What’s new in Teamcenter Quality 2312?
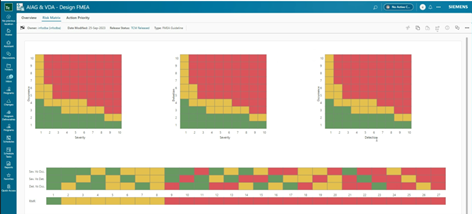
We are thrilled to announce the release of the latest version of Teamcenter Quality software!
Table of Contents
Relying on guided and standardized best practices for quality and compliance management
Teamcenter Quality software supports a closed-loop quality approach from design to manufacturing. Built on top of the Teamcenter software product lifecycle management (PLM) backbone, Teamcenter Quality helps you leverage product and process information, as well as share cross-departmental workflows so you can streamline the core quality management processes.
Teamcenter Quality works in the Active Workspace client (AWC) for Teamcenter. Active Workspace is an innovative web-based client platform that simplifies PLM for all users involved in product lifecycle, accelerating user adoption and shortening time-to-value by providing an intuitive experience anytime, anywhere, on any device.
Discover the greatest news about Teamcenter Quality
Teamcenter Quality version 2312 includes a new module release, Teamcenter Quality Audit & Assessment, and features improved application capabilities and usability. Our expanded set of supported quality core processes offers you access to the most up-to-date set of technologies to streamline your quality management system (QMS), including compliance tasks.
To harmonize the offerings across Siemens Digital Industries Software, Teamcenter Quality is being moved to year- and month-based version numbering. Version 2312 stands for the December (12) release in 2023. Therefore, version number 2312 follows version number Teamcenter Quality 6.3.
Audit and assess core processes for continual improvement
Company-wide audit management requires a structured system solution that provides benefits if it is integrated in QMS processes and accessible to all relevant stakeholders. The growing importance of audits has set the standard for boosting the performance of auditing procedures.
The new Teamcenter Quality Audit & Assessment module provides the tools to help with tasks, such as:
- Audit planning and creation – The auditor can create a new audit plan and related audits with their agenda, adding the main stakeholders to involve in the formal auditing process. The auditor can prepare specific quality checklists and define evaluation criteria with an automatic grading system. With all these data well set, the auditor can schedule and initiate the audit session.
- Audit execution – The auditor can implement a simple, straightforward audit management process. The auditor can identify weak points or best practices while focusing on core processes.
- Audit review – The auditor can use quality problem-solving methods, including Ishikawa diagrams and the 5 Whys technique, to analyze the root cause of the audit’s findings. Then the auditee can initiate actions to correct these deviations.
- Audit closure and controlling – At the end of the audit process, the auditor can create a report with all the required documents that have been prepared during the evaluation stage.
With an efficient audit process in place, manufacturers can identify potential risks and eliminate redundant activities to streamline their processes, saving time and money. Importantly, audit management best practices give the management team confidence there is a structured procedure for continual quality improvement, helping the company meet its business objectives.
Key new features
Teamcenter Quality version 2312 incorporates several improved application capabilities and features.
- Keep all relevant data in the QM workspace. Starting from version 6.1, using Teamcenter Quality enables you to work in a quality management (QM) workspace. The QM workspace has been further extended and improved. After opening the application, a preconfigured view appears, which can be adapted by the service at any time. As an additional improvement, Active Workspace has a new tile for each module.
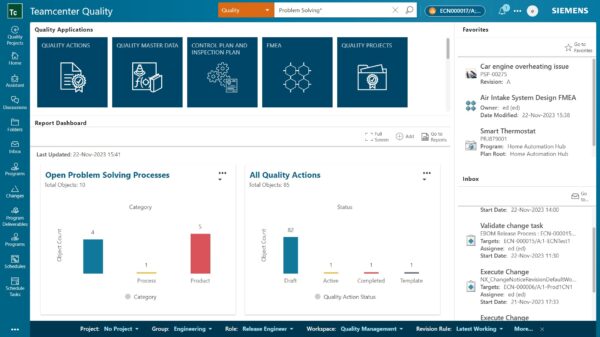
- Enhancing quality capabilities for Q-gates and checklists. The focus in the current version is to assess the questions and the entire checklist with enhanced quality master data and functionalities for quality checklists. The checklists have been extended for use in quality project management, especially for mapping the supplier production part approval process (PPAP). In the Quality Project Management module, if an activity is associated with the delivery of one or more documents, it can be directly attached to the question/task on the overview page. Using Teamcenter Quality now allows you to streamline more of these tasks with improved capabilities to track quality projects such as advanced product quality planning (APQP) or supplier PPAP projects.
