Podcast Transcript: Additive manufacturing – an industrial revolution (Part 1), the current landscape
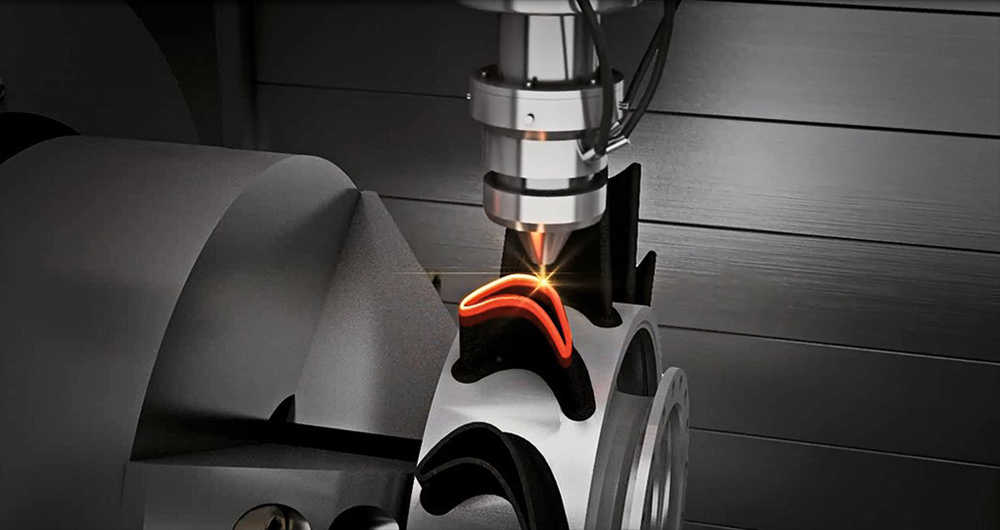
The untapped opportunities in the industrial manufacturing market are expanding. Expectations are high for additive manufacturing or 3D printing. There is a need to navigate the hype and advantages to adopting this technology.
Additive manufacturing (AM), and its next–generation of innovative products, are driving frontiers of performance and mass individualization. The induction of new flexible manufacturing capabilities and a more distributed manufacturing model are unlocking new business infrastructures for many companies. There are fundamental capabilities and a mindset that must shift to take advantage of many positive attributes.
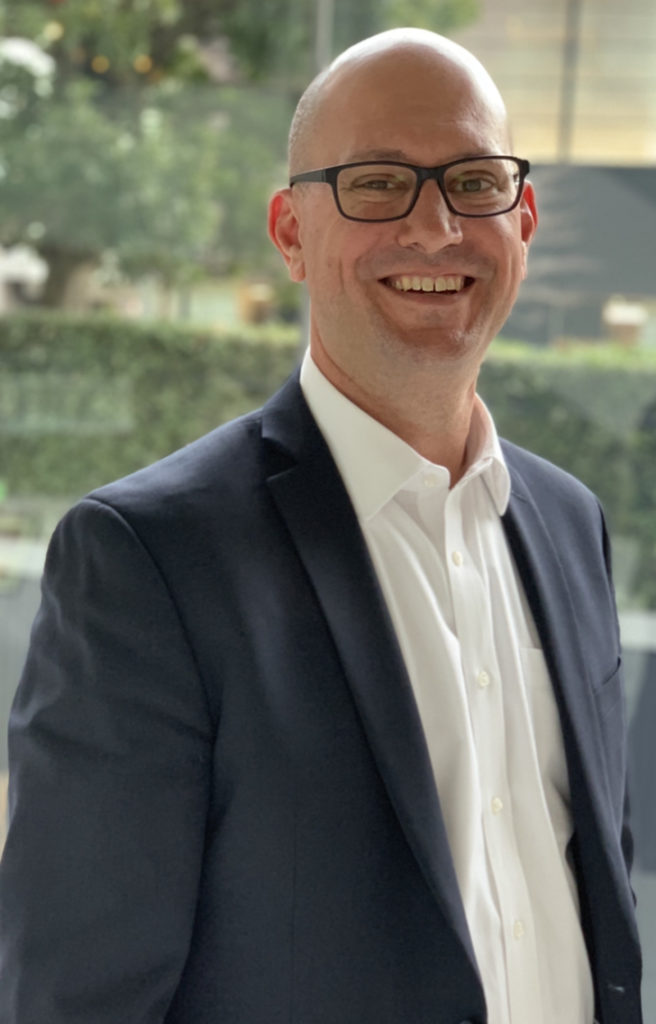
Read the transcript, below, of the first podcast in a new additive manufacturing series, hosted by Ashley Eckhoff, marketing manager at Siemens Digital Industries Software, interviewing our special guest Aaron Frankel, vice president of Siemens additive manufacturing software program, discussing the landscape of the additive manufacturing market, including its current state, customer interest, product performance and hindrances to adopting this technology.
