Tackle robotics engineering challenges efficiently
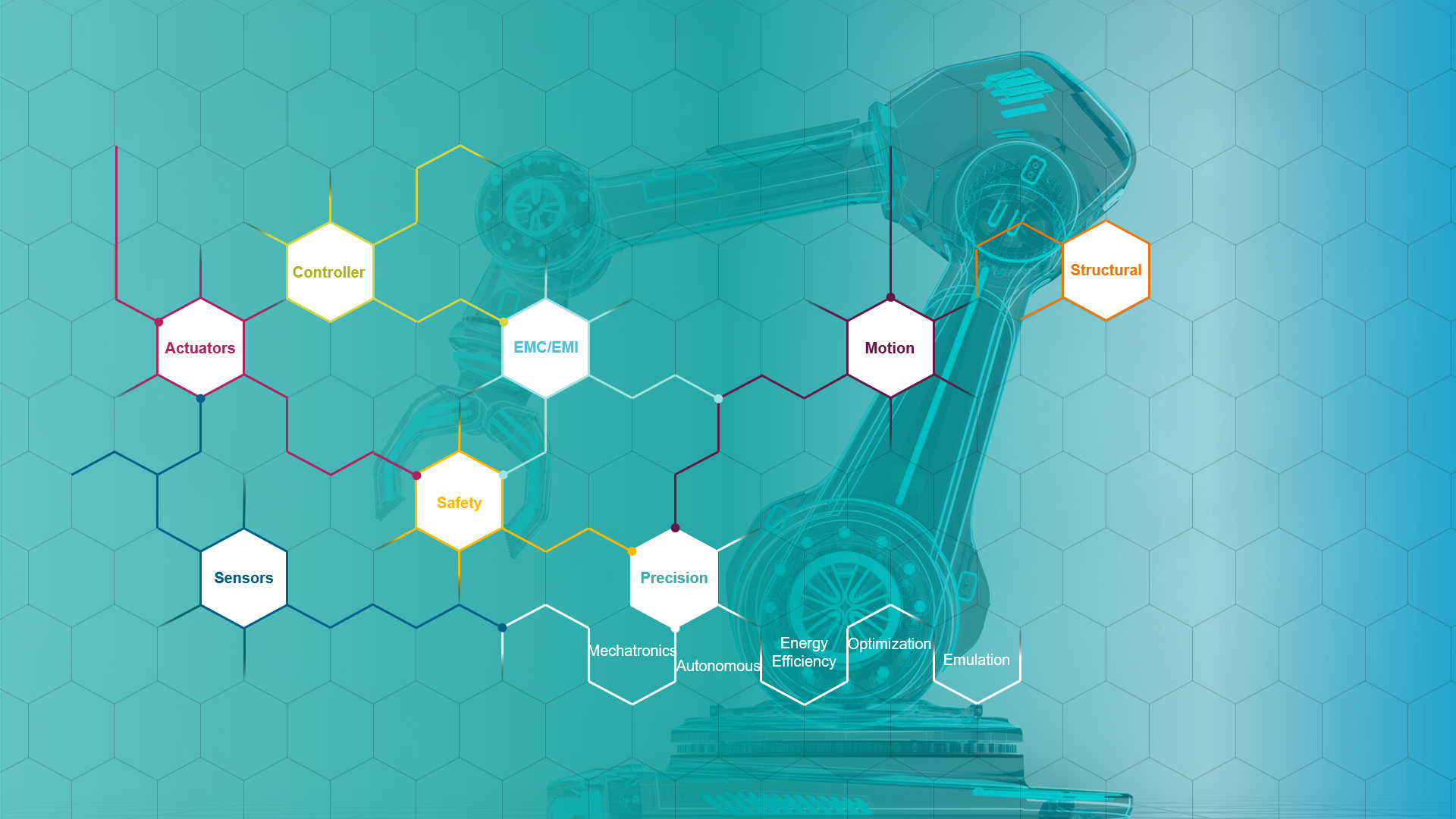
Believe it or not. The robotics industry is taking the manufacturing economies by storm. All labor statistics indicate that our co-workers, drivers, personal assistance will be a sophisticated robot soon!
Do you know annually 500000 manufacturing jobs are going unfilled, weekly 70,000 baby boomers are retiring from the workforce and millennials, the future generation, are not so excited to join the manufacturing trade? Consequently, it is no wonder automation technologies, including robotics are growing at a breakneck speed.
With the arrival of technologies — 5G, edge computing, machine learning, artificial intelligence and advancement in vision technologies, the robotics industry is at the sweet spot to deliver on Industry 4.0 promises. But, creating robots that are autonomous, flexible to handle small batches of work at very high precision without compromising on safety is challenging.
Both established robotics OEMs and start-ups companies face difficulty when it comes to balancing performance — reliability, accuracy, safety and energy efficiency.
