Commission your machine before building a prototype
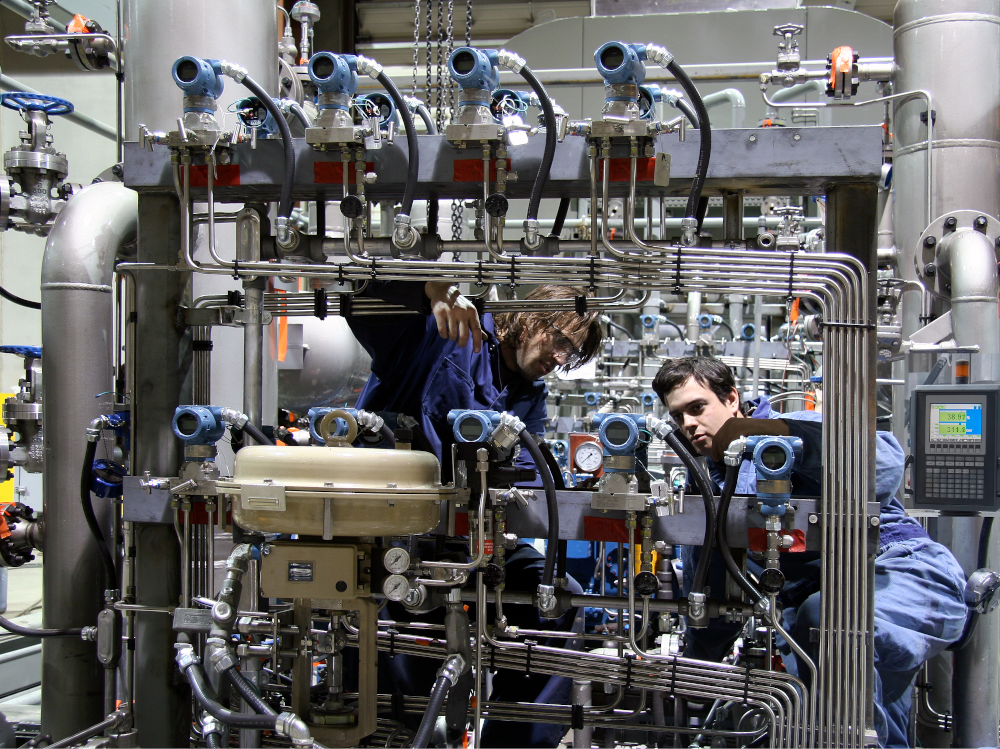
Overcoming 30-year-old legacy
On a client factory floor after erecting a new machine over two weeks, the senior start-up manager and his team are busy launching cold & hot testing.
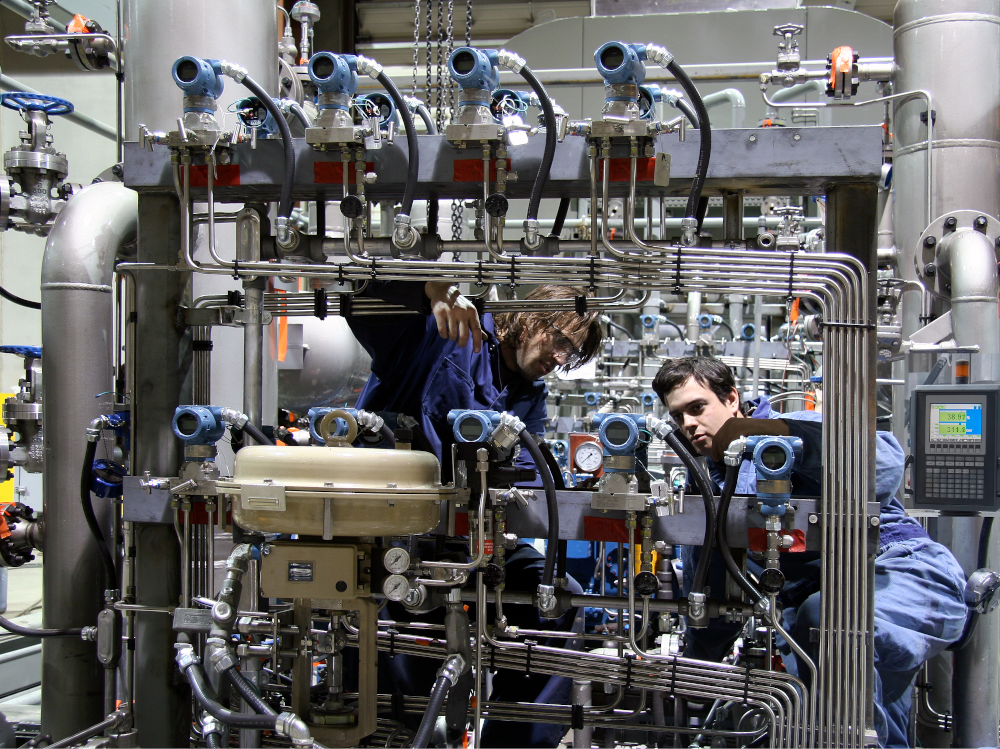
The next step in the commissioning phase is performance testing. The anticipation in the air is palpable. This machine, built to unique requirements, invokes special control algorithms (PLC code). Ensuring the smooth functioning of several physical domains (pneumatics, hydraulics, mechanics, and electrical) posed challenges of epic proportions. The automation engineer reflects on how the unavailability of the iconic controller delayed automation and sensors’ calibration.
