Do you feel it? We’re in a pivotal moment in aviation.
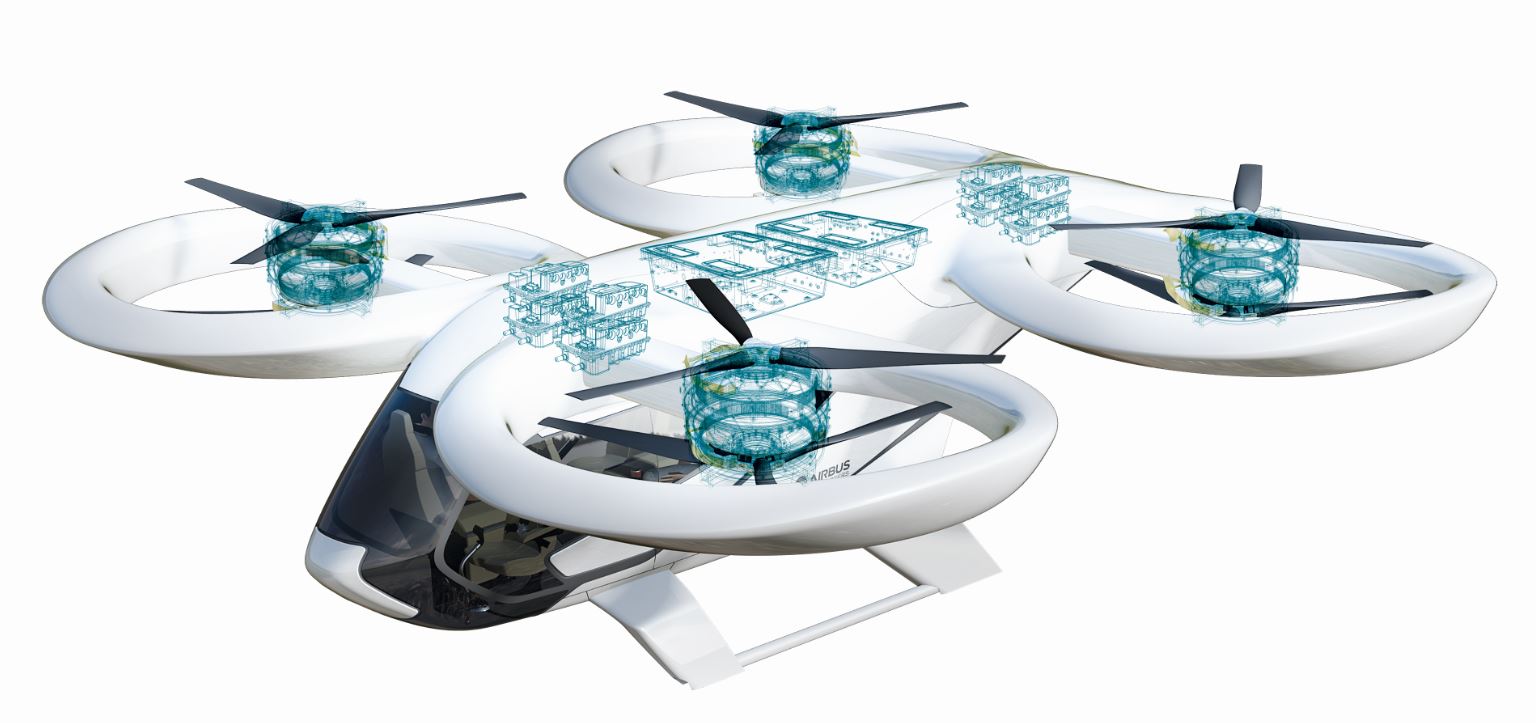
It must have been 15 years ago, a former Belgian Air Force C-130 pilot told me “When you want to see innovation, don’t visit the big aerospace shows, go to the aeroconferences in Friedrichshafen.” Of course, as a young engineer somehow blinded by the bling and noise levels of big airshows, I never invested the time to add this general aviation show to my development list.
