Nestlé uses Siemens’ software to go from outdated to trendsetting
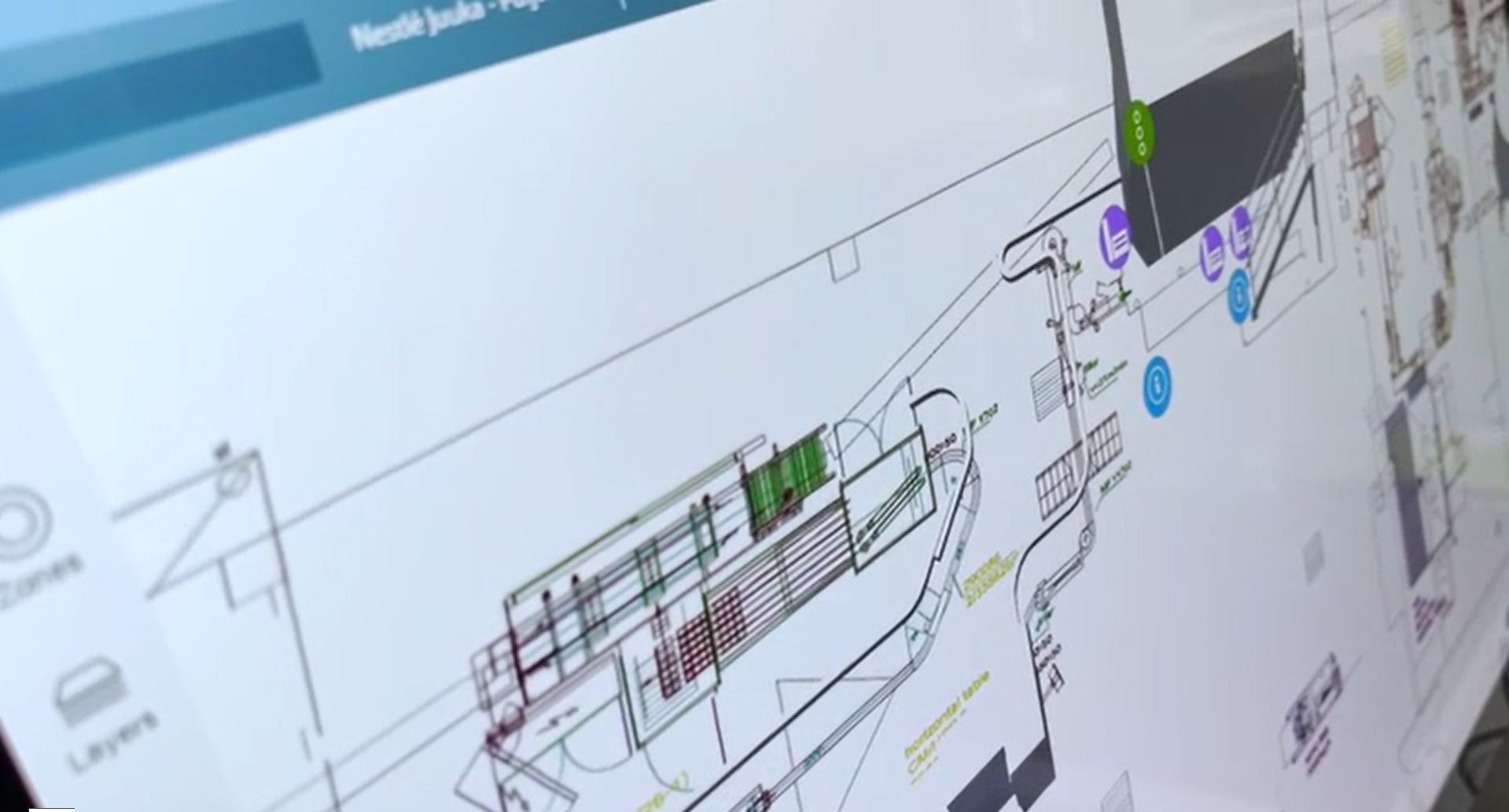
Nestlé is a well-known name in the food and beverage industry. Nestlé’s plant in Juuka, Finland, is known for producing high-quality gravies, demi-glace, and fonds for chefs and restaurants. For those not well versed in the food industry, these products are all types of sauces used in cooking and plating at restaurants.
