Podcast Transcript: Additive manufacturing – an industrial revolution (Part 5) – the future of AM
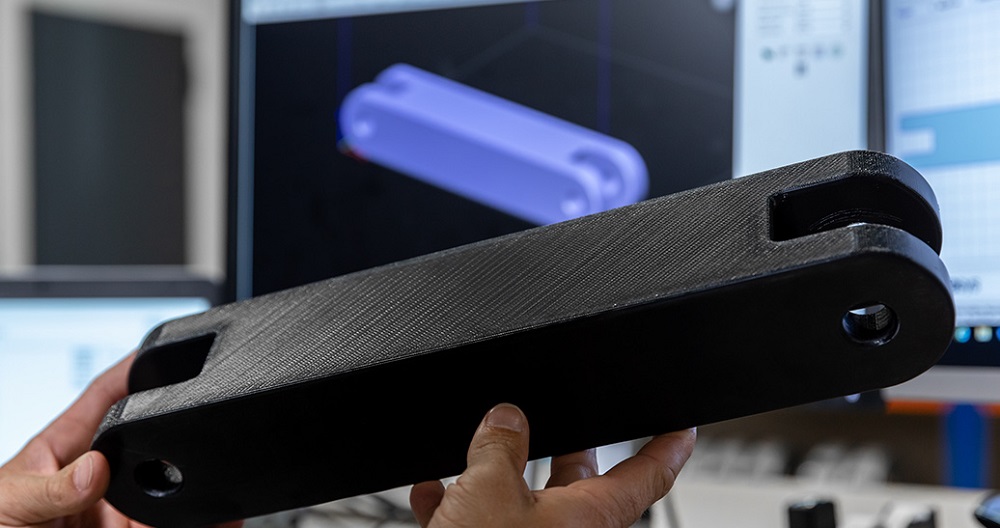
In our recently published fifth podcast of our new additive manufacturing podcast series, we are joined again by Aaron Frankel, vice president of Siemens additive manufacturing software program.
Additive manufacturing is a greenfield of opportunity. Everyone is starting at the same level, providing a game-changing impact for numerous industries to help companies transform their products to the market and reinvent their manufacturing process, supply chains and production. Subsequently, companies achieve a new type of business model. The potential, combined with the numerous industries, allows engineers to develop and offer new capabilities and solutions..
Read the transcript, below, where Ashley Eckhoff is discussing the future of additive manufacturing with Aaron Frankel. Also, you can link to the audio podcast.
Read the Transcript
Ashley: So, Aaron, I understand we have sort of a showcase for additive – it’s called ‘The Additive Manufacturing Experience Center’. Can you walk us through what that is and how people might be able to get involved?
Aaron: If you’re interested in learning about additive manufacturing (AM) and its benefits and combining your interest with an end-to-end process chain (from idea to finished part), then I recommend you visit our Virtual Additive Manufacturing Experience Center. The virtual center is based on a physical center that resides in Erlangen, Germany. It’s hosted by Siemens and a great team of experts in additive manufacturing, who are familiar with the different AM technologies and our digital thread and software to design and develop digital twins to design optimal parts that perform better, producing them using additional equipment. You’ll gain insights into different AM technologies for both polymers and metals (large and small scale) with several applications developed by Siemens and our customers and partners. We can provide a URL to register to attend the event or take a virtual tour, and we’ll team you up with an expert who will be able to introduce additive manufacturing and what Siemens has to offer to help you industrialize it in a superior virtual experience.
Ashley: Can you tell us what they’ll see there? Are there machines? Is there software running? How does it all work?
Aaron: Yeah. You’ll be able to see our software, including all the different applications that we have to offer – from design to generative engineering to build preparation and build process simulation onto the shop floor with manufacturing and execution, including the ability to collect data off machines. You’ll also be able to see a plant simulation model of an additive manufacturing factory producing hundreds of thousands of parts. You will see robots doing large-scale FDM (fused deposition modeling) processes, a DED process for metal and gain some insights into HP multi-jet fusion technology. So, you’ll be able to see a broad spectrum of both software and hardware when you visit the site.
Ashley: Awesome!
Ashley: I know you’re a very passionate person about additive manufacturing. What is it about additive that attracts you? What gets you excited about technology and how it works?
Aaron: I love the fact that it’s a greenfield — it’s brand new. it’s so very rare that you get to work on a technology where everybody’s at the same level of knowledge — learning together, starting from scratch. That is why I love it because I get to be with all these smart people. So, we are figuring it all out together, and that, to me, is amazing!
I’m excited about additive manufacturing because it can have a game-changing impact on numerous industries, if not every industry. It can help companies transform the products they offer to the market and change their manufacturing process, supply chains, and how they produce products. It also helps companies achieve new business models that are transformative with value to be gained by the company that delivers and offers that business and to the customers that takes advantage of it.
You need to think about design tools and consider what we need to develop from an engineer and simulation perspective, considering manufacturing, production, and data analytics. We now have tools at our fingertips that can allow us to reimagine products in a digital environment and, almost with the push of a button, to realize them on a 3D printer. The potential of that ability is exciting. This is what drives me to wake up in the morning and jump online and see what’s going on and work with a vast community of experts with in-depth knowledge in all kinds of different disciplines, so I’m continually learning.
