Manage complex heavy equipment MBOMs with smart manufacturing solutions
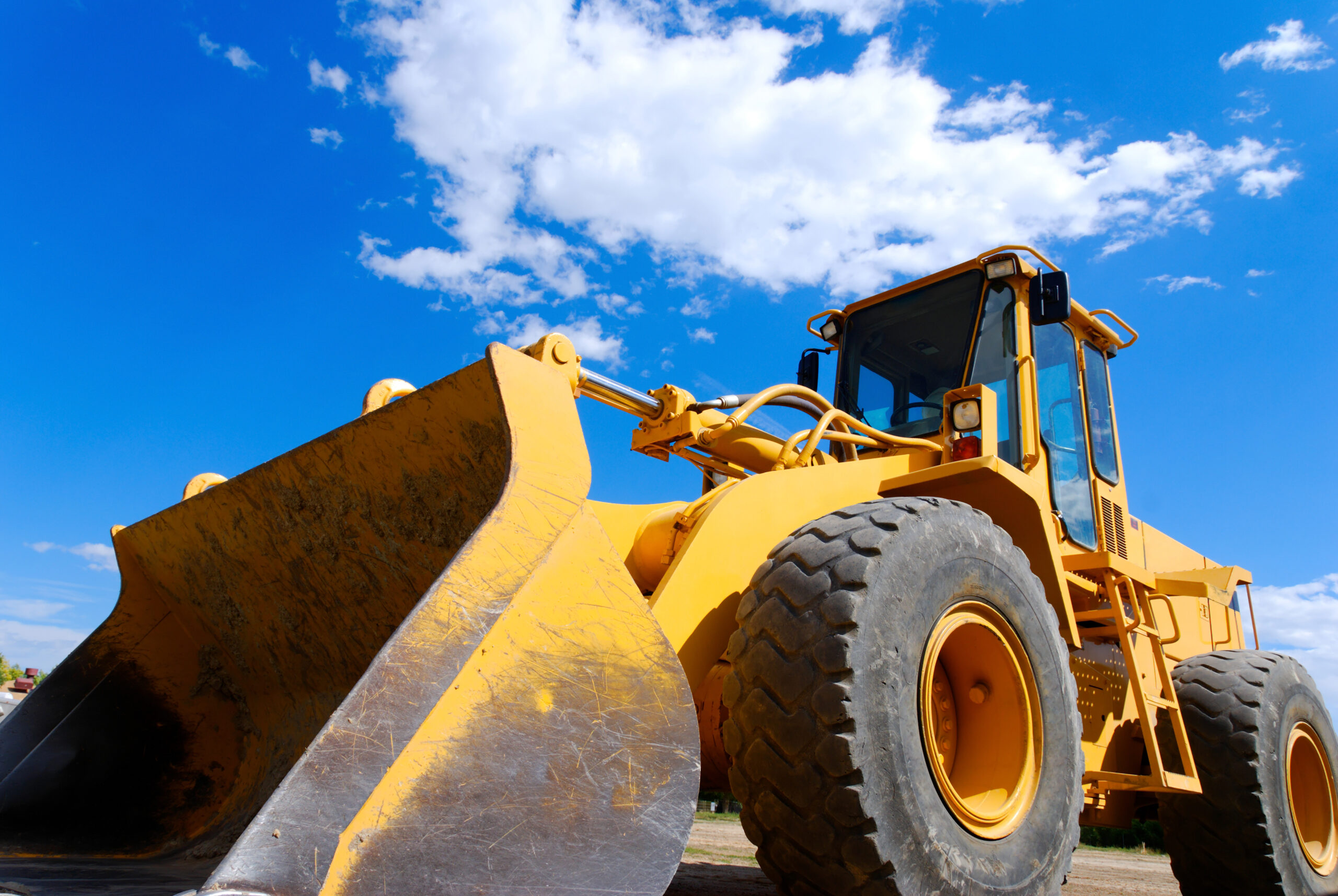
Heavy equipment manufacturers are under increased pressure to bring innovative, highly customized and lower-cost equipment to market much faster. New requirements around sustainability and the shift to electrification add further complexity to your manufacturing processes. A digitally connected enterprise of solutions that provides visibility early-on to manufacturing data and processes, and integrates stakeholders across domains can help address these challenging requirements.
