What’s new in Tecnomatix? (June 2022)
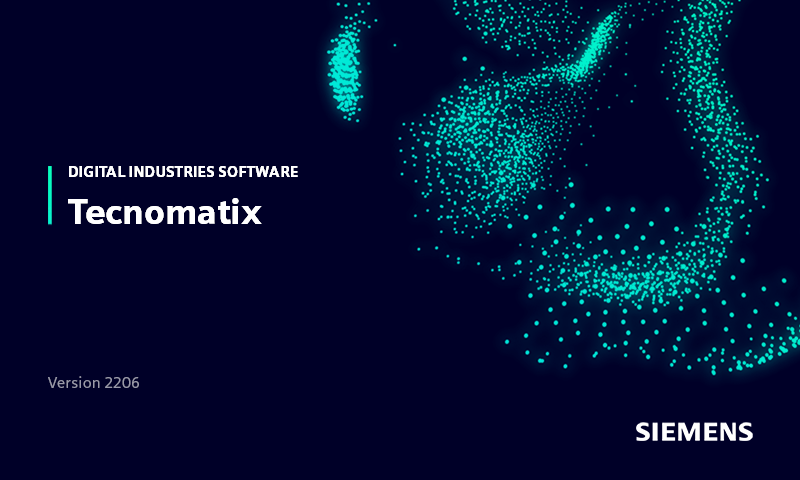
Digitalization for advanced manufacturing.
Digital manufacturing software in the Tecnomatix® portfolio is used by companies of all sizes in all industries to transform business and meet their strategic objectives. Tecnomatix software helps turn innovative ideas into transformative products more flexibly, more efficiently, and more sustainably.
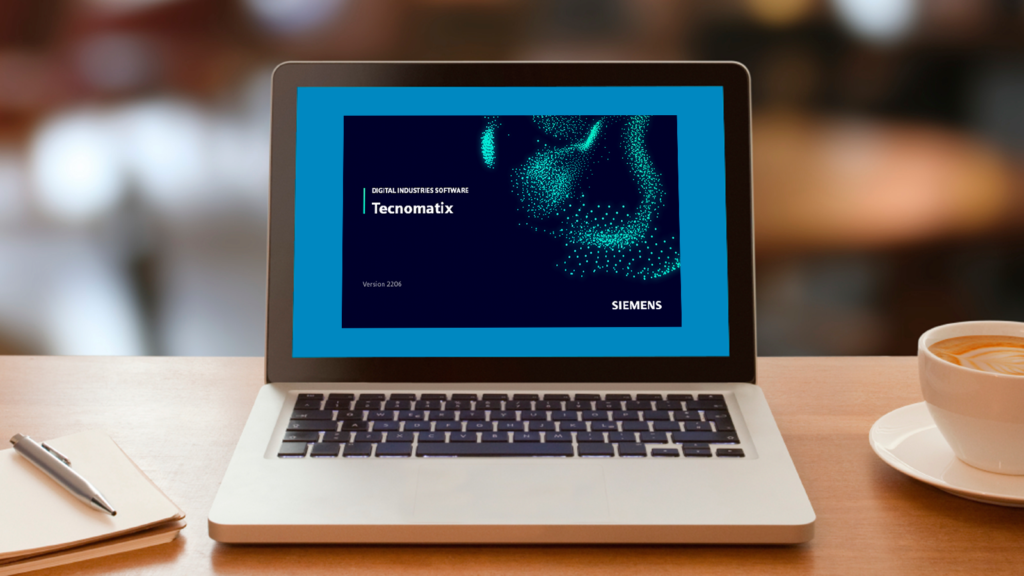
Tecnomatix 2206 was released at the end of June and delivers exciting new advancements. From Teamcenter connectivity and UI updates, robotics, offline programming, and virtual commissioning to human simulation and virtual reality, Tecnomatix software helps companies reduce manufacturing risk and develop better production operations.
You might be asking yourself, what is 2206? The new version numbering for Tecnomatix, starting with this version and for future releases, identifies the year in the first two digits, followed by the month in the second two digits for the current software delivery. In this case, 2022 and June, hence 2206.
As always, we are excited to deliver this new release to you!
You don’t have Tecnomatix software?
See the highlights from Tecnomatix 2206:
> General enhancements
> Robotics
> Commissioning
> Human
> Virtual reality
General enhancements
The following new capabilities are available in Tecnomatix 2206.
Product updates into a disconnected study
When loading a disconnected study with Process Simulate on Teamcenter (connected) it now is possible to use the Reload Product command for pulling product changes (parts and manufacturing features) that were previously not present in the specified operations or processes from Teamcenter into the disconnected study.
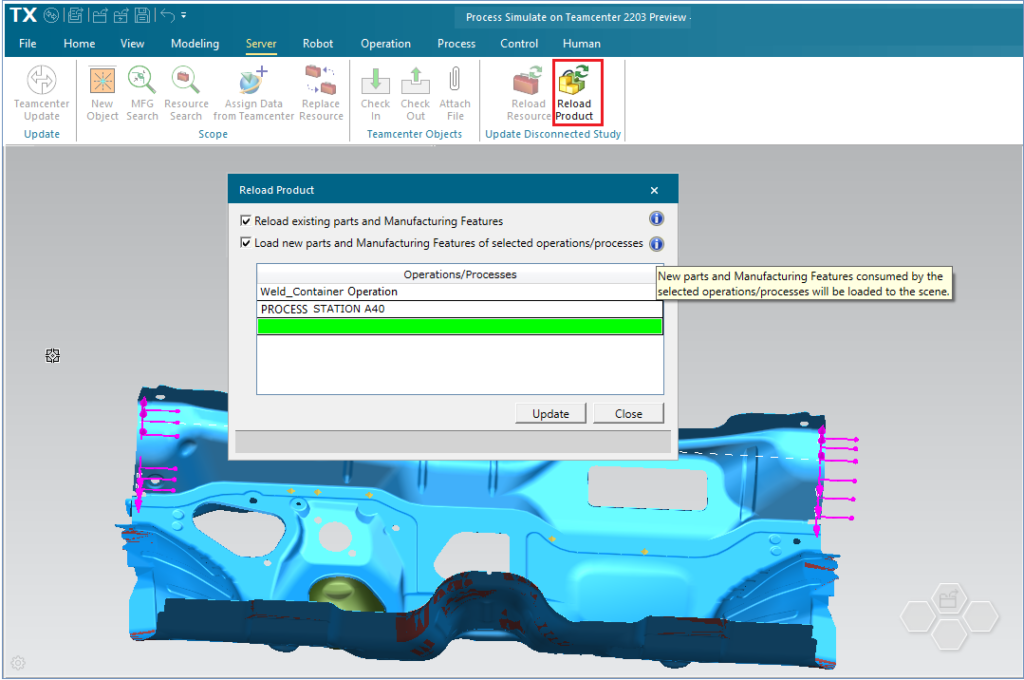
The command only considers product changes that are already in the scope of the disconnected study. It is also possible to use this command for loading parts and MFGs that are newly assigned in Manufacturing Process Planner (MPP) to selected processes and operations in the scope of the study.
This enhancement provides an efficient way to consume the product changes from MPP into the disconnected study.
Import of resource CAD files
In Process Simulate on Teamcenter, both connected and disconnected, you can convert and insert CAD files of resources into the loaded scene. It is supported for various CAD formats, e.g., CATIA, NX, DirectModel (JT), STEP, and more.
