Podcast Transcript: Additive manufacturing – an industrial revolution (Part 2) – customization, simulation, the future
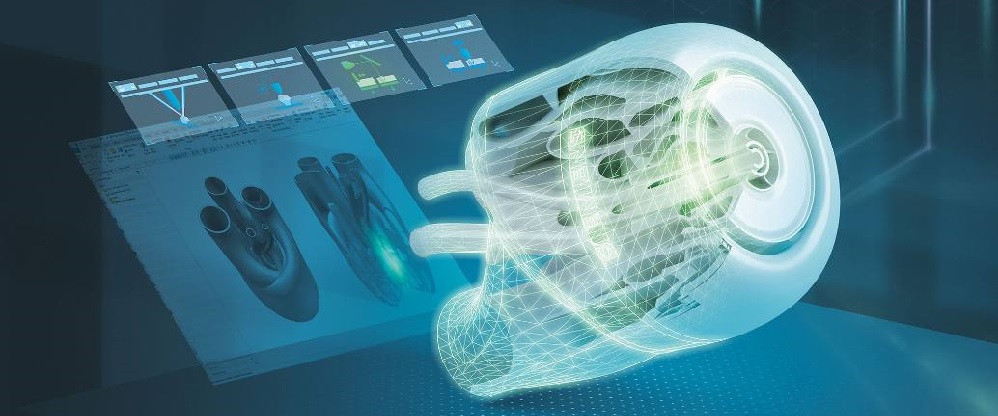
In this second podcast transcript of our new additive manufacturing podcast series, hosted by Ashley Eckhoff, marketing manager at Siemens Digital Industries Sofware, he continues to converse with our special guest Aaron Frankel, vice president of Siemens additive manufacturing software program, discussing personalization, customization and optimization.
The audio portion of this second podcast was previously posted to the Thought Leadership Community. You can connect, below.
Read the Transcript
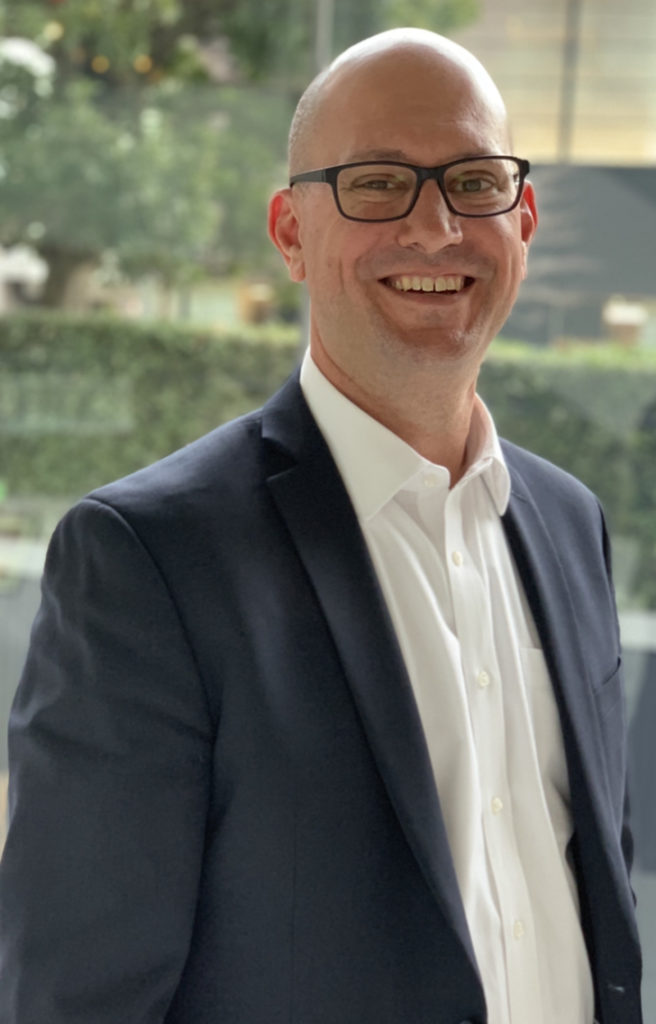
Ashley: Hi everyone, and welcome to episode number two of our new podcast on additive manufacturing where we discuss printing, the 3D printing industry, what Siemens has going on in this area, and generally whatever else seems interesting. Our podcast is sponsored by the Thought Leadership team here at Siemens.
For episode two we are continuing our conversation with Aaron Frankel who heads up the additive manufacturing program at Siemens Digital Industries Software. As you might remember, Aaron is the Vice President of Siemens Digital Industries Software Additive Manufacturing Program, and he has responsibility for the overall additive manufacturing business, our solution roadmap, and our partner ecosystem.
