Future-ready: simulation and testing as part of a core engineering education
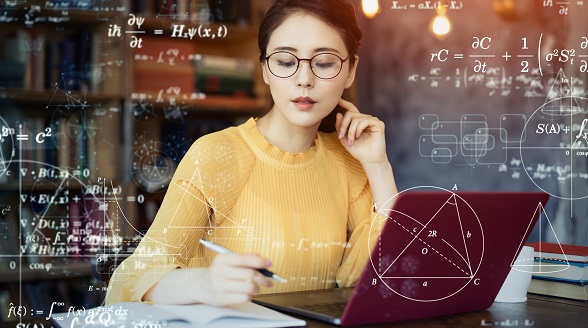
In our first Simcenter for Academia blog post, we talked about the future of engineering in these challenging times and how to bridge the skills gap between what is taught in class and what is required on the job. Next up, we’ll look at why hands-on simulation and testing best practices should part of a core engineering education to open a door of possibilities for the next generation.
Simulation and testing – what does it mean?
To start, simulation lets you try out new concepts and predict behavior virtually with the help of computer-based models or digital twins. Testing, its real-world physical counterpart, is a way to capture actual data to validate and verify existing models and improve future product releases.
Although engineering theory, fundamental physics, and basic modeling are important subjects, they are only pieces of the puzzle. Engineers today need hands-on experience, solving real product challenges with actual simulation and testing tools. Simulation software and physical testing processes are not individual engineering pillars. Consequently, for future engineers, the simulated model and the real-world data will need to be even more connected to facilitate simulation-driven design and digital twin engineering, product and machine learning, and the explosion of the Internet of Things – all areas that your students will need to be prepared for when they enter the job market.
Simulation and modeling fundamentals: a learning progression
Professor Alejandra J Magana from Purdue University surveyed a large group of industrial engineering sectors for her paper: Modeling and Simulation in Engineering Education: A Learning Progression [1].
She reports: “Employers consider of high importance students’ abilities to understand engineering principles and computational principles that allow them to use computational tools to solve engineering problems by moving between physical systems and abstractions in software. Specific abilities identified included the students’ ability to:
- characterize and solve problems at the operational and conceptual levels, translating between the physical and virtual world;
- manage (e.g., collect, store, secure) data, draw meaning from information, and communicate that information to others in a meaningful way;
- learn multiple software and computational systems;
- use information technology (e.g., collaborative tools, instant messaging) to increase business productivity.”
Prof. Magana provides a structured framework to build curriculum, assessment, and instruction for simulation and modeling. Her end-goals include being able to construct and use models to illustrate, explain and predict physical phenomena, compare and evaluate various models for patterns and well as performance prediction, and revising models to increase their predictive power. This all sounds like getting ready to work in a digitalized, highly automated, Internet-of-Things world.
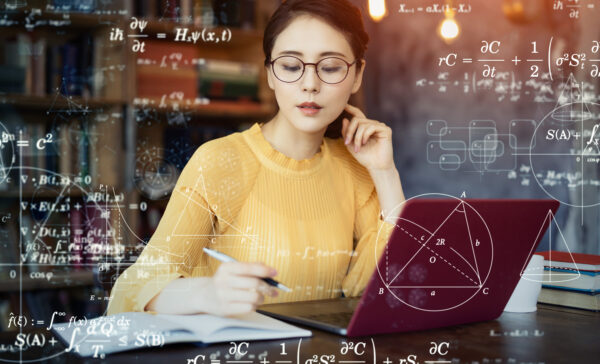
Leveraging simulation and testing fundamentals with knowledge of real industrial challenges in engineering education
Prof. Magana’s recommendations are an excellent start. Nevertheless, it also needs to leverage all those simulation and modeling fundamentals with knowledge of real industrial challenges. Developing industry-based courses and dedicated curriculum to help students understand the complete product development cycle and industry-specific issues is as important as knowing which type of simulation tools and testing processes are required.
Combined correctly, simulation and testing open up the world of digital twin engineering. It appears that the idea of a digital twin has been in use in the industry for a few years already, but it has still not been widely adopted by the academic world.[2]
Basically, a digital twin is defined as: “An exact, virtual representation of a product or process used to virtually validate the performance of its physical counterpart. Engineering departments use Digital twins throughout the product lifecycle to simulate, predict, and optimize the product and production system before investing in physical prototypes and assets.”[3]
Unleashing the true power of digital twins
To create an advanced digital twin, various simulation tools can be used throughout the product development process. This happens from ideation and product architecture definition to detailed design to final control verification and validation. Testing provides additional data and feedback about the model to further improve the design as well as verify physical prototypes. Many new test applications support simulation accuracy by creating more realistic digital twins. This especially considers new materials, complex components, and multi-physic trade-offs. At the moment, the world of testing is looking at real-time feedback loops in regards to in-field product performance and on-the-fly digital twin updates.
At the heart of the Siemens digital twin lies the Simcenter portfolio of simulation and testing tools. Suitable for a variety of applications and domains, engineers can use Simcenter to predict various aspects of a product’s performance. They can create a digital twin that can evolve throughout the entire product lifecycle. It is this unique combination of simulation and testing that delivers a large set of benefits. Thus, this uniqueness enables to discover insights earlier, achieve excellence in cross-domain engineering, unlock innovation and lifecycle optimization, reach unparalleled productivity and agility, and maximize return on investment.
Companies of all sizes around the world have implemented Simcenter-powered digital twins in pursuit of excellence. Preparing your students will help them make a successful transition from the academic to the business world.
Stay tuned…
Next up in our Simcenter for Academia series, we’ll talk to:
- Jan Leuridan, Senior Vice President in charge of simulation and test solutions for Siemens Digital Industries Software.
- Gil Morris, Global Academic Program Manager for Siemens Digital Industries Software.
- Stephen Ferguson, Simcenter Marketing Manager about their vision for Simcenter in the academic world.
Learn more: simulation and testing for engineering education
- Read part one of the series
- Browse our web page for more details:
- Get the latest news
[1] Modeling and Simulation in Engineering Education: A Learning Progression Article in Journal of Professional Issues in Engineering Education and Practice · October 2017. Alejandra J. Magana Purdue University
[2] Tech-Clarity reports : “schools do not prepare students will in the following skills: […] digital twin (44%)” page 10