Ashley: We have talked a lot about various products that help with additive, but we also know that customers face many different challenges when adopting additive. What are some of those challenges that you’ve heard customers discuss?
Aaron: Companies struggle with several technical challenges that are holding them back from scaling up to additive for production use – and they’re facing these areas all across the process, from idea to service. Our vision for additive manufacturing is a direct result of the feedback that we’re receiving from customers about these challenges. We are looking to address and solve their most challenging problems. These challenges are in design, virtual product, and virtual production, realizing the parts that they need to produce and service those parts.
Some of their questions include:
- · How do we know if a part is viable for additive manufacturing?
- · How do you design the ideal functional part?
- · How do you tap into the huge, costly, potential of producing parts with different materials?
- · How do we ensure that our parts can be qualified?
- · How do we minimize the high-failure rate of 3D printed parts?
- · How do you scale up the volume to hit the demand for the parts and the quantities of parts asked to produce?
- · How do you orchestrate production in an additive manufacturing factory that not only requires 3D printers but post-processing equipment?
- · How do you connect all of the different pieces of equipment on the shop floor for additive?
- · How do you automate and improve additive manufacturing factory efficiency?
- · Can you detect when a problem occurs on the printer, and what can you do about it?
- · Can we collect data from the machines to analyze the process where parts are being produced and determine the quality in line during the part production?
All these questions sum up to the bigger question: how can we deliver quality design for additive parts on time and at scale?
As we work with our customers and develop solutions, including the projects solving the solutions, we work with them to ensure that our solutions can deliver value to parts and geometry types. Then we confirm that we will answer these challenges using industrial-strength capabilities. We ultimately enable our customers to use additive manufacturing in a production environment.
Ashley: So, let’s pick a few of these customer challenges. I know we focused on a couple of these in some of the presentations you’ve done. How can we avoid the high-failure rate of 3D printing? And, how do we tap the vast but costly potential of materials?
Aaron: Additive manufacturing delivers tremendous value when companies use it to produce new designs, offering greater functional and personalized benefits. To provide enhanced operational performance, simulation-driven design tools effectively help engineers automate the engineering of parts and their shapes to achieve specified target performance objectives. We’re offering simulation-driven solutions to automate the design and engineering of parts that can be optimized not only for mass and strength but also for thermal and flow characteristics.
We’re also working on ways to combine performance with production cost and material utilization optimizations, which I think will impact the ultimate performance of the product in an economical way. Also, it’s important to point out that sometimes, to leverage these capabilities, you must define it within the context of what you want the system to create and engineer. This is a digital representation of the product that we can design using existing CAD assemblies in many cases. However, sometimes the engineering community designs an optimal part for a product where we don’t have the CAD geometry, so we provide exciting tools to do reverse-engineering, thus scanning products to determine the design envelope that the part needs to reside within. We can then apply these same automated capabilities to come up with the design and the shape that will deliver those target performance objectives.
Ashley: Aaron, we help people design these ideal functional parts, but I’ve heard a lot of people talk about qualification. So, how do we help our customers ensure that AM parts are correctly qualified?
Aaron: This is undoubtedly a challenge in the industry. Audi recently published a paper about a metal additive manufacturer part that unexpectedly failed in an unpredictable place. I think the ultimate question is, how can we avoid this type of unforeseen failure? We are working on some new technology – additive manufacturing durability solver that I believe will begin to solve this problem. We are training a machine-learning algorithm to predict fatigue properties for combining material, loading conditions, print, build orientation and heat treatments.
Moreover, we’re developing a new solver accounting for local features like the surface roughness and the material properties. Then, we’re combining all of this information and predicting the melt pool’s impact on the local microstructure of the part while it’s being built. We are displaying and generating this information on a finite element mesh model to see and visualize a map of the results to determine where the part might fail.
It’s a complicated solution to consider the design, the material, the process, the post-processing and visualization of the results of the combination of these inputs. But I think it’s one of these types of capabilities that is necessary to unlock the additive’s further adoption by giving designers and engineers upfront confidence to know that the design and the print process will yield the part and the part’s performance once it’s produced. So, indeed, a fascinating area and field that combines different aspects of design, simulation and manufacturing into an integrated solution.
Ashley: I would like to thank Aaron Frankel for joining me today and the Siemens Thought Leadership team to sponsor this webinar.
Siemens Digital Industries Solutions Software, through its Xcelerator portfolio, provides a breadth of many capabilities, including collaborating with experts to overcome the challenges of adopting additive manufacturing to fully gain its benefits.
This is the fifth podcast transcript in this series on additive manufacturing. A sixth podcast will be forthcoming.
For more information:
Listen to this fifth podcast in the AM series to learn more about this engaging topic.
Also, you can access this podcast via Apple, Stitcher, Spotify, Castbox, TuneIn or Google.
About our experts:
Aaron Frankel is vice president of Siemens additive manufacturing software program. He has over 20 years of experience in the PLM software industry and has held various positions in engineering services, product management, and marketing – all focused on helping manufacturers take advantage of the latest digital design and manufacturing technology.
Ashley Eckhoff has a background in engineering and has been with Siemens for over 20 years in various capacities. He has spent the past few years deep-diving into additive manufacturing in both product design and marketing roles.