It took me until 2016, when I joined my colleagues from Siemens eAircraft (now Rolls-Royce Electrical) to finally attend the aero conference and yes, you guessed it, in Friedrichshafen, Germany.
At that time, the show highlighted small and larger initiatives around electric aviation. It was the time when Dr. Frank Anton from Siemens eAircraft, together with his young and high-potential team, not only showcased some mock-ups of electrical motors but also flight demonstrated the full electrical Extra 330LE acrobatic aircraft.
From that moment in 2016, the show has focused more heavily on electrical aviation, and today we’re seeing urban air mobility (UAM) concepts mature with companies such as Volocopter.
Recently, I had the honor of appearing on the Siemens A&D podcast Talking Aerospace Today. The current series is focused on innovation in aviation. In my episode (which you can listen to below) I talk about the dynamics behind electrical propulsion in both traditional aircraft as well as in UAM vehicles. The only way to master electrical propulsion is to take into account the many disciples behind the physics and the domains needed to design and build…
Increasing power density of electrical machines
When you have experience in electrical machines, which Siemens has, you realize that the traditional electrical machines are too heavy to implement on aircraft. Indeed, when looking into the traditional electrical motors for industrial applications or for trains, you can roughly guess that they have a power density of 1kW/kg, meaning that for 1kg of machine, you get 1kW of mechanical power at the shaft.
In order to make electrical motors “flyable” power density needs to increase by at least one order of magnitude. Early studies in Siemens estimate that, depending on the aircraft and its mission, electrical propulsion systems need to reach 10 to 15 kW/kg.
Siemens eAircraft developed motors that at time had a record-breaking power density of 6kW/kg (RRP260D). They were not only machines that ran on testbenches, but these beautiful machines were also taken to the sky and Rolls-Royce Electrical has accumulated an unseen amount of flight test hours in a certified environment. Examples include the Magnus aircraft, Bye Aerospace aircraft, the Extra aircraft and also the CityAirbus.
eVTOL – the potential disruptor for the helicopter market
I strongly believe the examples I mentioned in the previous paragraph represent a pivotal moment. Indeed, the new “design” freedom with electrical propulsion units allows us to look into drastically new aircraft concepts, configurations and – most importantly – new business models.
Who would have predicted ten years ago that an entirely new market would emerge? Indeed, the urban air mobility (UAM) market is today looking into electrically-propelled versions. Significant research money has been invested in electrical vertical take-off and landing (eVTOL) systems, with over 230 initiatives worldwide according to Roland Berger, of which there are at least 95 UAM initiatives alone.
The fact that electrical motors are mechanically more reliable, easier to integrate and easier to maintain will have a huge impact on the Total Cost of Ownership (TCO) of these eVTOL UAM vehicles, hence these configurations have the potential to disrupt the lower end of the traditional helicopter market. Indeed, 50 percent of the traditional helicopter TCO is the maintenance of the very complex and fragile rotor-drive-and-control system, which requires so much attention to keep it safe to fly. Add to that 25 percent of the TCO is the crew, where the UAM industry also has ambitions to reduce the crew from two to one and maybe zero pilots in the future.
Electrical propulsion units while compelling, represent significant engineering challenges
The electrical propulsion units might be more reliable and easier to maintain, but when increasing installed electrical power with increasing power density and energy density, a lot of integration problems occur.
Increasing the motor electrical power while taking away mass from electrical motors results in challenges related to thermal management. Electrical machines generate a lot of heat. Also, when taking away structural mass, one influence becomes the stiffness of the motor, which can result in dynamic deformations which in turn, compromises the electromagnetic performance of the stator/rotor.
Additionally, although we live already in a world of “More Electric Aircraft” like the beautiful Boeing 787 and Airbus A350, electrical propulsion systems require a whole new level of required installed electrical power. Voltage levels of the electrical buses, along with current levels will go up, unseen in modern aircraft configurations.
Indeed, one can categorize the electrical systems of today’s aircraft as low-voltage and low power. Boeing indeed made a step to install approximately 1MW of power.
