Using a digital twin to validate advanced mechatronic motion control systems
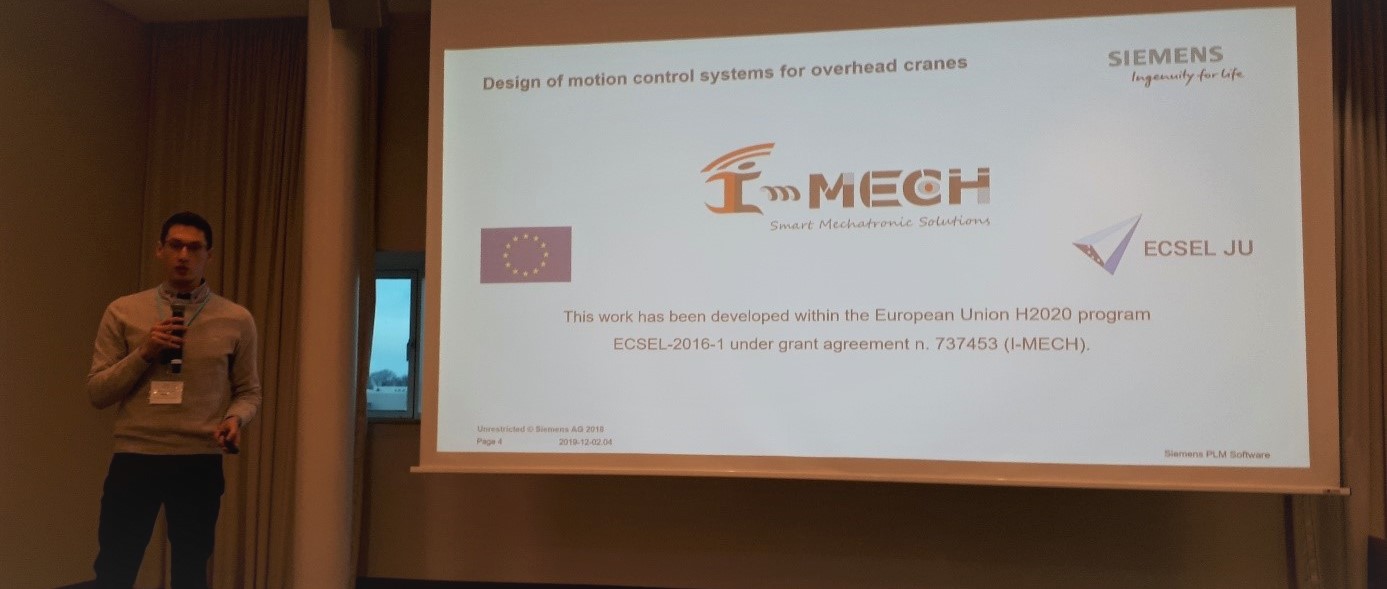
I-MECH, bridging the gap between the latest research results and the best industrial practice
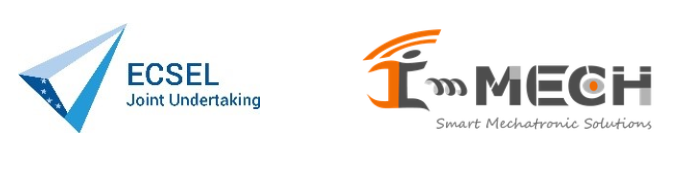
In the video below, we see two types of overhead crane behaviors:
- First case: the crane is moving
- Second one: the movement is much more stabilized.
What is the major difference between these two cases? The answer is the activation of the anti-sway control system.
During the Simcenter Conference held in December 2019, I met Dr. Luca Simoni from the University of Brescia (UNIBS), who introduced me to his work on the development of such control systems. These controllers are extensively applicable in a large community of industries, where safe, productive and cost-effective machines are highly demanded.
Dr. Simoni has been part of I-MECH, which is an ESCEL project launched in May 2017 and composed of 31 academic and industrial partners, including UNIBS as well as Siemens Digital Industry Software. The main goal of the I-MECH project is to transfer knowledge from universities to companies in terms of mechatronics systems control and bridge the gap between the latest research results and the best industrial practices. Software and hardware building blocks, featuring standardized interfaces, are developed to deliver a complete suite of the I-MECH reference motion control platform. Dr. Simoni has been working on the development of several building blocks. We interviewed him to shed light on project achievements.