Then to avoid overrun senior automation colleagues joined forces; performed code validation through evolving prototypes to ensure proper sizing, optimize control loops and evaluate every aspect of the performance falls within the expected efficiency range — its ability to cool, deliver required pressure, and meet energy efficiency requirements for different load scenarios…
As our automation engineer continues pondering:
The commissioning task is more complex and riskier than ever before but our current way of commissioning is a 30-year-old legacy. To sustain in the Industry 4.0 context things have to change. We cannot build a sustainable business model by solely relying on previous experience and existing prototypes; What would have happened if our automation code could not deliver intended performance on time?
The above machine commissioning excerpt, although specific, resonates across manufacturers. A traditional machine automation process involves a significant amount of software testing on expensive physical prototypes that could take months to build and evaluate. The system bugs and incompatibilities are only exposed when the plant is assembled and in some worst-case scenarios when the engineers are commissioning it on site.
Blaze a trail
With a shorter time to market and diminishing profit margins, machine manufacturers around the world wrestle with how to best evaluate control algorithms early in the development phase and optimize multi-physics system performance before committing to prototype.
Luckily, the digital emulation of logic or virtual commissioning technology is there for the rescue. As rightly stated by Mr. Michael Maier from Maier Werkzeugmaschinen GmbH & Co. KG
The longer it takes to commission a real machine, the longer the money is tied up on the shop floor. Each individual activity eliminated is therefore a gain, because we can perform this task ahead of time on the Digital Twin.
The ultimate goal of virtual commissioning is to provide an environment for the manufacturing automation controls engineer to emulate control logics, size multi-physical system, validate their PLC (Programmable Logic Controller) ladder logic and HMI (Human-Machine Interface) files
Virtual commissioning
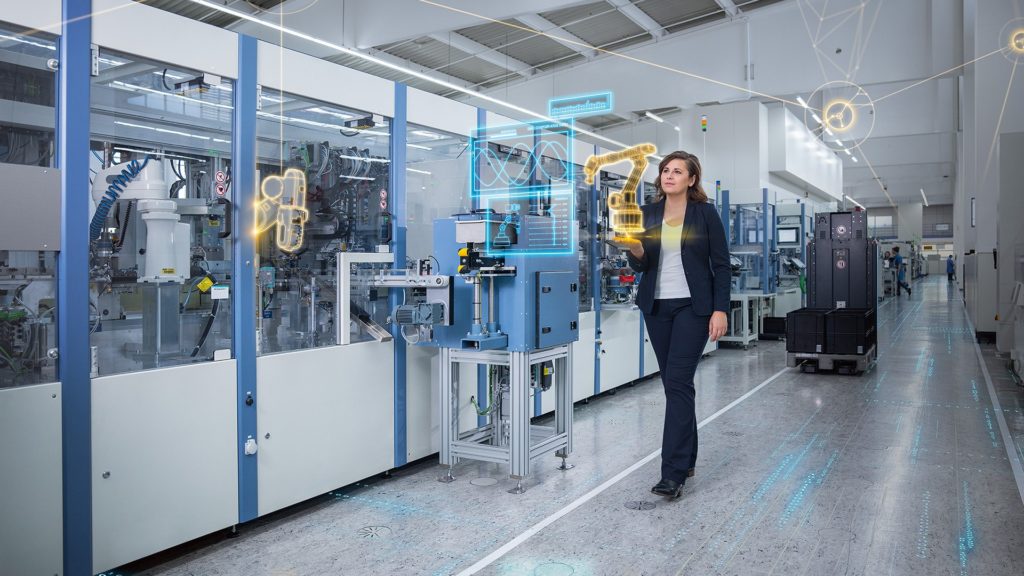
From improving the quality of the final product to reducing development time and cost, virtual commissioning permits manufacturers to roll out a concurrent mechanical, software, electrics and electronics (E/E) hardware design process and replace expensive and time-consuming physical tests with early virtual evaluation.
