Are you one of the 2 billion visitors of IKEA?
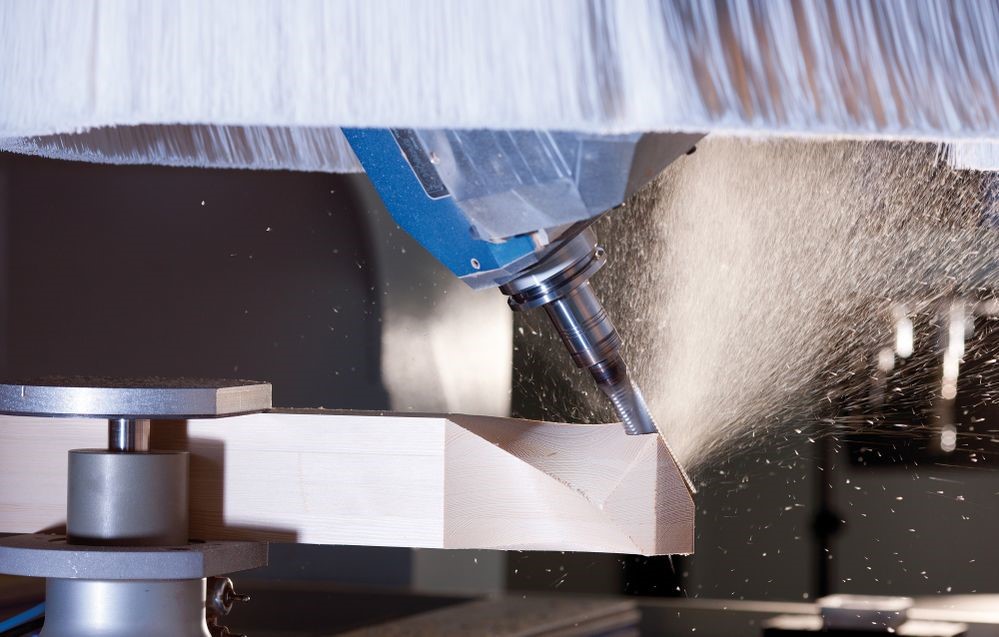
Let’s admit it: every single one of us has been in an IKEA store at least once, buying furniture and puzzling it all together at home (with varying success). With over 12,000 products in its catalogue and 2 billion yearly visitors, the company is responsible for approximately 1% of the worldwide wood consumption for commercial products. But did you ever wonder how all those panels and shelves are produced and how they are being cut, grinded, drilled, laminated…?
While everybody knows the brand name IKEA; who has ever heard about Homag? Better remember that name, because chances are high that your IKEA shelf, bed or wardrobe is manufactured on a Homag wood-working machine!

Having to produce those huge amounts of furniture, the speed of operation is crucial: the faster the Homag machine can produce those panels, the happier the manufacturing plant manager will be. But – like all other production machinery – simply increasing the operation speed to obtain higher productivity might generate unwanted vibrations. And these vibrations often lead to unexpected quality problems.
In the case of Homag machines, unwanted vibrations may cause bad surface finishings or poor lamination. For other industries, different quality problems can be related to unwanted vibrations:
- For paper, film and steel production: equal thickness
- For metal CNC machines: surface finishing
- For packaging and filling machines: correct filling of the packages
- For industrial printing machines: high-quality print thanks to correct alignment of the different color stages
- …
Understanding how the increased operating speeds affect the balance of internal vibrations, produced quality and energy consumption is a difficult exercise. The journey begins with identifying the guilty component but getting to the bottom of it is easier said than done. What exactly is it that affects the dynamics of the complex structure of a milling machine?
Siemens PLM Software developed and uses a particularly suited technique to answer such questions: the source transfer receiver methodology.
Source transfer receiver methodology explained
For industrial machinery and customers such as Homag, this was the best approach to find out how certain components transfer energy from source to receiver and negatively affect the final quality of the goods produced. Homag therefore chose to do impact testing and modal analysis with the Simcenter Testlab software and collect the necessary data with the Simcenter SCADAS Mobile hardware, both included in the Simcenter portfolio.
Are you interested in how we helped Homag producing even more of those IKEA furniture while maintaining the quality and shortening the loop between testing and simulation? Please read the full story here and remember their name next time you walk into the IKEA store.