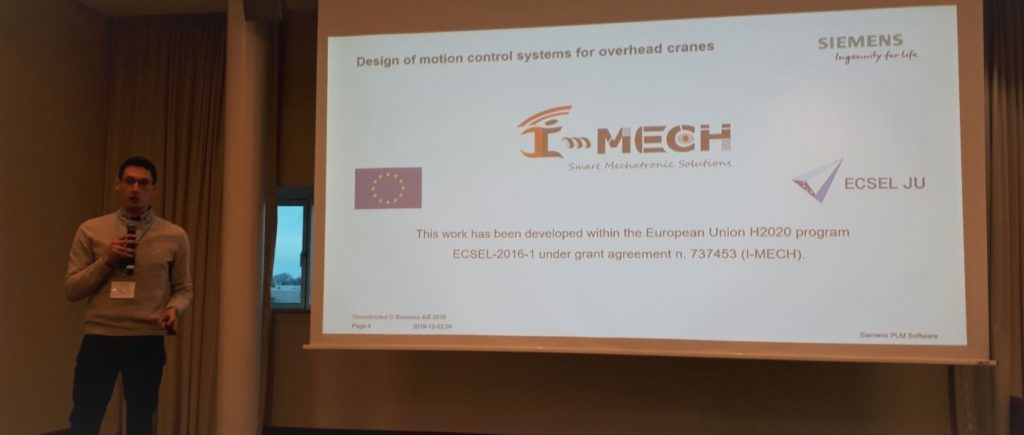
Simcenter: What’s interesting today is that the requirements to build machines are more and more complex. Could you tell us more about the overall context in which the I-MECH project is evolving and the way you proceed to address those industry needs?
Luca Simoni (L.S.): The increasing demands on size, motion speed, precision, adaptability, self-diagnostics, connectivity, new cognitive features, etc., make the development of new mechatronic systems for machine building more complex in terms of both hardware and software development. This is the reason why the I-MECH project aims at building up ready-to-use hardware and software – what we call “building blocks (BBs)” –, which eventually helps in the design and control of machines in order to obtain better results in terms of machine productivity, efficiency, etc.
The methodology we follow is via the development of 11 BBs, each of which is closely related to different types of control applications. In this context, the I-MECH BBs are related to smart sensors, predictive maintenance, high-speed vision, servo amplifiers, identification and modeling, automatic tuning, vibration control, and iterative learning control. Each of these blocks will be released in the I-MECH portal to be used in the model-driven development of the machine. A separate work package was designated to introduce a framework to enable the virtual commissioning of the design to the maximum.
In a few words, we bring in a solution to the industry by giving them access to the I-MECH platform in order to improve their machine efficiency. Indeed, we develop these controllers to be as generic as possible for any type of industry usage. For example, the BB6 that is related to automatic tuning of velocity and position control loops can be used in different types of machines, which is required to be generic. Obviously, the user can customize the block, by modifying the input parameters, to be specific in some cases.
Simcenter: It is pretty clear that you bring a ready-to-use solution to the industry. What do you think will be the added-value for them, should they use the I-MECH final platform?
L.S.: We hope that industrial practitioners will use the I-MECH building blocks (BB), because they can provide them with new and innovative solutions that are not always available in the industrial field. Also, we aim at reaching motion control-relevant SMEs, because they usually lack a dedicated R&D department, nonetheless, they still need to remain competitive and bring efficient machines to the market. Basically, they can use the building blocks to find the expertise they need by using the I-MECH portal. Thus, they can work independently but are reassured with the backup of the I-MECH center service desk. This approach is particularly compatible for so-called ‘green field’ projects. Some consortium partners, however, apply BB methods as part of their existing hardware topology (‘brown field’ application). One great example is that our project partners Gefran and Philips Healthcare are already using the building blocks I am developing.
Simcenter: Could you give us more insight about the building block you are developing for that project?
L.S.: I do focus on multiple building blocks: BB6 “auto-tuning and self-commissioning”, BB7 “vibration control” and BB9 “iterative and repetitive control”.
The BB6 basically applies a series of pre-calibrated tests to the system to estimate the behavior of the physical system and the effort to move it. This ends up with a new set of optimal parameters for the controllers inserted in the position and velocity control loops.
The BB7 focuses on vibration in mechanical systems. This covers the case of under-damped systems like the overhead crane, but also mechanical systems suffering from structural vibration due to very fast motion like a robotic arm. In the second case, the vibration perturbs the position at the end of the arm. The strategy involves adding acceleration sensors at the end of the arm to anticipate and eliminate perturbations.
The BB9 applies optimization techniques to systems following a repetitive cycle. During the first cycles (5, 10, …), the controller examines the system response and tunes its own control settings to reduce perturbations. This results in a more efficient control strategy for a specific working cycle.
Simcenter: In order to validate your controller early in the development cycle, you decided to use simulation. What has been the strategy and benefits of that methodology?
L.S.: Siemens Digital Industry Software is a partner in the I-MECH project and the team developing the system simulation software solution Simcenter Amesim provided me with the simulation models representing some mechanical systems. For example, I have been provided with the complete overhead crane system simulation, as well as a generic scheme for the self-commissioning from which I tried to apply my techniques on the system model. This enabled me to do a model-in-the-loop test of the controller I was developing.