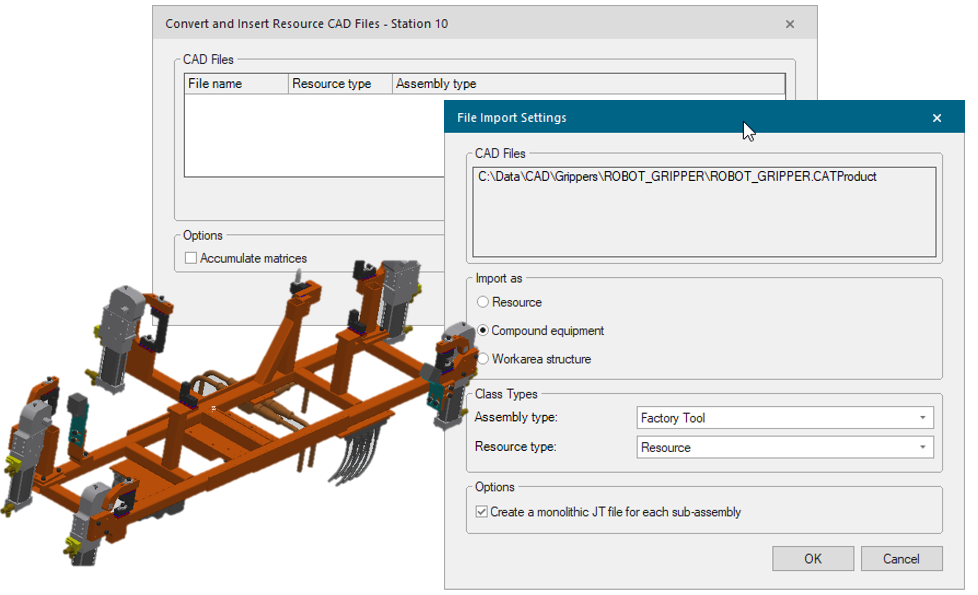
The CAD files can be imported either as a single resource object, a compound equipment object, or as a workarea hierarchy with resources below. When the source CAD file is an assembly, additional monolithic creation options are available such that it is possible to insert the imported assembly as a single monolithic resource or to create a monolithic resource for each sub-assembly. The imported resources are added below the selected parent resource and the added resources are always unique.
Continuous process generator
The Continuous Process Generator was enhanced to support additional use cases. A new option was added to create an adhesive process by simply clicking multiple locations on the surface.
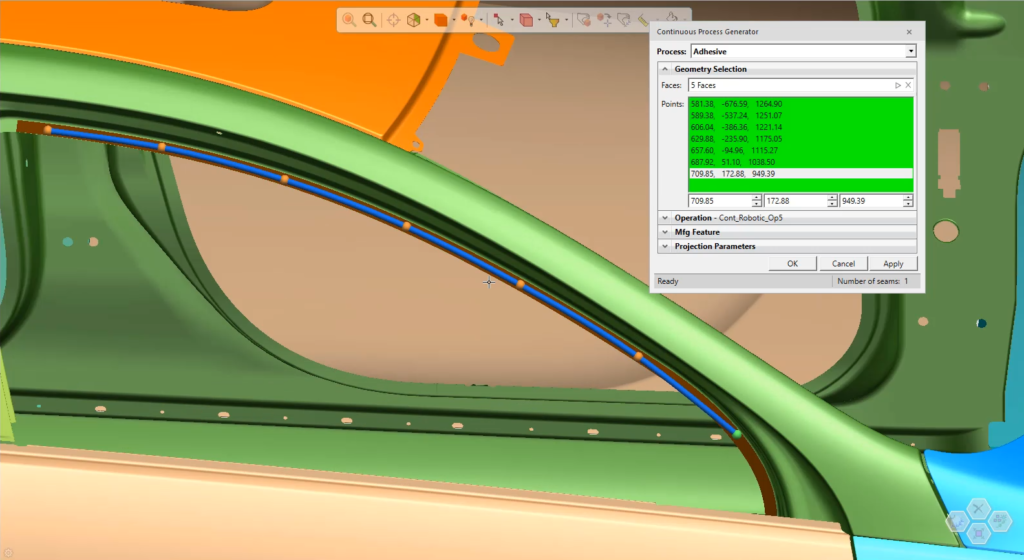
Also, the coverage pattern now allows for the control of the direction of strokes that can either zig zag or go in one direction.
Error viewer enhancements
Steps were taken in this release to improve the usability of the Error Viewer in Process Simulate.
Recurring messages are now grouped together so that the message displays only once, with the details regarding the impacted objects listed below. In addition, the messages are collapsible, so you can expand the message to display the details when needed.
A context menu is now available for the Error Viewer. It allows you to collapse and expand all messages, as well as copy all the messages, so that you can paste them in a text editor.
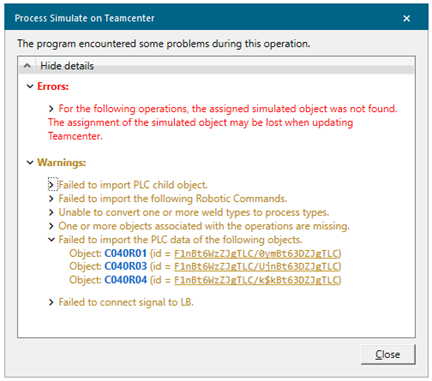
Object names in messages are now linked to their corresponding objects in the Process Simulate Viewers. Clicking an object name in an error message simultaneously selects it in the Object Viewer and the Graphic Viewer, enabling further analysis.
In the case of errors that impact hundreds of objects, instead of listing all the impacted objects, the number of lines displayed is limited to only the first few dozen messages. If you need to review the full list of messages for an impacted object, you can use the Copy All command from the context menu.
Flat UI style
Tecnomatix applications have been updated with the newer, flat controls look for dialog boxes and other user interface elements.
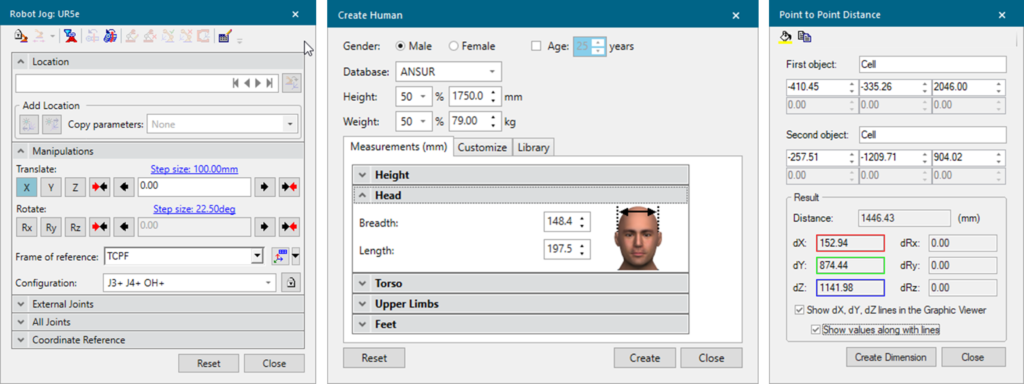
Robotics
Process Simulate Robotics helps you to program and validate your robotic processes in a dynamic 3D environment. It includes robotics applications for spot welding, metal processing, drilling & riveting, surface treatment, and assembly.
The following new capabilities are available in Tecnomatix 2206.
Realtime Robotics integration
Progress continues with the integration between Realtime Robotics and Process Simulate. Available now in version 2206 is a software-in-the loop (SiL) preview (beta) release of the integration. This SiL capability replaces the previous integration that was based on a hardware-in-the-loop (HiL) implementation, requiring a physical piece of hardware from Realtime Robotics (RTR).
