Blinded by the Obvious
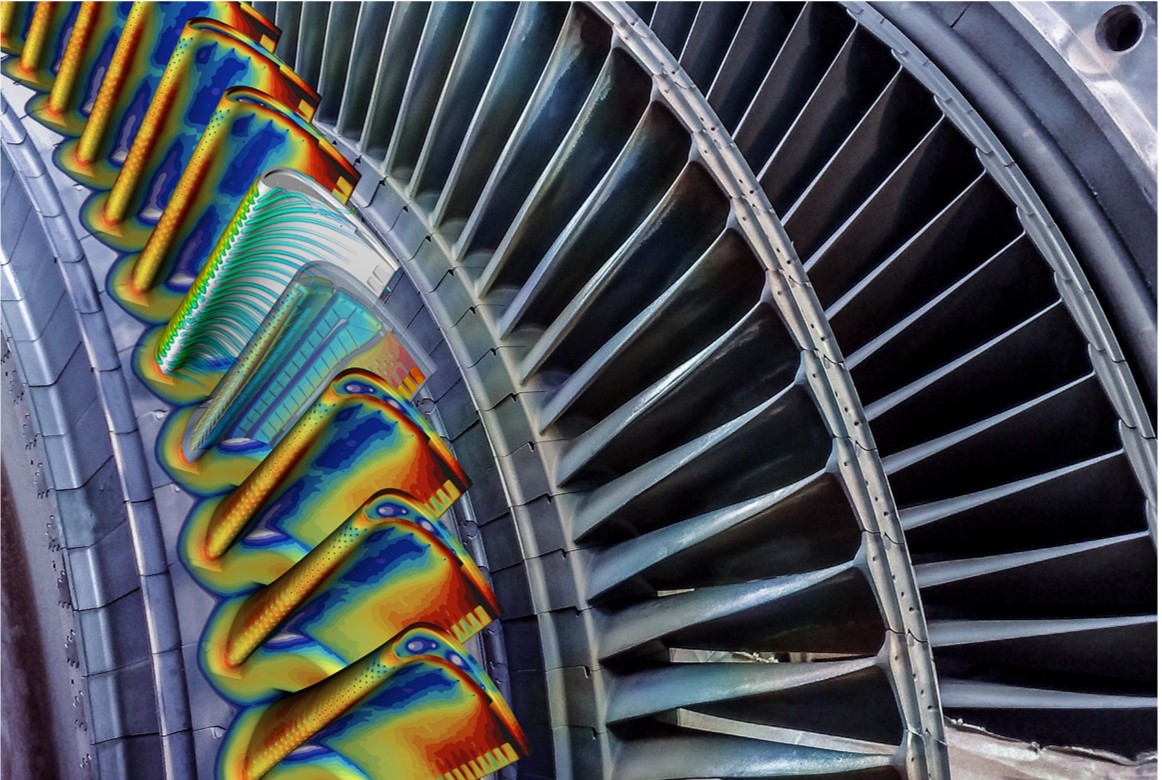
We can all be blinded by the obvious. The number of Dilbert cartoons on the topic is great evidence for how often it happens to all of us.
This has been on my mind lately because of a recent experience. About a year ago, my family finally had our kitchen renovated. When we first saw the house before buying it many years ago, I distinctly remember walking in and saying “well, we will need to renovate the kitchen.” But then time slips by and priorities shift. Soon the kitchen that so clearly needed renovating just became our kitchen. Our brains so quickly and easily plaster over the imperfections around us that those imperfections disappear from our perception.
On the last day in our old kitchen before renovations started, we took a picture of everyone crammed into the one corner that always seemed to be where everything in the kitchen was located. I found that picture the other day and was struck by what I saw. Was it really that small, that dingy? I found myself slightly embarrassed that we had happily hosted guests for so many years with a kitchen that looked like that!
This ability to tune things out that continually bombard us is often rather useful. Just think, that ability allowed me to happily live with a kitchen that desperately needed an update for many years. Imagine how draining it would be to wake up every day and have all the imperfections be as obvious as the day we first toured the home. However, there is also danger in not stopping to reevaluate. It’s possible to go on so long without reevaluation that our perception becomes entirely detached from reality.
