Modern Work Instructions Software for Engineer-to-Order Manufacturing
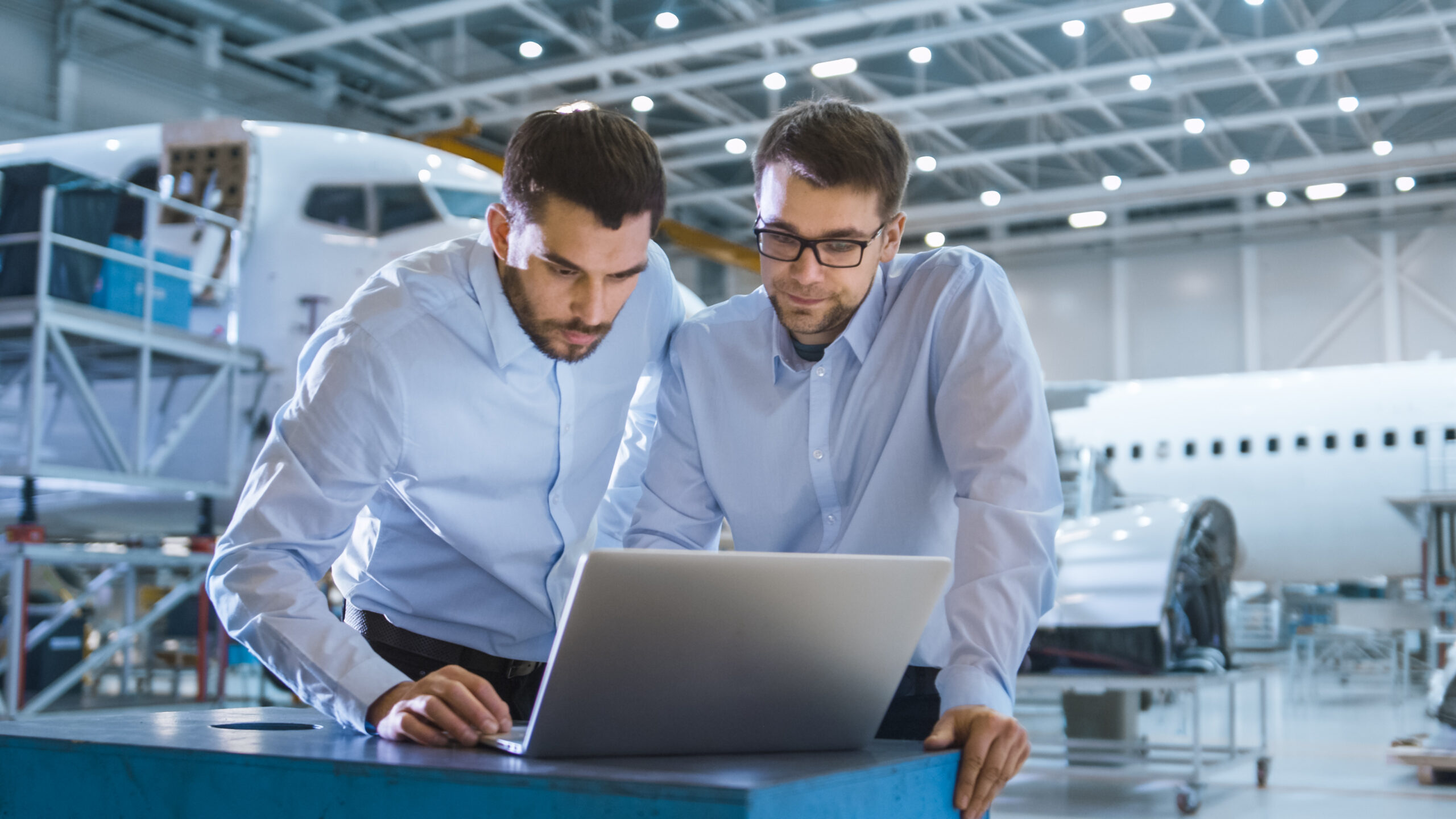
Save time and improve quality with modern work instructions software for complex manufacturing and change processes. Read on to learn more.
