Executable Digital Twin (xDT): Unleashing Revolutionary Efficiency in Power Plants
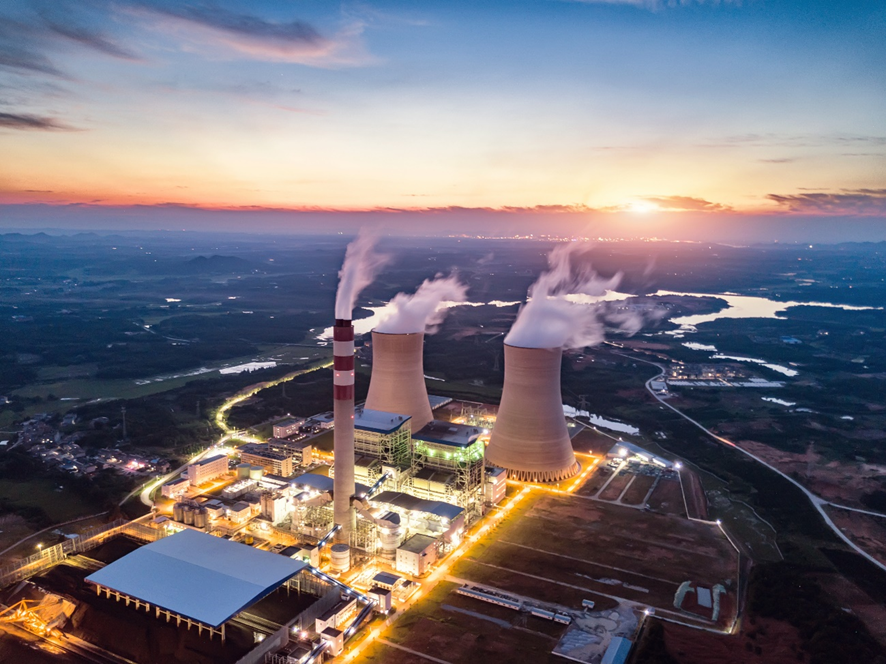
This blog, crafted in collaboration with Shivdeep Gaagat, Simcenter Industry Lead for Energy & Utilities industries, aims to illustrate the potential impact of Executable Digital Twin (xDT) technology on power plant efficiency. Drawing on Siemens’ extensive experience as a provider of simulation technologies, it highlights how xDT addresses the most demanding and challenging problems in this sector.
Introduction
A power plant is struggling with aging infrastructure and high operational costs. Frequent equipment breakdowns, and an inefficient cooling system were constant headaches, hampering the plant’s ability to meet energy demands and maintain profitability. The management knew they needed a radical solution.
The Turning Point
The plant’s management had been wrestling with three major issues:
Cooling System Woes: The plant’s cooling water system was notoriously inefficient, leading to excessive energy consumption and higher operational costs. The system, vital for preventing the plant from overheating, had become a significant drain on resources due to outdated technology and suboptimal operation. Pumps are known to be a leading cause for energy consumption as they count for more than 20% of the global motor electrical energy consumption. [1]
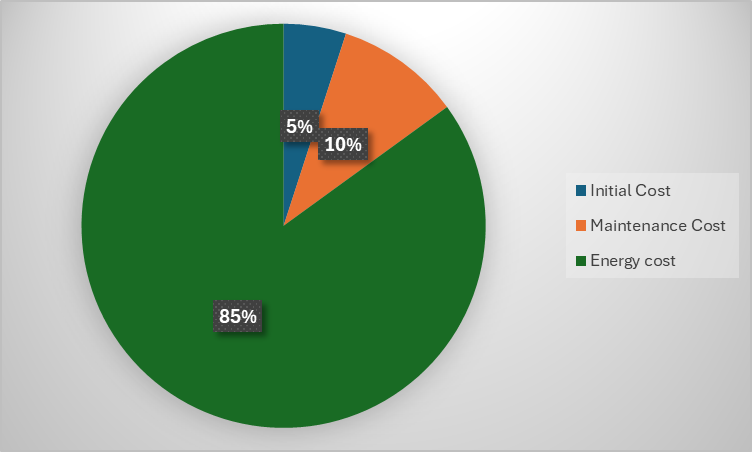
opportunity over the life cycle of a pumping system lays
within the electrical energy costs [1]
Equipment Failures: Frequent unexpected equipment failures caused costly downtimes and maintenance. The plant’s aging turbines, pumps, and other machinery were prone to breaking down, often without warning. These unexpected failures not only halted production but also required expensive emergency repairs.
