How to virtually evaluate thousands of vehicle configurations?
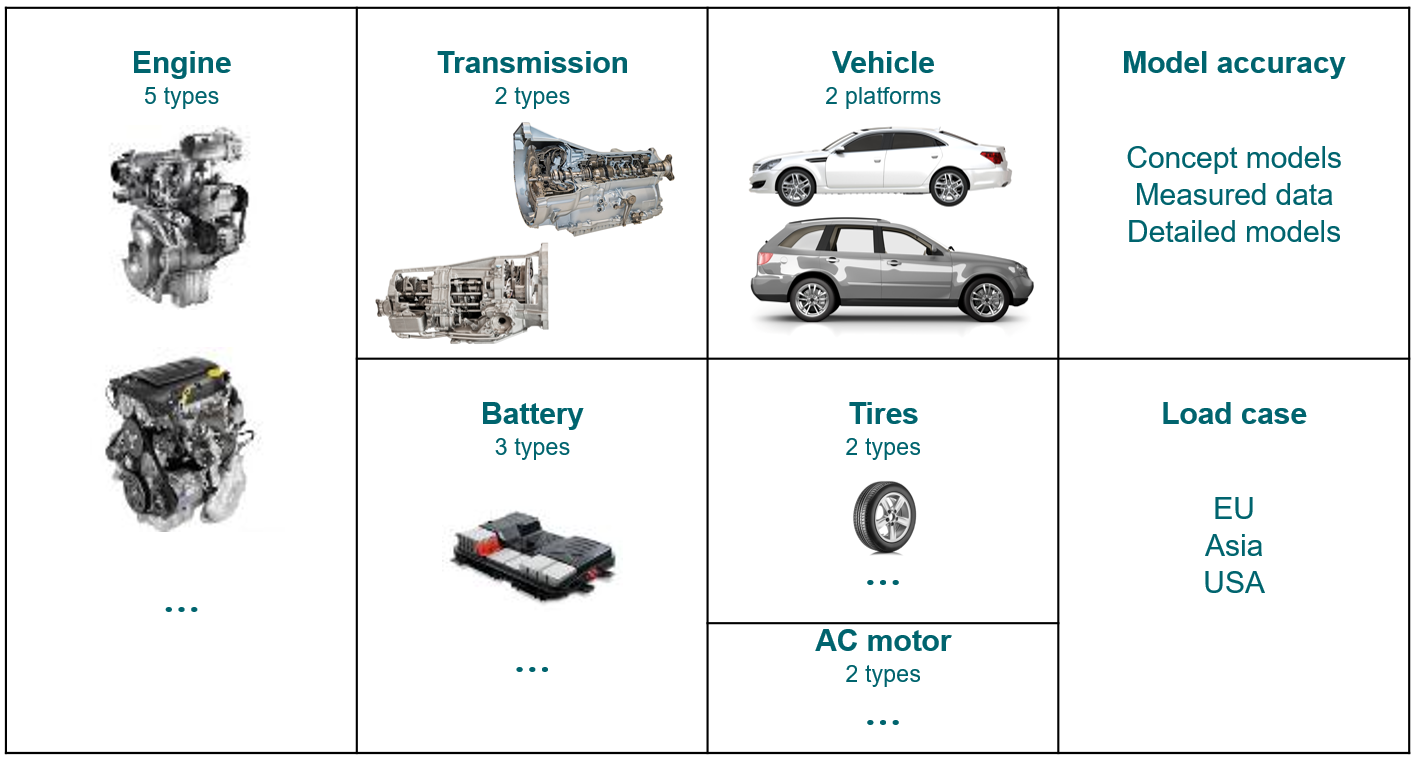
Carmakers use system simulation to virtually balance performance attributes taking into account not only the performance of vehicle subsystems but also control strategies. However, today, a large diversity of vehicle architectures and technologies exist.
Just imagine how many configurations an automotive OEM needs to evaluate when designing a new car. To get an idea, let’s take a look at the picture below. To consider different subsystems (and indeed, the list is not exhaustive), we end up with 2160 configurations: (5x2x2x3x2x2) x 3 levels of modeling x 3 load cases.
Strong variant and configuration management capabilities are needed to tackle this challenge.
Additionally, subsystem models are implemented by different departments, using different authoring tools. Therefore, a framework is needed to integrate these subsystem models and assemble them into an executable system simulation.
Last month, Siemens PLM Software participated in the 2nd Japanese Modelica Conference. The event brought together simulation experts from different countries to share their latest research results. As a member of the Modelica Association, Siemens PLM Software has demonstrated the value of architecture-driven simulation by taking an example of an electric vehicle.
To integrate the vehicle model, our team used supercomponent and cosimulation capabilities of Simcenter Amesim as well as the Functional Mock-up Interface (FMI) standard. The Simcenter System Synthesis software served as a neutral framework for managing heterogeneous simulations.
Want to learn how to leverage all the capabilities of your individual tools within a unique architecture management platform? Read our technical paper (The entire proceedings of the 2nd Japanese Modelica Conference can be found here).
See you in October at the American Modelica Conference in Cambridge, MA!