A perfect match – Model Based Definition and AM
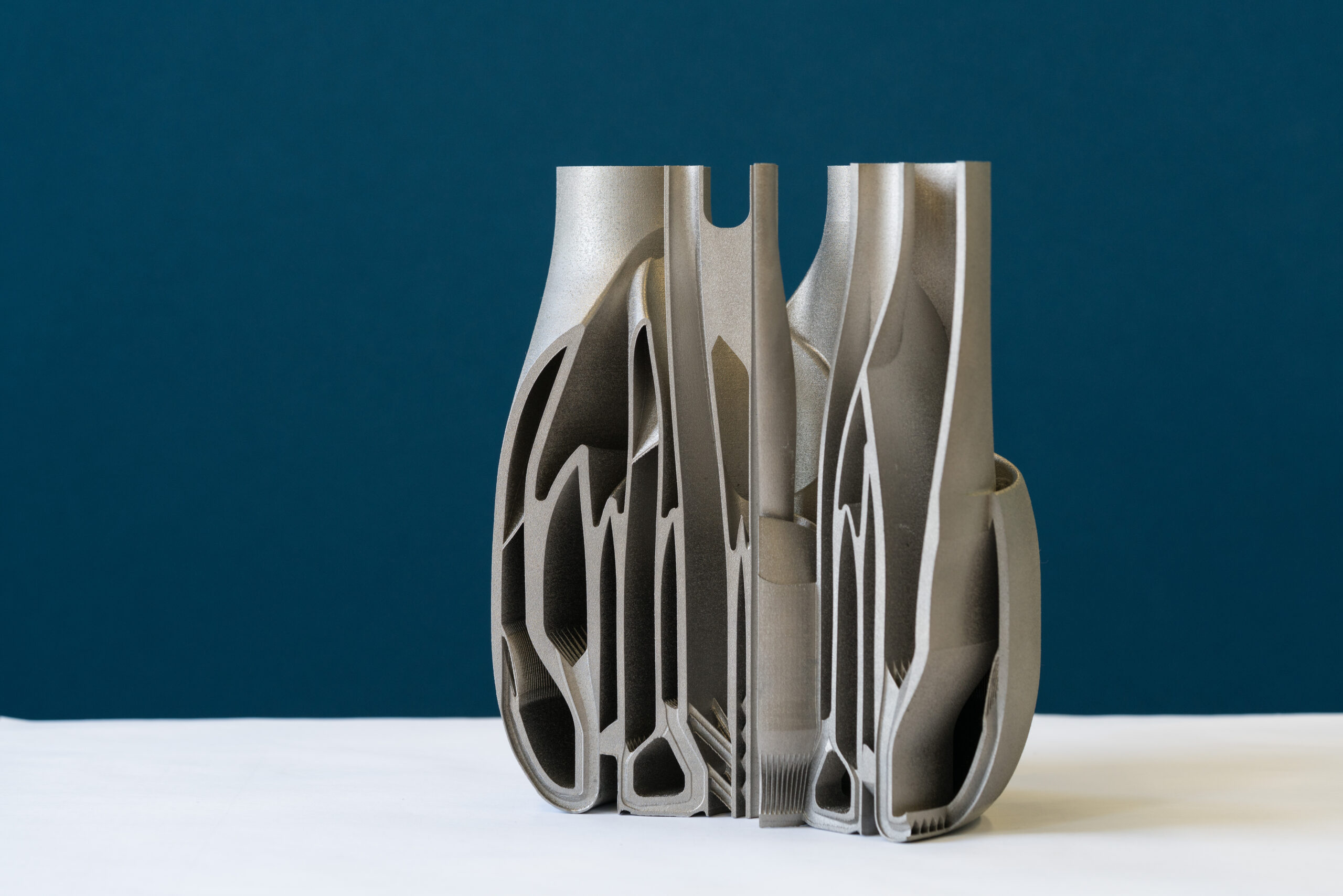
Additive manufacturing (AM) sits in a unique position for industrial scale applications. Entire systems can be compressed into a single part, as AM does not require complex molds or the removal of material that would inhibit such designs, but these geometries are not easily compatible with traditional CAD workflows. Surfaces for AM are more likely to follow complex curves than simple planar geometries. Fortunately, the CAD capabilities are always evolving, to ensure benefits of AM will continue to expand. This is exactly what happened with NX™ Software’s latest update – part of Xcelerator, the comprehensive and integrated portfolio of software and services from Siemens Digital Industries Software.
With an emphasis on Model Based Definition (MBD), engineers and designers will be able to work with the solid body itself rather than auxiliary geometries in defining a design. For more information on how this is changing product design please read this blog on MBD, but here we will examine the benefits for AM.
Though not strictly dependent on MBD, AM design benefits from the ability to use the 3D model as the single source of truth. 3D models for AM often need to retain information beyond what are already complex geometries for traditional manufacturing that could be in the form of lattices for light weighting or ribs for rigidity. When these designs go to print, their quality needs to be ensured as well. The cost, through time and material, can be high if a print comes out deformed. To create high quality parts, the AM process requires careful thought and consideration from concept to production – ensuring the component is printable and that it can be printed right, the first time and every time.
Algorithmic modeling
The additional value of AM combined with MBD is evident in a common design technique of the aerospace industry, iso grids. Used for structural rigidity without increasing surface thickness, iso-grids are often applied to thruster and rocket nozzles in a repeating pattern of the surface. With traditional techniques, these are added after constructing the base component by carefully welding the ribs to the surface. But with AM, these structures can be added directly to the model and printed at the same time or added by the aid of a direct energy deposition AM device more rapidly and precisely than welding.
These and similar structures are not new, but they are labor intensive for an engineer to implement – requiring tedious manual modeling and complex programming to apply the structure. With algorithmic modeling, the structure can be produced with predefined rules right in NX. This not only reduces the specialized knowledge needed to implement the design, it makes an associative connection to the attached surface and can be updated as the design changes, without recoding the geometry.
Convergent modeling
Aside from the advancements in additive manufacturing design, convergent modeling is the most relevant update in NX for AM workflows. One of the most common reasons to use AM for a component is to achieve either an organic geometry or one produced from topology optimization. Both tend to create geometries not producible with traditional manufacturing methods, either due to thin wall structures or layered cavities as seen with the ‘fennel bulb’ burner. This leaves designers and engineers to work with mesh bodies, traditionally difficult or sometimes impossible to integrate with precision CAD geometries.
The NX update changes that. Mixed geometries integrate both mesh bodies and CAD solid bodies. Users can even replace faces on a mesh with precision CAD geometry in a couple clicks, to enable continued refinements and additions as seen in the video. This could be revolutionary for reverse engineering parts to fit in an updated assembly or retrofitting a system with open-sourced topology optimized designs.
A great step for the future
Additive manufacturing will be a very important aspect of manufacturing of tomorrow but getting there will require work on behalf of users to design with AM’s benefits in mind and on behalf of software companies like Siemens to improve support and viability of the workflow. This update to NX is a step in the right direction, both improving the general process of AM, in Additive Manufacturing Design and through feature expansions benefiting tremendously from AM’s capacities like Algorithmic Modeling. For more information on the new update or to learn more about the possibilities of AM, please read Engineering.com’s coverage or our website.