the forefront; however, companies face a few issues when adopting it. Companies producing parts using additive face challenges across the digital thread, and these organizations have questions of every step along the way, so they need to understand things like how do they assess designs for printability? How do they avoid print failures? How do they detect and mitigate issues during production? And then, of course, all these questions feed into their ability to produce quality parts on time and at scale.
The focus of this webinar is metal printing. Conversely, a failed plastic print can cost a few hundred dollars, whereas a failed metal print runs into tens of thousands of dollars. Therefore, the penalty for failure is significantly higher with metal. Many things can go awry, including a re-coater collision or a microscopic defect within the structure of the part. “These issues manifest themselves in different ways from parts that are outside of tolerance due to distortions, to surface finishes that are subpar, to actual part failures in the field due to structural weaknesses,” says Ashley Eckhoff. Subsequently, each problem equates to a loss of time and money.
Additive manufacturing – getting it right the first time
A company’s knowledge of additive manufacturing on this acquisition journey is essential. Pertinent factors come into play in this journey. Firstly, for the apprentice, article parts are failing by over 40 percent. The use of varying support strategies can solve these build failures, but this is often inefficient due to inexperience.
The more experienced journeyman faces a 30-40 percent failure rate on the first article builds of a part or group that is nesting multiple geometries together. The focus is on surface quality and post-processing management but still using supports to fix build problems. Also, they may try to adjust the orientation, rotating things around the Z direction to alleviate major problems like re-coater collisions.
The master additive engineer uses simulation to tune the different SERP process parameters by solving issues like shrink lines, distortion and porosity. The first article build failure rates are usually less than 20 percent. The additive process for their hardware is clearly understood, and they’re driving a higher return on investment for their processes. However, moving up this learning curve organically in a traditional fashion takes a time investment. Therefore, successful companies are looking for ways to short circuit that process and leap ahead in their experience level with minimal investment in money and time. Software is the answer. Applying the right software via additive manufacturing, by experience level and need, augments the natural knowledge acquisition process, allowing a quicker path with a better return on investment.
Additive manufacturing – the cost
The upfront costs for additive manufacturing include acquiring the machinery, the materials necessary to print and hidden production costs, contributing to knowledge acquisition cost. Therefore, even with a failure rate below 20 percent (master level), there’s still a one in five printing failure rate. So, the cost for materials and time will factor into the price of the customer part.
Furthermore, trial prints and testing are at an ongoing cost. When acquiring a new machine or beginning to support a new material, a company introduces numerous rounds of testing into the process. As a remedy, a company must limit the support of several technologies and materials; however, this limits the scale of the business. For example, if a company focuses on selective lasers with titanium, it can’t service a customer who needs aluminum.
There is a myriad of factors to consider when adopting additive manufacturing.
Learn more by listening to the webinar.
Software solutions
Siemens Digital Industries Software drives the transformation to enable a digital enterprise where engineering, manufacturing and electronics design meet tomorrow.
Xcelerator, the comprehensive and integrated portfolio of software and services from Siemens Digital Industries Software, helps companies of all sizes create and leverage a complete digital twin that provides organizations with new insights, opportunities, and automation levels to drive innovation.
For more information on Siemens Digital Industries Software products and services, visit siemens.com/software or follow us on LinkedIn, Twitter, Facebook and Instagram.
Siemens Digital Industries Software – where today meets tomorrow.
Related links
Listen to the DPP Podcast on additive manufacturing.
About our expert
Ashley Eckhoff is the Marketing Manager for Siemens Manufacturing Engineering group, concentrating on Additive Manufacturing. He has a background in engineering and has been with Siemens for over 20 years in various capacities. He has spent the past few years deep-diving into additive manufacturing in both product design and marketing roles.