Ensure the safety of hydrogen mobility
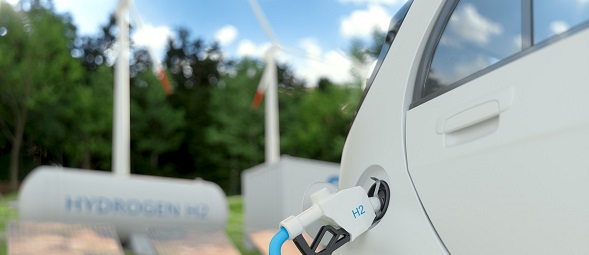
Battery or hydrogen fuel cell?
Mobility electrification is not a trend. It is a fact. Most OEMs are already planning the retirement of their combustion-engine fleets. But with electrification we generally associate Li-ion batteries and a lot of inherent challenges. Rare materials, range anxiety, lack of charging stations, battery safety, poor recycling possibilities are some of them. Although extensive research is being conducted to solve these challenges, an alternative is being considered: hydrogen fuel cell vehicles. In this article we discuss how simulation can help OEMs & suppliers virtually design and certify the composite pressure vessel used for hydrogen storage.
Hydrogen: the miracle source of energy for the future of mobility?
Hydrogen is one of the most common atoms on earth and is an unlimited resource; the range of a hydrogen vehicle is often higher than battery EVs; a hydrogen fuel cell only emits water vapor; and a hydrogen tank can be re-filled in minutes. We therefore consider fuel cells as a more and more serious alternative to batteries.
In the automotive industry, Toyota Mirai and Hyundai Nexo have been precursors. BMW is about to release their iHydrogen NEXT, while Daimler Truck AG and Volvo created a joint venture in 2021 “to accelerate the use of hydrogen-based fuel cells”. A growing number of mobility startups bet on hydrogen as well. In the aerospace industry, Airbus launched in 2020 a ZEROe program aimed at developing hydrogen commercial aircrafts by 2035. Railway industry leader like Siemens are also developing hydrogen trains.
This trend led many governments to fund research to develop hydrogen mobility. A recent example is France, announcing in 2020 that “7 billion euros will be used as funding to make France a spearhead of green hydrogen by 2030“.
Looks promising…so why only “27.500 hydrogen fuel cell vehicles had been sold by year-end 2020 since their sales first began”?
Some technological challenges to solve…
No miracle yet, unfortunately. We need a large quantity of hydrogen to produce every kilowatt-hour, leading to two technological challenges limiting hydrogen expansion.
- Hydrogen production was commonly done through a chemical reaction (SMR) starting from methane and water to produce hydrogen…and a lot of CO2! Hydrogen is now more cleanly produced through electrolysis, consisting of separating water into hydrogen and oxygen…but using electricity!
- Hydrogen storage must be done in a small volume to be embedded into the vehicle, in a restrained available space. This implies very high pressure, and storage systems must obviously be completely safe in all circumstances.
That would require large investments into recharging stations, and the cost of a hydrogen car is still high. For all these reasons, hydrogen fuel cells are still incubating as technology for e-mobility. But these are not insurmountable obstacles.
Storing a large amount of hydrogen in vehicles
Compact tank technologies, safe in all circumstances
Let’s focus here on addressing the second engineering challenge reported above: the safe storage of a large quantity of hydrogen, in a small volume, on a moving vehicle. The state-of-the-art technologies to solve this challenge are hydrogen tanks pressurized at 700 bar! Real embedded bombs…
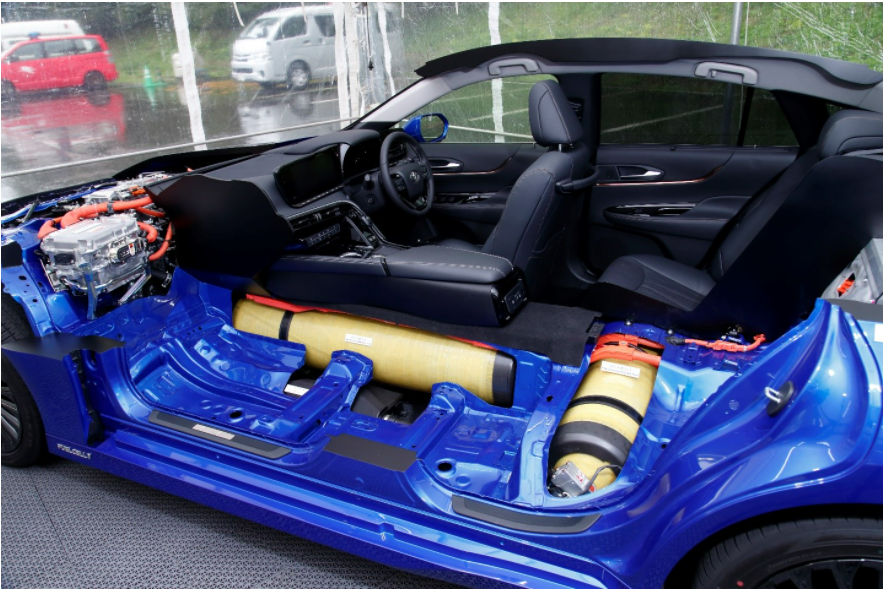
One single accident would probably be fatal for passengers and surrounding people. And it would obviously destroy the brand image of hydrogen as a future mobility solution. Such an accident happened in 2019, not on a vehicle but in a charging station, killing two people and destroying everything around. If we reflect on what a moving vehicle can typically handle during its lifetime compared to a stationary charging station (crash, misuse, tens of thousands of charges and discharges, extreme temperatures, drought, humidity…), safety is definitely a design challenge for these tanks.
