Bring Your Kids to Work Ep.1: The Executable Digital Twin
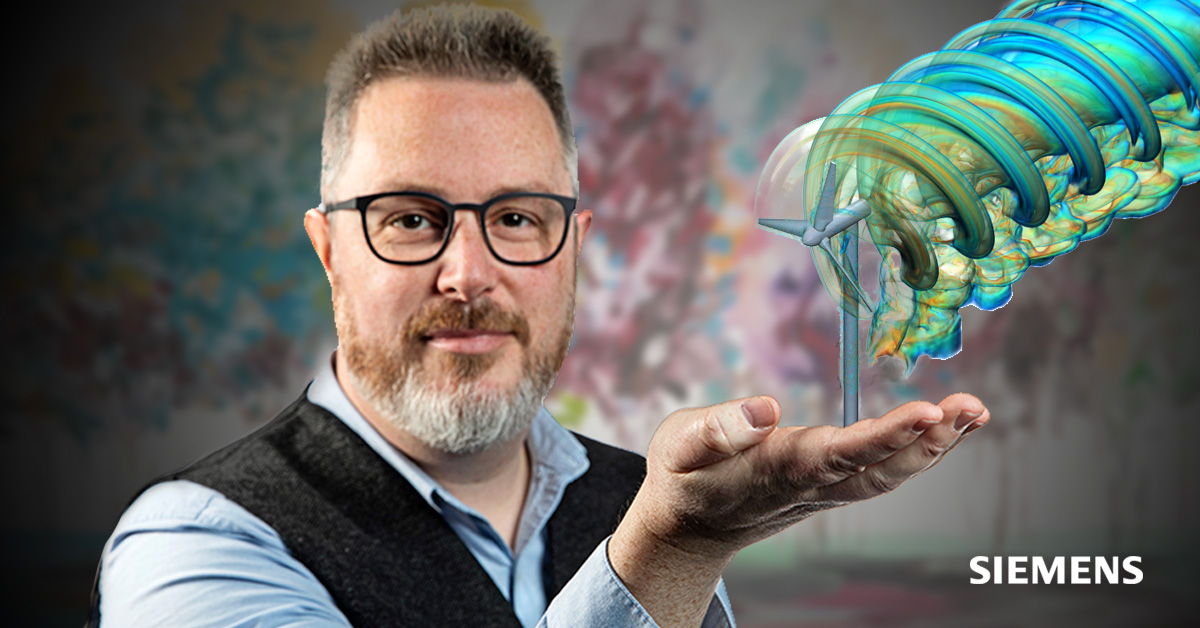
We recently invited some of our key staff to bring their kids into the office and to try to explain in a child’s terms what they do for work. The results were entertaining, funny, and quite informative. In the first episode, we invited Siemens’ executable digital twin expert Ian McGann to talk to his son Colin. They talked about how Simcenter is helping to engineer a more sustainable world by designing better wind turbines. As usual with Ian, it didn’t take long to twist the conversation round to the executable digital twin:
The key insight from Colin here is that Siemens can help to design the individual parts of the wind turbine – more efficient blades, quieter turbines, and more robust gearboxes. However, what happens when the turbine is out in the field, or more likely, out at sea?
This highlights a fundamental difference in how most of us in the simulation and test game define ourselves (mainly “helping to design things to make the world a better place”) and how members of the public define engineers (“people that fix broken machines”).
The executable digital twin is a way of reconciling this. It’s a way of extending the usefulness of the simulation models that we create into the operational life of the products we design. It’s a way of extending measurement and test throughout the lifetime of a product. More than that, it’s a way of combining simulation and test inside a living, breathing model. This model learns and evolves from the conditions that it experiences in the field (or more likely in the middle of the ocean).
After Colin had left, I sat down with his dad, for a less child-friendly chat about the executable digital twin as applied to wind turbines.