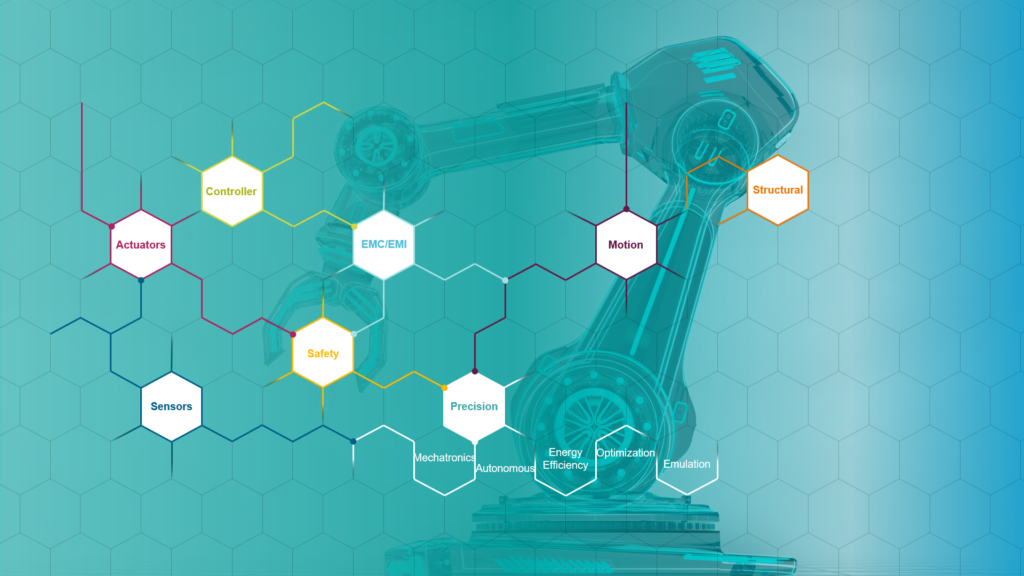
However, there are ways to prepare and handle complex robotics engineering challenges. In this blog, using a delta picker robot as an example, you will learn how Simcenter Amesim helps to address some major electronics challenges (sizing, safety, integration) effectively.
If you are more interested in tackling robots’ mechanical engineering challenges (kinematics, dynamics…), then there is an exclusive blog dedicated to that subject.
Simcenter Amesim for robotics engineering
Pre-sizing of actuators and components
Robots rely on actuators (DC motors, servo motors, stepper etc.) to perform real-world motion and manipulation tasks. Naturally, the components selected must meet the operating requirements and design constraints of the robots.
Currently, robot designers rely on a trial and error approach when it comes to sizing the actuator. For example, the component sizing is iteratively improved to meet performance requirements while advancing through prototype design. In other cases, the sizing of actuators happens considering a single point of operation speed/operating torque. Such an experimental approach often increases the cost of development and can lead to over-or under-sizing of actuators leading to performance issues.
Simcenter Amesim provides an efficient solution to address actuators/components sizing challenges. Using a digital twin of the robot, engineers can identify the speed/torque/power requirements based on the given machine mission profile. As shown, the user provides the kinematic joints and the motion profile of delta picker arms as input. Simcenter Amesim calculates precisely the motor’s power and torque requisite. Using these performance criteria engineers can select the actuators from the catalog.
Reliability & Safety
Robots in the factories function seven days a week and almost 24-hours. The continuous operation of actuators and servomotors can increase thermal stress and failure rate. Moreover, the electric motor are prone to produce arc or give off sparks increasing the risk of fire accidents.
With the help of Simcenter Amesim engineers can develop power demand management strategies and algorithms to limit the rise in temperature by controlling the motor’s operation.

Smartness
Another major challenge in robotics engineering is the development and validation of control logics used in PLCs and human machine interface (HMI). The automation and controls department procrastinate software validation until the availability of a prototype. Utilizing Simcenter Amesim virtual commissioning feature, controls engineers can evaluate the accuracy of logics, the machine cycle time and the acceleration/ deceleration profiles coupling PLC controls in the digital environment. The customer benefit is the reduction of the virtual commissioning phase using reliable virtual prototypes, in a risk-free environment.
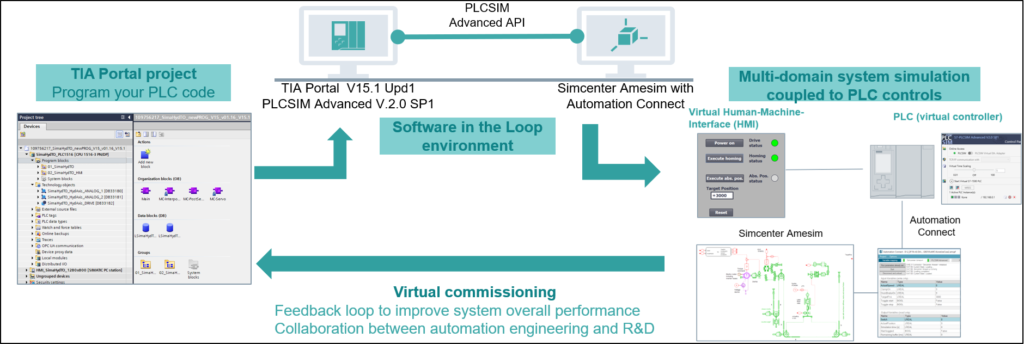
Want to learn more about our robotics offering?
The content above is just a sneak peek of the upcoming webinar on robotics engineering planned on 29th October. You like this content and wish to handle robotics and automation engineering challenges effectively? Please join the live session and get a unique opportunity to interact with the robotics experts.
There is one last thing. Do you know why your caged robots tremble and how to overcome it? You can read the following blog, which highlights vibration troubleshooting and characterizing unwanted resonance.