Also, listen to this first podcast posted in our intial promotional blog.
Ashley: Hi everyone, and welcome to the innagural episode of our new podcast where we are discussing additive manufacturing, the 3D printing industry, what Siemens has going on in this area, and generally anything interesting going in the additive manufacturing world. Our podcast is sponsored by the Thought Leadership team here at Siemens.
Today we’re talking with Aaron Frankel who heads up the additive manufacturing program at Siemens Industries Software.
So welcome, Aaron! Thank you for taking the time to talk with us today about the current landscape of additive manufacturing. But, before we dive into our discussion, would you mind giving our listeners a brief description of your role and background at Siemens?
Aaron: Absolutely. I’m Aaron Frankel. I am the Vice President of Siemens Digital Industries Software Additive Manufacturing Program. Part of my responsibility is for our overall additive manufacturing business, our solution roadmap and our partner ecosystem. I’ve been with the company for 23 years, and held various positions, ranging from an application engineer to product manager to marketing, spanning everything from design engineering all the way through manufacturing.
Ashley: Awesome! Well, let’s begin by talking a little bit about your view of the current additive manufacturing market. Is additive on track in its maturity and adoption rate? Is it meeting your initial expectations?
Aaron: To be open with you, Ashley, the adoption of additive manufacturing is not meeting my expectations. I think there’s still a tremendous amount of untapped opportunity in the market, but I should also point out that my expectations for additive are very high – and maybe I can share with you what those expectations are. I believe that with additive, the next–generation of products are going to be driven into new frontiers of performance and mass individualization. They’ll get produced with new flexible manufacturing capabilities, a more distributed manufacturing model and I think that this is going to unlock new business models for companies. And I still believe that there’s some fundamental capabilities and changes of mentality that are required by the industry to better take advantage of additive.
Ashley: Yeah, I’d agree with that. It seems like there is a lot of tire kicking going on with additive, but I also get the feeling that we’re just now turning the corner and companies are just starting to understand what’s possible, and they’re just now working through all of those changes of mentality you mention. But it seems like it’s going to be a process that will take most organizations a little while to navigate as they build up their additive knowledge. So, what else are you seeing in the market? What are some of the strong areas where we’re seeing customer interest in additive?
Aaron: I’m seeing a lot of interest in prototyping. Many companies are leveraging AM to prototype new products so that they can get it out of the digital world and get their hands on it. I’m also seeing more prototyping of additive manufacturing applications that are going to be scaled into larger production operations. We’re going to begin to actually use additive manufacturing to produce parts and larger volumes that will go into end–use products. And these types of applications fall into a number of different categories. Some companies are looking at leveraging additive from a part consolidation perspective, where we take multiple parts and combine them into a single part that can be produced. This would be something with a much more complicated geometry than maybe the part that was produced using traditional manufacturing methodologies. I’m also seeing individualization, personalization of products and these types of applications getting produced in higher volumes. Many of these are going to fall into more of the healthcare space.
Also, I’m seeing a lot of companies investing in developing applications related to improving the performance of the end product. This could be lightweighting, it could be better thermal and flow optimization, where this product that’s produced using the additive is going to have a stronger contribution to the overall performance of the products that it’s in. Those are some of the areas. I think as I’m talking here, another important area is production aids and tooling. Companies that are making their initial forays beyond prototyping into additive are also looking to leverage additive and 3D printing to produce parts that are going to help them enhance their manufacturing operations on the shop floor. Instead of outsourcing these components, companies are finding they can use 3D printing to more quickly produce those parts at middle level, that have the strength per the requirements they need on the shop floor to get production moving at the levels that they need.
