Hyundai’s durability testing boosted by Simcenter SCADAS RS and Simcenter Testlab
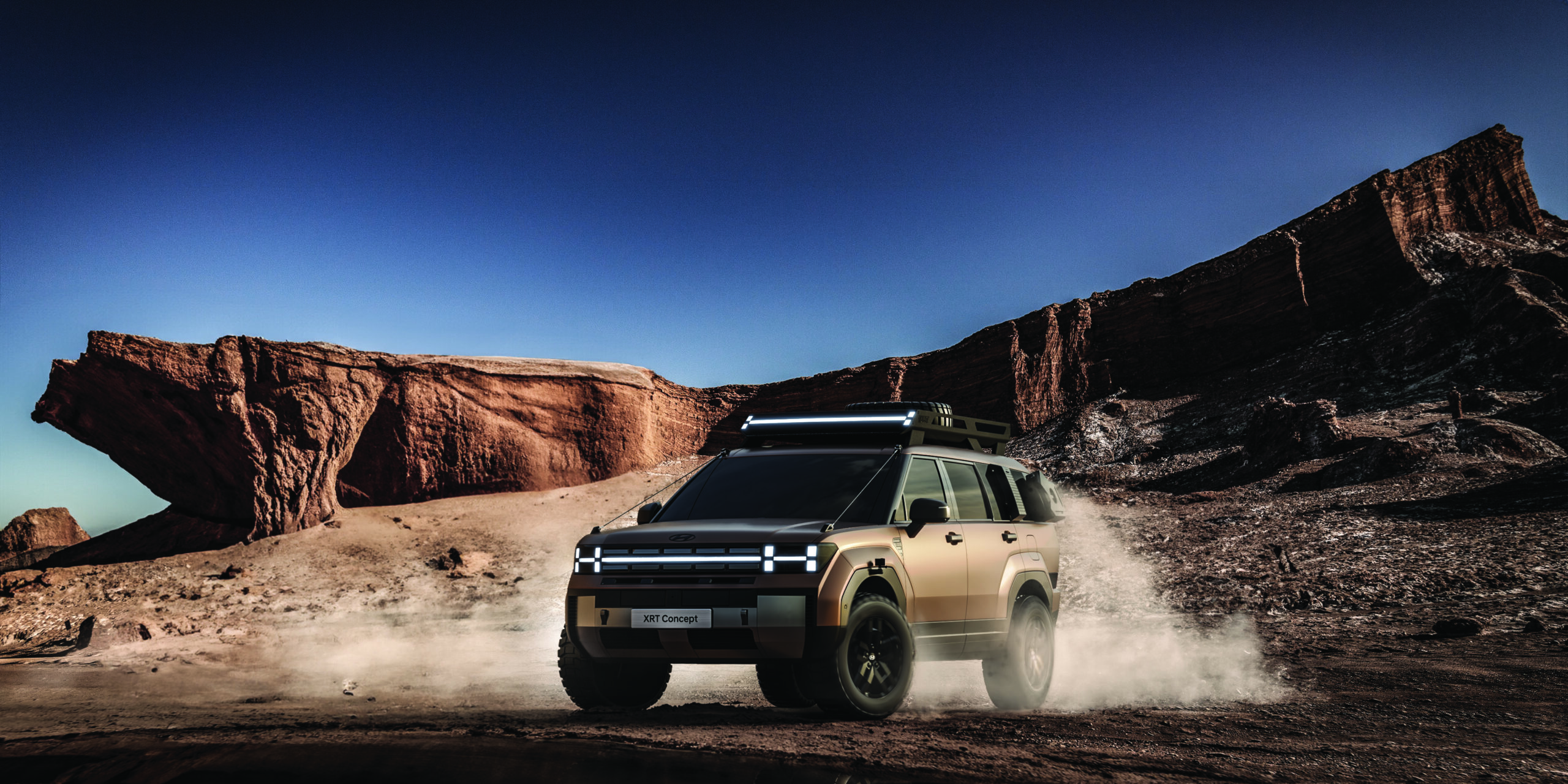
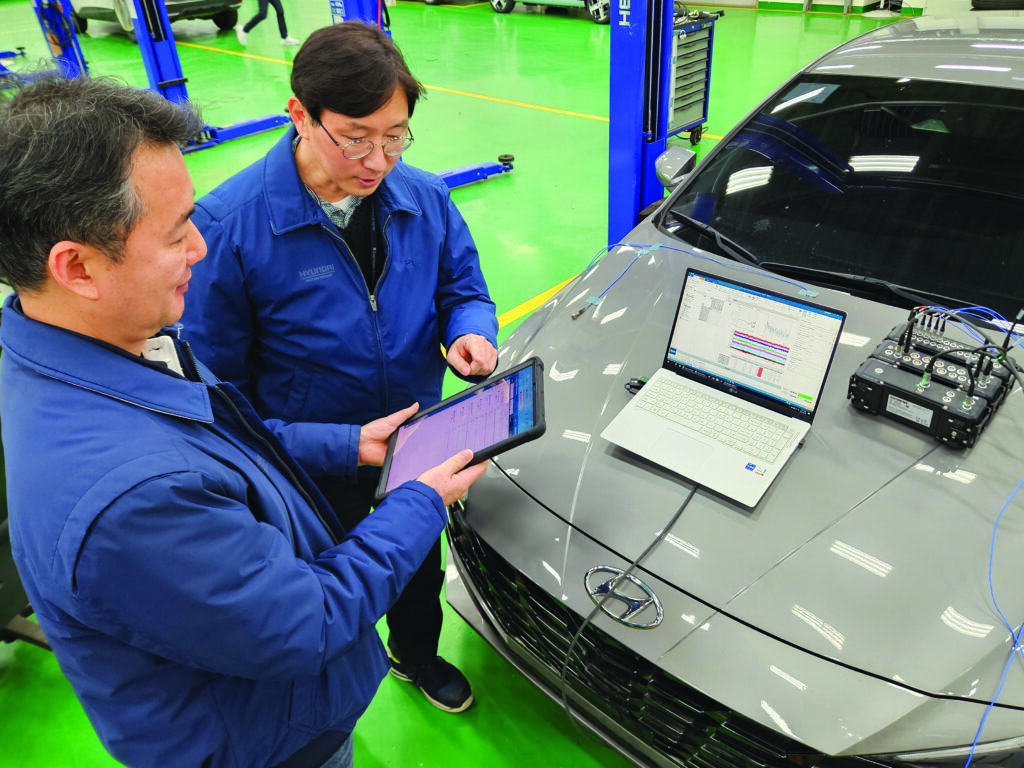
Purchasing a new car is an exciting proposition. It’s also an expensive one; according to Kelley Blue Book data, the average price of a new car purchased in the USA is close to $47,000. It’s usually a considered and extensively researched decision. It shouldn’t be surprising that buyers today, expecting their new cars, sport utility vehicles (SUV) and light trucks to last many years, rank quality and dependability highly on their purchase criteria.
Hyundai Motor Company (HMC) scores highly in both categories, the result of decades of prioritization in designing then building ever more reliable vehicles. This investment in focused, demanding design, engineering and manufacturing continues today in the collaboration HMC enjoys with Siemens.
Warranties and Peace of Mind
Across the globe, HMC offers some of the best warranties available to auto buyers, a commitment it can confidently make due to the reliability and dependability of the vehicles leaving its factories. European buyers, for example, enjoy unlimited mileage warranty protection for five years, plus eight years of coverage (up to 160,000 km) on high-performance high-voltage batteries. In the US, Hyundai, Genesis and Kia buyers enjoy similar bumper-to-bumper five-year coverage (albeit with a 60,000 mile limit) and powertrain coverage of 10 years (100,000 miles). The latter covers drive battery and drive system components for EVs and hybrids.
Proving It: Dependability From Pain
The automotive design and engineering world of the 21st-century is an expensive and extensive process of ideation, creation of the digital twin, iteration and physical prototyping, interspersed with a mountain of analysis. Much of the physical analysis happens at proving grounds and test tracks.
Proving grounds and test tracks are where the rubber meets the road…or dirt, rocks, bumps, potholes, concrete, uphill and downhills, depending on which data engineers need to capture. These purpose-built facilities are labs where design teams can intentionally stress vehicle prototypes, components and subsystems and acquire data on environmental conditions, shocks, vibrations, loads and noise in addition to myriad performance markers.
While HMC customers expect their Hyundai, Genesis and Kia vehicles to last for years before they need replacing, engineering teams can’t spend years testing vehicles to determine future durability. Instead, teams visit the company’s testing facilities and proving grounds to conduct tests designed to benchmark current performance of components and subsystems and extrapolate needs and project future lifespans.