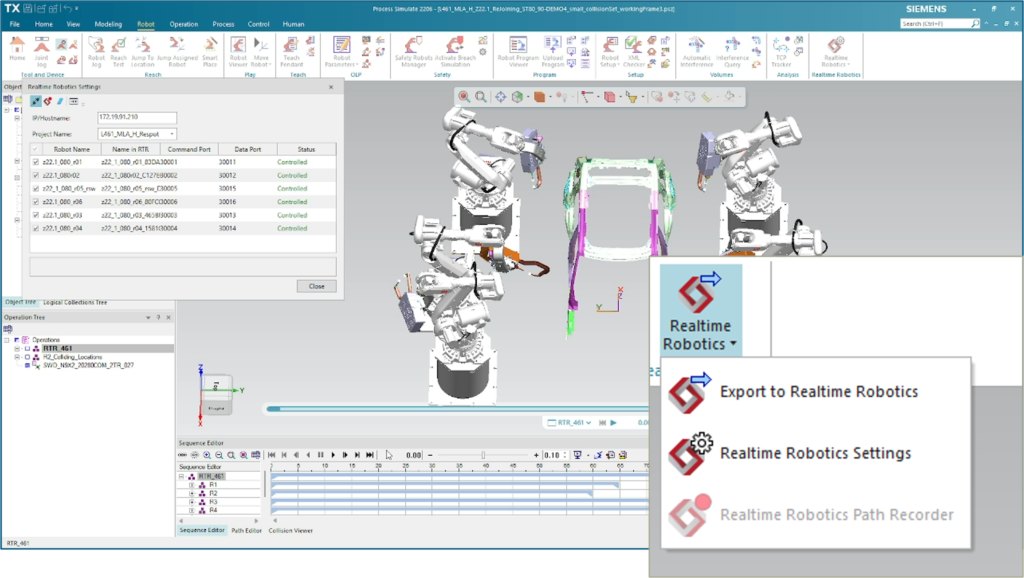
The new release adds the ability to connect to RTR without leaving Process Simulate as well as support for servo weld guns. This update provides the value of time savings with fewer steps and a fast and simple process of connecting to RTR and uploading a completed operation, greater clarity in the status of the simulation, and better error handling.
Automatic path planner interlock solving API
Tecnomatix 2206 now offers a public API release for the automatic path planner (APP). You now can use the APP public API to solve interlocking between multiple robots with the APP built-in command or the API to create a collision-free, optimized path for each robot.
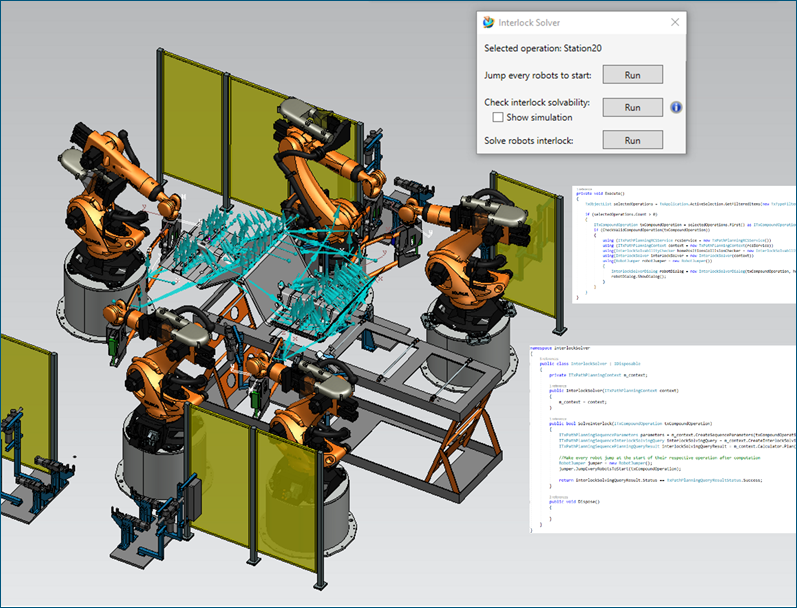
The interlock solving API can be used to synchronize all the paths. The APP API adds wait times on relevant locations to make the whole sequence collision-free. This update provides the value of time savings for synchronizing robots and solving for interlocking and is compatible with existing operations.
Offline programming free text to XML
The OLP Editor and Robot Program Viewer allow entering OLP Commands as free text. Now, all robot controllers such as those for ABB, Fanuc, and Kuka support the ability to automatically convert commands entered as free text into custom commands that exist in the custom XML file for that controller. This maintains your ability to add commands using a dedicated dialog designed in the UI Layer of the custom XML, but also allows you to use free text with manual entry or copy-paste while maintaining the connection to the custom dialog for easy editing.
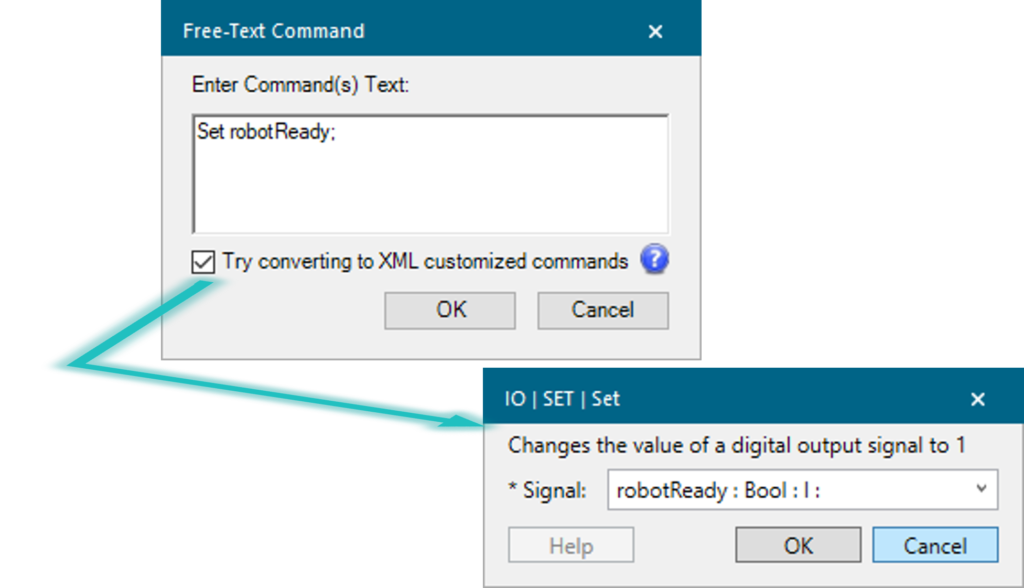
Offline programming comment out location
Now, in Process Simulate, you can comment out and comment in locations. Commented out locations essentially become program comments and are ignored during simulation, allowing you to evaluate a program without them, but without having to delete them. After validating the behavior, you can completely remove the location or decide to reinstate it. Uploaded programs with commented-out locations are also taken into consideration so you can upload shopfloor programs and check for any commented-out locations. Such locations can be toggled on, tested, and addressed. Commenting out a location can be easily done using the Path Editor or Operation Tree (“Commented Out” column) or Robot Program Viewer (right-click context menu when a location line is selected). This feature is supported when running the Fanuc-RJ, Yaskawa DX200, and YRC1000 robot controllers.
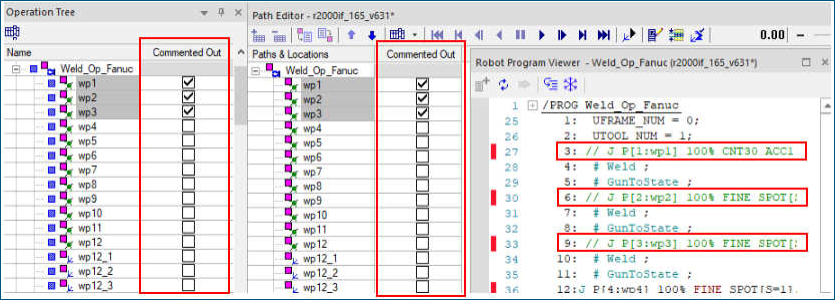
Offline programming debugging
The Robot Program Viewer features a new Watch tab that allows live monitoring and editing of robot variables. Simply enter a valid variable name in the viewer and it starts tracing the variable value live during simulation. This allows you or your robot programmers to easily watch the inner workings of robot variables and debug programs including complex handling in a better and much easier manner. Incorrect variable names are clearly indicated by the application to let you know of typographical errors and mismatches.
The Robot Program Viewer features the new Call Stack tab that displays the previously called robotic operations for the robot. The Call Stack panel allows you to trace execution when the robot steps into sub-routines by seeing their hierarchy and being able to navigate it.