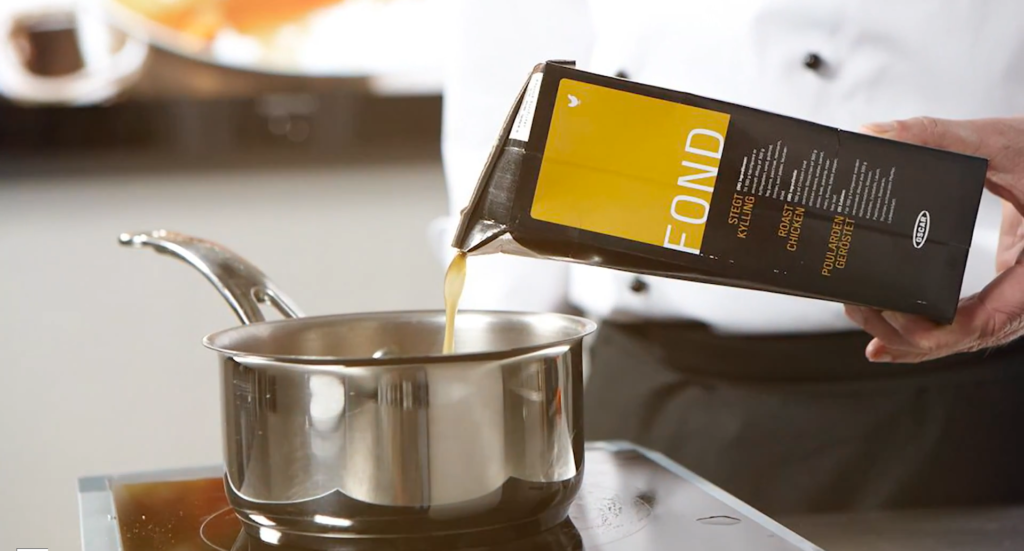
Producing these high-quality sauces for demanding chefs and restaurants became increasingly difficult as the factory in Juuka grew older, the efficiency of the plant decreased, and the automation become dated as the years went on. Modernizing the old, remotely located plant was a challenge but with help of Siemens’ Digital Enterprise portfolio, including Tecnomatix Plant Simulation, it quickly became a success story for Nestlé.
With Siemens’ Digital Enterprise portfolio, the Nestlé plant was able to find a complete solution to digitalize and allow the plant to take the next step into their digital transformation. Several digital twins were created to help streamline the project. One digital twin utilizes the performance data that’s collected from the factory’s live operation and can be used to optimize processes and performance.
The other digital twin is a digital model of the plant that was used to simulate the material flow in the factory. The use of Tecnomatix Plant Simulation allows Nestlé to model, simulate, optimize, and validate different production scenarios and their processes.
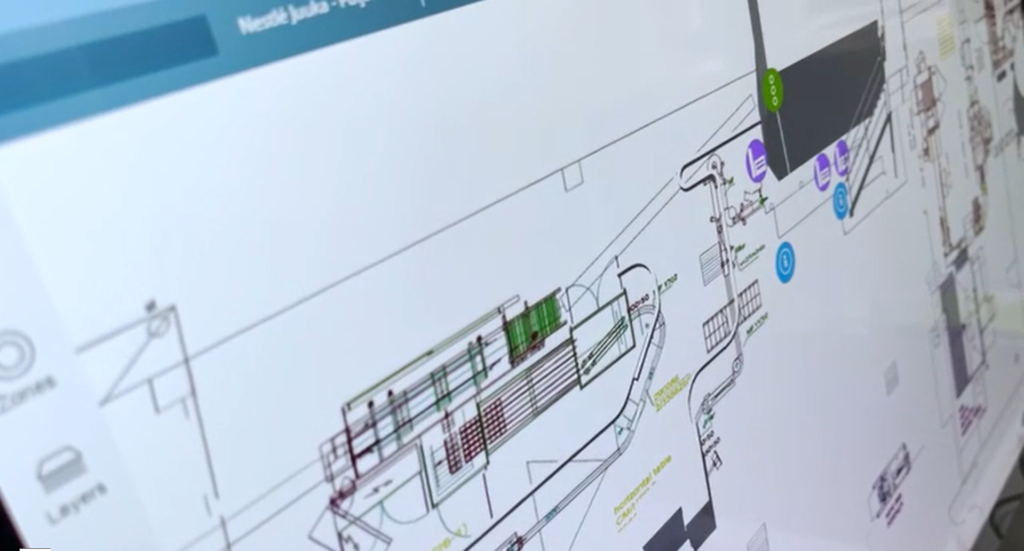
Since the implementation of Siemens’ Digital Enterprise portfolio and Tecnomatix Plant Simulation, Nestlé was able to establish a more sustainable production process in Juuka and reduce wastewater and chemical consumption. Production became more stable and reliable with an increased yield and optimizing the production scheduling process led to an overall improvement in the plant’s manufacturing performance.
Read the full story of Nestlé Juuka today!
For more information on Tecnomatix Plant Simulation, visit our website.