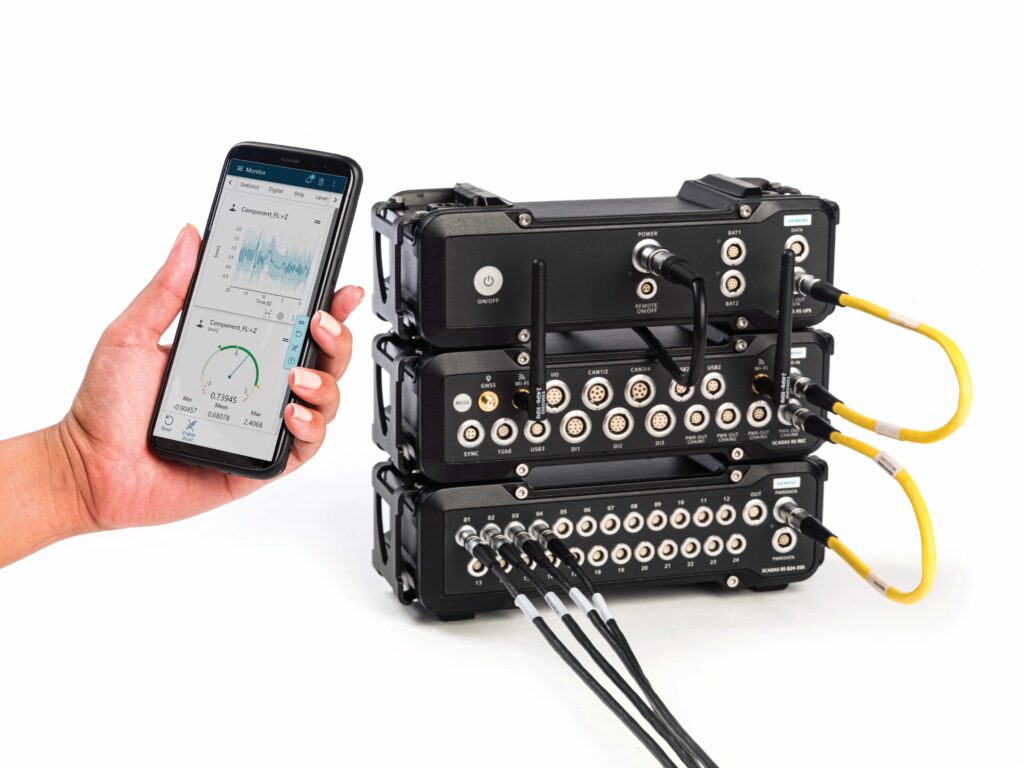
Wanted: A Data Acquisition System That Works in -40C and +40C
Hyundai looked for a data acquisition system that could:
- Acquire road load data for a wide range of sensors in harsh environments
- Accurately measure vibration and improve the durability of EV battery and other vehicle subsystems
- Create test bench schedules based on real-life measured vibration signals
Selection criteria also included portability, accuracy, flexibility, ease-of-use and compatibility with HMC’s preferred product engineering hardware and software. A comprehensive solution including Simcenter™ hardware and software, which are part of the Siemens Xcelerator business platform of software, hardware and services, was ultimately selected. The system’s core is Simcenter SCADAS RS for in-vehicle, real-world data collection and Simcenter Testlab™, an open, single software platform for data acquisition and processing. It has met all of Technology Team Manager Jongwoo Kim’s technical and performance requirements:
- Designed for the rugged and extreme locales where Hyundai tests vehicles,
- Precisely conditions and synchronizes a wide range of sensor types.
- Embedded web app so engineers can immediately validate data to increase efficiency and confirm the correct data is captured.
- Ability to scale to over 1,000 synchronized channels.
- Flexible wireless connectivity to ensure the system can be securely accessed by anyone, anywhere using any device.
An uninterruptible power supply unit to prevent unwanted shut-downs and costly test reruns.
