Define the digital thread for production systems engineering
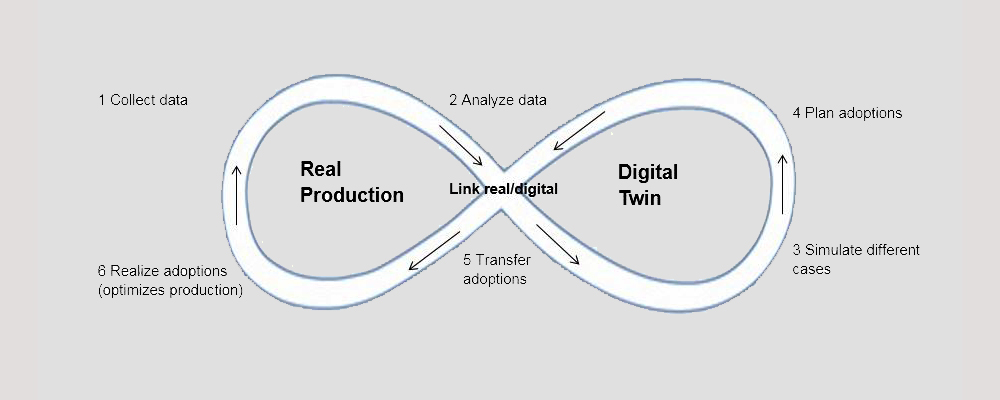
By: Wolfgang Schloegl and Christian Heck
Manufacturing is in the midst of striking changes which will impact the way products are made, and also how companies will remain unbeaten against their competition.
It’s about making products better and more quickly through the digitalization of production planning, engineering and execution. It’s also about digitally tying the production system to the desired product. Manufacturers want to build a better production system with such items as machines, production cells and lines, which are ideally suited to the end products and easily adapt to changes.
The entire data related to the production system for building a product is connected by and engineered along the digital thread, the structure of elements in the planning and manufacturing process which enable a connected flow of data across and throughout the normative lifecycle.
This concept originated in the aerospace industry, where buyers expect cost savings, fast responses and anticipation of their needs based on such trends as Industry 4.0, as well as unification with digital manufacturing, including smart manufacturing and Industry 4.0. The digital thread in the aerospace industry allows for tracing requirements from design to manufacturing, as well as providing the necessary knowledge throughout the production lifecycle across all disciplines, and similar needs are appearing in other industries, such as automotive.
The digital thread starts with the product design and crosses over to the engineering of a production system to build better production― and ultimately, better products.
Defining your needs with measurable benefits
Knowing how to find, interpret and use information can be a cumbersome and challenging task for engineers. Is the information found still valid? Is it correct? Which part of it is needed? These questions frequently arise when working with data from numerous isolated sources. A digital thread relieves these questions by delivering information that is:
• Definitive and connects in context with other pertinent information
• A mouse click away
• Actual and valid
These benefits speed up the lead time, reduce sources of errors and leave more time for actual engineering work. What is right for humans is also true for automated systems in Industry 4.0. These systems can only work with data that is available in a digital thread: systems can’t go searching for information, so implementing a digital thread in engineering is the logical start before applying it as a standard to production.
Benefits of the digital thread
A digital thread streamlines all production systems engineering disciplines to allow multiple benefits.
• High engineering efficiency. You build production activities on previous activities, which saves money. For example, you could develop your controls engineering based on the 3D model and properties from the mechanic. In production systems engineering, you can realize a smooth transition from product design to production planning. Production solutions used in the past are easily reusable. Engineering results can generate automatically, and unproductive activities are significantly reduced, leading to higher engineering efficiency.
• Delivering faster results. You finish your engineering work earlier so you can produce your products rapidly, which means they get to the market, and to your customers, much faster. The entire production system also produces more efficiently with first-time quality. In turn, you stay ahead of the competition in time and you add value to the machine builder and the OEM that operate the machine.
• Quality in engineering. With the manual interaction of data conversions, there is the potential to introduce serious error, which can be costly and difficult to fix. With the digital thread, you can significantly reduce this risk. You don’t copy what others have done, but you base what you do on others’ work. This philosophy allows you to learn from their successes and mistakes, and there’s a reduction in errors when you emulate information from one discipline to another.
• Flexibility. Performing changes is simple: when a parameter changes, the digital thread synchronizes this information across multiple disciplines. These changes are also more transparent to the production systems engineering process, allowing for quicker changes and improved quality.
• Maintainability. Better production systems are not only more efficient in producing products, but also have improved maintainability through digitalization of spare parts and repairs. You can monitor every stage in the production process and the quality of those products and parts.
• Improved collaboration. Collaboration is one of the top values digitalization enables, because manufacturers can view and explore others’ work. For example, electrical engineers can see 3D models from both the mechanic and the engineer, which leads to a much better understanding of the system, along with the ability to suggest improvements within other disciplines. This collaboration between people helps you improve your overall technical solution for the production system.
Mass production and the relationship to Industry 4.0 and smart manufacturing
Market trends change quickly, and they’re turning over with shorter lifecycles. It’s a daunting challenge to produce the right product, at the right time and faster than your competitors. The digital thread in production systems engineering assists you in developing the right product within a specific time with optimum positioning to improve the product.
New concepts are now developed to make production more flexible and increase your return on assets by efficiently adapting existing production systems to the new production concepts.
Even when you’ve mass produced a particular product for years, with no changes to your production line, your technology to deliver your product is changing. You have to change to keep pace with your competitors, not necessarily your product, but to increase the speed of your process to develop the product better and more efficiently, as well as improving the overall end product.
If the product stays the same, there are still threads to your production to be modified. You need to develop more flexible, new concepts that will increase your return on assets so you can efficiently adapt your existing production systems to new products.
According to the CIMdata 2016 PLM Industry Trends Market Analysis Report, updating materials and production methods such as additive manufacturing allow for changing everything via the digital thread for production systems engineering with:
• New production methods and processes
• Enablement of existing production facilities to more efficiently operate new materials
• Adapt production with critical capabilities for shorter lifecycles to stay ahead of the competition
New materials drive the need for everything, from machinery and computer applications to materials management and support services. Those in operations require new, enhanced design and simulation software to optimize the manufacturing process and its tools.
This concludes part one in a series on defining digital thread for production systems engineering. In part two, we’ll continue by discussing the manufacturing process planning.
About the authors
Dr. Wolfgang Schloegl leads the Digital Engineering department in the Siemens Digital Factory division and is amongst others responsible for the software Automation Designer. He also works on providing integrated solutions of Siemens PLM Software with Siemens automation systems. He has been with Siemens since 2003 and previously worked in planning and digital manufacturing for automotive production. Wolfgang was formerly with Daimler in Sindelfingen, Germany, where he worked on knowledge management for production planning, and later, in project management for assembly planning. He studied production engineering at the University of Erlangen-Nuremberg in Germany, where he earned his doctorate in the area of simulation for discrete production.
Christian Heck is a Production Systems Engineering Solution Manager for Siemens PLM Software, a business unit of Siemens Digital Factory Division. He has more than 14 years of experience in automation engineering and commissioning, as well as developing cloud-based industry applications. Heck gained much of his experience working for Siemens Oil and Gas Offshore in Norway, where he worked as System Responsible for several major oil and gas projects. His previous experience with Siemens includes leading a Service Line for optimizing production plant performance based on data analytics applications. Heck holds a Bachelor of Science degree in automation engineering from the University of Cooperative Education in Karlsruhe, Germany.
Comments