How thermal testing and thermal characterization improve your electronic systems design
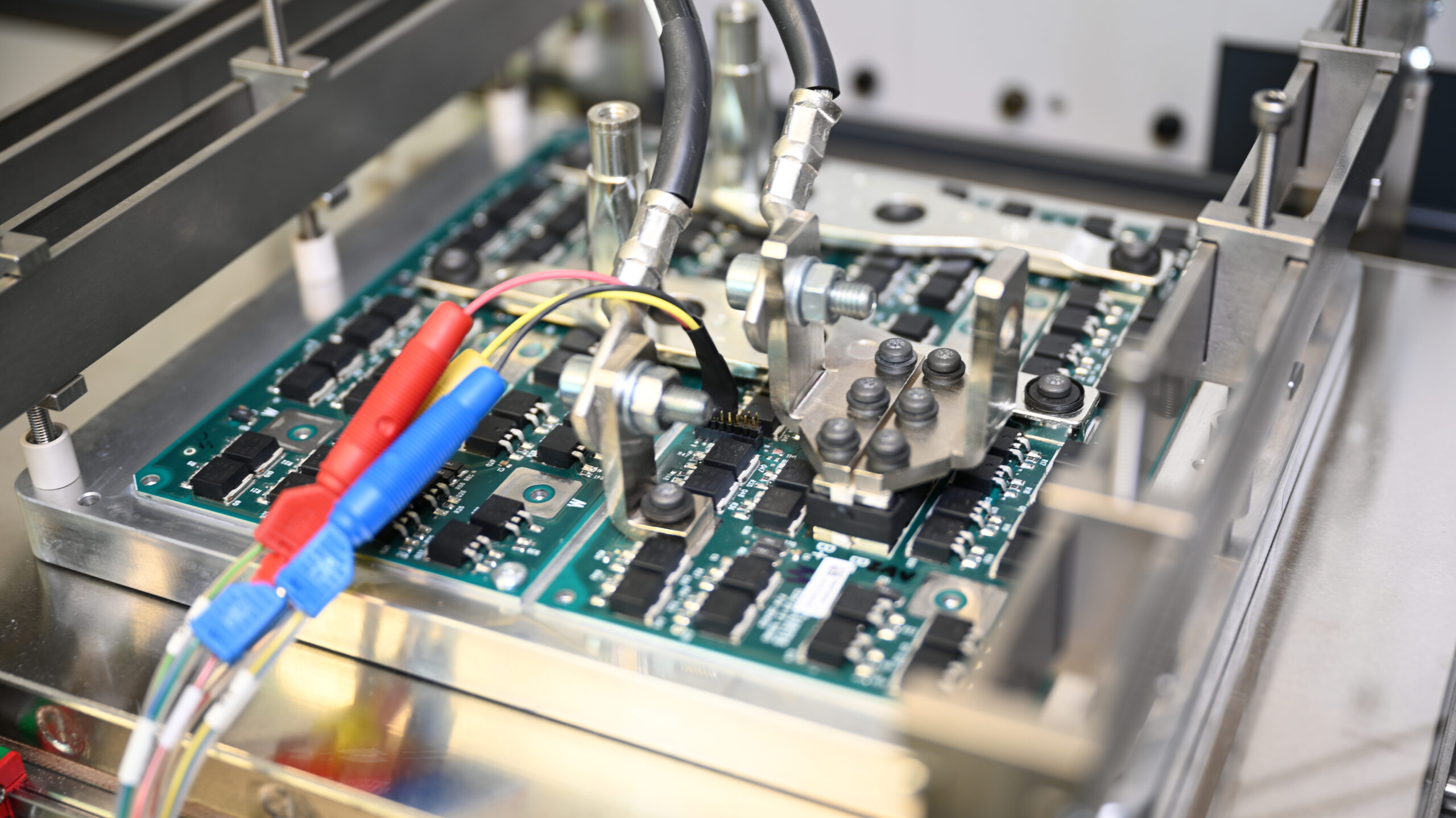
Why heat and electronics don’t mix
It is known that electronic components can fail due to high temperatures or frequent temperature variations. The majority of electronic failures can be attributed to excessive heat and it may not be clear where the heat is being generated within a package. Heat may be concentrated in certain hot spots which are not easy to locate so it is not enough to measure heat on the surface of a package, the designer needs a picture of the thermal behaviour within, to understand how heat travels through different structures and materials.
