System Simulation in the Context of MBSE
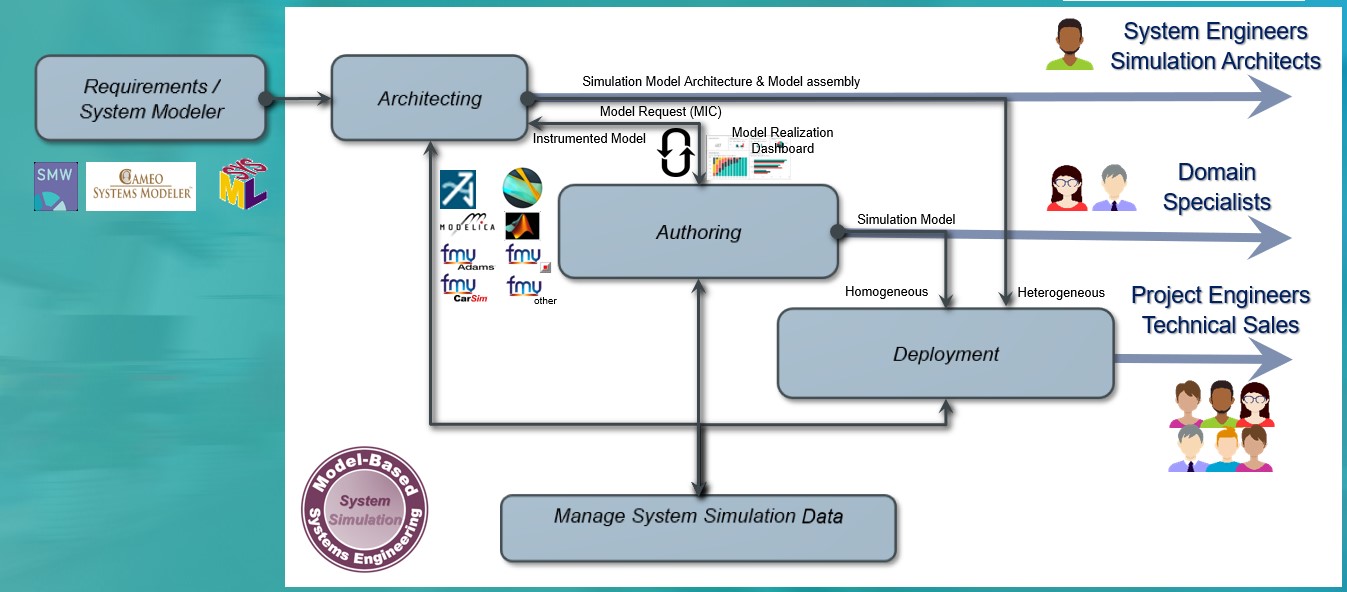
Why is System Simulation an essential asset in support of Model Based Systems Engineering?
In all business discussions we have with our customers and partners, we clearly observe that the race to innovation across industries leads to constantly redefining how companies are working. Let us put ourselves in the shoes of some of our industry users for a moment: do we have an idea about the complexity of designing autonomous vehicles (mechanical and controls) with so many parameters to be calibrated, so many mission-critical profiles to be verified? And what about Urban Air Mobility trying to reinvent the way we will travel in the future but also implies coping with stringent regulations and relying on even more efficient validation processes? Are we able to quantify the number of safety & reliability requirements that come with the design of new generations of hybrid propulsion aircraft, nuclear plants, space rockets that need to be checked in an extremely rigorous and timely manner? Can new technologies like Artificial Intelligence push innovation to extreme boundaries and lead to revolutionary designs unexplored until now?
Siemens Digital Industries Software relies heavily on its Xcelerator portfolio and the expertise of its teams to support industries going through these major changes with unique solutions. In what follows, we will update you on the System Simulation Factory vision and strategy, how this vision helps solve issues related to current industry trends as mentioned in the introduction and why it is such an important element to optimize the system performance across its requirements and performance attributes, and how it further enables the best validation and verification process of our customers.