700-bar tanks being developed today consist in a polymer liner ensuring the sealing, surrounded by a large thickness of high-strength continuous carbon fiber composites enabling a very high mechanical performance of the tank, and a metallic boss with a valve to close the system and ensure its integration into the vehicle. We call this technology ‘Type IV’, meaning 4th generation of pressurized tanks, or ‘Composite Pressure Vessels’.
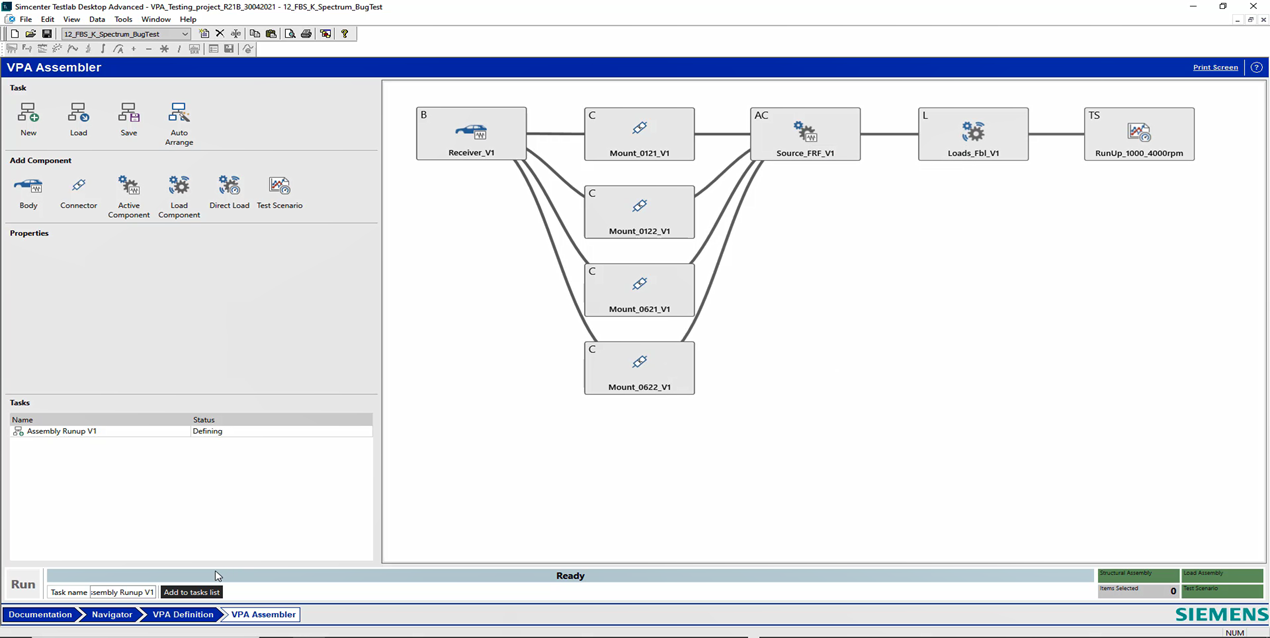
How many years and dollars to certify a Composite Pressure Vessel?
The absolute necessity to ensure safety of hydrogen vehicles leads to very high margins of safety imposed by global standards. The Global Technical Regulation standard N°13, one of the main global references, imposes for example 225% of margin of safety for the burst at ambient temperature, which means a 700 bar tank should never explode before 1575 bar. Variability leads manufacturers to add their own extra margin, up to 1700 or 1800 bar. That allows to secure success of certification tests, and to check, through hundreds of expensive and complicated physical tests, the integrity of their tank.