Also, pause OLP commands now freeze only a single robot and not the entire simulation. Unfreezing a robot can be done through the Robot Program Viewer’s operator panel. This feature is supported for both default motion planner (MOP) based simulations and RRS-based simulations.
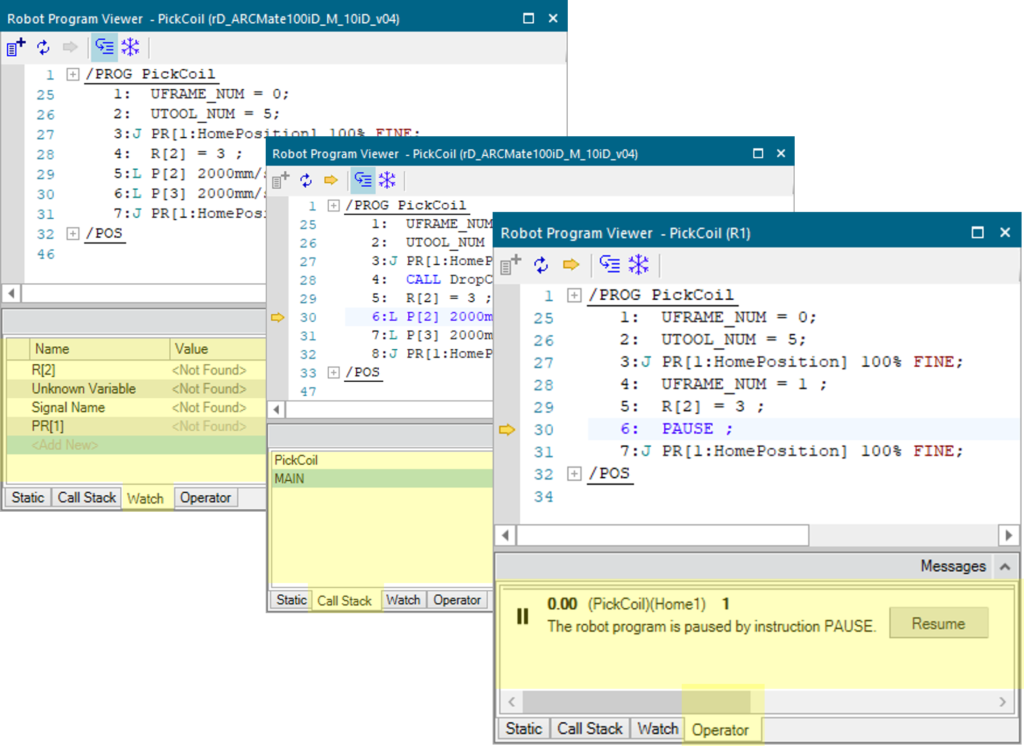
Virtual commissioning
Process Simulate Commissioning helps you to run the PLC code that controls the station to validate robot motion, robot logic, and other mechatronic components such as clamps, conveyors, and the entire process sequence. Virtual commissioning works with real PLCs (hardware in the loop, HiL) or virtual PLCs (software in the loop, SiL), or with the Process Simulate Cyclic Event Evaluator/Emulation (CEE) internal evaluation tool.
The following new capabilities are available in Tecnomatix 2206.
Material flow
Process Simulate now allows a new approach for material flow by using the SCL Editor. With the new Create Part Appearance and Destroy Part Appearance functions, the SCL Editor allows creating part appearances without any operation assignment or material flow transitions. Such material flows can be created in one place and are re-usable, as they are stored within components. Since it does not make use of operations, SCL-based material flow can run in the same manner in both SCL and CEE modes, saving you the effort of modeling it for both and reducing the differences between the two modes.
The new material flow approach leverages new .NET APIs that can be used by you and your developers to create your own custom material flow functions using the Process Simulate API. The SCL templates folder under the eMPower\Scripting folder includes several templates that can be used to define material flow using SCL.
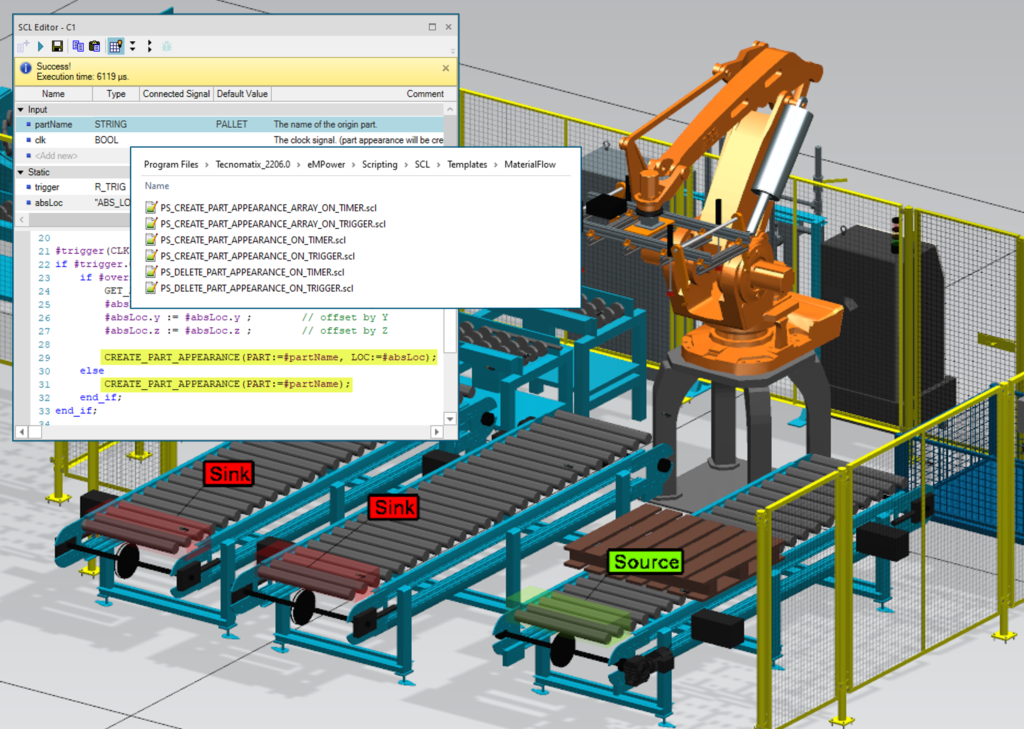
The Generate Part Appearance command now can be executed without any operation pre-selection and generates all available part appearances. This allows you to assign part appearances to other use cases, such as gripping lists, directly in line simulation mode even when no part is assigned to an operation. Additionally, you now can use Undo to reverse the results of the command, removing all generated appearances.
PLCSIM Advanced
In the PLC Connectivity area, the PLCSIM Advanced External Connection now allows exchanging memory bits and data blocks when using a name-based (symbol) connection. You can create input or output signals in Process Simulate, map their names to any memory or data block tag and exchange them during simulation. Input signals in Process Simulate are sent to the PLC and output signals are read from it. This allows you to read internal data from PLCSIM Advanced and avoid using workarounds and code changes on the PLC, such as writing DB or memory areas into the IO memory to exchange it with the simulation.