THE SIMULATION FACTORY
But first, let me recall the 4 main pillars of our System Simulation Solutions and explain their complementary contribution within the Simulation Factory. My mission is that anybody reading this post can clearly view the issues we can solve. Our Simulation factory comprises interoperable architecting, authoring, deployment, and model and data management solutions that can integrate with any enterprise digital thread to support Model-Based Systems Engineering processes. The journey basically always starts with a set of product requirements coming from marketing teams and customers, related to certification procedures, linked to the numerous variants in which this product has to be delivered … these requirements are generally stored within the PLM environment. They need to be validated and verified throughout the design cycle process.
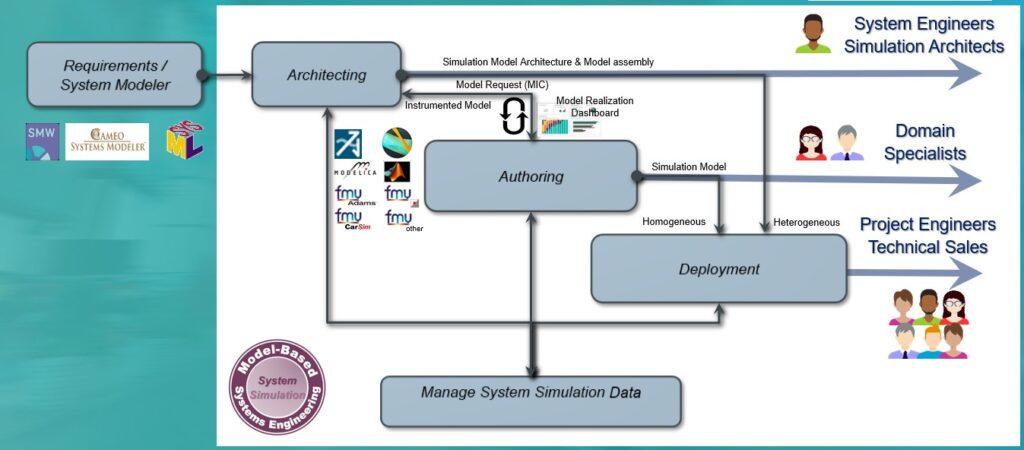
ARCHITECTING
The Simulation factory will help translate these requirements into simulation architectures, directly importing Systems Modeler architectures or using AI-based generative engineering technology to explore all possible simulation architectures which could verify the requirements and associated validation criteria. Let us take the example of the thermal management of an EV and an associated requirement corresponding to the temperature range in which the battery needs to operate.
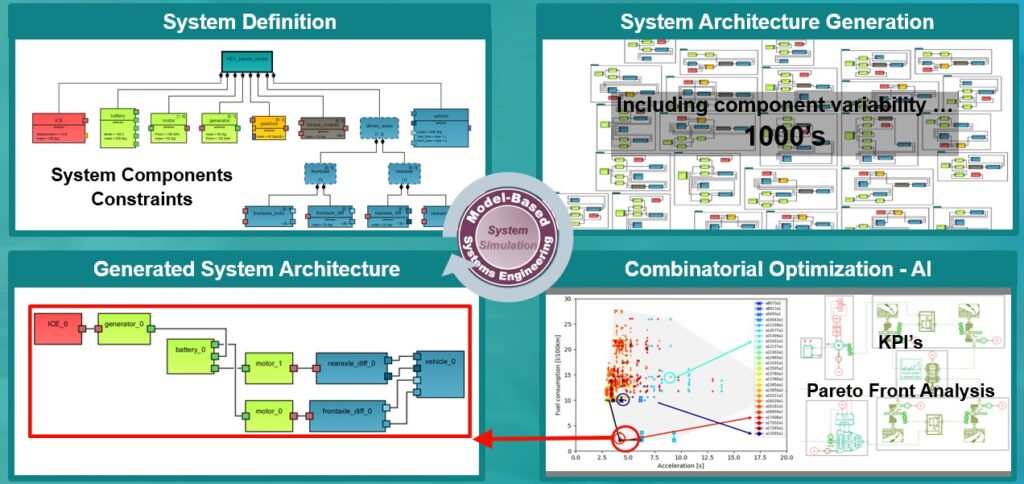
We know OEMs and suppliers are still investing a lot in R&D to define the best thermal management strategy and thermal management system architecture. With our AI-based architecting solution, we can support the generation of all thermal management systems architectures based on the components composing the architecture (pumps, compressors, heat exchangers, thermal expansion valves, thermostat, pipes …) connected to the control and extract from the thousands of architectures that will be generated (by evaluating all possible connections combinations between all components), the ones that are compliant with the requirement to be validated. In some cases, this generative engineering technology can develop unanticipated innovative architectures, making it so unique on the market.