As simulation engineers, we are especially at risk in this regard. One of the most important aspects of what we do is to determine what is important, what should be included into a model being developed and what can be neglected. Even worse, we must balance the amount of personal and computational effort required to capture a certain piece of physics. We may deem it important, but not so important that we are willing to invest in modeling the phenomenon.
One perfect example is the process that goes into designing and modeling a gas turbine such as those used for powering aircraft or generating electricity. These are massive machines that start with tens-of-rows of compressor blades working to create massive amounts of high-pressure air. That air is then mixed with fuel and ignited, producing gasses at even higher pressures and temperatures. All that work is done so that the high–pressure and temperature gasses can rotate turbine blades to extract mechanical energy. The gasses driving those turbine blades are so hot that cold air is pumped through complex internal passageways of the blades and out over their surface just to keep them from being damaged.
To simulate a system this complex, the level of physics appropriate for a model depends on how far along the design process we are. For example, when coming up with the right shape for those turbine blades so that they extract the most energy possible, those complex internal passages are usually not included. Conversely, when determining how to most efficiently cool those blades, it is necessary to include that complex internal detail. However, it’s not always so easy to decide what can safely be neglected.
Simcenter STAR-CCM+ is particularly strong for modeling complex cases. Modeling conjugate heat transfer, complex geometry, combustion chemistry and unsteady blade-passing effects are some of the common types of analysis done by our gas turbine simulation users. A streamlined workflow gives unmatched ability to accurately mesh the most complex geometry features while enabling the simulation of complex physics such as combustion, conjugate heat transfer and unsteady flows.
Multi-timescale simulation capabilities are now available in Simcenter STAR-CCM+, making it a good time to stop and re-evaluate the tradeoffs being made in our gas turbine simulations. Mixing plane interfaces allow us to model just a single blade passage in each row, which keeps the computational cost down. However, these heavily cooled blades produce distinct cold wakes that wash over the next row of blades downstream.
Ignoring the impact of these localized, unsteady wakes on blade temperature prediction is common. Until now, many have decided that capturing that effect would require too high a computational cost and so mixing planes have become the standard. At one point, the decision was made to ignore blade-passing effects and deal with the decreased accuracy of the simulation. Now it is an assumption made so often that most are blind to it, not recognizing that there are other options available.
Simcenter STAR-CCM+ has been a pioneer in developing harmonic balance simulation capabilities for gas turbine engine simulation for many years. The harmonic balance method allows the unsteady blade-passing effects in the fluid to be modeled at a much lower computational cost than traditional time-domain unsteady simulation. The method takes advantage of the periodic nature of the unsteadiness in the fluid to formulate a much more efficient simulation method.
With Simcenter STAR-CCM+ 2019.1, it is now possible to use the harmonic balance solver on the fluid side to capture the unsteady blade-passing effects and the steady solver on the solid side, all within the same simulation. This decoupling of the fluid and solid timescales makes efficient use of computational resources while more accurately representing the physical system. With this time-scale decoupling, it is no longer necessary to assume that the flow–field is steady and to neglect the impact of localized wakes when performing conjugate heat transfer simulations.
Simcenter STAR-CCM+ will continue to push the boundaries of what is possible with simulation, tackling the most complex cases, and timescale decoupling is evidence of that progress.
In addition to taking on the most complex gas turbine simulation needs, a new initiative has begun for gas turbine simulation with Simcenter STAR-CCM+ that is focused on improving gas turbine simulation for all levels of complexity. Each phase of the design and simulation process have unique challenges. Early in the cycle, flow and thermal predictions must be extremely fast and reliable and provide automatic reporting on the performance of a candidate blade. Later additional geometric and physics complexities are added, and more blade-rows of the machine are simulated simultaneously. Late in the cycle, very large simulations are performed once the design is nearing maturity. Many new capabilities are being brought into Simcenter STAR-CCM+ to help address the unique challenges of gas turbine simulation at each of these design phases. Interaction with design tools, specialized meshing and gas turbine specific post-processing are all on the way. Additionally, with unrivaled abilities to simulate the complex, it will become much easier to mature a given model with additional details as a design progresses.
It’s an exciting time for gas turbine simulation. With so many new capabilities, it may be time to reevaluate assumptions and look for blind spots.