Aaron, to begin episode two, I’d like to go back to a subject that we discussed briefly in episode one. For those who didn’t listen to episode one, one of the things we discussed was use cases for additive. When we left off in that episode, Aaron, we had talked about production aids, digital inventory and optimization. Are there other use cases that you are seeing as you talk with our customers?
Aaron: We’re also seeing companies consolidate parts that were once in assembly into a single part. We can now print assemblies or we can start to print functional capabilities into the part – like springs or switches. These are some interesting applications we’re seeing. And then, certainly, personalization and customization. Additive manufacturing unlocks tremendous flexibility in the manufacturing process to add detail to parts, textures and labels. We’re also seeing personalization from a scan, to print the anatomy of a human being, and then use that scan information to be able to design prosthesis. I should say – for the customer it has been personalized specifically to fit the body. So, that is one tremendous opportunity for additive.
Ashley: Ok. Yes, I think I’ve heard this called a “lot size of 1”, and that’s a pretty good description of one of the killer apps for additive. You know when you can print a single unique part at about the same cost as a non-unique copy of a part, it opens a whole new world of possibilities for customization and personalization.
It seems to me, though, that another killer app for additive is optimization. I see tons of articles, blog posts and webinars about topology optimization and how well that technology works with additive. But it seems to me that almost every example is about strength or material optimization. I see a lot of topology optimized brackets, right? It reminds me of the initial phases of 3D printing where everyone was printing these rabbit models as test prints with their desktop printers and you saw picture after picture of 3D printed rabbits. Seeing optimized bracket after bracket would lead one to believe that topology optimization is a one trick pony. But I know we’ve been doing some work using topology optimization for other purposes, right?
Aaron: One interesting example related to thermal and flow performance optimization is a project that we embarked on with HP. They were looking to leverage their 3D printer to produce parts that also enhanced the performance of their 3D printers. So, we worked together to re-engineer a key component within the system that is responsible for keeping the print heads cool in the 3D printer. We leveraged some unique capabilities offered by Siemens – it’s simulation-driven CFD topology and optimization, where we specified the performance objectives of the cooling system within the printer. We turned our software loose on basically autonomously engineering a better performing duct that delivers air to the print heads. And the system was able to determine where the material needed to reside in the duct to control the airflow through the system in a more efficient way than human engineers.
The results of this project provided a 22 percent improvement in airflow through the system, ultimately delivering a better-performing overall print capability. These types of examples are quite inspiring and when we share these stories with others in the market we find that they can be quite enlightening. Engineering managers and leaders within organizations are looking for ways to leapfrog the capability of their products over others and are turning to innovative approaches to do so – additive manufacturing shines in this area. Eventually, due to these examples, we’ll drive a greater adoption of additive in the industry.
Ashley: Very true. That example of the “Mighty Duct”, as we call it with HP, was something that I think even surprised us as we were working on that project. I remember the moment when the analysis team showed us the geometry that resulted from the fluid domain topology optimization. It took us a moment or two to wrap our heads around the geometry because it was so organic, and so strange, that it almost seemed inside out for lack of a better term. That kind of stuff, where you see something that just blows your mind for a moment, really brings home the realization that this technology is opening up unbelievable possibilities for new designs and next-generation products.
Aaron: I believe that with additive manufacturing, next-generation products are going to be driven by new frontiers of performance and mass individualization to enable new business models. Additive manufacturing provides the fundamental capability that enables us all to transform the business of innovation. When you combine advanced capabilities like the Internet of Things (IoT), artificial intelligence (AI), systems engineering, predictive analytics, simulation and automation and low code development with additive manufacturing, we’re going to ultimately realize this goal of autonomous innovation.
Someday, every company is going to have its own autonomous innovator. And this innovator is going to know everything about their business, their products, down to the smallest part, the function of the parts in the larger system, the cost of materials that they’re made from, where they’re made and how they’re made. It will know your company’s financials, your competitors’ and the markets that you serve. In the future, we’re going to be able to set the requirements for what constitutes a successful innovation in a company and the autonomous innovator is going to take it from there. I think we’re going to get to the point where you’re going to give your autonomous innovator a standing order, like “Tell me whenever the cost or performance of one of my products can be improved by 20 percent.” And I think that your innovator is going to text you back and let you know that it has fulfilled that condition and it’ll ask you if you would like to have it in 3D and print the part for you. This might not happen for ten years, or in my career, but I do believe that it’s going to happen.
