Simcenter STAR-CCM+ 2019.2: Faster In-Cylinder Simulations
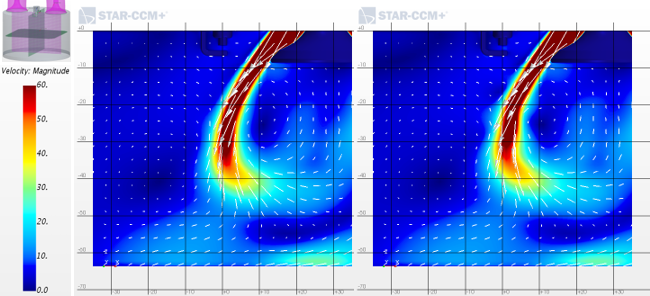
As a CFD simulation engineer you will routinely have to answer technical questions, however, there are a couple of questions that are asked even more frequently: “How long will it take to perform the simulations?” and “Can you quickly do a couple of more parameter or design variations?” are at the top of the list, with the former one being posed in the project planning phase, and the latter one appearing when discussing the outcome of the simulation campaign. Wouldn’t you like to answer: “Less than half the time than in the last project” and “Yes!” the next time that someone asks these questions of you? If you are an in-cylinder CFD simulation engineer, you will be able to do that once you start using Simcenter STAR-CCM+ 2019.2, where we have made it possible to run in-cylinder simulations more than twice as fast as before while maintaining solution accuracy.
Figure 1. Speed-up factor for in-cylinder simulations.
Figure 1 shows the speed-up factor for a set of industrial in-cylinder test cases. How is it possible to make in-cylinder simulations run that much faster, I here you ask? For those of you not familiar with in-cylinder CFD simulations, let me first say a few words about the challenges of performing such simulations. Over the whole engine cycle, the flow pattern is complex with vast differences in flow velocity and turbulence levels. We need to consider piston and valve motion and complex physical processes such as fuel injection, evaporation, fuel-air mixing and heat transfer to name a few. Those processes are occurring in different spatial locations and they all proceed at different time-scales. In order to resolve them accurately, we need to use short time-steps since the time-step size is limited by the time-scale of the fastest process.
What can be done to make these complex, transient simulations run faster without any loss of accuracy? Since we cannot simply take larger time-steps, let us have the time-step size restriction work in our favor, solving the flow equations using an algorithm that provides good performance when advancing the solution with short time-steps. With the Simcenter STAR-CCM+ 2019.2 release we are introducing the use of the PISO algorithm for in-cylinder simulations. The PISO algorithm delivers significantly better computational performance than the SIMPLE algorithm when the time-step size is small.
Figure 2. Pressure (left) and turbulent kinetic energy (right) obtained for a GDI charge motion case using SIMPLE and PISO algorithms.
But what about solution accuracy? In Figure 2, the evolution of pressure and turbulent kinetic energy over crank angle is shown for a gasoline direct injection charge motion case and there is no discernible difference in the results obtained with the different algorithms – only the run-time differs. This case ran three times faster with the PISO algorithm!
Figure 3. Velocity field from simulations using SIMPLE (left) and PISO (right) algorithms.
Investigating flow-field details, Figure 3 shows the velocity field from PIV measurements from an optical engine and from simulations using the SIMPLE and with PISO algorithms. As for the cylinder averaged results discussed earlier, the choice of algorithm is not affecting the prediction of the velocity field.
So the next time you are running an in-cylinder simulation study or an optimization campaign, using Simcenter STAR-CCM+ 2019.2 you will be able to provide results more than twice as fast as before. Moreover, if you are performing other transient simulations requiring a small time-step size, you are free to use the PISO algorithm and take advantage of the computational performance it provides. Don’t forget that you can use our built-in Design Manager to quickly and easily perform design exploration, and you will now be able to explore more designs, faster!
Download Simcenter STAR-CCM+ 2019.2 when released later this month.