Once the most promising thermal management simulation architecture has been detected, it is completed with interface contracts to really organize the process of creating the physical detailed models of the different components of the architecture and connect them seamlessly. This is also a way to define connecting rule processes to have departments from the same company exchange models and integrate them together. You can also imagine it streamlines the process of integrating supplier models into an OEM integration model. The simulation architecture needs to also be “agnostic” to integrate component models coming from different SW authoring tools, possibly under the form of FMUs, and co-simulate the different architecture compounds. This is, in a nutshell, what we offer as an architecting solution.
AUTHORING
Once the simulation architecture is finalized, the interface contracts known, and the requirements to be checked traced under the form of a Model Identity Card, we can launch the model request phase: this consists of creating the mechatronics models that are going to be consumed by the architecture to deliver the simulation results required to check that the battery indeed operates in the appropriate temperature range. We propose leading authoring solutions, multi-physics based, which will support the process of creating the 0D/1D models of any physical system (mechanical, thermal-fluids, electrical, controls). Most of the time, the authoring platform is being used by Simulation experts who will deliver the proper model at the different stages of the design cycle, relying on a unique feature of our offer, which we name modeling scalability (as illustrated in the next image).
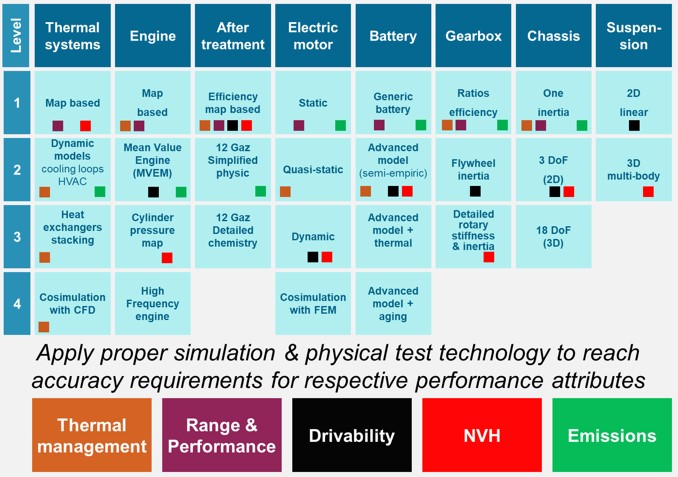
Authoring solutions can be used at early design and detailed design stages for Model-In-the-Loop (MIL) characterization as well as in the calibration and controls strategy validation process up to the creation of the executable digital twin (Software-In-the-Loop (SIL) and Hardware-In-The-Loop (HIL)). For the latter, it might be needed to rely on powerful Reduced Order Models (ROM) tools to do so, and these are also part of the Simulation Factory. Also, many additional analysis tools are delivered together with the authoring solutions to support the simulation expert in efficiently delivering and validating steady-state and dynamic models (CAD import, parameterization Apps, DOE, Linear Analysis tools, Embedded CFD, flow balancing features …)
DEPLOYMENT
Once the simulation architecture is combined with the authoring models composing it, there needs to be a way to very quickly consume these combinations in an easy-to-use environment to generate variants, scenarios, or mission profiles, create customized pre and post-processing.