Now, it is mandatory to use system simulation in product design and development for several reasons. First, we can damage our actual machine by trying to control it for the first time, for example, we can create a controller that is not stable for the machine and thus break the machine. Second, it enables to speed up the process of machine development. Using the digital twin of the machine dynamics can facilitate the faster development of the controller even before the machine is completely built.
The use of system simulation is also of interest for much bigger and complex industrial projects, since Simcenter Amesim enables to simulate multiphysics systems. So even for complex machine development and control, the usage of system simulation at the early stages of the development cycle will be more and more common in the future – which of course enables us to save time in the development process and propose a mature design, before building the machine itself.
Simcenter: What are the first achievements, aside from the development of the building blocks, you can already share with us?
L.S.: The results achieved are really promising; we show that the residual oscillation can be significantly reduced with both open-loop and closed-loop control techniques. The results obtained at the simulation stage have been an essential step before the application of the method in a real industrial crane provided by our partners from Gefran (Italy). Testing the methodologies in simulation mode has been very important, as an overhead crane is a dangerous system and, therefore, we had to be sure of the effectiveness of the control strategies before their implementation in a real system.
The I-Mech project is now at its final phase. Currently, UNIBS jointly with the I-MECH industrial partners are implementing the BBs into the I-MECH demonstrator and pilots.
The pilots of the I-MECH project are:
- A generic substrate carrier (GSC) for digital printing for graphics and/or functional electronics (Sioux CCM, Pilot 1),
- A wafer stage with high precision stepping performance (Nexperia, Pilot 2),
- An in-line filling & stoppering machine (IMA, Pilot 3),
- A smart machining tool for a high precision CNC milling machine (Correa, Pilot 4),
- An X-ray intervention medical manipulator (Philips, Pilot 5).
For UNIBS two implementation paths are envisioned:
- GEFRAN implements the BB7 in their real crane control (for anti-sway purpose)
- Philips Healthcare implements the BB6 in their medical manipulator (for self-commissioning, meaning the automatic calibration of the controller parameters for the control of velocity or position of a machine)
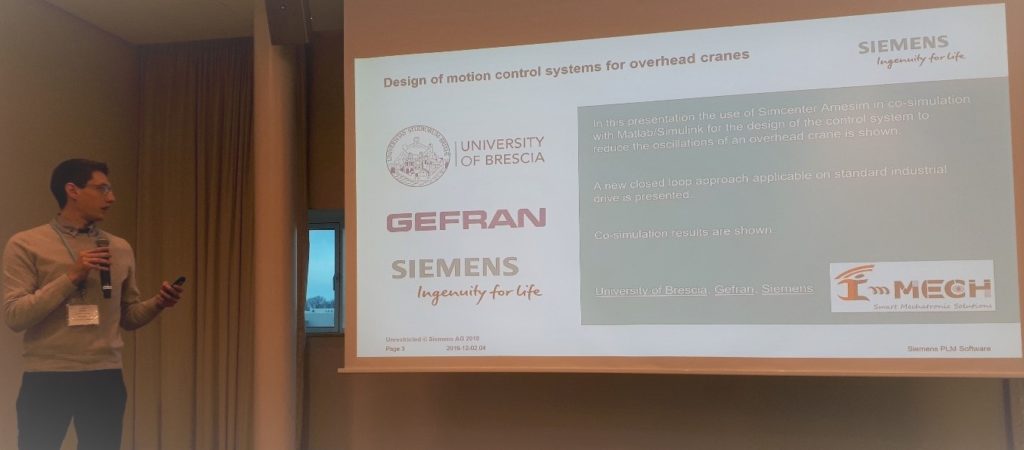
About Dr. Luca Simoni: Dr. Luca Simoni has graduated from the UNIBS, from which he was awarded with his PhD degree. From 2014 to 2017 he worked on two research fields: the first field was related to robotics and the development of friction models that consider the temperature inside the joints of the robots; the second topic was related to mechatronics system modeling and control. During his master studies in the UNIBS, Dr. Simoni was familiarizes with simulation environments and “digital control”, with the aim being to learn how to discretize a system and write different equations that rule the system. Dr. Simoni stresses out that nowadays it is mandatory to learn about simulation during university studies. When joining a company, a newly graduated employee has to present preliminary simulation results to an industrial problem and decide whether the technologies that are being developed are operational or not. Mastering simulation is the key to evolve in such a context. In addition to this, getting familiar with software used by the industry is particularly important, since it facilitates the integration process of employees newly graduated from the university to the company.
Reference: Comparison of Linear and Nonlinear MPC on Operator-In-the-Loop Overhead Cranes Marco Giacomelli1, Davide Colombo2, Marco Faroni1, Olivier Schmidt3, Luca Simoni1 and Antonio Visioli1 (1 Dipartimento di Ingegneria Meccanica e Industriale, Universita` degli Studi di Brescia, Italy , 2 Gefran S.p.A., Gerenzano (VA), 3 Siemens Industry Software SAS, Lyon, France)