Digitalize battery manufacturing for a greener future with electric vehicles
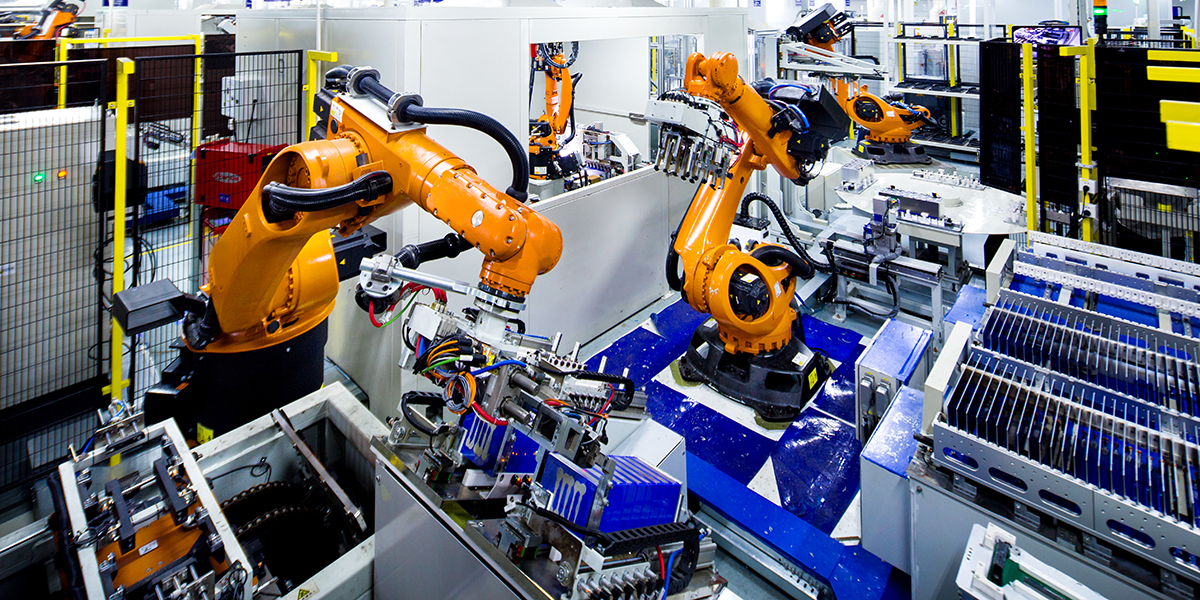
Digitalize battery manufacturing for a greener future with electric vehicles
The electrification of automobiles is gaining momentum globally as many countries have laid out plans to prohibit the sale of internal combustion engine (ICE) cars. The closing deadline is 2025 for the Netherlands and Norway, with Germany and India to be the next down the line in 2030, followed by the UK and France in 2040. Other major economies in the world provide aggressive initiatives to push the electric vehicle (EV) into the market. For example, USA, China, Norway, Denmark, and South Korea have been implementing cash subsidiaries to EV buyers in amounts over $10,000 per vehicle, with Denmark and South Korea paying the consumer almost €20,000 for each car purchased.
These incentive plans, however, also indicate that the price of EVs is still high compared to traditional ICE cars. Independent research shows that the cost of the electrical powertrain is roughly 50% of the EV while the cost of the powertrain for ICE cars is only 16%. While it is largely true that the components of a vehicle, whether it is an EV or ICE car, are largely similar except for the powertrain, the source of the difference in total cost is obviously the powertrain. The most expensive component is the battery pack, which accounts for roughly half of the powertrain and a quarter of the entire car.
Fortunately, the cost of the battery has been going down steadily over the past 10 years. It is about to hit the point where the total cost of an EV is competitive to an ICE car and that point is about $125-150/kWh.
