Streamline quality audit and assessment with Teamcenter
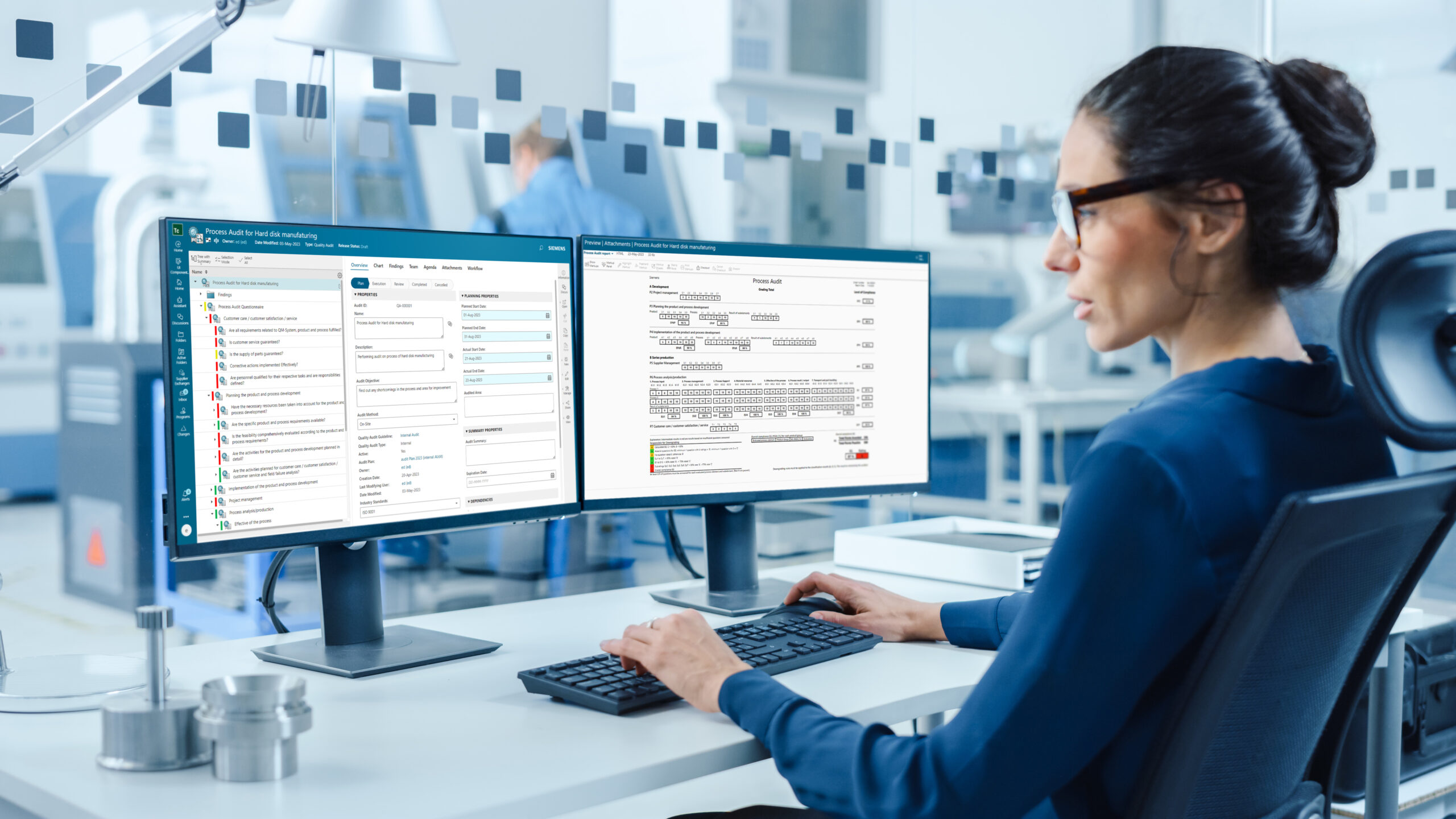
Quality audit and assessment. How to drive best practices by using the unique Teamcenter collaboration platform
During my 15 years as a user of quality management systems (QMS) in the automotive sector, including my involvement in QMS rollouts at several plants and locations, I experienced firsthand the challenge of “digital gaps.” In particular, quality assessment tools used to create audits typically were stand-alone software components, resulting in a gap between quality and compliance efforts. Consequently, the value gained by processing the audit findings and using the problem-solving process is reduced and effective lessons learned are not fully integrated into quality processes.
So naturally, when I came onboard at Siemens Digital Industries Software, I was on the lookout for technology that closes this digital gap. I’m happy to share with you the results of this effort. Our recently released Teamcenter Quality includes the new Teamcenter Quality Audit & Assessment module, which uniquely supports efficient audit processes through a unified collaborative platform. Allow me to tell you a bit more about the challenges of quality audit management and how Teamcenter Quality Audit & Assessment overcomes them.
Why a quality and compliance gap makes quality auditing difficult
Despite the quality objectives of the industrial/manufacturing sectors, quality and compliance sometimes feel at odds with one another. Theoretically, compliance measures are designed to ensure the quality and safety of your products, in conformity with enterprise quality management policies. Quality and safety are required in the manufacturing processes you use and in the products you deliver.
In my experience, however, the rigor and evidence required by many regulatory and industry standards have unintentionally led to burdensome efforts in documentation. All too often, it seemed that our compliance efforts became document-driven rather than quality-driven.
