Moving Product Master Data Management closer to the product innovation epicenter
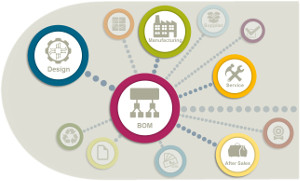
Previously, we’ve introduced BOM management at a high level, and taken a closer look at some key concepts including BOM configuration and product variant management. The issue of BOM and Product Master Data Management has come up in several places. Let’s take a closer look at this topic.
The Product Master
Data that drive the most business impactful activities of an enterprise are often referred to as Master Data. In industries that manufacture and sell products, data that define the content and configuration of these products is central to the Master Data and is referred to as the Product Master. The Product Master drives activities such as engineering, production, procurement, finance, short and long term planning and forecasting – activities that directly impact the top and bottom lines of the enterprise. Master Data Management that is well integrated with and serves these business critical activities is a necessary lifeline for manufacturing industries.
Bill of Materials
A Bill of Materials (BOM) usually refers to a list of items – parts, assemblies, consumable materials – that is required to assemble or manufacture a product. A BOM for a specific product is derived from the Product Master data by supplying appropriate contextual information – such as the specific configuration, and purpose for which it is being requested (eg. for production at a given plant, for engineering analysis etc.).
Why is a ‘high definition’ BOM critical?
A ‘high definition’ BOM is richly qualified with supporting information that is relevant to the request context. Easy inline access to 3D visualization, design, manufacturing, procurement, service, or other relevant data makes the BOM ‘visual’ as compared to traditional BOMs that tend to be textual parts list reports.The availability of a high definition Bill of Materials on demand accelerates operational decisions and activity, thus providing a competitive edge to the business.
What is the situation with BOM today?
Product Master Data management and BOM management are very fragmented today at the vast majority of manufacturing firms. By this, I mean that the means to arrive at an authoritative Bill of Materials for a product for a given configuration and purpose along with all the relevant qualifying and supporting information usually involves several systems and multiple touch points between these. Engineering, Manufacturing, Plants, and Service departments often have their own systems that hold their ‘version’ of the BOM and changes to one need to be reconciled with the others through paper based or other time consuming processes.
The BOM that is closest to manufacturing is the often the de-facto ‘master’, since not disrupting production has traditionally been considered more critical than speed of consuming product innovation.
After all, loss of production can be directly and immediately traced to the top and bottom lines whereas the effect of slowness in consuming product innovation is not perceivable till much later. This ‘manufacturing’ BOM is usually restricted to ERP systems and cannot directly access all the rich engineering data that is central to product innovation.
The increasing urgency of the need to innovate and reduce time to market for new products is driving the Product Master Data Management and BOM management balance to shift towards the innovation end of the product lifecycle. PLM systems in general and Teamcenter in particular are well established in managing product data for the innovation lifecycle. This ‘innovation’ product definition includes data produced by or for Design, 3D Visuals, Requirements, CAE analysis, Digital Mockup activities etc. Locating the Part based Product Master BOM within the PLM system where direct access to this innovation data is readily available is very valuable to be able to make informed decisions for planning, engineering, manufacturing and support.
What is the Teamcenter approach to BOM and Product Master Data Management?
Teamcenter recognizes the need for Product Master Data Management and BOM management closely aligned with engineering data as well as with all downstream consumption needs. Our Integrated Product Definition approach in Teamcenter promotes engineering definition and formal release as well as direct annotation of the engineering released BOM with information that is relevant to multiple consumption purposes – such as manufacturing, service planning, procurement, costing, production at multiple plants etc. – so that the right context relevant view can be derived directly from the Engineering BOM by appropriate consumers. This approach allows for engineering changes to be visible to all consumers and reduces effort that goes with maintaining and reconciling copies of the BOM.
Importantly, product master data management, including the Product Master BOM, within the PLM system allows the BOM to be ‘high definition’ and promotes informed and efficient decision making processes throughout the product lifecycle.
About the blogger: I am a member of the Teamcenter Product Management team, focusing on Bill of Materials management.