Ashley: Yeah, you know it seems like I’ve seen an uptick in people who are interested in printing manufacturing aids over the past year or so. I think that printing tooling gives companies a nice entry point into experimenting with more production type additive. They can print a number of jigs and fixtures, work on their output quality, experiment with materials and their process, all without putting delivery of an actual product at risk. So it’s a great way for a company to build up that knowledge base and iron–out their additive process without high levels of risk.
Now I know you said that additive is not quite meeting your expectations for adoption. So, what do you think needs to happen for companies to fully adopt additive?
Aaron: I think that in order to get us to full adoption of additive, ‘we’, meaning the market or industry, needs to better contend with three culprits that are killing additive innovation. First, I think that companies need to contend with a change–resistant culture. Sometimes this resides in leadership but not always. Leaders are often very enthusiastic about additive – sometimes they can be even overly enthusiastic. It really comes down to the program and the project leaders who can be really difficult to bring around. They’re the ones that are responsible for delivering the product to the market. They have to manage the costs. They’re on the line to meet the deadlines and they can’t afford the risk. And, they’ve got to have a process that works. Maybe it doesn’t have to be perfect, but good–enough, so why change? So we really need to be able to focus on helping companies kind of change their culture and perspective of additive.
Secondly, companies need to contend with inefficient project workflows. What we’re observing with many additive projects is companies are trying to get up to speed on the software they’re using, the hardware they’re trying to use, and sometimes they’re connecting together multiple applications of software coming from different vendors. It’s very painful to transfer data between these applications. Whenever a change occurs, the change and the cost of making the change is magnified by the fact that they have to ripple that change through a bunch of disconnected applications that don’t talk to each other. All of this adds waste into additive projects.
The third culprit that we have to contend with is the lack of meaningful benefits. Whenever there’s a hiccup in a process, we’re seeing costs go up for a company’s time, and it can drag on, with product performance getting compromised. And whenever this occurs, the projected benefits that may have persuaded a decision–maker to push additive forward in the first place, don’t materialize; I think it becomes harder for them to justify the organization’s advancement of additive adoption. These are three of the big challenges that the industry faces.
Ashley: So, I’ll second that. You know very well that we’ve spent a large amount of effort working on the inefficient process portion. I think that was one of the areas we identified right at the start as an area where Siemens can add value to what our customers are able to do with additive. So our extensive work around the end–to–end additive software process is what delivers on that goal. But more recently, it seems like Siemens, our partners and other companies have been working hard on the other two issues as well, right? The change–resistant culture and lack of meaningful benefits kind of go hand–in–hand in my mind.
As you know, we’ve kind of found that if we show companies in the industry useful, real–world examples that hone–in on the tangible benefits of additive for product development and production, then we start to change minds about the value of additive. The „Mighty Duct” project we did with HP is a good example. And if we get enough examples out in the market where the return on investment is fairly self–evident, then I think the momentum will begin to shift from resistance to acceptance. I imagine you probably have other examples of what we’re doing at Siemens to help our customers address these challenges.
Aaron: We recognize that overcoming these challenges can be, in some cases, daunting. I think at Siemens we have observed these behaviors and we’ve put in place an approach for helping nurture additive within our customers with the help of our partner ecosystem. This is a multi–step, multifaceted approach. We engage with customers. We make sure that there are experts on the team with deep knowledge and experience in our customers’ industry. We set up workshops with our customers to identify what the biggest opportunities for additive manufacturing are. Sometimes we might find that there is not a viable opportunity for the technology. And, if that’s the case, we’ll just say so. From there, when we find opportunities that we agree on, we spend time upfront before any work is started to scope out the workflow. Then we ensure that the proper tools are in place and we’re making sure that everything is going to be as streamlined as possible. And then and only then, we begin to work – and that’s in close collaboration with our customers. It often involves hands–on training, consulting services and support. And as the project goes on, we make sure that we’re tracking our planned objectives. Once we complete what we intend to achieve, we make sure that all the results are documented and we articulate the reasons why we may have deviated from the expectations, but usually, we end up hitting the target. That’s kind of the process that we’ve put in place for helping our customers adopt and advance their adoption and deployment and scaling up of additive.