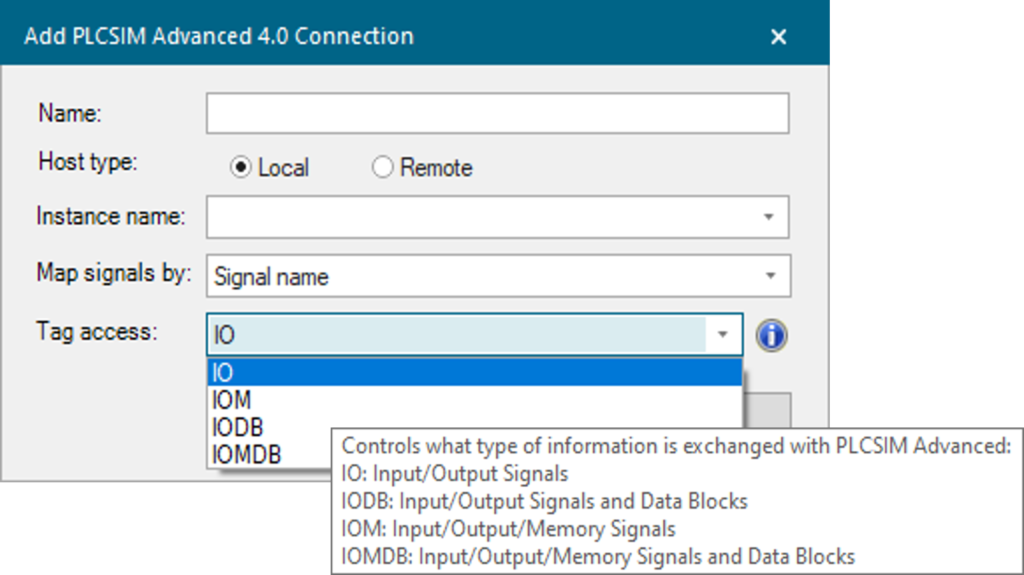
You can define the exchange filter setting per connection: IO, IOM, IODB or IOMDB to have the simulation only exchange the required information.
Simulation panel performance
The Simulation Panel now features improved performance in a variety of cases. You now can more freely add signals into the panel for monitoring and triggering and avoid significant performance slowdowns.
SCL editor improvements
The SCL Editor features several extensions allowing better usability and behavior modeling in Process Simulate. You now can make use of new math functions including trigonometrical functions (sine, cosine, tangent), inverse functions (arcsine, arccosine, arctangent), square root (SQRT) and square (SQR), exponential functions (EXP, EXPO, LN, LOG) and a random function. When a signal is connected to an input or output of an SCL block, the connection appears in the Signal Viewer’s resource column, as it appears for logic blocks. This allows you to easily find, sort, and filter signal lists that are connected to SCL blocks.
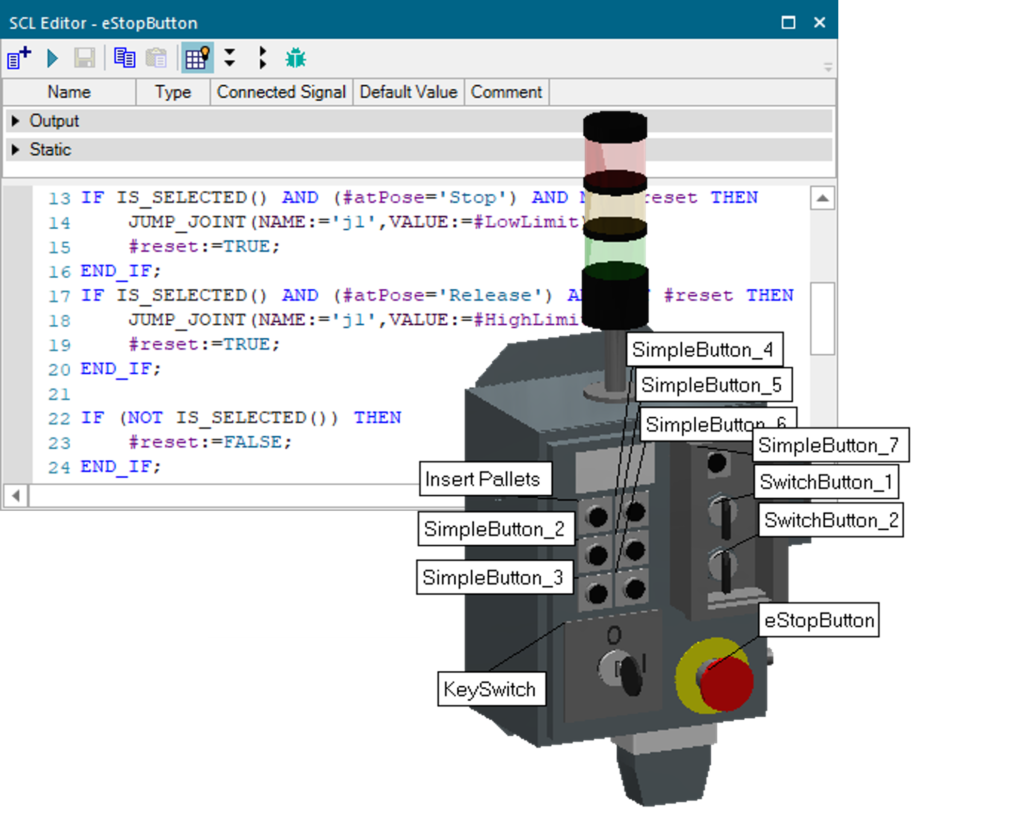
The new “IsSelected” and “IsPicked” functions return simple information to the SCL Block, if the SCL block (resource) is selected. This allows you to create functions based on user interaction such as keypads, buttons, and more, and use them directly in 3D and virtual reality.
SCL debugger
Now, you can debug Structured Control Language (SCL) scripts using a new standalone debugger provided with Process Simulate and started directly from the SCL Editor application.
The SCL Debugger allows you to track, navigate, monitor, and step through SCL code on any level to test and validate that it works correctly. You can load SCL scripts into the debugger and review the currently active line, call stack structure, variable values, and more. You can also step through code by easily using breakpoints or step-by-step execution to test and validate behavior models.
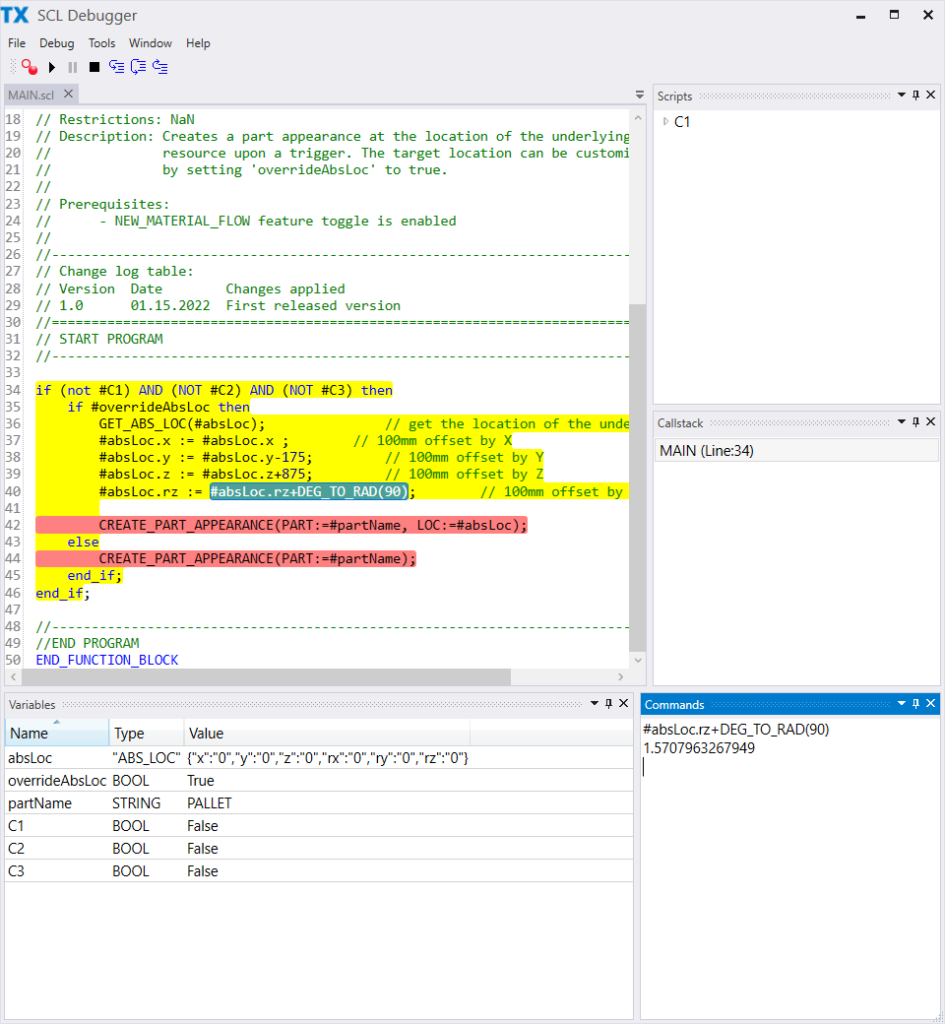
The SCL Debugger requires you to pre-install Microsoft’s Visual Studio Remote tools. Find additional information about this requirement in the online documentation.