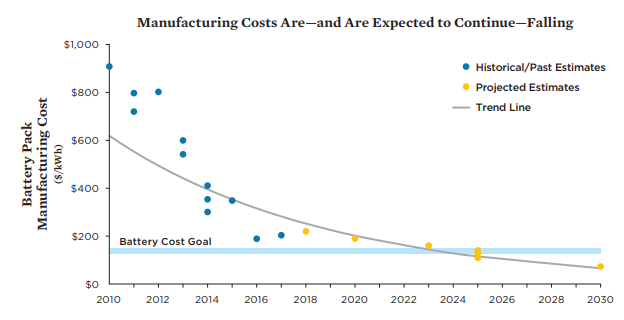
> https://www.ucsusa.org/sites/default/files/attach/2017/09/cv-factsheets-ev-incentives.pdf
As a result, battery manufacturing capacity has been ramping up quickly. Tesla is leading the way through its Gigafactory in Nevada with a target annual capacity of 35 GWh. Yet the race is tight as the battery manufacturing in Asia is catching up. CATL of China had recently announced a plan to boost its capacity in Germany to 100 GWh.
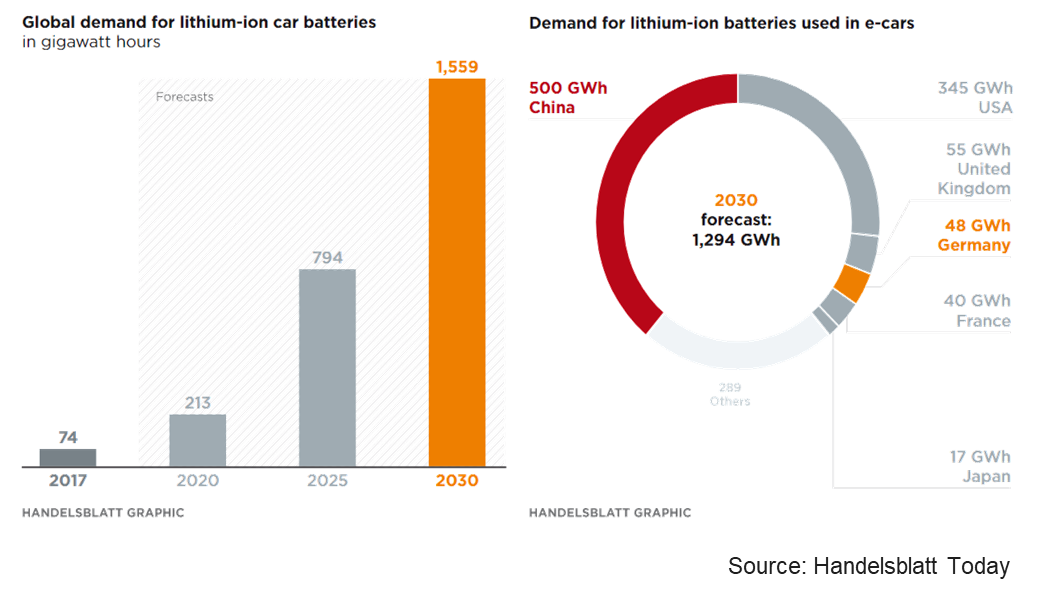
Certainly, there are many challenges for both battery makers and EV manufacturers in this new and dynamic market. Occasionally we see it in the news that an EV is burning for unknown reasons, or we are told an EV maker is recalling its product to fix a battery pack harness design issue. Recently, all the countries started to lower or stop incentive plans for EV buyers. How can battery manufacturers, as well as their EV customers, stay competitive in this dynamic market with fast global expansion?
For the battery makers, they need to focus on the research of chemistry and material science to maximize the power density in the battery cells to provide the range the EVs need. In addition, both battery makers and EV manufacturers (they usually build the battery pack in-house) should adopt the digital enterprise concept to make sure the design and production of battery cells, modules, and packs can address the needs from the market in speed, quality, flexibility, and cost.
Siemens’ digital enterprise suite is the ideal toolset to cover the entire product life cycle for battery manufacturing, connecting the digital world with the real world.