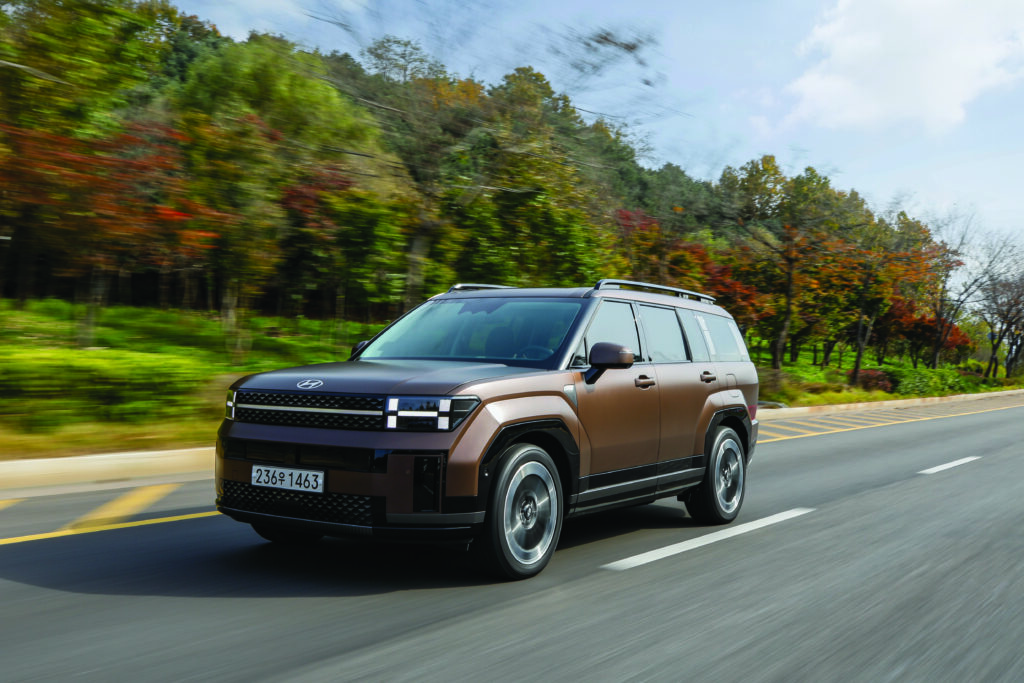
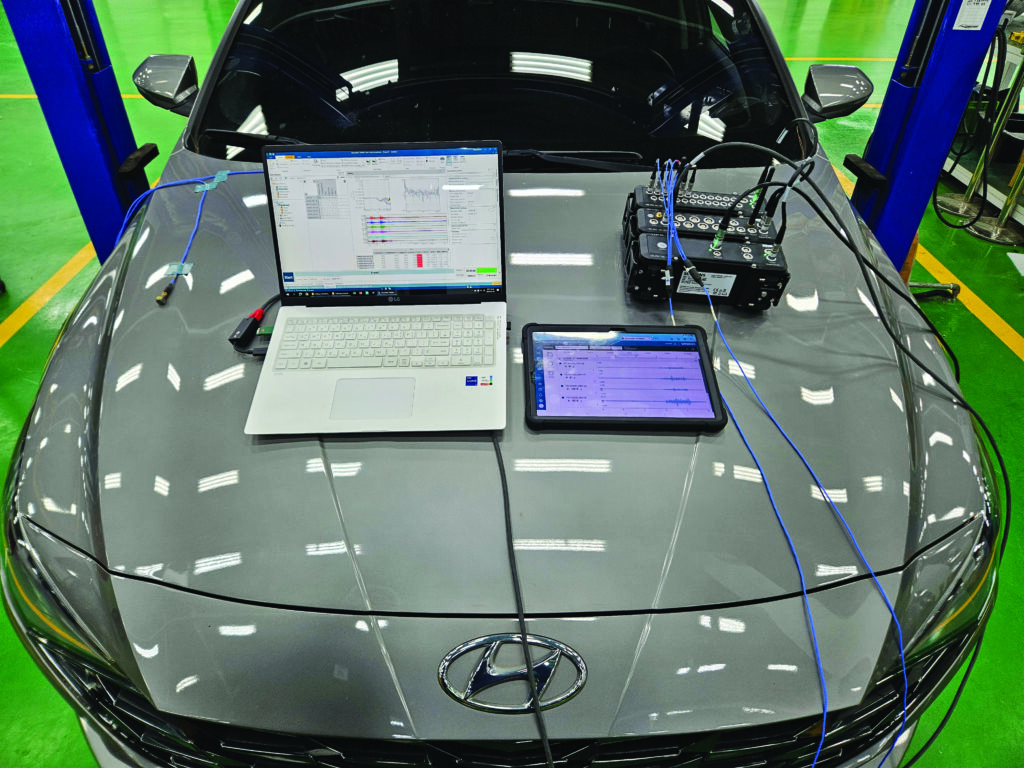
Accuracy Plus After-Sales Support
In combination with Simcenter Testlab software, the Simcenter SCADAS RS hardware provides everything Kim and his team needs to acquire high-fidelity test data and analyze results for efficient design troubleshooting and root-cause analysis. After-sales support included extensive staff training on both software and hardware as well as regular in-person visits by a Siemens engineer to ensure the team was comfortable with the system and ready to fully take advantage of its functionality.
