Top 4 Challenges to Railway CAE and How to Solve Them
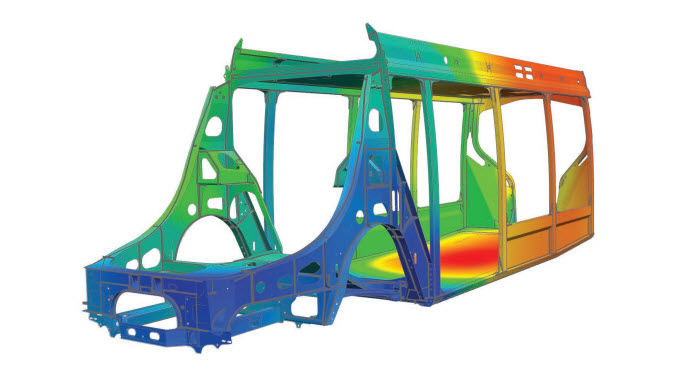
If you are a CAE expert for the railway industry, chances are the challenges we will cover today are ones you and your team face every day. What if you could make the most difficult parts of your job a little easier? Or perhaps eliminate them all together? Far from just being able to accomplish more, you could reap the benefits of some major life changes such as increased happiness, decreased stress, all of which lead to a healthier lifestyle. So if you want to live longer, read on.
It’s a bit of a dramatization, but studies do show that less stress and more sleep lead to a longer life and increased immunity. You could use the time you save from these tips to take a nap or do some relaxing yoga to reap those health benefits. Anyway, let’s get down to the challenges and how you can solve them.
Before we do that though, we should understand what developments in the rail industry have led to the current way of doing things. In other words, what is the cause behind the challenges you face now?
Like any industry, rail transport has evolved greatly since its early days. The first trains date back as far as the ancient Greeks if you count man or horse powered carts on wooden or stone tracks. Since then, people have developed steam locomotives, electric and diesel-powered engines, and finally the high-speed rail of present day. This evolution has impacted the way in which trains are designed, manufactured, and tested.
Today you can solve many issues related to requirements verification with the help of finite element analysis or FEA. Take Validation of Crashworthiness for example. The chapter dedicated to this specific aspect of requirements verification states, “It is impractical to evaluate complete train behavior by testing [physical prototypes]. Numerical simulation alone is sufficient for accurate prediction of structural behavior.” Why? Well, consider the unwieldiness of a train. Such a large, heavy piece of machinery is costly to produce; it takes time and money, and a lot of it! Physical testing requires not just one prototype, but many, so take that cost and multiply it. You can easily see how physical prototypes become not just impractical but nearly infeasible.
What does this mean for the rail industry? Well, a few things. Reliance on physical prototypes has waned, shifting instead to an increased reliance on simulation. This, in turn, has led to a greater variety of simulations, increased complexity, and more data to manage and store. And that is where the challenges come in.
So, without further ado, here are the 4 most common challenges you face when performing railway simulation and how you can solve them with Simcenter 3D.
1. Preparing geometry takes 70-80% of your time.
Geometry preparation is a major pain point for all CAE analysts, but the complex, thin-walled structures common to the railway industry only exacerbate the problem. The more complex the model, the more time you must spend to resolve inaccuracies and defeature extraneous geometry. You can read extensively about the pains of preparing geometry for analysis in a past blog post, Overcome the Barrier to Faster CAE Geometry Preparation. Most people accept this as the cost of doing simulation, but the fact is you can reduce the amount of time you spend on geometry preparation by hours or even days in some cases.
The solution: An integrated modeling and simulation system that combines CAD and CAE for a seamless experience. Simcenter 3D empowers you to prepare geometry for analysis in minutes using Synchronous Technology. The integration helps with complex, thin-walled structures and simplifies geometry preparation. LOHR Industrie, for example, cut their geometry preparation time by 60%.
2. Large models and systems are difficult to understand in their entirety.
With traditional CAE tools, you must manually build monolithic finite element models for the entire CAD assembly. That is difficult and time-consuming, not to mention expensive to manage in the context of the system and available resources. Another drawback is that you must repeat geometry simplifications and meshing preparations for all components. So you are now doing the same painstaking work over and over. The other option you have is to copy the FEM, but then you lose the link between the FEM and geometry.
The solution: System-level modeling and simulation with Simcenter 3D gives you the ability to efficiently build and manage FE assemblies through a unique, multi-level approach that allows for multiple instances of the same FE component. Simcenter 3D instances and connects FE component models together, which enables you to distribute modeling work and build up the assembly faster when the component models undergo changes.
3. Multiple CAE tools slow you down and complicate things.
A lot of companies opt to use multiple CAE solutions each specialized for a particular type of simulation. The reasoning behind their decisions is multifaceted and complex, so we’ll save the “why” for another post. Suffice it to say, multiple CAE solutions end up costing you time and energy. Most obvious is the learning curve you face with different tools. Every interface is different; commands may be in other places or even have different names from what you’re used to. It takes time to master each software solution you use. Then when you need to perform multiphysics simulation—which is increasingly often given that the real world contains several types of physics acting on objects at once—you are forced to transfer data into different formats since not all CAE tools use the same one. This doesn’t just take more time and effort on your part, it’s also stressful!
The solution: A true multidiscipline tool such as Simcenter 3D eliminates the need for many single discipline tools and reduces data transfer. With NX, you can perform structural, thermal, flow, motion and other types of analyses using the same interface, analysis and geometry modeling capabilities, and file structure and management scheme. Say you run a motion analysis, for example. Your outputs can be directly applied as inputs to a structural analysis run (such as loads for stress calculation), without the need for error-prone external data transfers to link them together. Coupled-physics analyses are streamlined as a result of this integrated environment.
4. An increased quantity of CAE data is difficult to capture, manage, and store.
Simulation data management has always posed a challenge, but it becomes increasingly difficult as the amount of CAE data increases. With larger, more complex models becoming the norm, this is a trend we can expect to stick around for a while. When you lack sufficient software to manage your simulation data, you are forced to search for the data you need. This wastes a lot of time. Additionally, you struggle to communicate CAE insights to your other team members. This leads to lost opportunities for improvement. You also aren’t able to capture and share your best practices, so the CAE team is disjointed and not performing as well as it could.
The solution: Seamless integration with a simulation data management system, such as Teamcenter and Simcenter 3D, allows you to standardize analysis methods across your team. This results in less errors and increased efficiency because everyone uses the same best methods. You are able to build models faster and with improved accuracy, because you can now quickly locate the data you need. It’s even easy to share insights you gain from the analysis with other product development teams. After all, the whole point of CAE is to understand and improve product performance, right?
You can learn more about the challenges and solutions discussed in this article when you watch the on-demand webinar Efficient Railway Industry Innovations with Simcenter 3D