Human simulation and ergonomics
Process Simulate Human helps you to eliminate any risk to operators with walk path analysis, reachability tests, vision analysis, and ergonomics assessments.
The following new capabilities are available in Tecnomatix 2206.
Enhanced scaling
Clearance, fit, and reach studies require accurate representation of human dimensions. In version 2206, ten additional anthropometric scaling parameters have been added to the scaling dialog, allowing for even more detailed specification of the figure size and shape.
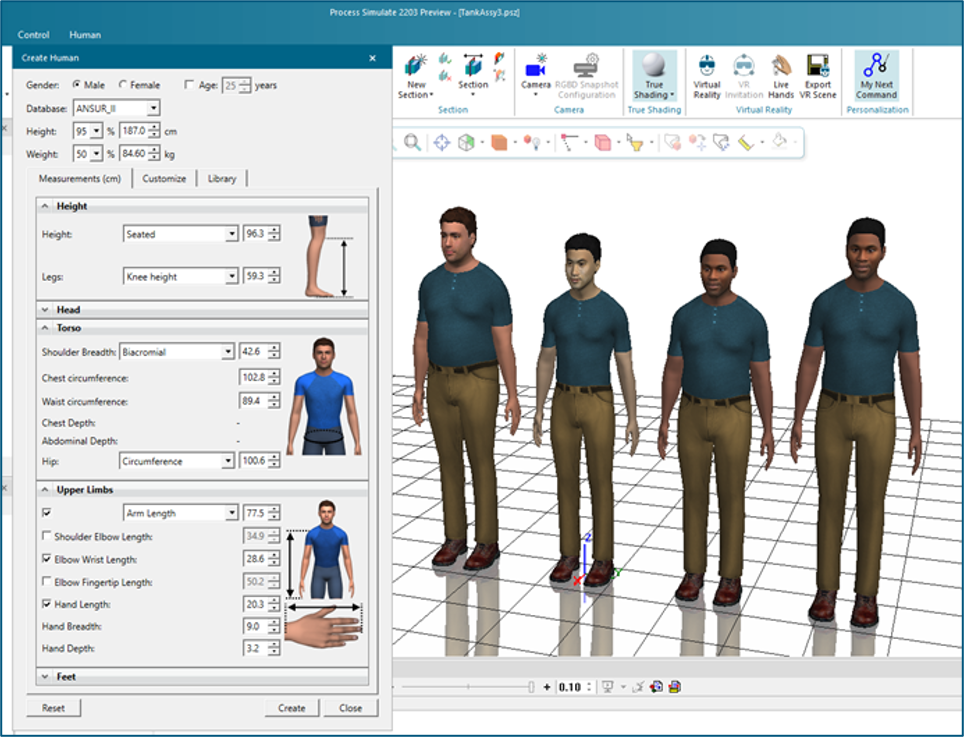
Scaling options for the figure head, torso, and upper limbs have been expanded, and the dialog layout has been updated for easy access to all figure definition inputs.
Swept volumes
Swept volumes of a human and their reach volume can now be created for TSB simulations. As the human moves, swept volumes of the head, torso, arms, hands, and legs are created, allowing you to review the space claims for the full figure, or individual body parts.
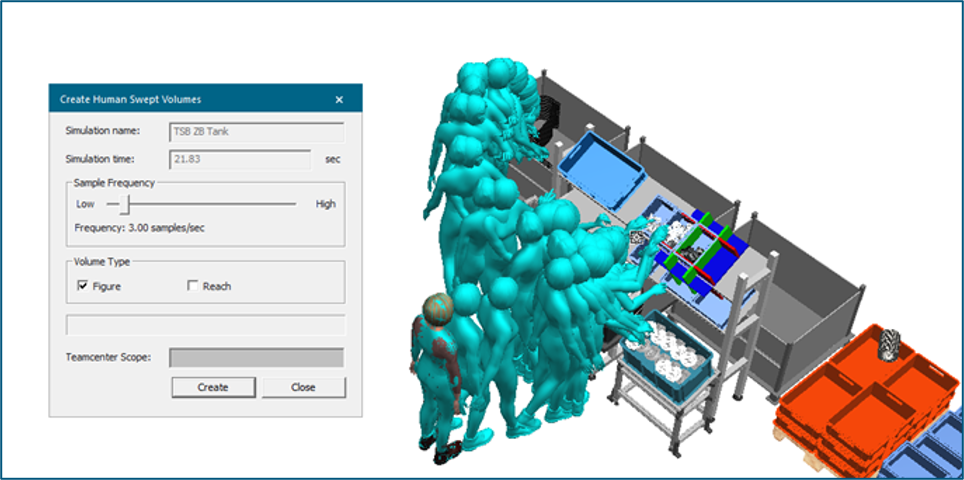
Swept volumes offers a unique way to assess potential collisions for the human while performing tasks and can also help to consider interactions with robots or other machinery in shared workspaces. Volumes can be stored with the study, and exported as .jt files to be shared with other colleagues or used in other applications.
Hand scaling for motion capture gloves
Using motion tracking equipment, human subject movements can be used to animate a virtual human avatar. With suitable hand tracking gloves, this can be extended to also include the hand and finger motions. Particularly for hand studies, an accurate match between the virtual finger dimensions to the real hand is needed to achieve realistic tracking results. While detailed hand scaling was implemented for disembodied hands in earlier releases, it is now also implemented for the hands on standard whole-body figures.
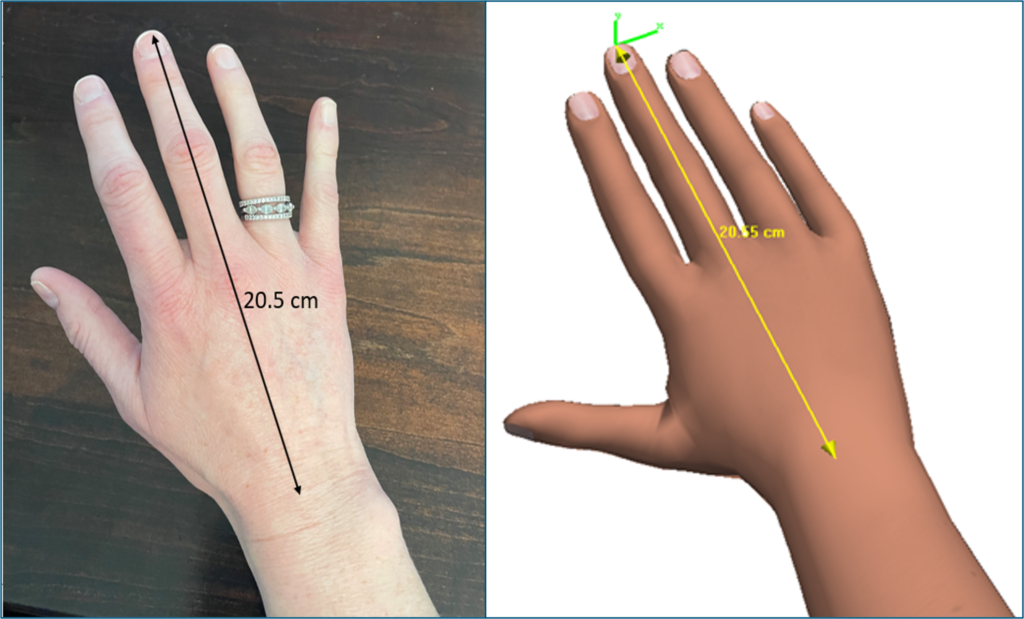
This allows motion tracking studies that utilize both whole-body and hand tracking to achieve the greatest accuracy. Hand scaling is handled automatically whenever a data glove is detected, so there is no additional setup required to take advantage of this improvement.