In the virtual commissioning process, the first step is to mimic the multiphysics system with its components and their connections on a digital mockup. Next, parametrize the individual components and define the automation interface. The input/output of the virtual model has to be connected with the PLC program. Depending on the requirement and hardware availability a real or virtual controller can be used for this purpose. The digital model linked with the controller commissions the real machine virtually and helps analyze any multiphysics and PLC control parameters of the machine and its components (hydraulic oscillations, pressure loss, Temperature, cycle time, energy consumption or what-if scenarios etc).
The virtual commissioning technology is as simple and direct as it sounds. Watch this new video and learn for yourself how Siemens technologies — Simcenter Amesim, TIA Portal and PLCSIM Advanced — seamlessly commission the hydraulic axis virtually.
Benefits of digital commissioning
Validating automation code and machine performance limits early is vital to deliver competitive products at a profitable price. Virtual commissioning enables such early validation even before committing to expensive prototypes. Some of the key benefits to machine manufacturers are listed below:
- Reduce the total time and cost for the development of machine
- Overcome design losses. Deliver customized machines by sizing multi-domain systems according to specifications.
- Make perfect design choices through profound engineering analysis. Perform trade-off between individual performance attributes with cognizance.
- Save resources and life by analyzing failures scenarios in a digital environment
- Provide insights during machine operation and prescribe maintenance only when needed
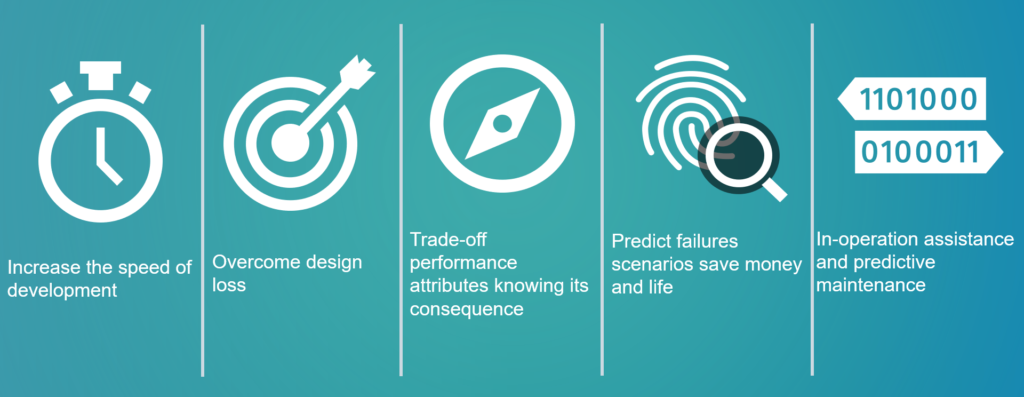
Technologies used for virtual commissioning
As explained in the above video the following technologies are used for virtual commissioning of hydraulic axes.
Simcenter Amesim software is an integrated, scalable mechatronic system simulation platform that allows you to virtually assess and optimize system performance. With ready-to-use multiphysics libraries combined with application and industry-oriented solutions, Simcenter Amesim let you rapidly create models and accurately perform analysis of the mechanical, hydraulic, pneumatic, thermal, electric and electronic system.
Automation connect module permits connecting your Simcenter Amesim digital twin model with real or virtual programmable logic controllers (PLCs)
SIMATIC S7 controllers offer powerful hardware for controlling all types of machines and plants.
PLCSIM Advanced enables creating virtual controllers is the basis for software-in-the-loop solutions in virtual commissioning. Virtual controller PLCSIM Advanced is based on the SIMATIC S7-1500. An open interface (API) ensures flexible use with other simulation tools and test environments.
TIA (Totally Integrated Automation) Portal provides you with unrestricted access to a complete range of digitalized automation services, from digital planning and integrated engineering to transparent operation. The PLC code controlling the hydraulic axis is created using the SIMATIC SimaHyd standard application for hydraulic presses (https://support.industry.siemens.com/cs/ww/de/view/109756217).
In combination with the example HMI you can simulate and validate your PLC Code together with the digital twin.