Design. Performance. Lifetime – Insights from Thermal Ohm’s Law

There’s a catch. You only get to choose 2 of 3 from design, performance and lifetime. The third is a consequence of the other two choices with consideration of Ohm’s law thermal analogy applied to thermal management of electronics. This is an insight shared by Wendy Luiten, an electronics thermal expert and a design for six sigma master black belt, who has learnt the hard way. Wendy now teaches others, including yours truly.
Consider Thermal Resistance fundamental impacts
The temperature rise over a thermal resistance is proportional to the amount of heat that flows through it. That’s Thermal Ohm’s Law, the thermal equivalent of Ohm’s Law for electrical circuits. It sounds simple, complete and all-encompassing. It is – it’s quite literally the big picture. But what does this scientific understanding mean for real engineering design?
In practice the temperature rise is linked to product use and customer expectation regarding usage conditions, lifetime and reliability.
The heat dissipation links back to customer expectation about performance. Thermal resistance is linked to the design of the product, its size, and aesthetics which give the product its characteristic look and feel.
So while Thermal Ohm’s Law applies, the power dissipation, reliability and thermal resistance are interdependent. You cannot independently choose performance and featuring *and* use case, lifetime and reliability *and* design. In short, you can only choose two out of three.
Why do companies often still over-look this thermal Ohm’s law lesson?
The main reason is that these three aspects of the product’s attributes are worked on separately, by independent groups working in their respective technological silos. No problems will emerge in development and testing as Thermal Ohm’s Law only manifests itself when all three need to act together, typically at the first product integration step when the development budget has been spent and physical hardware exists. The dissipation and thermal resistance having been locked in, and too late to fix the thermal problem, the performance specifications have to be relaxed. At this point the time pressure will be enormous, the situation complex, and compounded by the vested interests of the different groups involved. The underlying cause may never be fully understood.
Many companies now have incorporated computer simulations to verify the thermal design, and some for over 30 years. Back then simulations took place after the respective departments completed their design and development trajectories, replacing like-for-like hardware prototypes with computer simulations. Simulating a design was cheaper than building a prototype, so the main business driver for adopting simulation was saving cost. Thermal engineers were experimentalists, swapping thermocouples that only show temperature at selected locations, with simulations that showed temperatures everywhere. But there was an unexpected benefit – Insight. Thermocouples don’t show what the air is doing. Computational techniques make it possible to check for conflicts between expectations of performance, usability and design without having to wait for the development stage where hardware would traditionally be available. The thermal models at the time were built at the system level, as it at this integration stage that the problems were identified by prototyping. Without realizing it at the time, in electronics thermal design, the digital twin was being developed in the mid-1990s.
Simulation in early stage design – critical electronics cooling insight
Early use of system-level thermal simulations can show up issues well before they escalate, when there is sufficient time still available to find a better design. By using thermal simulation early in design, and communicating results and the impact of design choices between the different groups involved, you can have three out of three. But then you do have to use thermal design pro-actively, from early design.
Learn from experts in thermal management of electronics
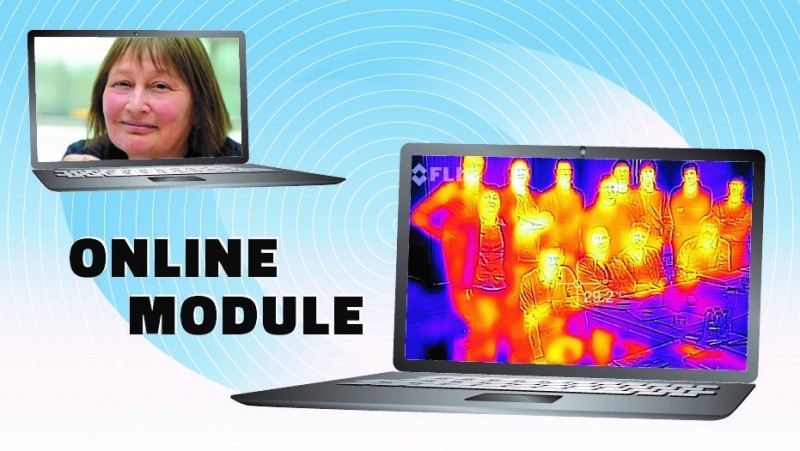
Wendy Luiten regularly runs virtual thermal design courses through The High Tech Institute in Eindhoven, the Netherlands, on-line, and in-house for companies. She often hears participants explain that at in their company, they only get to run CFD simulations when the electronics and mechanical CAD is finished and they can read in the respective files. By then, it is too late to make changes. It is a misunderstanding that you need electronic and mechanical CAD files in the final versions to run meaningful CFD. You can get very meaningful insights working from earlier versions, and incorporating thermal simulations in concept phase is very often key to get to a three-out-of-three design solution.
If you’re interested in getting started with thermal design, or want to understand how Simcenter software for electronics cooling can help you move thermal design higher up your workflow, you can try yourself for free through online virtual labs for Simcenter Flotherm and Simcenter Flotherm XT. There is also a variety of complimentary application topic on-demand webinars you can watch, such as this recent example on appropriate chip package thermal modeling vs the design stage. For clients and those learning to use tools, there are also online on-demand training libraries which can be accessed free for 30 days.