Digital Threads Connecting Design to Manufacturing
The digital twin is at the heart of any smart manufacturing strategy used from design to new product introduction (NPI) to plan for, simulate, predict, and optimize the product’s build quality and the efficacy of the production system building it. Digital threads connect manufacturing data and processes to design engineering early-on in the product lifecycle to ensure quality manufacturing process planning. The process plans are then validated using simulation solutions. The digital threads provide a controlled and consistent data feed to stakeholders in different domains across the digital enterprise, from design to manufacturing to production operations.
Siemens digital manufacturing solutions enable you to collaboratively create, validate and optimize manufacturing information, such as the manufacturing bill-of-materials (MBOM) and bill-of-process (BOP), concurrently with product design. The solutions provide a common environment for collaborative manufacturing, where multiple disciplines share the same requirements and can easily author and navigate multiple views from a common structure and leverage automated tools to compare and validate information structures. This collaborative environment also provides consistent ways to deal with revisions and versioning and enables users to view and validate re-use of costly production assets across multiple programs.
Why Digital Manufacturing is Key to MBOM Value
You may have implemented some level of manufacturing BOM management that provides the orderable BOM within your ERP system. However, this MBOM, if manually replicated and based on the related engineering BOM, provides plenty of potential for human error. Even when automated transfers of data are implemented, they typically lack the necessary processes and accountability to ensure accuracy of the data. Another typical pitfall is relying on your engineering department to manage your MBOM definition based on the manufacturing and supply chain requirements. This can result in unnecessary design changes and costs that provide no added value to your products. In fact, this is likely creating new issues and delays due to the volume of change, increasing the chances for error. For example, in multi-plant scenarios, there can be significant non-value added changes created by engineering just to manage plant specific manufacturing assemblies required to support the material breakdown and flow of work orders.
Another approach is to allow manufacturing to manage a unique view of the MBOM directly within the ERP system. This approach creates a complete disconnect and lack of traceability to the engineering intent, introducing the possibility of significant quality or compliance escapes. This disconnect also limits collaboration between engineering and manufacturing which can prevent early manufacturing validation, which could help identify critical issues sooner. It can also drastically increase the time required to implement new products or changes due to the sequential, “throw it over the wall”, nature of this approach.
Integrated MBOMs with PLM
Implementing an integrated manufacturing BOM, within your PLM system, that is directly linked to the engineering definition provides a mechanism for manufacturing and engineering to collaborate much earlier in the product lifecycle. This linkage also provides enhanced reuse of existing information, beyond just part metadata. You can provide manufacturing earlier controlled access to design details such as 3D models and drawings, as well as access to associated requirements and specifications. This access can allow manufacturing to assess manufacturability and provide feedback to influence the designs while the cost of change is low. Additionally, this linkage can provide your design engineers a clearer understanding of the impact of potential changes and the ability to coordinate with relevant manufacturing stakeholders based on the related MBOMs.
Beyond just enabling earlier collaboration, managing the MBOM within your PLM system allows for formal change processes to be implemented to trigger adequate validations or signoffs that ensure the quality and accuracy of the data prior to releasing it for downstream use. A broader Manufacturing Change Notice (MCN) process could also be introduced to ensure all necessary supply chain stakeholders have been notified and acknowledge any potential impacts.