1. The xDT is not just another “black box”!
“For a land-based wind turbine, I can easily walk up to it, plug a device in. I can say, ‘give me your updated status; everything is easily accessible,” says McGann. “Out in the middle of the ocean, nothing is easily accessible. It’s much more expensive in terms of time and resources. It can also be dangerous in the wrong weather conditions. This means I don’t want to go and do regular maintenance every six months if I don’t absolutely need to. So, I really need the wind turbine to tell me ahead of time when it’s going to break.”
Traditionally this problem was (and still is) tackled by collecting lots of operational data from existing wind turbines. This data is used to construct a statistical model to predict when some essential component of an individual turbine might fail.
“These algorithm-based approaches are too reactive for something like a wind turbine for which I don’t necessarily have a lot of data and for which failure modes might be particular to a specific installation or use case. We need a more industrialised approach.”
According to McGann, that is where the executable digital twin (or xDT for short) comes in.
2. The xDT is physics-based!
“During the development process, we rely on embedding physical sensors into a product – for example, a wind turbine blade – so that we can validate our simulation models and gain confidence that they are providing sensible predictions,” explains McGann. “There might be hundreds of sensors embedded into a test blade.”
“Ideally, we’d like to have our production turbine blade providing that much data, but no one can afford to build hundreds of sensors into every blade,” says McGann. “But the good news is that with the xDT, we don’t need to because we can replace them all with two or three sensors and a physics-based model that can predict response data at any number of ‘virtual’ sensor locations”.
What is happening here is that the executable twin is running real-time simulations in the background, which allows it to reconstruct data across the whole model that corresponds with the known data measured at the limited number of actual sensors. This is not “extrapolation” but physics-based prediction.
“You have to have known inputs, so the virtual model needs to know where the sensors on the real model are located, but the output can be anywhere on the whole model,” he explains McGann. “You can even put “virtual sensors” in places that would be impossible on the real blade.”
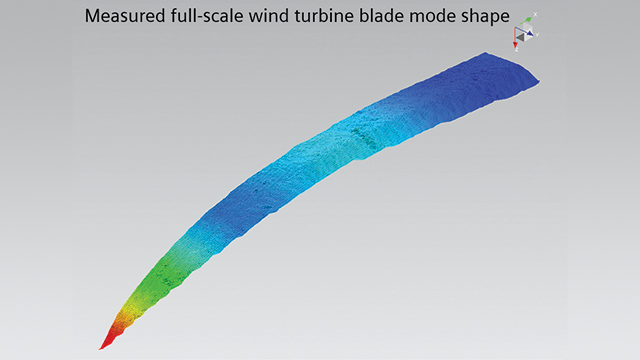
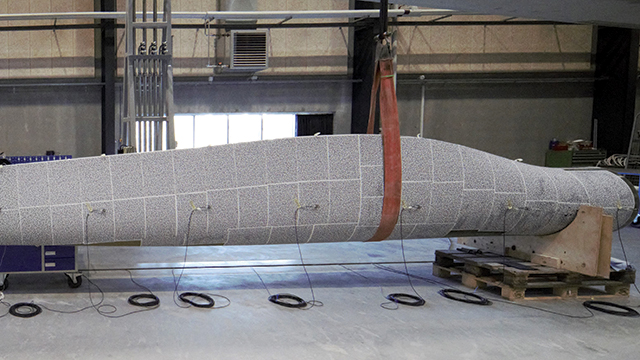
3. The xDT is adaptable!
Of course, we are not just talking about training a prediction model in the lab and then deploying it in the real world. To be useful, the executable digital twin must adapt and learn from its environment. According to McGann, that’s not a problem; it’s one of its strengths.
“We can augment the xDT with new data using Kalman filters, where we make it smart,” says McGann. “So, the xDT updates itself. What happens is you get data coming in, and the model says, ‘Oh, this is new data, I don’t recognise it!” so it correlates the known inputs with the known outputs, and the model automatically adapts. It says, ‘I’m going to match whatever you’re telling me is the input.’ And it gives you really nice results.”
