Thermal simulation helps Maya HTT keep things cool
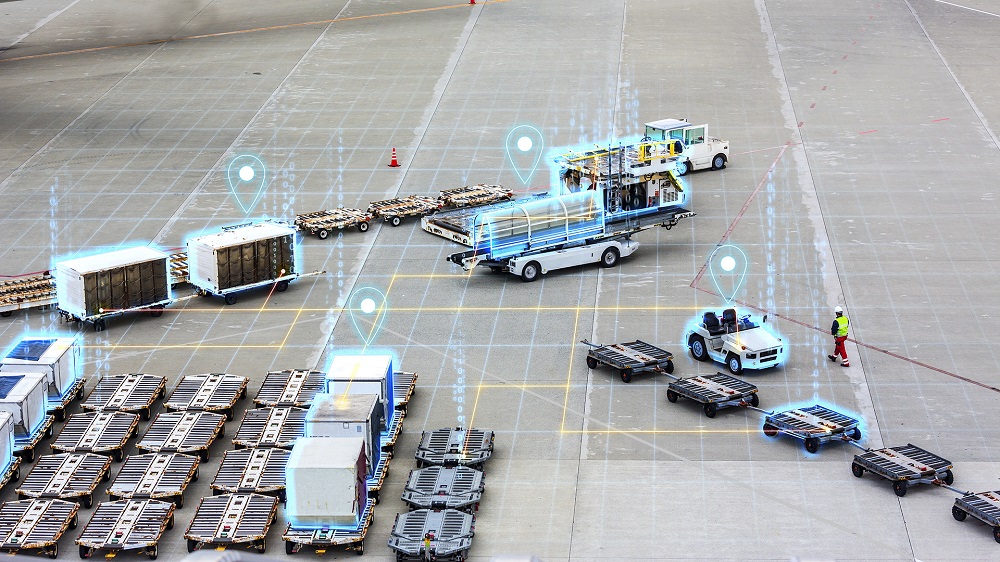
Maya HTT created a unique contest involving thermal simulation at their exhibition booth recently at Realize LIVE 2019. With the goal of demonstrating the accuracy and efficiency of their thermal simulation software, Maya HTT tied simulation activity with the giveaway at the booth by taking a large block of ice and freezing a gift card inside of it.
The contest: Maya HTT provides a thermal simulation based on environmental conditions expected at their booth location and predicts when the gift card will be released from the ice. They provide this information to their booth visitors and participants predict when the real “drop” time would be. The closest one is the winner.
To predict the results of the Ice Challenge, Maya HTT entered the environmental data into their computational fluid dynamics (CFD) code which predicts melting based on the dimensions of the ice block, changes from ice to water, water runoff, room temperature, characteristic airflow speed, the starting temperature of the ice itself and other factors.
The start of the Ice Challenge began at 8:00am. It finished at 5:50pm.
The simulation ran over by just four minutes.
Simulating the melting ice block offered a different glimpse into how simulation technology could be used. Implementing thermal simulation is proving to reduce costs and maximize efficiency in a variety of industries, including cold chain logistics. How is simulation being used to help keep things cool?
Cold chain: getting from point A to point B
According to the Center for Urban Education about Sustainable Agriculture, to make it from the farm to the plate, the average meal in the United States travels approximately 1,500 miles.
Also, countries imported approximately $400 billion pharmaceutical drugs and medicine in 2018.
How can shipping companies ensure temperature-sensitive products like produce and pharmaceuticals can journey for multiple days, experience multiple events and arrive in the best condition possible?
Cold chain logistics, or temperature-controlled supply chain, uses refrigeration storage and distribution to ensure product integrity throughout the entire delivery process. When it’s simply too time-consuming and expensive to replicate every temperature variation and condition in a lab, how can you test to ensure product and container integrity? For example, how do you test a two-hour flight delay in Phoenix in July where medicine sits in a shipping container on a tarmac before being loaded onto a plane?
Thermal design and simulation must be used to build and design the packaging of the containers used to protect the integrity of the product regardless of unknowable conditions.
Pharmaceutical products start at a processing facility and must maintain a certain temperature from there on. Simulation begins at the point when they’re packed in containers, usually with gel packs to regulate temperatures.
Temperature profiles with established parameters are created and include the type, number and location of gel packs within the container. From there, the shipping methods for every step of the journey is required. For example:
- The product starts at a processing facility
- It’s placed on a loading dock
- It’s then loaded on a truck
- The truck takes it to the airport where it then might sit on hot pavement in the sun
- It’s then placed on an airplane in a likely poorly conditioned compartment and flown for hours
Then the reverse occurs at the new location – off the plane, on a ramp until it’s loaded onto a truck and then to a processing facility or final destination.
A client provides these temperature profiles that are simulated to determine how the ice and gel packs cool down the product initially and how they maintain cooling properties throughout the changing environments.
Just like the Ice Challenge, simulating how ice will react in various temperatures and environments involves large amounts of data points to determine an end-result which can be tested and verified. For containers involved in cold chain logistics, the simulation to find the best packaging solution saves hours of testing and countless costs in food or pharmaceutical spoils.
Many manufacturers test package integrity in environment-controlled chambers that run through the cycle in real-time. These live tests, though, can take days to conduct and produce a single analysis based on the individual test. Simulation condenses this time to hours providing multiple variances instead of a single result in days or weeks.
Conflicting requirements present a new challenge when designing shipping containers. Shipping from Chicago means packages are sent out both in 90-degree heat in the summer or nine degrees in the winter. Both require different methods of packaging and thus, a one-size-fits-all approach is unreliable, especially when it involves pharmaceuticals and their narrow temperature range. A simulation approach can provide guidance on how things need to be changed.
But what if two or more shipping container options aren’t feasible or simply the business only wants one? Simulation can also prove what methods work to maintain product integrity with a single shipping container, such as adding cardboard or foam inside the container during the wintertime to help prevent the product from getting too cold.
Simulate for results and options
Simulation gets a lot of credit for its wonderful work in the automotive, aerospace and manufacturing industries but the use of simulation has a wide variety of benefits across countless industries. The preceding example shows how Maya HTT provides the expertise/services and thermal simulation software that helps companies innovate their processes and products.
Click here to learn more about how simulation is changing the way businesses design and build their products.
Carl Poplawsky, Engineering Simulation Services Manager, MayaHTT contributed to this blog.
Mr. Poplawsky has been providing computer aided engineering (CAE) based services for nearly forty years, starting in the “good old days” when engineers would sketch finite elements on to 2-dimensional drawings and measure node locations with an engineers’ scale. He has been with Maya HTT for 15 years, supporting both CAE software sales and engineering services.
Maya HTT was founded in 1982 as a company specializing in 3D thermal and fluid dynamics analysis. Maya HTT has more than 35 years of experience developing and implementing specialized software solutions in a wide range of fields and has been at the forefront of specialized software development. Click here to learn more about Maya HTT.