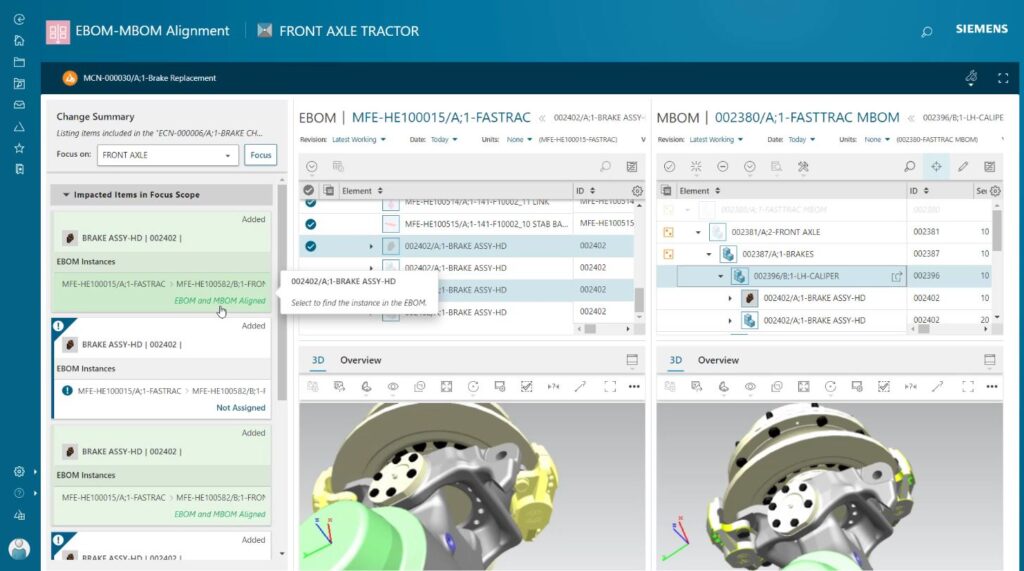
Heavy equipment buyers are demanding more options in your products. You need to be able to offer this variety without driving up costs. This becomes even more important when different products are being manufactured on the same line. As you offer more and more custom orders to the market, the number of parts in the equipment’s MBOM continually increases. Being able to visualize the different configurations during the planning phase is critical. Using a PLM system with configuration capabilities makes it possible to manage, visualize, and validate all of your potential customer order configurations.
Market globalization is another factor making it more difficult to meet your manufacturing KPIs. The “design anywhere, build anywhere” concept is rapidly becoming the norm, resulting in the need to build the same equipment in multiple locations around the world. Global design with local manufacturing means increased communication challenges and plant-to-plant variation in the equipment build. The capability to create an MBOM for each plant based on the equipment design and the advised fabrication and supply strategy (make/buy) makes it easier to adapt your equipment to local markets.
As you look to improve your manufacturing efficiency and address new challenges it is critical to ensure that you have a common understanding of your products’ part requirements across your organization. Without this basic foundational data and an ability to ensure the traceability and accuracy of your MBOM data you have the potential for delays, compliance risks, and quality misses. By introducing an integrated manufacturing BOM as part of a broader digital manufacturing strategy you can provide significant benefits to your organization. As highlighted in the video below, digital MBOM connected with PLM can help you:
- Avoid costly changes with early identification of issues across the supply chain through improved collaboration between manufacturing and engineering
- Improve accountability through clear visibility of BOM impacts ensuring inclusion and sign-off from required stakeholders
- Improve customer satisfaction with improved quality and compliance through direct linkage and validation of engineering intent
- Reduce inventory costs through clear visibility to latest part requirements minimizing inventory holds and reducing scrap of obsolete parts.
- Avoid rework with accurate and consistent transfers of MBOM data to downstream systems (e.g. ERP, MES) ensuring the quality of BOM data across your supply chain
In an environment of increased pressure to get innovative and highly customized heavy equipment to market faster, leveraging digital solutions that connect the dots between design, manufacturing, and execution will help you get ahead of your competition.
It all begins with a digital twin for smart manufacturing, enabling accurate manufacturing information threaded into downstream systems. For better heavy equipment manufacturing today, and tomorrow.
Learn more about Siemens solutions for heavy equipment
Visit siemens.com/easyplan to learn more about task-based solutions for Manufacturing Process Planning
Try Teamcenter Easy Plan today, with a free-30 day software trial