Preventable Electric Motor Failure with Simcenter SPEED
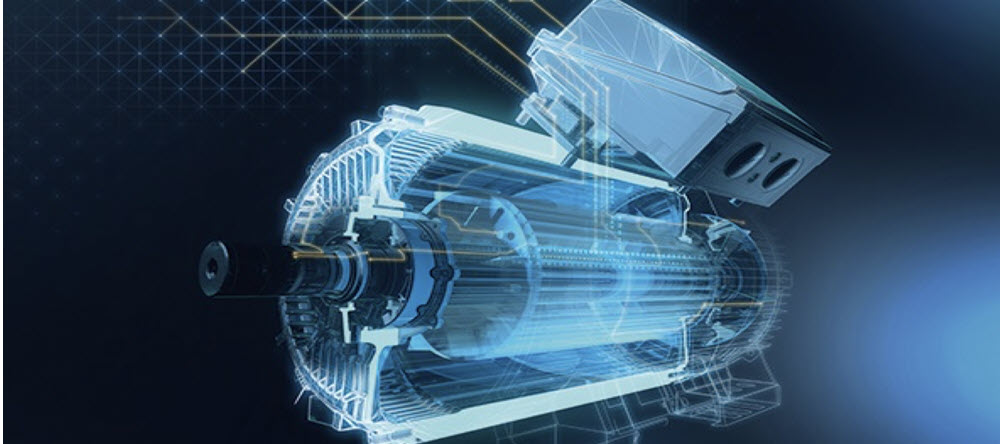
Overloading a motor is a preventable failure that can be avoided with rapid electric machine design software such as Simcenter SPEED.
Preventable Failure of Overloading and Cost of Underloading Motors
Overloaded motors, provided they do not outright fail, will overheat and lose efficiency, which degrades the machine’s performance. On the other hand, consider an underloaded motor. An underloaded motor will typically see a dramatic efficiency drops with decreasing load. All of this culminates into higher costs and improper motor performance, which is why the load point calculation is critical for designers in the preliminary stages of their virtual prototyping. These are common types of preventable electric motor failure and inefficiencies that design software can help avoid.
This on-demand webinar demonstrates how you can increase your efficiency with Simcenter SPEED
Preventable Electric Motor Failure: New Load Point Calculations
Simcenter SPEED is an all-in-one specialized tool for the sizing and preliminary design of motors, generators and alternators. It is a rapid electric machine design software. The latest update, version 2020.2, is now available.
In Simcenter SPEED 2020.2, for Induction machines (PC-IMD), you can save time through a smart calculation of the base speed point for a given torque and terminal voltage value, or of the load point voltage from torque and speed specification with the above corner frequency.
Method 1 – Calculate the base speed point for a given torque and terminal voltage value
Given a supply voltage (less or equal than base voltage) and a requested shaft torque value, this method searches for a rotor speed or rotor frequency (less than the base frequency) with the lowest current matching the requested shaft torque.
Method 2 – Calculate the load point voltage from torque and speed specification with the above corner frequency
Given a shaft torque, speed and base frequency, this method searches for the lowest terminal supply voltage and current whilst matching the requested shaft torque
Additional features and enhancements include:
- More flexible design for permanent magnet assisted synchronous reluctance rotor types through magnet insertion in the flux-barriers (PC-BDC)
- Improved user workflow to share data files between users and within tools reading XML format for the PC-IMD data file.
- An improved user experience within PC-BDC through automatic Torque/Speed graph

Simcenter SPEED 2020.2 includes magnet insertion in the flux-barriers for synchronous reluctance rotors