Burst at ambient temperature, cycling at extreme temperatures, effect of surface damage, resistance to chemical products, falls under different angles and from different heights, creep, bullet shooting, and fire are just some of the tests that safety standards impose. A lot of tank manufacturers execute some of these tests in-house in a very iterative way and assume (or hope…) the other tests will just be fine. In a competitive and increasing market, this is not acceptable anymore. That’s where digitalization comes into play.
Virtual design and certification of a Composite Pressure Vessel
The complexity of the vessel’s technology and the variety of certification tests impose new methods that we can integrate into CAE solutions, targeting full accuracy of the digital twin. Simcenter solutions integrate process and technologies to discover the best possible design, that will be as compact, light, cheap as possible, will be able to carry the expected quantity of hydrogen while respecting all the regulations, and enabling a virtual certification of the as manufactured design, before prototyping.
CAE methods scalability
These innovative CAE methods do not belong to so-called ‘standard CAE’ methods. They must incorporate a lot of different physics and are sometimes not fully mature in the industry. However, the number of CAE analysts working on tank certifications is, in general, rather small, and companies do not have expertise in all the domains. Simcenter solutions span from simplified, automated methods to enable non-experts to determine early concept designs faster, to advanced high-end methods developed and evaluated through research projects with industrial customers to model the complexity.
Early design of Hydrogen tank with simulation: Evaluate thousands of designs in a few hours
With Simcenter, a tank designer would typically start with a very wide design space exploration study leading to one or a few preliminary designs. Instead of approximate analytical methods typically used, we incorporate automated FEM workflows into a Simcenter Heeds problem. A non-expert will be able to evaluate the performance of thousands of designs (with different liner mandrel geometries, boss geometries, materials, composite layups, filament winding strategies…) in a few hours against certification and design requirements. Then he or she can determine best candidates for final adoption. At this stage, the simulations remain linear or include some simple geometric nonlinearity and he / she can use simplified efficient models with basic material laws for all components. The fiber placement is accounted for by automating the execution of the integrated 3rd-party tool, as described later. This gives much more accuracy than analytical methods, while keeping very reasonable efficiency.
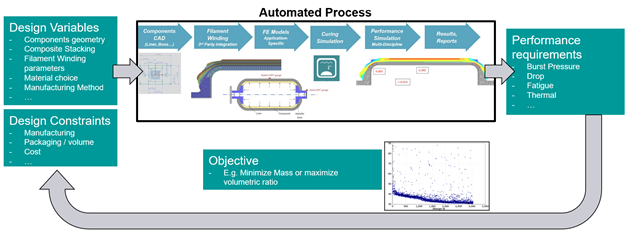
The Simcenter Engineering team (formerly LMS Samtech) worked on the OSIRHYS IV research project. That project aimed at developing and validating these methods, which enabled a 30% mass decrease against vessels designed with analytical methods, with no compromise on performance and capacity.
The importance of simulating the end-to-end manufacturing process of Composite Pressure Vessels for an accurate virtual certification
The manufacturing process of a Composite Pressure Vessel will have a very strong impact on its final performance, and on the variability of these performances. When neglected, tanks may even fail before we use them for the first time. Simcenter solutions accurately simulate the end-to-end manufacturing process to assess a-posteriori the performance of the as-manufactured vessel.
From rotational molding…
The first step is the production of the polymeric liner, done with a rotational molding process. The final geometry and mechanical properties of the liner are highly depending on this process. A too thin or wrongly designed liner will crack and then create leaks in the tank. While an oversized liner would reduce the capacity of the tank and increase its mass. We use Simcenter STAR-CCM+ to simulate the rotational molding process. That includes the temperature control, to achieve the expected liner geometry and mechanical properties.
… to filament winding…
The carbon fibers are then applied around the liner in a pre-defined sequence of orientations by filament winding. This process involves large machines that wind the fibers around the liner. A lot of variables that relate to process control must be handled and will have a very strong impact on the local orientation and thickness of the composite shell [Figure 6], and therefore on the global performance of the tank. Simcenter 3D allows the integration of third-party specialized vertical solutions to accurately simulate the filament winding process. All needed manufacturing parameters are then available through a specific GUI.