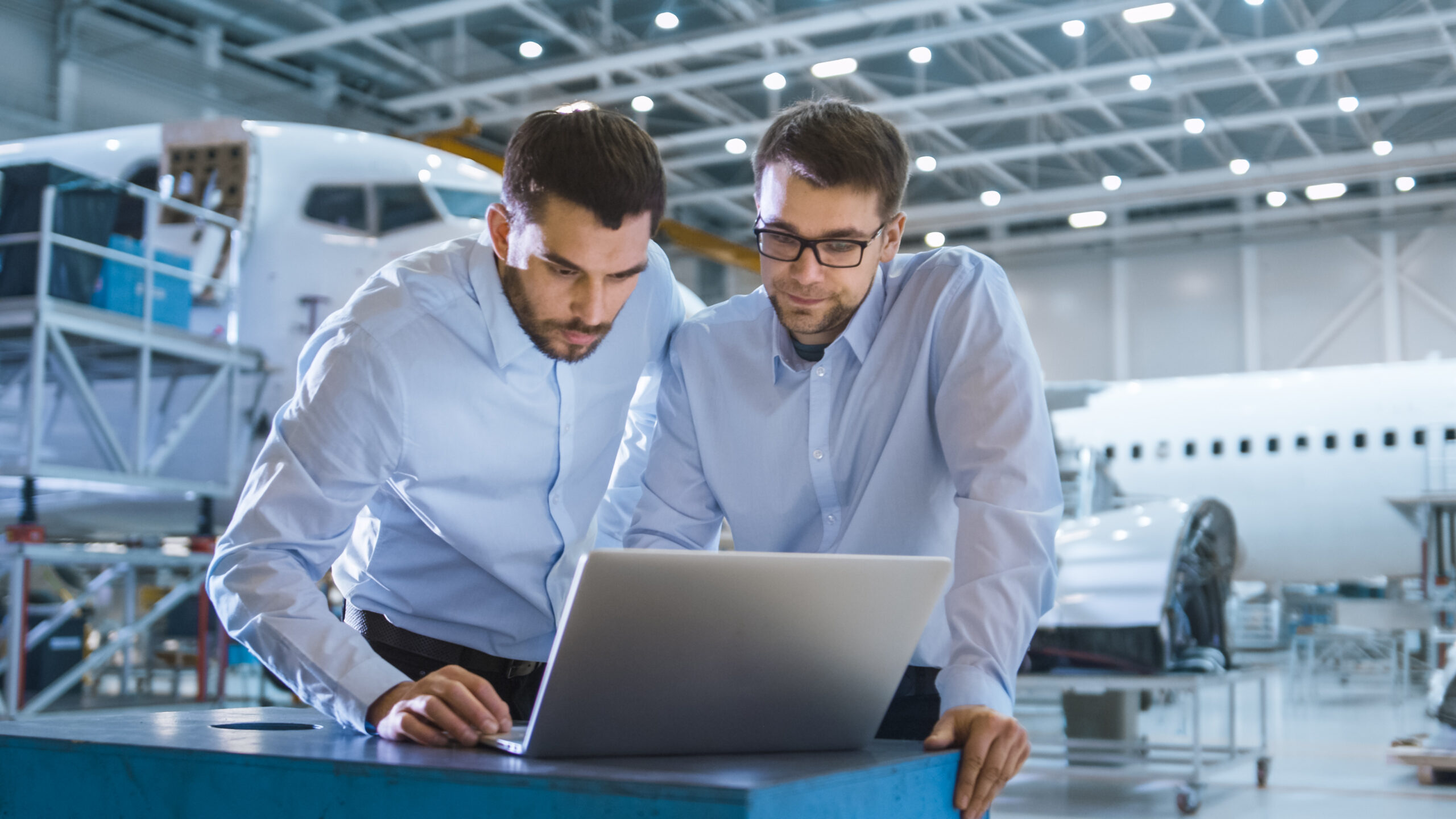
Having worked in the manufacturing industry for decades, specifically with engineer-to-order (ETO) processes, I have seen tremendous innovation in products, and in systems that support the manufacturing of those products. Airplanes, ships, industrial equipment, and other complex, high-value products have become more sophisticated, with many custom options to choose from. While manufacturing processes for these products have also evolved, one of the basic requirements for quality remains the same: the correct manufacturing steps must be communicated accurately to the right technician on the production line.
Challenges to electronic work instructions
In digital manufacturing, the function of communicating step by step procedures on how to manufacture products is accomplished by work instructions software, commonly referred to as Electronic Work Instructions, or EWI. As engineering and manufacturing processes have evolved, many disciplines have become involved in the product and production lifecycle process, from initial design, to assembly, to delivery of the product to the customer. With so many stakeholders working in an ETO process, and the movement of data from design to the shop floor, the challenges for EWI have grown.