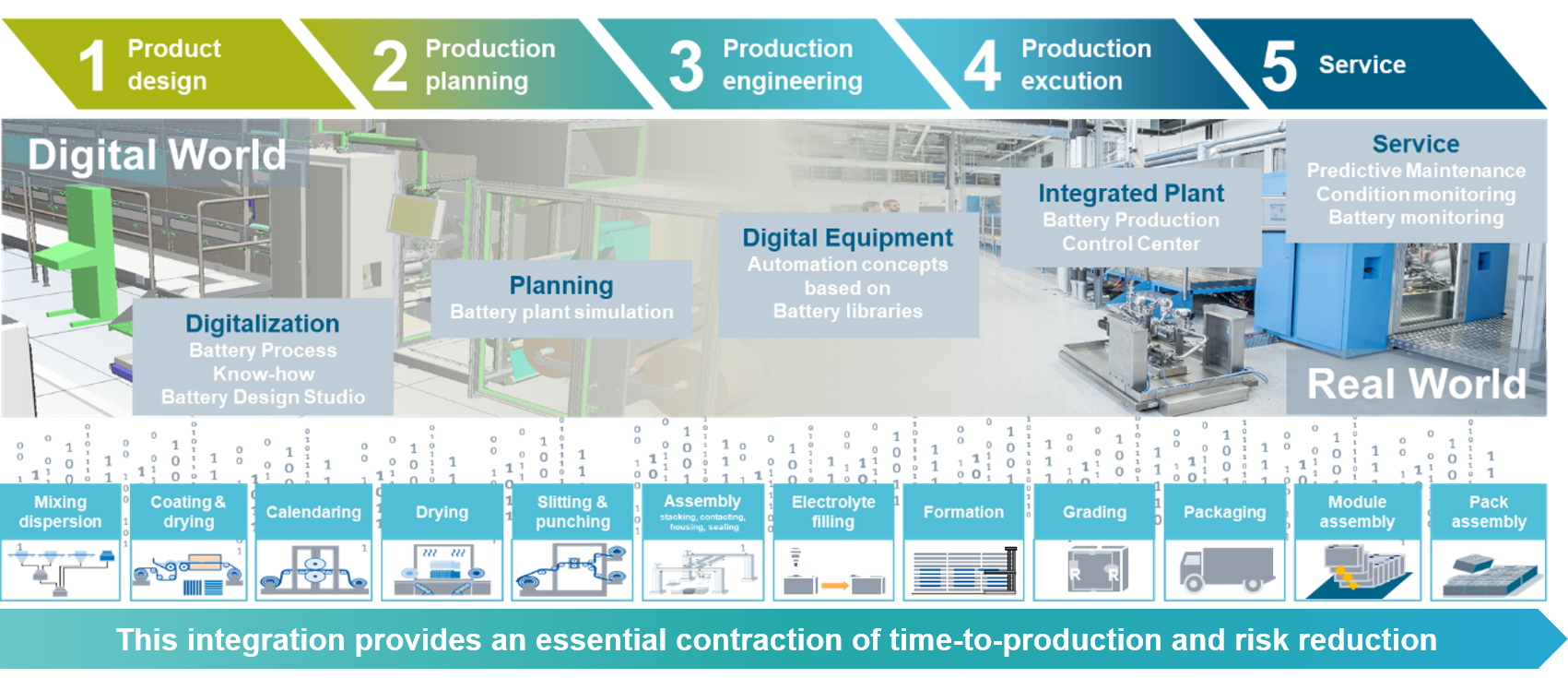
In product design, battery makers can leverage the Battery Design Studio of the Simcenter portfolio to simulate the electrochemical and thermal performance of lithium ion battery cells. Traditional mechanical and structural simulation is also possible in the CAE suite to ensure the quality and safety of the casing. One easily overlooked aspect is the need for not only manual assembly but also disassembly, as environmental policies may require the battery module in each car to be separately maintained and recycled. Jack for NX Human in the mechanical design phase helps validate whether the parts can support easy plug-in connection for operators.