“The question is do I need a different digital twin for each turbine I develop?” asks McGann. “We’re increasingly finding that the xDT is so adaptable you can often deploy the same xDT on a different wind turbine, and the model just updates itself. We’re even building a small demo version using the same xDT so potential customers can play with it themselves.”
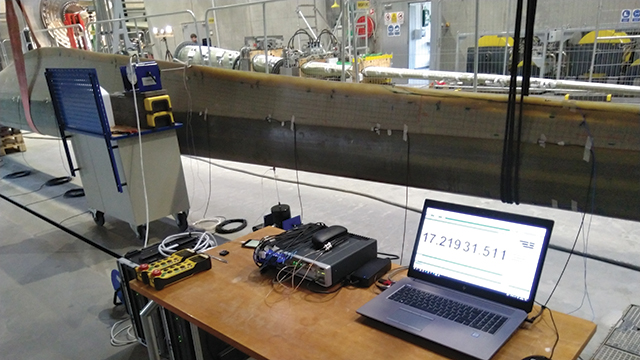
4. The xDT is available NOW!
There has been a lot of talk about digital twins in the last few years, but there are relatively few real-life examples of them. I ask Ian if the xDT is available today, or is it just another digital pipedream?
“I think the difference is if somebody said to me, ‘I want to create that flexible Digital Twin that you’re talking about,’ 10 years ago, we could have done it. And it would’ve been a great services project, and it would’ve been a couple of million dollars, and it would’ve been very fixed to that design,” explains McGann.
“So, what we’ve done now is that we’ve created the software behind it to make it easy to create, easy to validate,” and then the deployment and the management of those Digital Twins is now in place. And that wasn’t there before. So, customers would’ve said, ‘I can’t create this myself. I need an expert to help me. It’s literally a button you press!”
5. The xDT is secure and scalable!
So, having determined that xDTs are ready to be deployed in the real world, the next question is one of scalability and security. How do we cope with all the data transfer and processing if we have these arrays of wind turbines out at sea, each with a digital twin on board? How do we make sure that the data is secure?
“Well, why would you transfer the data?” he asks pointedly. “Why not just transfer the updated Digital Twin and the inputs? And that Digital Twin can be compressed, and it can be made so that it’s not hackable. It’s IP protected. So, the customer who creates that Digital Twin is creating their IP into that Digital Twin. And rather than transferring data that might not be secure, I now have a secured validated model, and I can just move the model around and then recreate all my data.”
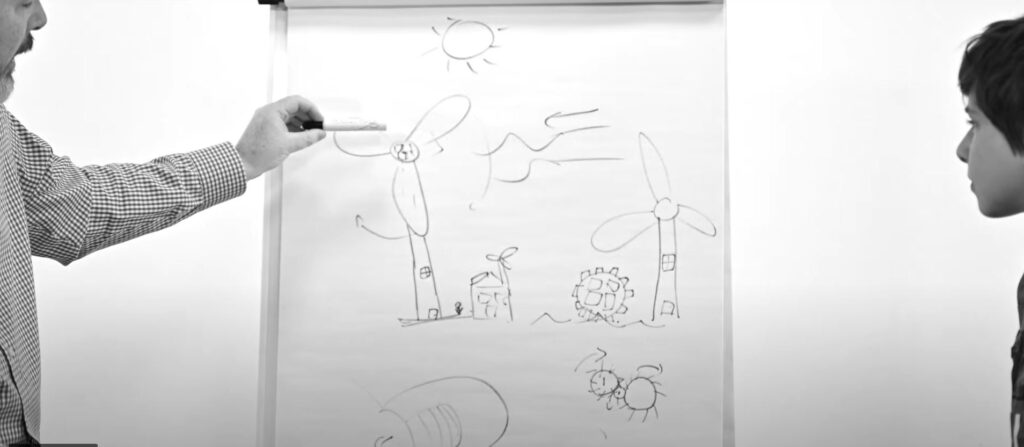