When we consider the market today, with new customer requirements coming in at a rapid pace, and new production techniques for new materials and systems, the need for change is accelerating. In each step of the production process, a critical priority to manufacturers is ensuring that required manufacturing process changes are easily identified, and the most up-to-date data is easily found. Shop floor technicians are struggling to understand what tasks are new, and how changes will impact what they are doing from product to product, especially as products in ETO industries can have several different configurations or customizations.
Another challenge we often see is with aging, standalone software tools, each performing a specific task, but not connected with other tools used to support various domains in the product lifecycle. When manufacturers start to digitalize their manufacturing processes, end-to-end workflows that incorporate these standalone tools are problematic. Data needed to support the workflows is not easily captured, and manufacturers try to adapt with manual integrations, exporting from one tool and importing into another. Each of these steps presents a risk that data is errantly modified or lost.
Connected manufacturing data through a Digital Twin
When we look at the way many ETO manufacturers work today, we see that simply digitalizing work instructions using standalone work instructions software is not good enough. For example, industrial engineers or process planners create work instructions, adding visual aids like part drawings and sequence of assembly steps, to guide the technician on the shop floor. They capture these visuals and paste them into a document, but the content of that document is not connected to the design processes – it is in a silo. When changes are made to the design, there is no path to update the instructions. The instructions will need to be manually updated for every product or process change. In an age where speed and quality are keys to market success, you need more than simple digitalization of your work instructions. You need connected manufacturing information and processes realized through a Digital Twin of your product.
Work instructions software in digital manufacturing with Teamcenter Easy Plan
With Siemens Teamcenter Easy Plan, EWI is a function of a holistic digital manufacturing platform. Product and manufacturing data and processes are connected through a digital thread of information as part of a Digital Twin. This ensures a single source of product knowledge, eliminating the data silo issues mentioned above. For example, industrial and manufacturing engineers have access to the product BOM and related graphical data that can be pulled in when authoring work instructions. Work instructions are inherently linked to the design process, where changes are immediately populated and highlighted in the work instructions displayed on technician screens on the shop floor.
The reality is that EWI is simply another view of the process plan that is intended for the shop floor. The data is presented in a way that is meant for the technician – this is the task, these are the steps, this is what the parts look like, here is their orientation. No translation or import/export of data is required. If there is associated 3D geometry, it is accessible with a simple click. There is no need to navigate between systems.
Accommodating unique manufacturing environments
When work instructions authored in Teamcenter Easy Plan are created or updated, they are immediately available to the shop floor users – wherever the connected shop floor is located. I say connected, because this assumes the shop floor has a digital connection to the Siemens digital manufacturing backbone – Siemens Teamcenter. But what about environments where a connection is not feasible? For example, a floating shipyard or a desert-based water pump.
This type of environment is accommodated using an offline mode. The offline mode provides all electronic work instructions as of the last data sync for the technician to use remotely. Teamcenter Easy Plan allows the technician to collect any required inputs or measurement data while they are working offline, as well as signoffs, completion times by step, technician verification, catalog or lot numbers, etc. This is often required for future auditing purposes and is another benefit of EWI as part of a larger platform. When the technician is reconnected later, the data automatically syncs with Teamcenter online.
Some customers use EWI specifically to have the backup of offline mode. Any data that is ready for production is exported and placed in a specific location where it can be fetched automatically. Work is executed at any location, collecting required data.
Features of Teamcenter Easy Plan Electronic Work Instructions
Teamcenter Easy Plan electronic work instructions capabilities are feature-rich, with an award-winning user interface. The instructions can contain text, images, videos, and links to different documents such as machine operating manuals. Next and previous steps are available with a simple button click, allowing the technician to go back and forth in the sequence.