Ashley: That’s what is cool about all of this. As they say in the Matrix, you must free your mind and then you can let your imagination run wild with possibilities. Because, let’s face it, when you really start to think about how this all might pan out, there are a thousand places where additive might enable a new product, a new business model or a new discovery. It’s truly a greenfield opportunity now, so I hope we do one day have artificial intelligent advisors who can help us innovate. As we saw with the duct project that we talked about earlier, an algorithm can design a geometry that a human could never even envision, so you can imagine what technologies like AI and machine learning can bring to the table.
So, our conversation over the past episode, and this one, has ranged from use cases for additive, to examples of innovation, and even things we see for the future of the technology. Let’s bring things back down to today. I know we’ve been spending time here at Siemens working on innovative ways to enable the entire AM process. Do you want to talk a bit about how that focus is playing out in our software and how the various pieces of that fit together?
Aaron: Yeah. The solution that we’re building spans procurement, product development, manufacturing, planning and production – and our goal is to enable a digital thread that connects every step within these areas together, all the way from order management through design for AM of additive parts through automated design and engineering with generative engineering capabilities. Then. we provide simulation tools to validate that the parts that we’re designing for additive will perform the way we expect them to, after they’re manufactured. We’re investing in build preparation tools, combined with build simulation capabilities that will enable engineers and manufacturing engineers to develop the bill job that the different types of 3D printers on the shop floor are going to be able to use to produce or print the parts.
We’re also taking advantage of our software capabilities in the areas of post-processing and planning for how we need to finish the parts after they come off the 3D printers. One example of this is in the area of de-powdering. In many cases, the parts that we’re designing have intricate and fine-detailed channels within them and we need to get all of the powder out of these parts to have a finished part. We are looking at leveraging the digital twin of the design of these parts to develop the articulation of the de-powdering machines.
Ashley: Yeah. I’ve seen our solution for automatic de-powdering where we partnered with Solukon. What else are we up to?
Aaron: We’re also investing in capabilities to automate the removal of support geometry used to hold the part while it’s being printed. When we get into scale production, and looking to produce larger volumes and quantities of these types of 3D printed parts, we need to be able to control and orchestrate what happens on the shop floor. Therefore, we are investing in tools to manage the execution of the manufacturing process and the factory floor schedule, including the jobs, the orders and what needs to be delivered through the system and the process to produce the parts via connectivity to the machines. Then we can deliver the information to the machines and collect information off the machines that can give us input into different ways that we might want to think about scheduling the work as it goes through the production operation. Also, we monitor what’s happening on the machinery to ensure quality. So, it’s quite an expensive solution that we’re investing in, but this is what the market is telling is necessary to industrialize additive. Therefore, Siemens and our partner ecosystems are stepping up to the challenge to provide solutions across all these various areas.
Ashley: That’s quite a laundry list of capabilities, but I think it’s a testament to the level of potential we believe additive must help our customers in their businesses. We’ve done a really good job of picking out some of the more difficult problems to invest in creating solutions. That is something that I think the industry needs in moving forward.
I heard you mention process simulation. I know that one thing we hear over and over is the somewhat high failure rate for prints, especially in metal where the process takes a lot of time and the materials can be very expensive. Does the process simulation tool help with that, and is there anything else we’re working on that can assist companies with their print quality?
Aaron: I think the high failure rate of 3D printed parts is a big challenge for companies. Many companies are printing five or more attempts to qualify a part in the process. This is one of the areas that’s really holding back the entire industry. I think what it basically means is that because of the amount of time and energy and engineering that has to go into these different attempts, we’re seeing a build-up in the queue of new parts and new designs waiting for the engineering community to figure out how to produce them on a repeatable basis.
Simulation plays a fundamental and critical role in helping companies to reduce the cost and time required to qualify these new designs and processes. Ultimately, as we continue to improve these capabilities, we get to first-time right prints. And we’re investing in this ability – the simulation capability, in several different areas that span the process.
There are three primary areas where we’re investing in this: First, is upfront in the design process by providing some very easy-to-use cloud-based capabilities for companies looking to quickly analyze a part to determine its optimal build orientation. This provides insights into the best way to orient a part based on its geometric shape for the shortest build time, minimum distortion, minimum support removal and even minimal material consumption. This is a key capability in giving insights very early into the production of repeatable high-quality parts.
Secondly, we are investing in simulation to support the overall process in build process simulation. This is more of a CAE-based macro-scale simulation. It considers all the parts in the build, including supports and the powder. It predicts thermal-mechanical distortion of parts during the process and provides the ability to alter the CAD geometry to compensate for any distortion problems that it might uncover.
Lastly, is related to path optimization. We introduced a new technology last year called AM Path Optimizer, and this technology can predict mesoscale defects that can result from overheating along the scan path. When we determine where there may be some overheating, it can re-sequence the scan vectors to correct the defects that we predict. I think the combination of all these capabilities on the simulation front are all targeted at efficiency and cost-effectiveness of 3D printing, ultimately helping to accelerate the industrialization of AM.
