Design safe and reliable landing gear ready for future aircraft configurations
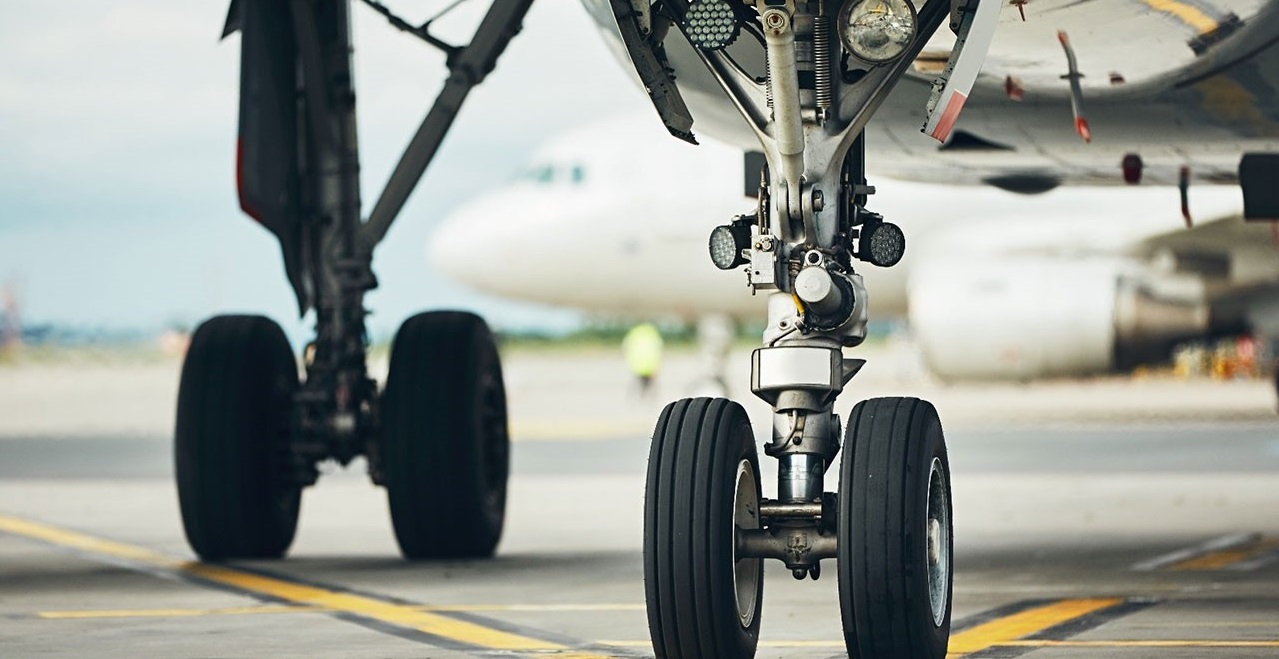
When you sip from your cappuccino and look out on the tarmac from your favorite airport café it’s hard to imagine that those aircraft slowly taxiing, and gliding do that with a highly optimized piece of equipment developed through an extremely elaborate engineering process: the landing gear.
A safe, robust and reliable landing gear is among the most vital parts of an aircraft. Because, just as a bird, a plane could never survive without strong legs when settling down on the ground.
The design of a landing gear starts very early in the development process. Critical decisions such as landing gear arrangement, positioning & ground clearance all have a major impact on ground maneuvering and take-off capabilities. For each configuration, loadings must be calculated to determine the best strategy to pass these loads to the fuselage. This is not a trivial exercise. Take for instance the A350, where Airbus had to adopt a new landing gear attachment philosophy to allow for a better distribution of the loads on the composite wing structure. Simulation is an invaluable tool to perform both system and mechanical design trade-offs.
Frontloading accurate loads not only helps aircraft manufacturers reach a decision on the fuselage structure and attachment locations, it also gives the landing gear manufacturer the necessary data to design a system that is strong enough to support the maximum landing weight. At this point we are optimizing a truly mechatronic system with a shock absorber, retraction/extension actuator with controls, a brake system with anti-skid and brake to vacate capabilities. Simulation models created early in design can be re-used and scaled up for detailed design.
The landing gear is now ready for the ultimate test: a controlled drop in a test rig to ensure that the system will survive the harshest of landings. The extracted performance data is used to correlate and update the virtual landing gear model. Consequently, the updated landing gear model provides more accurate loading data on the fuselage and wing that can help to validate full aircraft behavior.
These validated simulation models serve extremely well during in-service, where the models are used to analyze hard landings and decide if an aircraft is “good to go” or should remain grounded for further inspections.
As time goes by, market requirements evolve in such a way that such that a redesign of the original landing gear architecture is needed. This was recently confirmed with 737 MAX jet. When Boeing’s customers said they wanted a stretched-out 737 MAX jet, there was one big problem: The 737’s landing gear was too short to handle it. Boeing engineers had to redesign the landing gear make it shorter during retraction so that it would still fit in the original landing gear bay, conceived in the 60’s!
In this case, simulation is an invaluable resource to analyze the implications of modifications in the virtual world before committing to prototype.