- Improved FMEA tools and linkages provide quality deliverables. The Teamcenter Quality FMEA module helps you avoid defects by allowing you to evaluate the effects caused by potential problems early in the planning phase. The Teamcenter Quality FMEA version 2312 provides an essential piece of the puzzle to fully support the methodology, which is related to introducing special characteristics, and can be defined for failure representations inside FMEAs. You can already derive a control plan from the process FMEA. Now if a control plan was created with improved visibility for control plan linkages, the user can see it in the FMEA. Displaying the control plans derived from the respective FMEA continues to improve closed loop quality. Implementing the risk matrix in the last version was already a valuable addition. Now the risk matrix is enhanced with the risk matrix results (RMR).
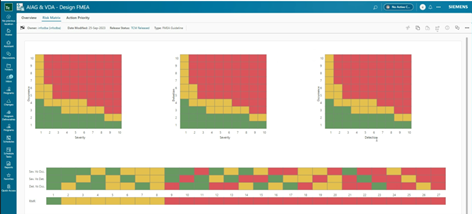
- Optimize planning quality inspections. You can use Teamcenter Quality Control and Inspection Planning to improve product quality while decreasing development time. In the latest version, enhancing naming rules are available for the quality master data. A new attribute – decimal places – has been introduced for variable characteristics based on the number of decimal places for nominal value and tolerances that are shown. The support the automatic ballooning of characteristic-relevant information has been improved, especially with the model views defined in the 3D model. Beyond the enhanced ballooning functionality, other enhancements for better usability are available. Multiple references can be added inside the inspection definition or on the control plan level. Another important element is the possibility of copying the control plan structure, a new duplicate function offers the possibility of copying the complete control and inspection plan structure.
- Realizing smoother problem-solving process. The Teamcenter Quality Problem Solving module comes with additional updates in version 2312 to include valuable enrichments such as in root cause analysis (RCA). Another improvement is related to quality checklist functionalities that impacts the root cause analysis. Many new functionalities are provided in the checklists, that includes checklists for problem-solving process (PSP), too. One of the most beneficial features of this latest version is the definition and key performance indicators (KPIs) in standard reports for overall PSPs.
- Improved quality actions management functionalities. Using Teamcenter Quality offers quality action management (QAM) capabilities for creating and performing actions in the context of several Teamcenter Quality modules or as a standalone action. In the QAM, it is now possible to add new supplementary proprieties to each action, such as graphic symbols to highlight the action status.
Benefits of our quality management solution
- Efficiently manage the quality checklists for better assessment
- Simplify tasks on quality project management best practices to manage quality and project milestones
- Deliver enhanced FMEA tool
- Optimize planning quality inspection leveraging drawings and models
- Provide greater defect descriptions to facilitate problem solving
- Close the loop in your root cause analysis with a deeper evaluation
Experience the advantages of the closed-loop quality and start your digital journey with Siemens today!
Would you like to get a general overview of our offerings of quality management software?
Take a few minutes to look into our new Teamcenter Quality 2312 fact sheet, or learn how to experience the benefits of closed-loop quality for best-in-class products with our videos experience.
Are you interested in more details on our quality management software solution components?
Take a deep dive by reading these product fact sheets:
- Teamcenter Quality – Problem Solving
- Teamcenter Quality – Control and Inspection Planning
- Teamcenter Quality – Failure Mode and Effects Analysis
- Teamcenter Quality Project Management
- Teamcenter Quality Action Management
- Teamcenter Quality – Audit & Assessment
Find out more about quality management and compliance on our website!
No matter how you choose to deploy Teamcenter,
you get the same proven solutions designed to help you innovate faster.