Electronics manufacturer controls its production with plant simulation
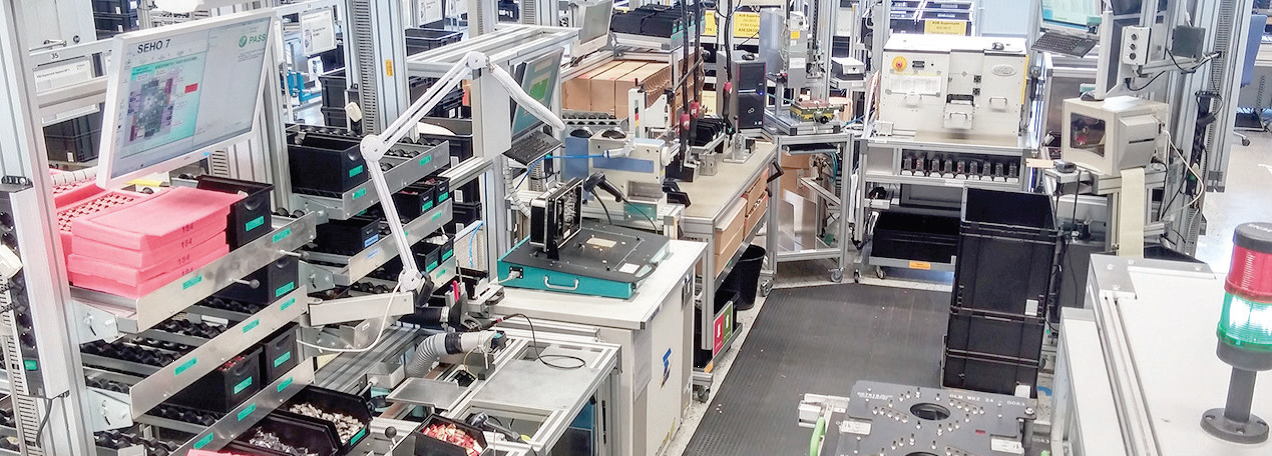
The Siemens Manufacturing-Karlsruhe (MF-K) plant introduced the Tecnomatix Plant Simulation solution to support the company’s continuous improvement process. Today, not only are production lines simulated before they are built, but workers actually control daily production using the software. Learn more in the following case study summary.
“Our mission is 100 percent quality, 100 percent delivery performance and 100 percent waste-free,” says Bernd Schmid, plant manager at Siemens MF-K. “That means we want to manufacture our products with as few resources as possible. This requires that the manufacturing processes operate how we envision them to. Plant Simulation is a big help to that end.” For its consistent use of simulation software, Siemens MF-K was recently named one of the winners of “100 Places for Industry 4.0 in Baden-Wuerttemberg.” The jury of experts recognized the company for practical concepts that intelligently combined production and value chains.
Siemens MF-K is a prime example of the challenges that manufacturing companies are mastering with the help of Industry 4.0: a high degree of variance, continuously shrinking batch sizes and fluctuations in order volume that are increasingly difficult to predict. Today’s industrial customers behave like consumers of PCs: they want to configure their product online and if possible have it delivered by the next day. To be able to respond to these individual customer requirements and fluctuations in the order volume, Siemens MF-K will completely restructure its production in the next months. The effort is “like open-heart surgery,” and will also be simulated using Plant Simulation. To avoid collisions while reorganizing production, the manufacturing lines, which so far only exist as 2D models, must first be remodeled in 3D using the Line Designer capabilities of NX software.
Continuous improvement processes are a tradition at Siemens MF-K. “We are proud of the increase in business value to the tune of nine million euros per year achieved by the suggestions for improvement by employees,” emphasizes Schmid., “Plant Simulation is a beacon of our overall digitalization strategy to improve every day with Industry 4.0.”
No new capital investment required
The vision of creating a digital model of the plant by using Plant Simulation was born four years ago after a presentation by colleagues from Siemens PLM Software. As a pilot project for testing the software, Siemens MF-K chose a production line that had reached its capacity limit and was actually due to be replaced. In this production line, through-hole technology (THT) elements are soldered selectively to printed circuit boards that are already fitted with other components. “The difficulty is that different products, each with its own processing time for the individual processing steps, are processed in the production line simultaneously,” explains Bernd Bastian, one of the first Plant Simulation users at Siemens MF-K.
“By optimizing the preparation of product combinations and the line balancing of the process steps in the system, Siemens MF-K was able to increase the output by so much that an investment in a new production line was no longer necessary,” says Markus Fischer, head of Siemens MF-K’s continuous improvement processes in Karlsruhe. “The investment would otherwise have cost the company a six-figure sum. Based on the positive experience with the pilot project, the plant management decided to implement the software enterprise-wide to optimize production.”
Re-creating the existing production cells, production lines and manufacturing cells using Plant Simulation cost Bastian and his colleagues some time. While the software includes libraries of standard objects for modeling assembly lines and material flows or value streams, it must still be adapted to the requirements of electronics manufacturing. So far, the three application users have re-created approximately 60 to 70 percent of the existing plant production, facilitated by the equipment’s re-usable modules. Fischer explains, “Thanks to our modular system, the basic model of a production cell currently takes about two hours to complete.”
To learn more about how Siemens MF-K simulates entire production lines, read the complete success story in the attachment below.
The working platforms at Siemens MF-K are made of re-usable modules, which makes their simulation using Plant Simulation easier.