Ashley: Yeah, I think this kind of hand–in–hand work is what it’s going to take to get the adoption of additive that we’d all really like to see in the market. Assisting companies with understanding not just the core additive process, but also the surrounding processes like post processing, shop floor management, materials management and so–forth is something I think we’re really doing right at the moment. It seems to me that another thing we’ve done right so far is that we’ve set up a really good ecosystem of partners.
Aaron: We’ve recognized early on that in order to industrialize additive and help industry adopt additive, that we at Siemens cannot do it alone, we won’t be able to do it by ourselves. And so, we’ve built a vast network of partners, both within Siemens businesses and across both software and hardware industries out in the market. We focus in on building an ecosystem based on our customers’ needs, their strategic endeavors – and we work very closely upfront with our customers to outline what the objectives are, we align with our partner ecosystem in order to make sure that we have the proper alignment of our technology roadmaps. And then, we also work together on building opportunities to engage together on the business side in order to help go to market and help our customers ramp up their additive operations. So, within Siemens, we have included within our broad solution base, motion control, automation capability. We also include factory automation capabilities and, as we develop our solutions and look to be able to better connect and drive sophisticated 3D printing machinery, we look to ensure that we have the proper interfaces in place and the proper capabilities within the software to define what the hardware is needing to do in order to be able to produce repeatable quality parts as would be expected.
Also, we recognize that we’re not going to be able to develop all the software that our customers need for an industrial additive solution – so we’ve tapped into the industry and developed very deep strategic relationships with a handful of companies on the software side to insert key technology and capabilities into our solutions set that preserve the digital thread. When we use these tools that are coming from our partners within the Siemens solutions set, the customers’ user experience is the same experience that they would have with the Siemens tool – so they’re accessing the capability through our UI. We are also maintaining the proper data structures to ensure that we have the continuity of the data, such that when we make changes, we’re able to ripple those all the way from design through the process plan to be able to produce the part on the equipment.
We have many relationships with a number of machine OEMs that are developing 3D printing capability, as well as post–processing capability, to drive the equipment in the most proficient way at the right level of fidelity, to control the process such that, again, we get repeatable quality of the parts coming off those machines to meet the end customer’s objectives. So, it’s a quite extensive approach. It requires a lot of communication and dialogue and alignment together, but we found that our partners are eager to achieve the same objectives that we are – to industrialize additive for the market – and it’s been a pleasure to work with all of our partners in order to help the market progress and advance.
Ashley: I think those relationships with partners has been extremely valuable on both sides. The reason you partner with other companies is because they bring capabilities and knowledge to the table that you, yourself, don’t have. So we get to learn from them, and they get to learn from us. This eventually gets reflected in the products we turn out where our customers get to benefit from the strengths of both organizations.
How about we shift gears just a bit and talk about what we’re seeing with customers. You get to spend a lot more one-on-one time with customers than I do these days. When you’re out in the field and talking with the various customers we work with, what kinds of companies are adopting additive and what are the reasons they’re giving you for pursuing this technology?
Aaron: I think that all kinds of companies are trying to adopt additive. Many of the companies that I’ve been engaging with, recently, have been companies who have been working in the additive space the last five to ten years and looking to advance the use of additive within their organizations and expand the it into their product development, engineering and manufacturing operations.
This is a part of the effort to scale up to industrial additive manufacturing. And these types of companies are looking for a consistent set of capabilities and tools that their broader engineering communities can leverage. These companies are in all kinds of industries – in aerospace, automotive, consumer goods, electronics, energy, machinery, marine and medical – and they’re ultimately looking to leverage additive to generate greater value for the products that they offer to their customers in the market.