Subsystem and Vehicle Durability Testing
HMC’s durability technology team creates test bench schedules to accurately measure the vehicle subsystem durability. These test schedules are created based on vibration signals measured during road load data acquisition (RLDA) tests on their proving grounds. Test output is further processed and analyzed to predict the durability lifecycle of individual subsystems such as electric vehicle (EV) battery systems.
According to Kim, these RLDA campaigns tests serve multiple purposes: “In addition to measuring accelerations to replicate these on our test bench, we measure wheel forces, chassis part transfer forces and body deformation to enable full vehicle testing. This load data also serves as input for simulation during future development to further optimize the design of each subsystem and the entire vehicle.”
While Kim’s team typically measures 15 to 20 acceleration channels, full-vehicle testing can require as many as 100 channels and many more sensor types, such as strain gauges, accelerometers, displacement sensors, load cells and wheel force transducers. Not surprisingly, setup and configuration take time.
“Each test takes around two to three weeks,” says Kim. “It’s a significant amount of time, so we must ensure the results are accurate and that testing doesn’t take any longer than necessary, especially when the tests are executed in extreme environmental conditions, which is often the case for durability tests. We need the best tools that allow our engineers to work conveniently and easily.”
A Rugged Solution With a Small Footprint
“The compact size of Simcenter SCADAS RS made it much easier than with other solutions to install it in the vehicle and connect the sensor cables,” Kim explains. “Its ruggedness ensures it can withstand strong shocks and vibrations and the wide operating temperature range typical for durability tests. Simcenter Testlab was also very straightforward to install and use.”
Once implemented, the benefits were immediate: “Simcenter SCADAS RS is an extremely accurate and reliable measuring solution. It is also much easier to connect with a wide range of sensors. We can even read vehicle bus data in a specific communication protocol, like CAN-FD, which some similar solutions on the market do not support. The wireless connectivity for controlling the hardware-embedded web application is very useful and the modular system architecture makes it easy to optimize the setup for both small and large test campaigns.”
Since switching to Simcenter SCADAS RS, Kim has seen significant improvement in efficiency: “In terms of time spent setting up measurement channels during the preparation phase, we drastically reduced this by simply using a template rather than starting from scratch each time. The real-time monitoring of the measurement progress with the web application made it much easier and faster to review the acquired data during the actual measurement. Thanks to all these features of Simcenter SCADAS RS, we estimate savings of one to two days over a two- to three-week testing program (a time savings of about 12%).”
“We believe Siemens’ durability and systems analysis tools and noise and vibration analysis tools are excellent and will be important for Hyundai in our future development in areas such as electric vehicles, purpose-built vehicles, urban air mobility and robotics.”
Jongwoo Kim, Technology Team Manager, Hyundai Motor Company
The Future: Perhaps a Little Help from AI
Kim is confident that Siemens Digital Industries Software will continue to play a key role in the development of products at his company. “We believe Siemens durability and systems analysis tools and noise and vibration analysis tools are excellent and will be important for Hyundai for our future development in areas such as electric vehicles, purpose-built vehicles, urban air mobility and robotics,” he says.
He’s also ready to take advantage of the latest artificial intelligence (AI) technology. “Recently, we’ve worked with the Siemens Engineering and Consulting services team to investigate the possibility of using a simplified 1D full vehicle model to predict the wheel forces for given road profiles for later use within a detailed 3D component fatigue analysis,”Kim adds. “We’re looking at using a machine learning-based wheel force corrector approach based on real measured data and a 1D full vehicle model that I think will be an important tool for us in the future to stay ahead of competition.”