Cross platform figure support
Human figures that have been scaled and postured in NX 2206 or newer, now can be exported and loaded into Process Simulate. This cross platform human support allows for stronger collaboration between working groups, and more efficient processes.
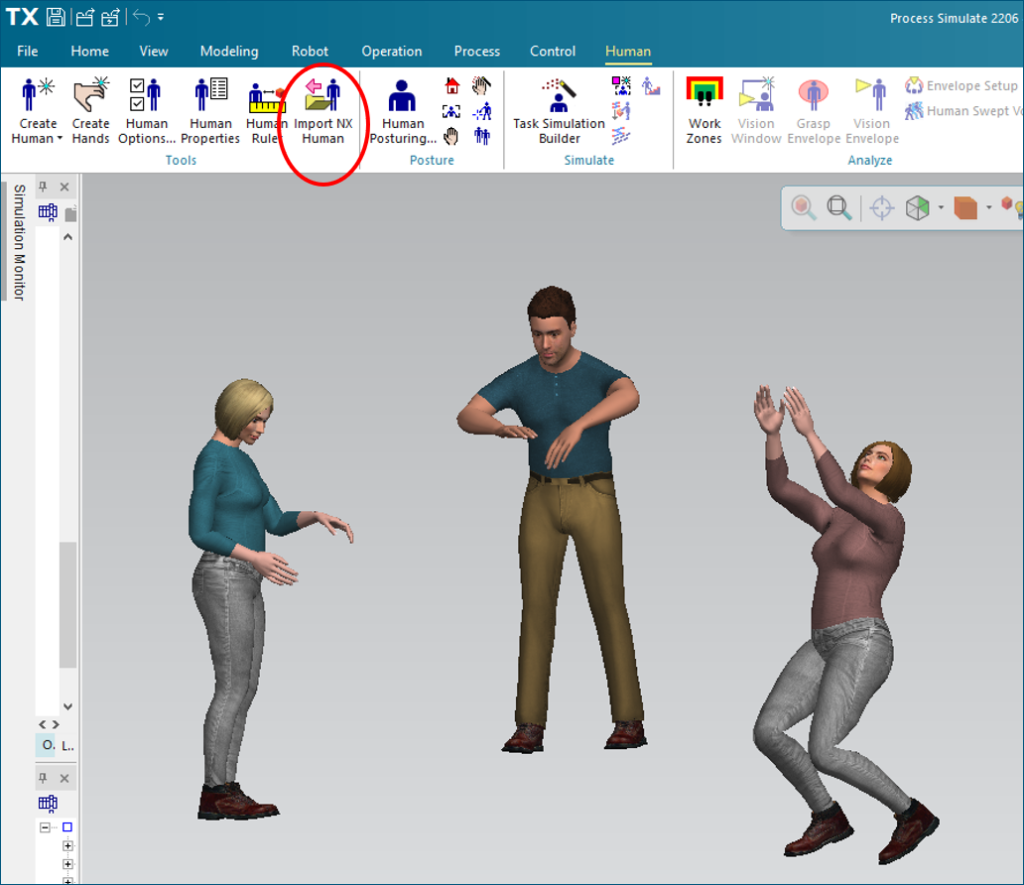
For example, human figures scaled and postured for design evaluation in NX can be transferred seamlessly to Process Simulate Human for more in-depth ergonomic assessments.
Virtual reality
Process Simulate VR delivers an immersive virtual reality environment for better engineering reviews, staff training, and realistic process validation.
The following new capabilities are available in Tecnomatix 2206.
Valve index controllers
In this release of Process Simulate Virtual Reality, we have extended hardware support to include the Valve Index controllers. These controllers feature sensors to detect basic finger postures. Seeing your virtual avatar’s hands move in tandem with your physical motions adds to the realism of the immersive experience.
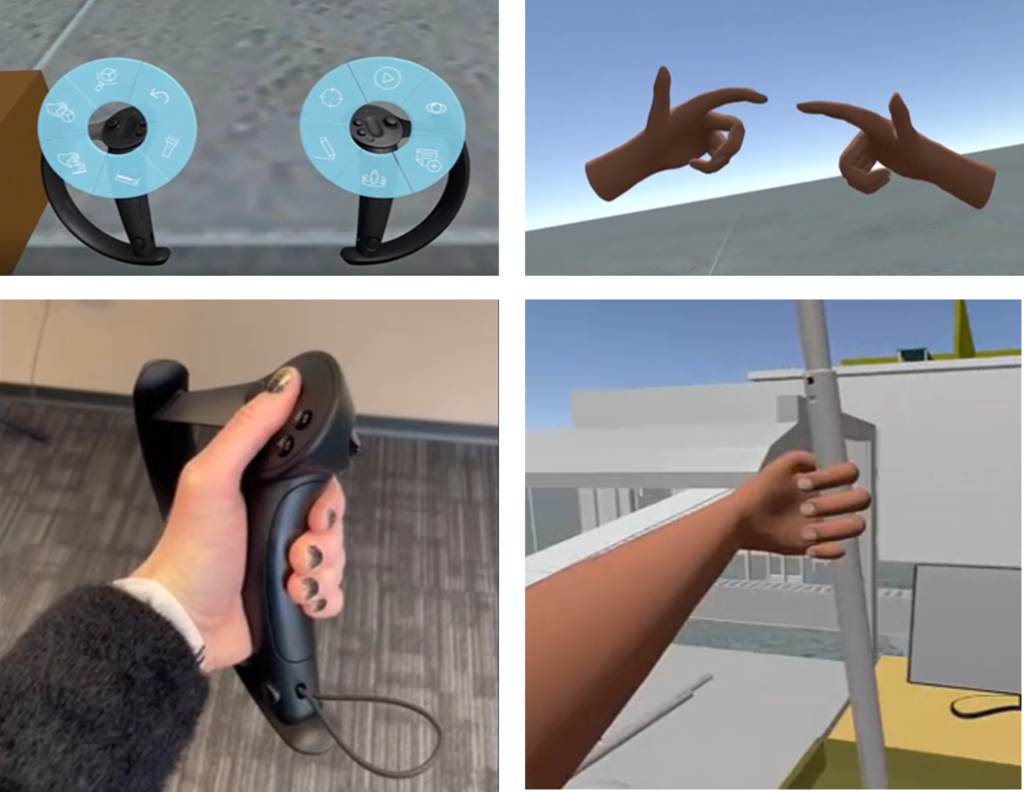
Hand shapes, such as power grips, pointing, trigger grips, and flat palms are recognized. When the Valve Index controllers are used along with VIVE full body tracking, you can explore the virtual environment and assess ergonomic issues with your body and hand movements.
VR sequencer
The VR Sequencer is designed to help you quickly define a task sequence in Process Simulate that can subsequently be experienced in virtual reality (VR).
In sequential order, objects are selected and added to a list in Process Simulate, prescribing the order in which they will be moved or assembled once you are immersed. Work instructions are automatically generated for each step and can be edited to provide additional details, if desired. Once in VR, a tablet appears in the scene displaying the instructions for each step, along with feedback about which steps have been completed. Arrows lead you toward the next step and show you where to place objects in the scene. Automatic virtual hand grasping of objects in VR adds to a natural experience.