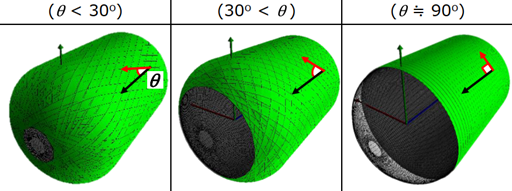
… and curing
The tank is then cured, enabling the polymerization of the composite shell, but possibly affecting the liner performance and inducing residual stresses in the assembly. During the curing, the different materials composing the tank react to temperature changes in very different ways. Simcenter 3D integrates thermal and mechanical solvers and methods that consider the material history during the curing process, determine the process-induced deformations, and evaluate the effects of residual stress on product performance.
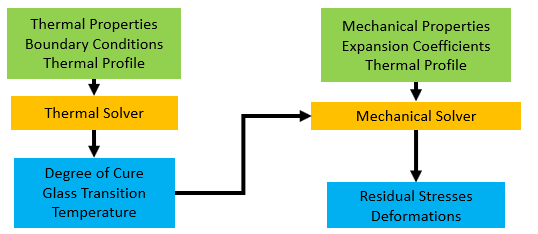
Virtual Certification of Composite Pressure Vessels: Model the Complexity, with full accuracy
You can use Simcenter 3D, the Simcenter Mechanical platform, to model the full complexity of the certification tests.
Composite damage models are natively integrated into Simcenter 3D. It enables the prediction of local phenomena like delamination or stiffness reduction happening during pressurization and de-pressurization. These include innovative static and fatigue methods for composites, developed and validated through industrial projects and applicable to composite pressure vessels.
Thermo-mechanical models are available to assess the effect of temperature combined with different mechanical load cases. Transient dynamic solvers are used to compute the strength of the tank submitted to standard drop tests. Fire resistance has also been studied through the research project FireComp. Finally, Simcenter embeds multi-scale simulation to account for the microscopic behavior of the material in the macroscopic simulation. This opens access to the maximal level of fidelity of the models.
This list is not exhaustive. The benefit of an integrated platform is that we can perform all the load cases in one single platform. One single user can have access to all KPIs in the same environment.
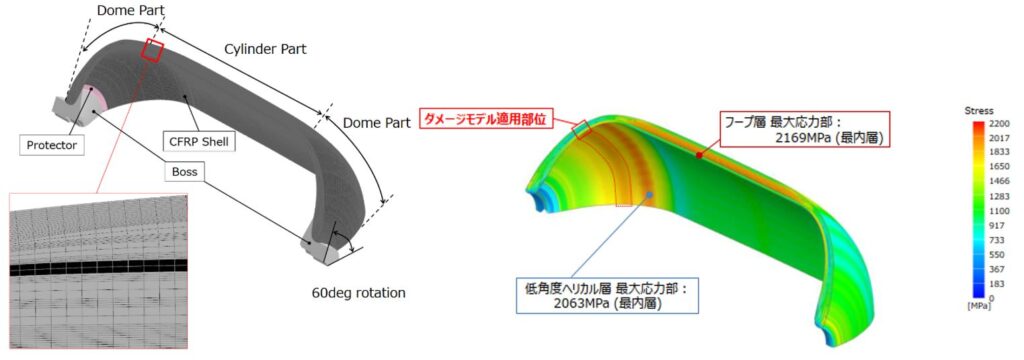
Ways forward to hydrogen mobility
If most analysts predict that battery EVs will keep the lead for small, private passenger cars, we expect to implement the hydrogen solution more and more in larger vehicles like buses, trucks, trains, ships or forklifts. The reason is because they have the space available for pressure vessels and the Li-ion batteries required to power them would be too heavy.
Companies involved in the production of Composite Pressure Vessels for hydrogen storage need to anticipate this expansion. The competition will be fierce. Successful companies will be precursors and not followers. With Simcenter, they can build complete trust into the digital twin of their pressure vessels. The Simcenter team is investing a lot into research. We are working with industrial customers like Honda R&D Co., Ltd to minimize the uncertainty of the predictions, and to create a real digital twin. Those collaboration help on reducing and hopefully someday eliminating all physical tests performed before the certification, replacing them with trustful, cheap, immediate simulations and optimizations, all integrated in one simulation platform.
Obviously, safety also relates on how and where the vessel is integrated into the vehicle. It must be protected from typical crash scenarios, without influencing vehicle weight, NVH, or dynamics behavior. Simcenter offers an integrated and precise digital twin for electric vehicles addressing challenges for all vehicle domains. But that’s another story!
Comments
Comments are closed.
Great article! Simcenter 3D strong capabilities for designing hydrogen high pressure tank are coming as a perfect brick in the Simcenter portfolio to address the challenges related to H2. Especially Simcenter System Simulation also provides solutions to address hydrogen production, transportation, storage, distribution and usage (fuel cells, aircraft turbofan, combustion engine…).