Click here for more information on Simcenter SCADAS RS and Simcenter Testlab
Prefer in-depth case study? Click here
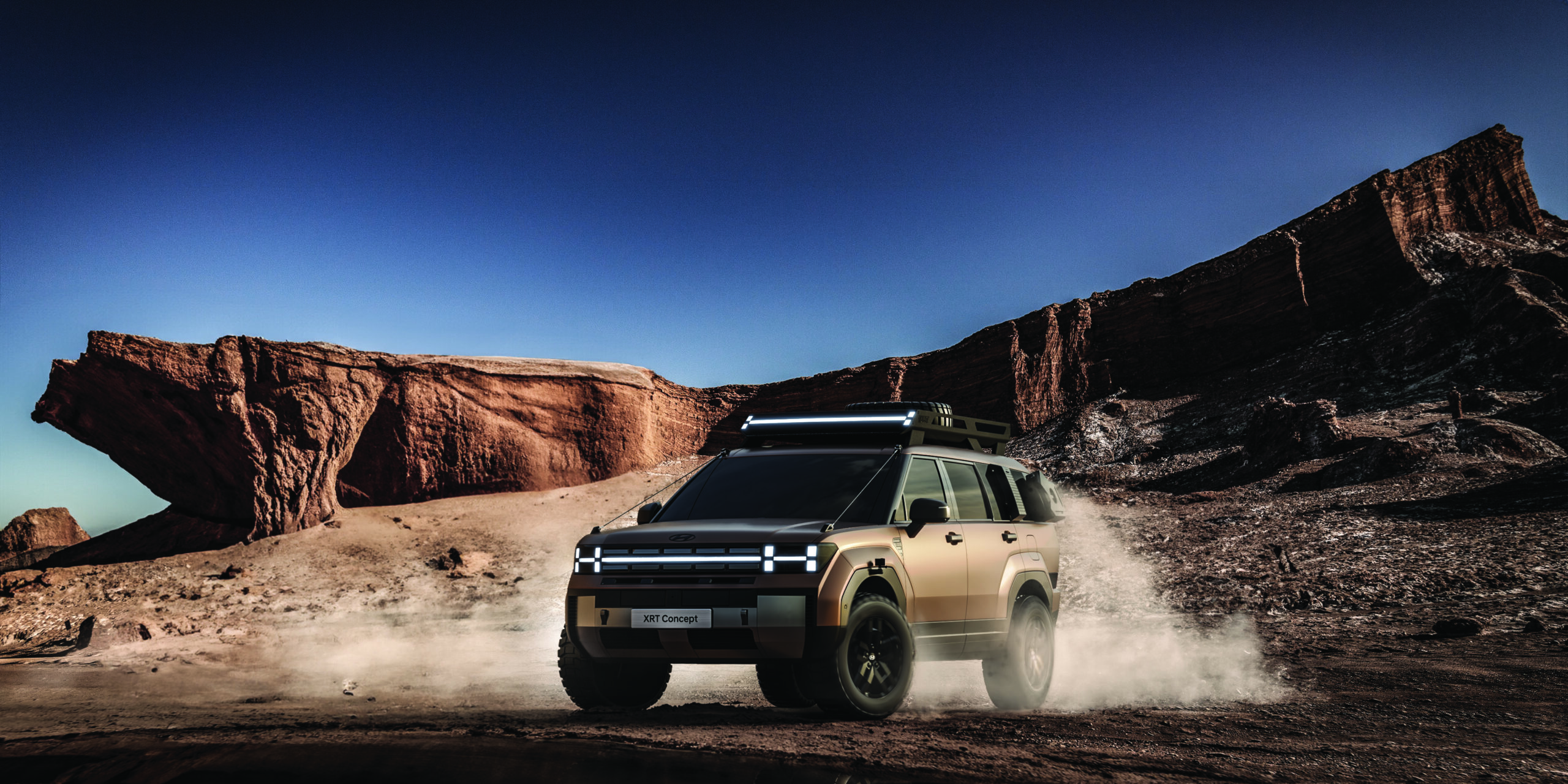
Hyundai and Siemens
Hyundai Motor Company (HMC) is the third-largest automaker in the world, behind only Volkswagen and Toyota. Headquartered in Seoul, South Korea, its mobility brands include Hyundai, Kia and Genesis. HMC has been a Siemens customer for years, notably benefitting from Siemens Simcenter™ Engineering Services, Simcenter SCADAS hardware and Simcenter software portfolio, including Simcenter Testlab, Simcenter™ Amesim™, Simcenter™ Reduced Order Modeling and HEEDS™ applications.