High fidelity combustion simulations drive down emissions
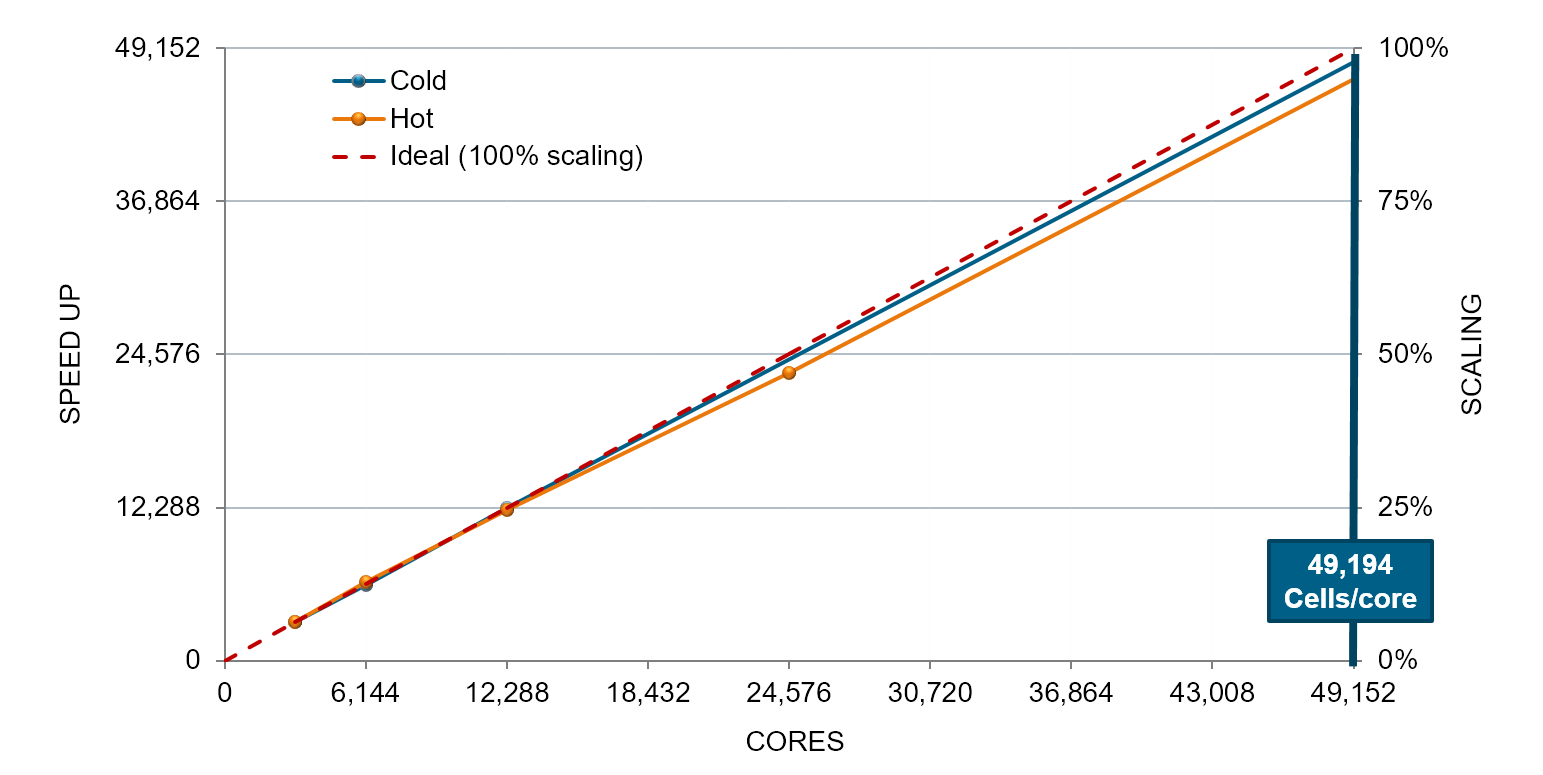
Here in the UK, we are not known for large amounts of sunshine but this summer was the greenest ever for energy, largely driven by the huge growth in the number of solar and wind farms. Between May and September 2017, over 50% of power came from low-carbon sources, compared with 35% in 2013. The energy mix for power generation is changing rapidly, driven by the global goals agreed in Paris to significantly reduce greenhouse gases from electricity production. Natural gas power stations play a vital part in this effort, open and combined cycle gas turbines are increasingly being used to smooth out the peaks in power generation, balancing intermittent wind and solar.
The International Energy Agency anticipates that the world’s use of natural gas will account for at least one-quarter of global energy demand by 2035, and this trend is driving an increasing number of projects to convert idle coal power plants to use natural gas. In comparison with coal-fired power, combined cycle plants offer shorter construction time, lower investment costs and half as much CO2 per kilowatt hour. Non-greenhouse gas emissions such as SO2, NOx, and soot are also relatively low.
Gas turbine manufacturers are investing heavily in research and development, to further increase efficiency and reduce emissions. Today, combined cycle natural gas power plants achieve over 60% efficiency but a performance improvement of just 0.1% equates to a $15M (€13M) reduction in fuel costs over the life of a single gas turbine.
Simulation is a key tool for engineers seeking ever greater gas turbine efficiency. High fidelity modelling of turbulent combustion, focusing on turbulence-chemistry interactions, provide fundamental insight used to improve performance and drive down emissions.
Simulation of combustion is very demanding, chemical reactions take place at the Kolmogorov length scale (which can range from about 0.1km for atmospheric flows, to less than a millimeter for some industrial flows). Correspondingly timescales for chemistry range from nanoseconds to minutes.
Here at Siemens PLM, we are dedicated to providing the best tools for engineers doing this important work. We continue to make advances in complex chemistry and transient large eddy simulation (LES) capabilities in STAR-CCM+ (see Karin’s blog). As the available computing power continues to grow, running detailed simulations with meshes of hundreds of millions of cells is possible. This enables engineers to capture sufficient detail in the combustors of the gas turbine to improve the design.
Over the past few years, we have worked hard to improve the scalability of STAR-CCM+, this enables combustion engineers to run very high fidelity simulation in a practical amount of time. Not just for turbulent “cold flow” but for the entire “hot flow” process, which is essential to improve combustion efficiency and provide accurate predictions of soot and NOx emissions.
We have partnered with the University of Stuttgart to improve the scaling of STAR-CCM+ and recently demonstrated that STAR-CCM+ is capable of running high fidelity gas turbine combustion simulations on a CRAY cluster, using more than 2,000 servers, with over 50,000 compute cores. This model had 692 million trimmed cells and was run using the FGM (Flamelet Generated Manifold) combustion model. Making efficient use of such a large amount of computing power is key if the engineer doubles the number of cores, they expect the simulation to complete in half the time.
In the chart below, you can see that both hot flow, (orange line) and cold flow (blue line) showed almost perfect speed up, very close to the dotted red line, which is 100% parallel efficiency. This kind of scaling makes it possible to distribute the calculations for less than 50,000 cells across each core. A simulation that may have taken weeks to complete can now provide insight to the engineer overnight.
Siemens PLM is proud to provide the tools for increasingly sophisticated simulation, used by engineers around the world to create better gas turbine designs. The efficiency improvement and reduced emissions from gas turbines, supplementing power generation from wind and solar, are making a meaningful difference in the global fight against climate change.
Comments
Comments are closed.