Decision-Making Hurdles: Operators often had to make quick decisions with limited data, relying heavily on previous experience rather than precise information. In a complex environment like a power plant, this could lead to suboptimal choices and inefficiencies.
Realizing that patchwork fixes wouldn’t cut it, the management team decided to embrace innovation. They chose the Executable Digital Twin (xDT), a cutting-edge technology that creates a digital replica of the plant’s physical assets and systems through physics-based simulation models. This digital twin integrates real-time data with simulations, offering a dynamic and comprehensive view of operations.
xDT implementation
A key advantage of xDT is its ease of integration with both existing systems and workflows. This played a crucial role in the decision to adopt it. By seamlessly connecting with the current infrastructure and requiring minimal additional training for operators, xDT ensured that both the technology and the staff could quickly adapt and start reaping the benefits. This holistic integration enhanced collaboration, making it easier for teams to make well-informed decisions and maintain high operational standards.
Overall impact
The introduction of xDT revolutionized the plant’s operations. Energy consumption dropped, operational costs fell, and equipment reliability improved. The plant was no longer plagued by unexpected failures and inefficient systems. Instead, it operated smoothly and efficiently, meeting energy demands and maintaining profitability.
To understand the depth of these transformations, let’s explore the specific improvements brought by xDT in detail…
Tackling the Cooling System
One of the first targets for xDT was the cooling water system. By simulating water flow and predicting blockages, xDT helped engineers redesign the system. They could see exactly where inefficiencies and potential problems lay. The operators could use this basis to quickly assess “what-if” scenarios and plan maintenance with minimal impact. As a result, they optimized the flow, significantly reducing energy consumption and operational costs. The plant’s cooling system became more efficient, using less power and contributing to a smaller environmental footprint.
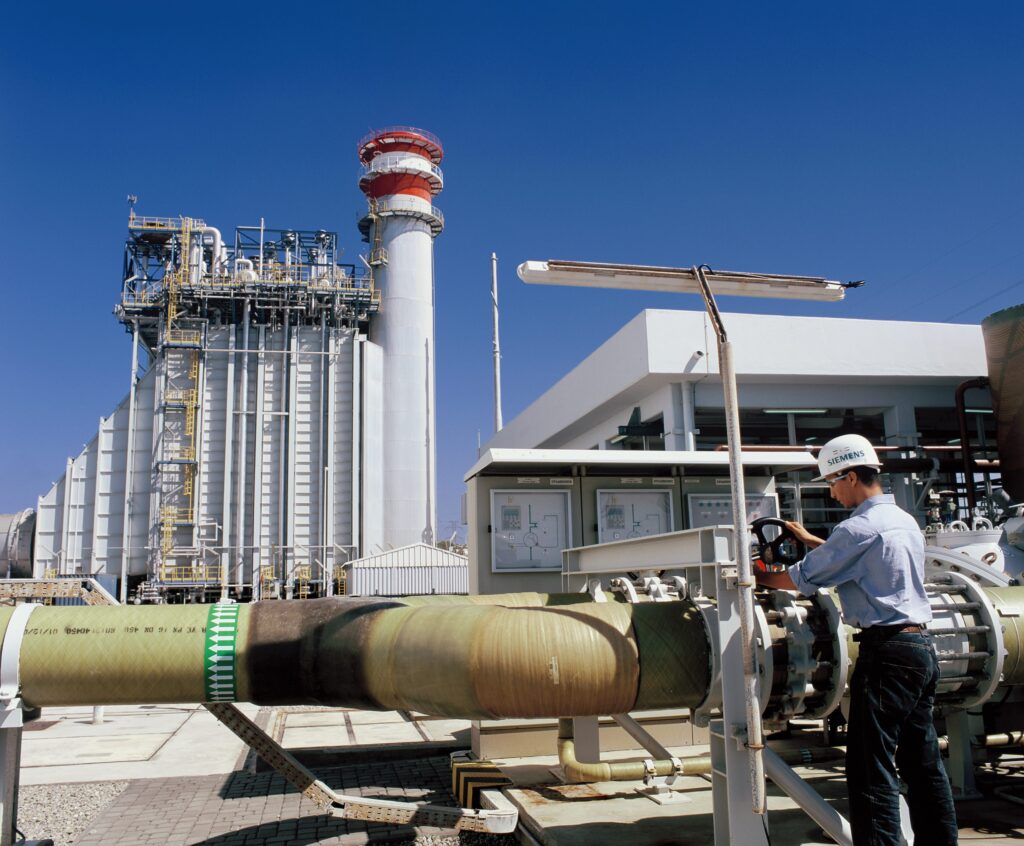
Predictive Maintenance