While increasingly powerful chips will generate more unwanted heat, products are also becoming smaller. Miniaturization is a trend where more components are concentrated in smaller designs so designers need to consider how heat will behave in more compact packages that could also include AI chips and advanced AI accelerators.
How do they know if a package will operate correctly and if it will pass certifications? And how will the latest AI accelerators and materials such as Gallium Nitride (GaN) and Silicon Carbide (SiC), which operate at higher power densities, affect thermal behaviour?
High powered ICs and power inverters
Machine learning and generative AI, IoT, transport, 5G and scientific research are all moving to higher processing power and it is critical to control heat in the new high powered products. This means designers working in these industries will want to understand thermal behaviour better. Then they can address cooling in their designs and ensure that their products are not impacted by thermal fatigue.
For example, in self-driving cars the CPUs and graphic processing units (GPUs) will process data from signs and sensors while simultaneously reading the position of other vehicles to steer a vehicle. Additionally developing the inverter of an electric car requires deep understanding of its thermal behavior as the power density increases.
Thermal characterization provides answers
Adopting a thermal testing strategy can play a crucial role in measuring the thermal metrics and performance of electronic components under static and dynamic conditions. This is also vital for creating accurate thermal simulation models at early stages of the design cycle.
Thermal characterization provides the key to perfecting a design where heat is dissipated successfully. It can also generate the metrics required for datasheets and certain industry certifications such as the thermal test data for AQG 324 (Automotive Qualification Guideline) and the specific junction-to-pin (RthJP) or junction-to-ambient (RthJA) values for the JEDEC-51 standards for semiconductor devices. With more accurate thermal data, it becomes easier to gain certifications and create devices that will perform correctly through all stages of their product life cycle.
Using thermal characterization in the electronic design cycle
The two examples below illustrate that thermal testing delivers more accurate thermal simulation models, and it can bring excellent business results in terms of a faster design cycle, enhanced product reliability and lower design and manufacturing costs.
Denso supplies parts for electric and hybrid vehicles. They used an integrated simulation and test process to reduce long lead times in their product design time. This resulted in a 50% reduction in both the duration and costs associated with thermal design.
Nari Technology used Simcenter solutions to build a comprehensive digital twin to optimize the tooling, fixtures and other components in their in-house product testing. They improved their heat dissipation capacity by 30%, reduced test costs by around 50% and made time savings of 80% in the design workflow.
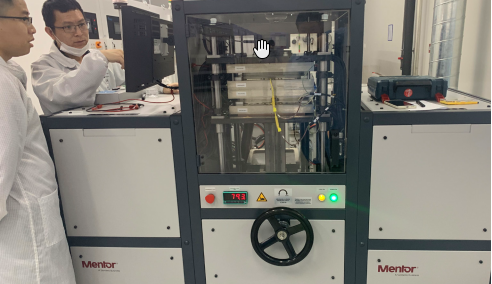
Both companies chose to use Simcenter Simcenter MicredTM hardware and software because it gave them the most effective way to integrate thermal testing and thermal characterization into their automated CAD and CAE workflows.
Integrated test and simulation enables designers to build accurate thermal models so that they can create products with whole-life reliability, from the early design stage of a product to manufacture and support. It can bring valuable commercial outcomes in terms of easier QA testing, benchmarking against competitors, generating test data for documentation and ensuring compliance with warranty terms.
Learn more about Simcenter thermal testing solutions read our solution guide: Using Simcenter to test the thermal performance of electronics
Read this story on how simulation-based testing enabled Nari Technology to realize time savings of 80%.