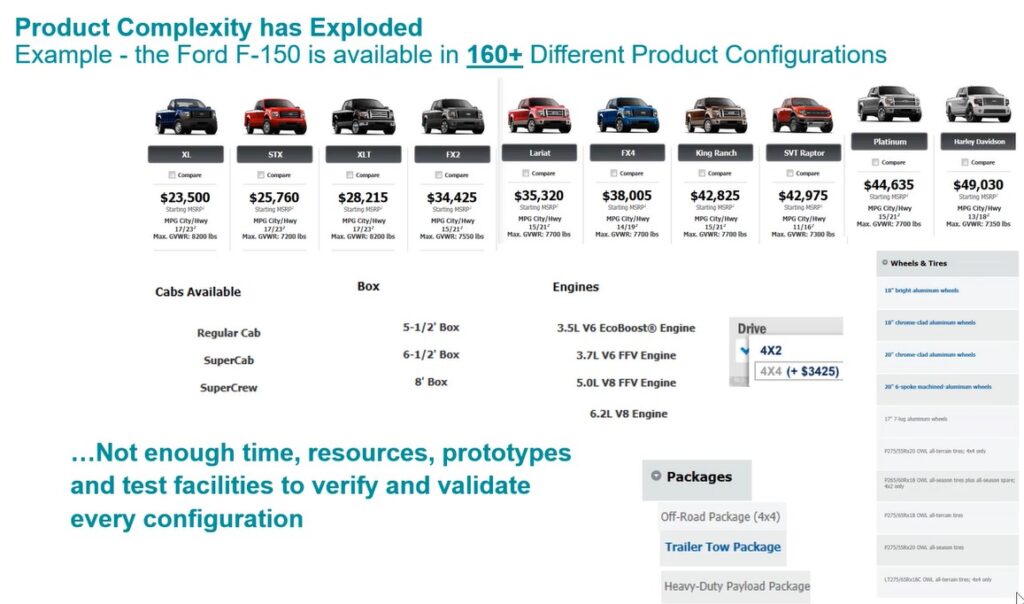
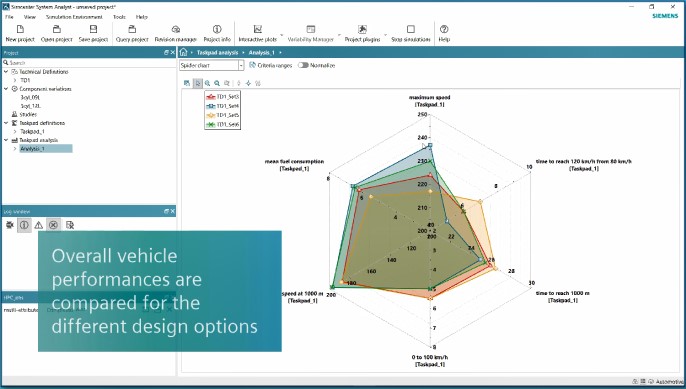
This stage will be the one in which the real ROI of the previous mandatory stages is extracted: here indeed, the prepared architectures and models are delivered so that many non-expert users can easily perform massive numbers of analyses and validate and verify the requirements for each variant and mission profile of the product to be designed. No need to be a simulation expert to execute this part of the work. The deployment solution provides companies with a way to democratize simulation tasks and has many more stakeholders supporting the validation, verification, and configuration of the final product. It goes without saying that this process is supported by powerful design optimization and HPC and Cloud computing capabilities.
MODEL AND DATA MANAGEMENT
In the process of creating architectures, models, and deployment projects, it is finally mandatory to have a model and data management infrastructure supporting the full process and in which data, architecture, and models can be organized, versioned, shared, and capitalized to ensure traceability and digital continuity, including Work-In-Progress and Enterprise model and data management layers. This is the final important and transverse key pillar of our simulation factory.
Presentation from Realize LIVE 2021
Learn more by watching this presentation on how System Simulation Solutions enable verification and validation process in the context of MBSE.
Learn more
Discover the Simcenter system simulation portfolio and the latest features of our product in this video.