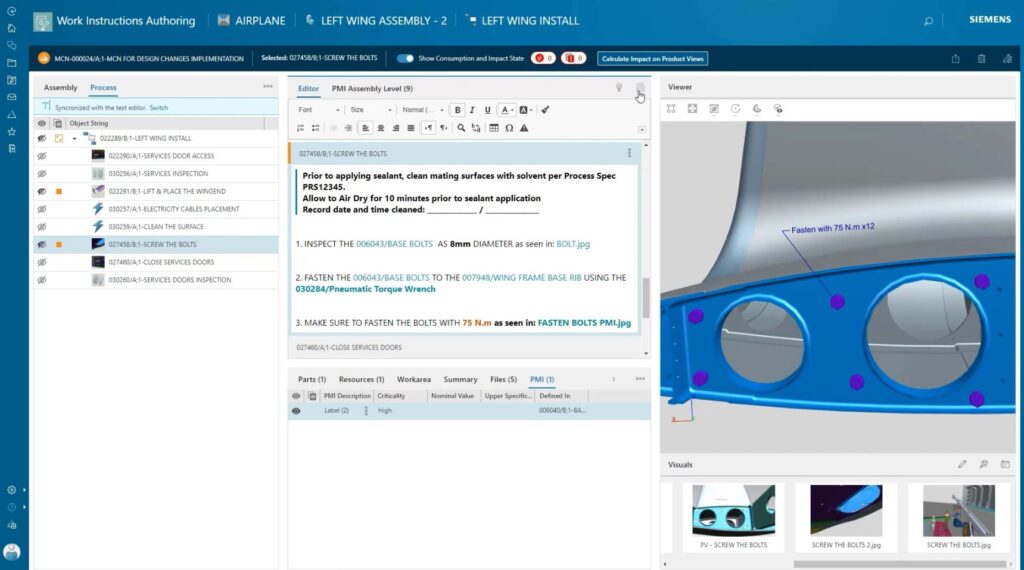
The layout of the instruction components is flexible, so it can be configured by the customer to display exactly what they want the technician to see at every step. While this makes the life of the technician easier, it also simplifies the process so they can quickly and correctly execute the task, saving time and improving quality.
As part of work instructions authoring in Teamcenter Easy Plan, the engineer can specify which tools are in view to shop floor users, and then open the instructions using the technician perspective to test that the technician view is working as expected.
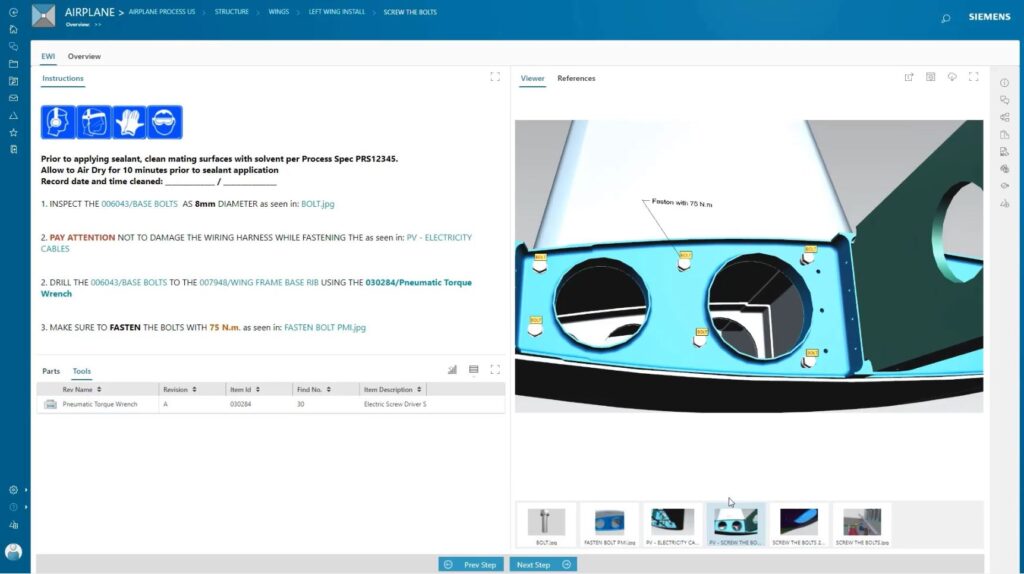
Foundational to digital transformation
Siemens solutions are unique because they originate from the engineering side of the value chain – as opposed to the shop floor or finance side. The engineering design is what must be produced in the physical world, and this connection from product design and manufacturing engineering to the shop floor is critical. Not only do we ensure that the correct instructions are always present at the production location, but any shop floor issues can be reported back to engineering inside the same system, capturing and storing contextualized data for future reference. The feedback loop is completed when the issue is resolved with an engineering change order, and instructions are seamlessly updated and made available to the shop floor users. We call this closed-loop manufacturing, and it is foundational to digital transformation.
Learn More About Teamcenter Easy Plan
Visit siemens.com/easyplan to learn more about task-based solutions for Manufacturing Process Planning
Try Easy Plan today, with a free-30 day software trial
See a demonstration of Manufacturing Process Planning with Easy Plan 6.0
About the author
Sivan Freud currently works for Siemens in product management for Teamcenter Manufacturing solutions. He has been with Siemens for over 20 years, working in various roles including product development, customer support, and business development.