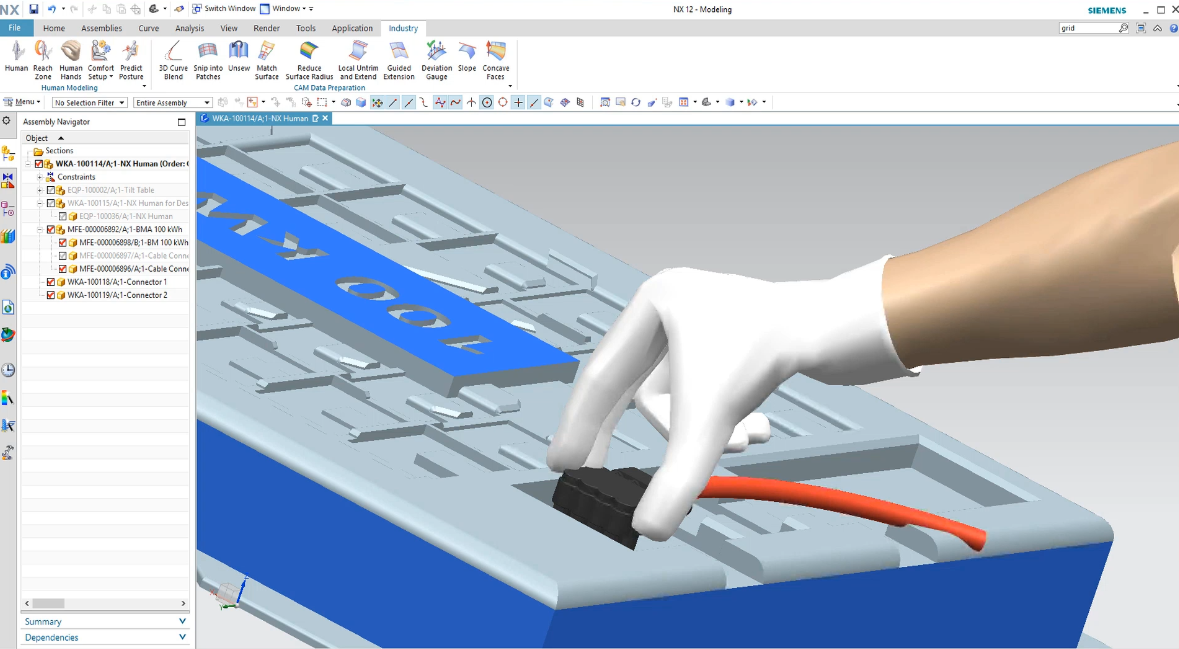
In the production planning phase, Tecnomatix Plant Simulation supports validation and optimization of a battery factory. The software will enable the user to understand the expected throughput, equipment utilization, power consumption, material flow, and even production cost for the designed resource allocation. For already implemented factories, Plant Simulation software further optimizes factory operations. For example, some assets on the battery cell manufacturing line have a predefined speed and cannot be changed. These assets are usually bottlenecks in the line and limit the utilization of other equipment. By careful design of buffers and work schedules, users can save unnecessary run time for machinery at low utility therefore increasing the overall equipment efficiency and reducing energy consumption.