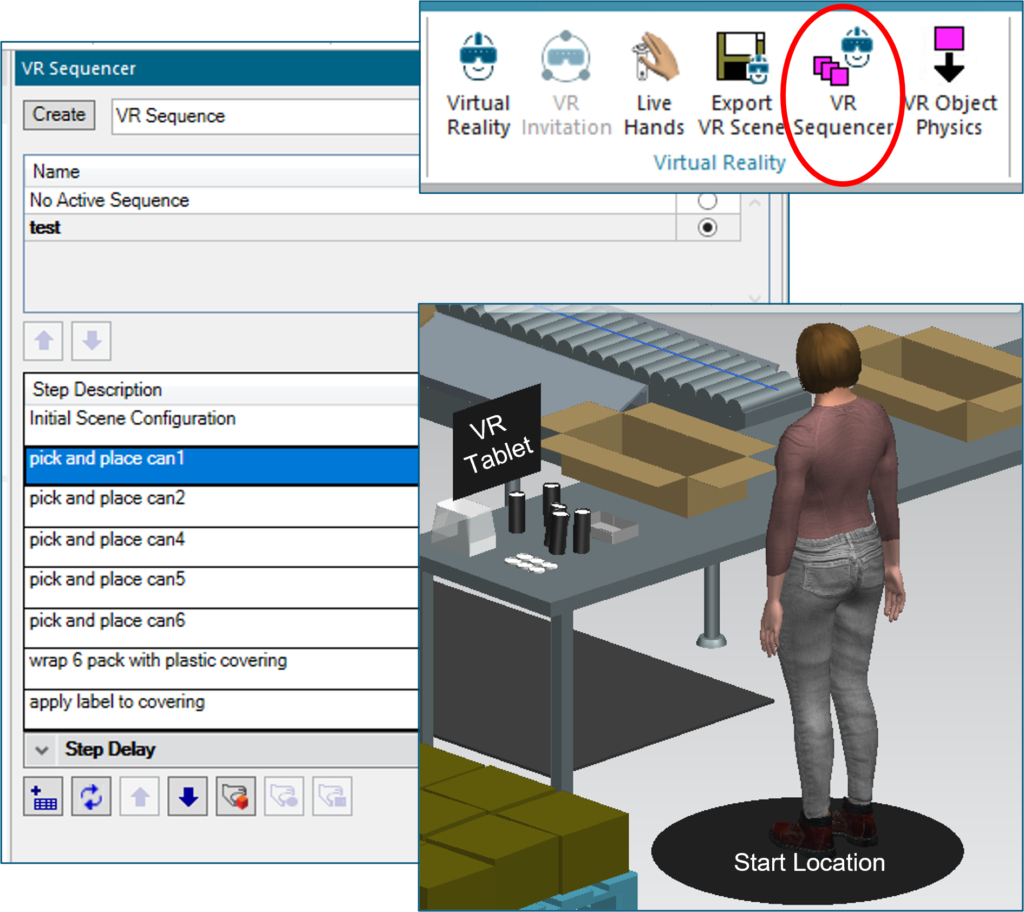
The VR Sequencer can help an individual become familiar with task sequences and learn operations. Times are recorded for sequence completion and the sequences can be repeated to assist with learning.
Object physics
For this release of Process Simulate Virtual Reality, object physics has been added to dramatically enhance the immersive experience. When using either Live Hands or VR Sequencer to pick and place items, the objects will respond as you would expect in the real world, falling naturally and rolling down graded surfaces.
This brings the virtual and physical worlds closer together allowing tasks to be performed more naturally, removing time consuming efforts to precisely place items in the virtual world. You can fine tune physics parameters to optimize performance and easily display or hide them on the VR ribbon menu.
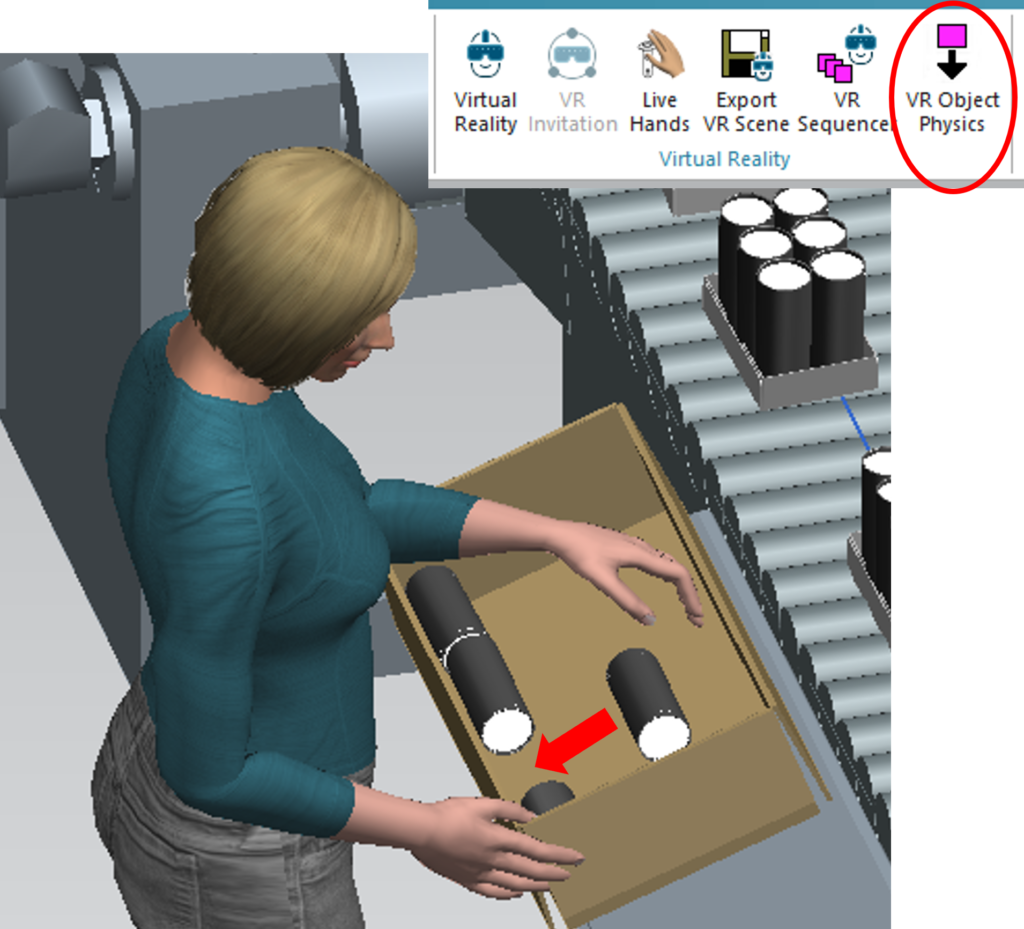
Full body tracking improvements
During a VR session, you can track body motions and assign them to a virtual human. For this release, the motion tracking has been improved, creating an even closer mapping between the real and virtual humans. Accurate motions ensure that analysis of posture, reachability, and physical performance can be completed with confidence. Natural motions in VR also promote a realistic immersive experience.
During a VR session, you can track body motions and assign them to a virtual human. For this release, the motion tracking has been improved, creating an even closer mapping between the real and virtual humans. Accurate motions ensure that analysis of posture, reachability, and physical performance can be completed with confidence. Natural motions in VR also promote a realistic immersive experience.
Watch this video to see how it all works:
In this video, you can see the sequence created with the VR Sequencer being performed in VR with guidance to teach and explore the defined steps. You also can see natural object behaviors using Object Physics and full body tracking in use along with the VR sequencer for a truly immersive experience.
Return to top. ^
—–
These are just highlights of the advancements delivered with the latest Tecnomatix release. For complete details on the new features of Tecnomatix 2206 and its supporting releases, please refer to the release notes and new features presentations offered with the software download.
And, as always, hop on over to the public community and website for all things Tecnomatix.
Yours in digital manufacturing,
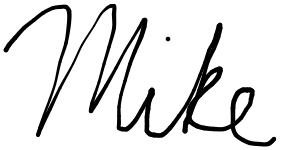
(on behalf of the entire Tecnomatix product team)
—–
You don’t have Tecnomatix software?