Ashley: Yeah, it seems to me like the market is segmented into three groups at the moment. There are the early adopters who went through the learning process and have come out the other end with nice processes that mostly work for them. They’re looking to tweak things around the edges to eke out the efficiencies and quality that will bring them to the next level. Then there are the intermediate companies who have started the learning process, but are not quite through the woods yet. And, there are the tire kickers, who are still trying to figure out how additive fits in their organization. I assume that the companies we’re talking to have many reasons why they’re adopting additive. We talked earlier about production aids and consolidation as use cases we’ve seen. What else is there out there? What are companies doing with additive that’s interesting? I know I’ve heard about part repair in come cases.
Aaron: Yeah, there are a number of applications. I think in every industry and every company that we engage with, many of these customers are looking to develop more than one type of application. They’re looking at production aids – it could be grippers, handling devices, tooling and work holding devices. In many cases, companies are thinking about how to add even more value to their manufacturing operations with these types of production aids and they’re looking at how we use topology optimization for lighter weight tooling devices or grippers that might go into the automation equipment to start minimizing energy utilization and also speed up the process. Companies are looking at leveraging additive for part repair, in refurbishment – how can we take turbine blades and leverage, let’s say a DED process to be able to add and remove material, or add material to the blades, so we don’t have to create the blade from scratch but just use additive to fix it and move on.
Other organizations are looking at additive for part replacement of digital inventory. We all recognize that the casting process is quite time consuming and building a physical inventory of cast parts can be cost-prohibitive, and ordering parts for casting can take a long time. Companies are looking to analyze their bills of materials of cast parts within the products they offer and are beginning to turn to additive. There’s an alternative manufacturing approach where we don’t have to create a physical inventory, but we can tap into a digital inventory of parts that reside in the cloud and pull those parts out of the cloud to produce them on-demand. Companies are looking at part system consolidation. Some companies have visions for embedded electronics and we’re seeing different startup companies engage in this area. Also, larger machine OEMs are looking at different approaches of combining materials in parts that are printed to support electronics.
Other applications pertain to performance optimization. I mentioned lightweighting before, but also there’s thermal and flow optimization – looking at how we better manage the heat in the system to enhance the performance of the part of the product that the parts are in. Energy management is an interesting application area where companies are looking at leveraging advanced lattice structures to better absorb energy, like a cushioning effect, maybe as a foam alternative. Companies are beginning to look at replacing the soles of shoes with lattice structures that are personalized to the runner who’s going to be wearing those shoes in races. So, all kinds of really fascinating applications that companies are investing in. It’s quite an exciting space and a fun innovation process to be able to engage directly with these customers and help them work out the best ways to engineer and produce these types of parts.
Ashley: I agree that there are a handful of really exciting possible use cases for additive that have a ton of unrealized potential. It’s going to be fun to watch this industry evolve over the next few years as more and more companies get experience with designing parts for printing and with the printing process. That high-level of innovation and potential is one of the things I find most exciting about working in this field.
Well, I think we’ve covered a lot today. I’d like to thank my guest, Aaron Frankel, Vice President of Siemens Digital Industries Software Additive Manufacturing Program, and I’d like to thank the Siemens Thought Leadership team for sponsoring this podcast. My name is Ashley Eckhoff, and I hope you’ll tune in for episode two where we will continue the discussion about additive manufacturing and the way it’s going to change our world. Thanks for listening, everyone!
Siemens Digital Industries Solutions Software, through its Xcelerator portfolio, provides a breadth of many capabilities, including collaborating with experts to overcome the challenges of adopting additive manufacturing to fully gain its benefits.
For more information:
Listen to the audio podcast in the first podcast in the AM series.
You can also access this podcast via Apple, Stitcher, Spotify, Castbox, TuneIn or Google.
About our experts:
Aaron Frankel is vice president of Siemens additive manufacturing software program. He has over 20 years of experience in the PLM software industry and has held various positions in engineering services, product management, and marketing – all focused on helping manufacturers take advantage of the latest digital design and manufacturing technology.
Ashley Eckhoff has a background in engineering and has been with Siemens for over 20 years in various capacities. He has spent the past few years deep-diving into additive manufacturing in both product design and marketing roles.