Ashley: For sure. I know when I’ve talked with people who have come by our booths at various conferences and expos, back when we were doing those things, a topic of great interest for companies who print in metal is first article part quality. It’s a terribly expensive process of trial-and-error to get a quality part, and everyone in the industry is looking to shorten that process. I’m glad to hear that this is an area of focus for us moving forward, because many companies need assistance in this area.
Also, as I’ve talked with people at these events and learned over time what portions of the Siemens solution really resonate with them. What are you hearing? What are the companies we talk with saying about our solutions? The advantages. What do they like about what we’re doing and what are we are bringing to the table?
Aaron: I think that because Siemens is looking at a broad solution for additive – an end-to-end solution for additive manufacturing – we offer some unique values.
It would be a four-key value proposition. First, because of the integrated end-to-end digital thread, we offer a three times more efficient idea to the additive manufacturing process. This is because we eliminate the need to transfer data between different applications. So, whenever changes are made, we’re able to ripple those changes through with associativity versus having to manually input information into a different system.
Secondly, we offer a much greater breadth of functional performance. Our algorithms are generating 50 percent plus better functional performance in several areas for weight reduction while maintaining strength, along with improving flow and managing heat.
A third area is eliminating failed builds. As we spoke earlier, this is because of our investment in simulation. All the way from looking at orientation optimization to macroscale and mesoscale simulations of the AM process, companies are able to predict whether or not their build strategy, combined with the geometry of the parts, are going to result in the shape and quality of the part they originally anticipated.
Lastly, because of our investments in our additive manufacturing network, we can connect supply and demand between OEMs and the supply chain. We are seeing companies gain cost reduction advantages for procured parts, all the way upwards to about 20 percent, helping facilitate the different types of transactions and the collaboration between the OEMs and the supply chain in a digital form versus manual and traditional forms of communication.
Ashley: Yeah, that connection between supply and demand is always a topic of interest. How does a company find a good supplier? How do they find good advice? Being able to help our customers with issues like that brings good value to their partnership with Siemens.
Aaron: And I think that these values are resulting from several key investment areas and the progress that we’re making. One key area is our view and development of a unified solution that can connect requirements all the way through the design and engineering optimization process, to the build preparation and simulation, and onto the factory floor for execution and quality. The unified solution for additive manufacturing from idea to part is a key differentiator that we offer.
Another differentiator is our multi-disciplinary generative engineering capability, not only to optimize designs for better structural and weight performance, but also flow and thermal, looking at multi-objective optimization by combining competing requirements for the performance of parts. Therefore, our software can iterate digitally on hundreds of different design alternatives and then present the best-performing ones to the design engineer to select and move forward with it.
And, as mentioned before, we are unique in the breadth of simulation capabilities that we offer to help the engineer determine the best build approach to achieve first-time right printing. We offer simulation capabilities in the areas of build orientation, optimization, macro and mesoscale process simulation.
Lastly, to enable companies to produce parts in highly regulated markets, it’s critical to manage the data and the process with traceability. We have built all our authoring capabilities to work in a managed environment with Teamcenter to support the ability to design and produce parts for highly regulated industries. So, I think these are the four big key differentiators and investment areas.
Ashley: So, if I heard you right, you mentioned our end-to-end solution, our multi-disciplinary generative engineering capabilities, our ability to simulate not just the design performance but also the print process, and even the shop floor efficiency. Finally, the fact that all of this resides in a tightly controlled, managed and traceable environment. I would say the level of investment we’ve made in our AM software is proven by that list of solutions that we bring to the table.
I would like to once again thank Aaron Frankel for joining me today and the Siemens Thought Leadership team for sponsoring this webinar.
Siemens Digital Industries Solutions Software, through its Xcelerator portfolio, provides a breadth of many capabilities, including collaborating with experts to overcome the challenges of adopting additive manufacturing to fully gain its benefits.
This is the second podcast transcript in this series on additive manufacturing. A third podcast will be forthcoming.
For more information:
Listen this second podcast in the AM series to learn more about this engaging topic.
Also, you can access this podcast via Apple, Stitcher, Spotify, Castbox, TuneIn or Google.
About our experts:
Aaron Frankel is vice president of Siemens additive manufacturing software program. He has over 20 years of experience in the PLM software industry and has held various positions in engineering services, product management, and marketing – all focused on helping manufacturers take advantage of the latest digital design and manufacturing technology.
Ashley Eckhoff has a background in engineering and has been with Siemens for over 20 years in various capacities. He has spent the past few years deep-diving into additive manufacturing in both product design and marketing roles.