This clash is particularly apparent when audits and assessments are conducted in a traditional system, where different aspects of quality and compliance are managed as independent silos within disconnected systems. The quality department is focused on ensuring that the manufacturing process and as-built product achieve the quality and safety standards established in the as-designed and as-planned product. The compliance department and associated auditors (both internal and external) are focused on demonstrating to regulatory and industrial bodies that the process and product conform with their standards. These points of focus can and should be complementary, but siloed systems hinder cross-departmental interactions and create a considerable risk of discrepancies between the two.
Our vision for complementary quality audit and compliance
At Siemens, I joined a team committed to offering a solution that ensures continuous, real-time compliance with main quality standards and industry guidelines while also facilitating efficient achievement of product and process quality. We recognized three key requirements our solution must meet to achieve this goal. First, an integrated and collaborative digital backbone for data and documents would provide visibility for all stakeholders of relevant cross-departmental information, and that information would always be up-to-date. Second, a comprehensive quality management system would oversee:
- Design and production control
- Process validation
- Employee training and risk management
- All relevant and up-to-date regulatory requirements and industry standards
Third, the solution would establish data and trace transparency, especially in the case of third-party certification or customer audits.
Siemens Teamcenter Quality supports all three of these requirements. It is built on top of the Teamcenter product lifecycle management (PLM) backbone, facilitating cross-departmental workflows, and it supports a closed-loop quality approach from design to manufacturing. Traceability is a cornerstone feature of all Teamcenter modules.
Meet management needs with Teamcenter Quality Audit & Assessment
Teamcenter Quality 2312 provides a unified quality management solution that shares data and actions across all quality-relevant processes. It serves as the collaborative platform that supports all audit and assessment efforts. The Teamcenter Quality Audit & Assessment module is native on Teamcenter, as are all Teamcenter Quality modules.
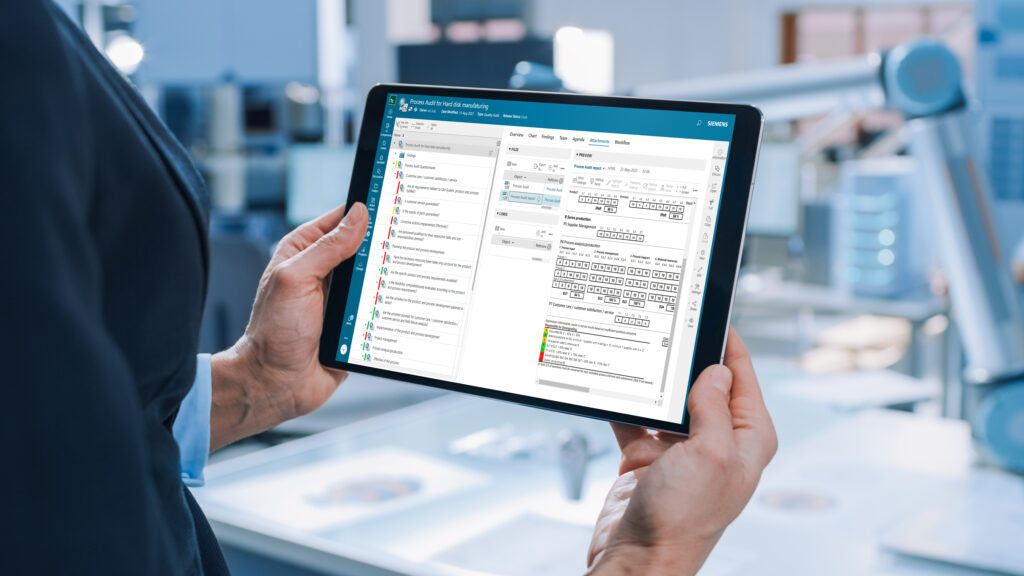
While Teamcenter Quality Audit & Assessment is a comprehensive audit and assessment tool with a wealth of features, I’d like to focus on three key functionalities the module offers.
- A highly configurable workflow enables users to track and document the audit process all from one view. The workflow supports all audit milestones: planning, execution, review and closure.
- Fully integrated and flexible capabilities let users build and complete audit-specific questionnaires. Operating within the Teamcenter ecosystem, Teamcenter Quality Audit & Assessment is linked to master data and Teamcenter version management, ensuring that audit checklists/questionnaires are built on accurate, up-to-date product, process and compliance data. Questionnaires may include regulatory compliance questions as well as customer-specific questions related to quality. Users can employ answer/rating options and assessment rules provided in Teamcenter Quality or their own answers, ratings and rules. Fully integrated and traceable with all Teamcenter modules, the audits can be triggered or referenced by other modules, such as Teamcenter Change Management or Vendor Management.
- Template functionality provides users with pre-defined audit questionnaires and audit data that can be used as-is, modified and reused. This reduces tremendously the effort involved in creating audits. Users can also set up series based on these templates, so that the system automatically creates audits out of a template in a defined timeframe.
One platform benefits for quality audit management
With the robust and flexible audit management process, our customers can support efficient audit planning and execution, as well as analysis of audit results that verify quality control processes and enable continual improvement – all fully aligned with regulatory standards and industry guidelines.
Using Teamcenter Quality Audit & Assessment, it’s possible to identify and manage key risk factors, mitigate potential negative impacts, and eliminate redundancies to streamline processes, saving both time and money. I hope you’ll consider learn more about Teamcenter Quality Audit & Assessment today!