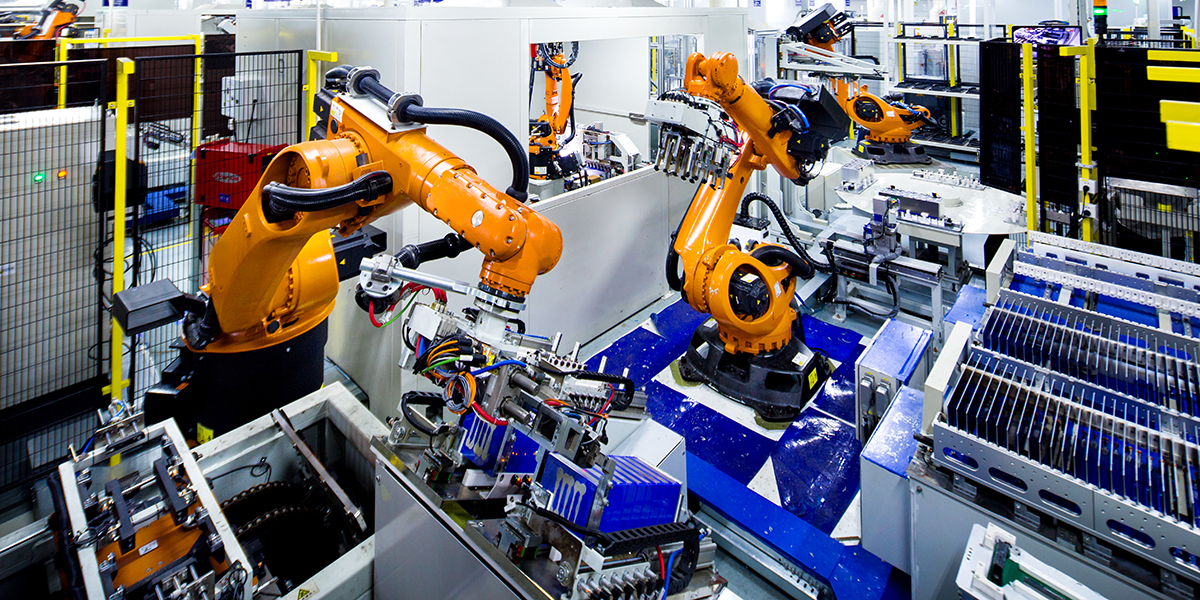
The assembly of battery modules and packs is highly automated with lots of robots for welding, adhesive application, pick-and-place operations, surface treatment, etc. Robotics process simulation, offline programming, and automation commissioning now can be done in the digital world before they are carried out on the shop floor thanks to the combination of Tecnomatix Process Simulate and TIA portal software. The revolutionary process of “virtual commissioning” allows the engineering to start before any hardware is delivered or while manufacturing for the former product is still going, saving precious time. The digital simulation and validation tools help robotics engineers and automation engineers identify mechanical interference and control logic issues without any risk of damage to the parts, assemblies or production machines. Moreover, with integration to Teamcenter and Teamcenter Manufacturing software, the battery maker can enjoy the power of the digital thread to ensure consistent and timely data across the entire value chain with potential to build its own library for re-use.
Humans are essential for assembly and disassembly jobs of flexible parts, for example, the joining and separating of connectors that we discussed earlier. Tecnomatix Process Simulate Human helps manufacturing engineers design a human-friendly work environment that poses no risk of labor injury as well as making sure the work cycle time suits the delivery needs. Users generate work instructions with the software from the first-person view of the operator to accelerate the delivery of those instructions to the field. It is expected that the shop floor ramp-up of production will have a much lower risk for trouble during the implementation phase.
On the battery production shop floor, Siemens PLCs, servo motors, drives, and circuit breakers provide the best-in-class automation system for high quality industrial machines. The field devices are connected to Siemens’ manufacturing operation management system, SIMATIC IT, to make the shop floor transparent and well under control. MindSphere, the Siemens industrial IoT platform, will support data collection in the factory or during the product usage to feedback key insights to product design and manufacturing engineering for continuous improvement.
By implementing the factory of the future concept with Siemens’ digital enterprise portfolio, battery producers can counteract the risk of lower prices that results from potential overcapacity, accelerate time to market, and help the automotive industry to fully realize the potential of electric vehicles. Producers cannot only rely on superior battery cell chemistry to save their economics, but must also reduce manufacturing cost to maintain profitability. We expect the industry to go through consolidation and only the leading players who master the art will survive and lead the global market.
Vincent Guo is a Digital Manufacturing Business Consultant at Siemens Digital Industries Software.
—–
> Watch to this webinar to learn how EDAG and Siemens solve tomorrow’s battery manufacturing challenges today.
> Read this white paper to learn how to accelerate electric vehicle manufacturing by leveraging a digital twin.
> Try Tecnomatix Process Simulate Human software for free.
> Try Siemens Virtual Commissioning software for free.
—–
If you like this article, please give it a thumbs up! Let us know what you think in the comment section below.