These high voltages and high currents will require completely new development methods and verification. The integration of the electrical systems will not only generate thermal integration problems but also the configuration of the electrical harnesses – the way a harness runs through the aircraft will create electromagnetic integration problems.
“It requires a careful engineering balancing act to secure all mission-critical aspects.”
Add to this that for UAM systems, low noise levels generated by the vehicle will be of capital importance to make its integration in urban areas acceptable. Electric motors as such don’t create a lot of noise, however, the propellers that need to create the required lift create significant downwash and noise.
Making UAM systems affordable and assuring low-cost operations while operating in a certified and safe context is another major challenge. Add to this the desire to make these systems automated (with fewer pilots in the loop) and integrated into traditional controlled airspace will also require significant investments and technological evolutions.
It requires a careful engineering balancing act to secure all mission-critical aspects.
Because the configuration of the UAM aircraft will change drastically, the current development tools and processes will fall short of what’s required as the industry moves forward.
Virtual integrated aircraft – fly it before you build it!
Reaching record-breaking power density can only happen when using a pervasive digital development approach. You can only develop these high-power density systems, when you understand in an integrated way, how the different physics of the system interact with each other. So it is not only about whether you can model the structural side, the electro-magnetic side, or the thermal side of the batteries, inverters and motors, it’s also about how do you comprehensively capture the interactions between these domains?
Siemens’ comprehensive digital twin technology is used to model the physical behavior of the motors, while Siemens’ digital threads keep track of the development workflows, traceability of engineering decisions and verification actions.
More specifically, Siemens Simcenter Aircraft Performance Engineering solutions allow teams to model, gain insight, understand and optimize the physical behavior of all elements of the eAircraft EPUs. It allows teams to model in detail the aerodynamic, fluid and heat transfer behavior, providing insight into the structural and dynamical performance. Simcenter has different modeling technologies to model all aircraft systems in a very scalable way, from component level all the way to integration at the aircraft level. Covering low- and high-fidelity physical representations, in support of all development phases from early concept and trade-off studies to detailed design and into the verification phase, covering the multiple physics and disciplines are important in such complex systems.
For more information on Simcenter and the electrification of an aircraft – and how a digital development approach can help teams in all facets of development, I urge you to read the blog “Digitalization for aircraft electrification.”
But it’s more than just modeling physical behavior. Finding the optimal design for an eVTOL mission requires close integration with how the mechanical product is defined (mechanical CAD), along with the electrical system definition (ECAD) which requires tight links to the behavior. And then, of course, there’s the abundant amount of software lines that will be needed to have a safe and comfortable flight.
Conclusion
In the previous episode of Talking Aerospace Today my colleague, Durrell Rittenberg, talked about how simulation is the great equalizer, allowing young engineers and start-up companies to completely rethink aircraft configurations enabled by electrical aircraft propulsion systems.
Great things are happening today. Teams are progressing at incredible speed to build new aircraft systems that have the potential to disrupt a good part of the current aerospace business. These teams that are leading the way all have one thing in common: they are using pervasive digitalization to design, engineer, manufacture and orchestrate their program. In fact, you might be interested in a white paper that talks about this very topic. I urge you to download “Innovate the Future Aircraft: Rethink Next-generation Aircraft Engineering.”
I’m convinced we live in a pivotal moment where young engineers are focused to find solutions for their dreams.
And as young engineers were key in the successful development of the Apollo Project, where the complete Saturn V stack, including the Moon Lander and the Command Service module, was developed in merely seven years, including drastic new technology like the Apollo Guidance and Navigation computer, I see that key players in electric aviation count on the energy, enthusiasm and smartness of young engineers, supported by Siemens’ Xcelerator which includes our digital twin and digital thread solutions.
They will be successful and they will change our society! Please take a moment and listen to the podcast as I go into great detail on eVTOL power density and thermal management.
Thierry Olbrechts is the Director of the Simcenter Aerospace Industry Solutions. Thierry has 23 years of experience in the aerospace industry, responsible for the Siemens Simcenter Aerospace strategy, business development, research and go-to-market. Most important though, Thierry is extremely passionate about aerospace engineering.