Next, xDT addressed the frequent equipment failures. With its advanced simulations, it could predict when and where a failure might occur. For example, by feeding operation data into the xDT engineers could forecast when the components degrade. This allowed maintenance teams to perform timely interventions, scheduling repairs during planned downtimes instead of reacting to sudden breakdowns. This shift from reactive to proactive maintenance extended the lifespan of critical machinery and minimized disruptions.
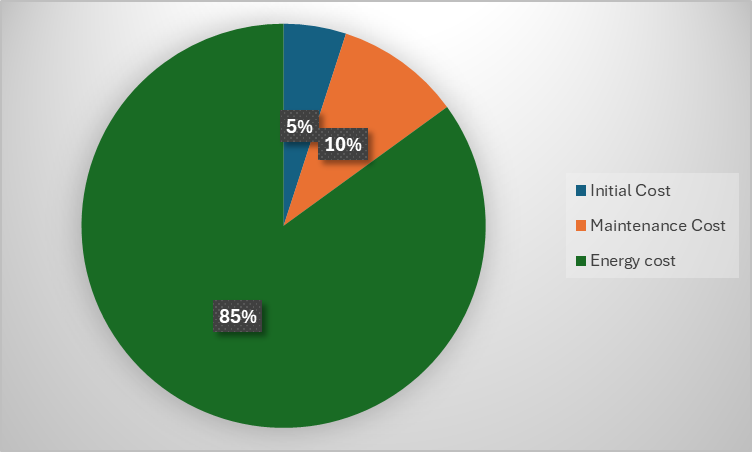
Enhancing Decision-Making
For operators, xDT was a game-changer. It provided a holistic view of the plant’s operations, integrating data from various sources and filling gaps where data was missing. Operators could make informed decisions quickly, backed by precise information. For instance, if there was a sudden drop in turbine efficiency, xDT could help pinpoint the cause and alert operators for immediate corrective actions. This real-time insight prevented minor issues from escalating into major problem
Looking Ahead
With xDT firmly in place, the plant is now well-positioned for the future. The technology provides a solid foundation for continuous improvement and adaptation. As the energy sector evolves, the plant can leverage xDT’s capabilities to integrate renewable energy sources, comply with new regulations, and enhance overall efficiency.
The potential of xDT extends beyond current operations. By incorporating emerging technologies like artificial intelligence and machine learning, the plant can anticipate and respond to future challenges proactively. This approach ensures competitiveness, efficiency, and sustainability, paving the way for a greener and more reliable energy future.
Conclusion
This case study demonstrates the transformative power of xDT technology. By integrating advanced simulations with real-time data, it enables significant efficiency improvements, cost savings, and strategic foresight. As the energy landscape becomes more demanding, traditional power plants must adapt and innovate to stay relevant. xDT offers a proven path to achieving this, turning challenges into opportunities and securing a sustainable future.
Implementing xDT enables powerplant owners to enhance operational efficiency and sustainability. Embrace xDT technology and lead your organization into a new era of efficiency and resilience.