Process automation: Streamlining simulation workflows
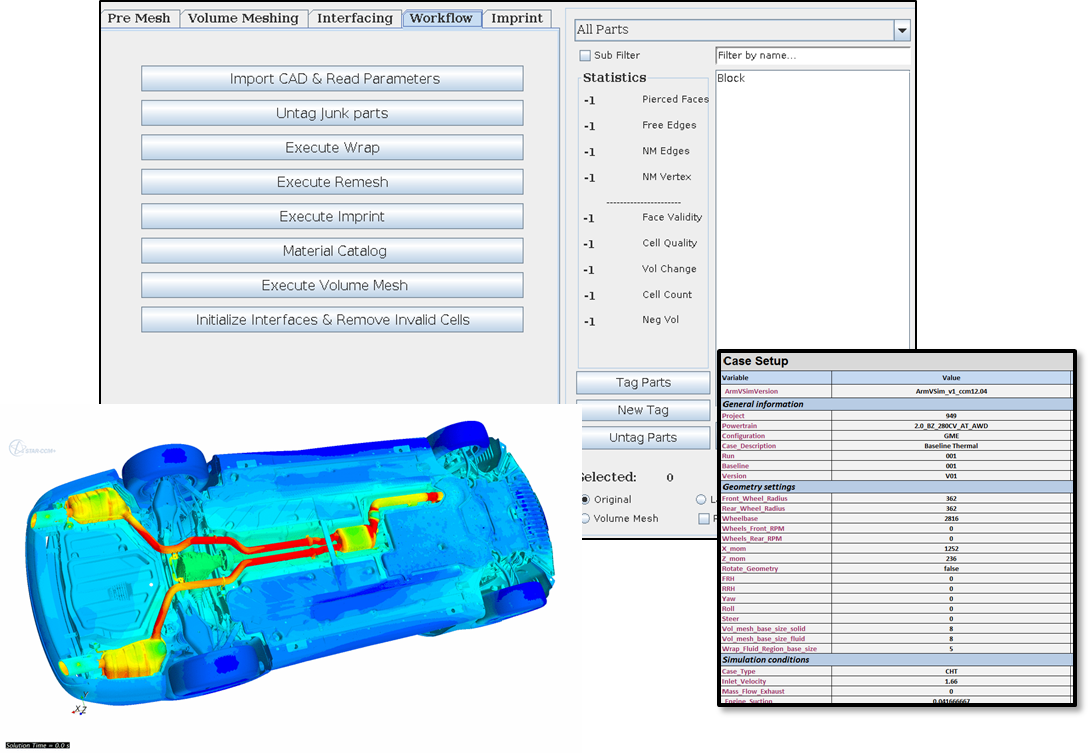
This process automation article is based on an interview with Mark Farrall, Business Engagement Manager for Simcenter Engineering at Siemens Digital Industries Software.
Companies are constantly trying to increase productivity and reduce costs. Before industrialization, a single person would develop and assemble all the components of a given product.
The first step towards a more efficient process was the invention of the production line, where a product is put together in steps and every person is responsible for a single job that they continuously repeat. One of the best-known examples of this was Henry Ford’s moving assembly line for cars in 1913. This new process reduced the time to build a car from 12 hours to just 13 minutes.
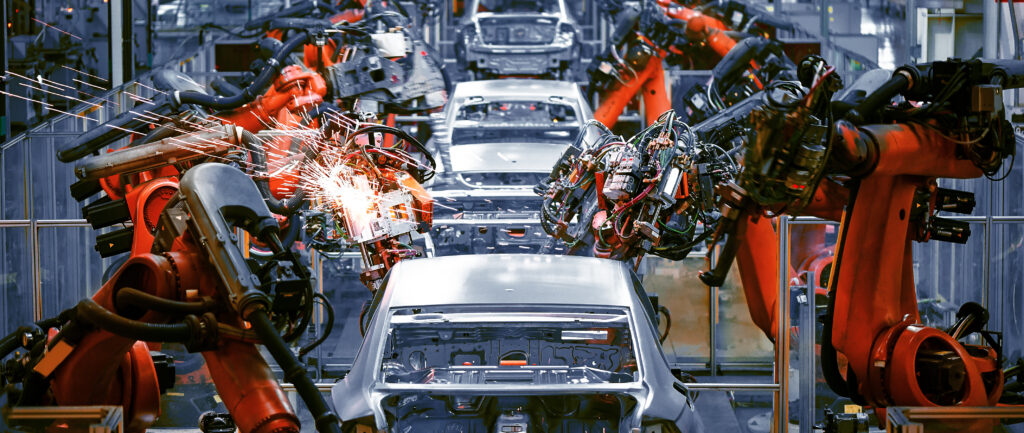
Recently the production line has evolved through the introduction of robots, eliminating human error and minimizing downtime.
Maximizing productivity
Engineers are expensive, so it is the goal of most companies to maximize their productivity. This can be achieved by eliminating tasks that take time, but do not bring high value to the company. In the simulation world, this means minimizing the amount of time spent on pre- and post-processing, such as CAD preparation, mesh generation, and simulation setup.
If an engineer is required to perform a particular analysis several times a week, month, or year, the engineer’s focus should be on the results and their interpretation rather than on time-consuming and repetitive tasks. This allows problems with a simulation model to be identified and resolved before the product goes to market.
In order to achieve this efficiency, companies should take advantage of customized, batch, or GUI-driven automated workflows. To illustrate the return on investment of these tools, let’s look at two examples.
Example one: Process automation in the automotive industry
Consider the automotive sector, where the use of simulation techniques is mature. Thermal challenges with the powertrain and in the integration of the vehicle’s other components are common. It is necessary to analyze these challenges in order to define adequate heat protection. In the early days, this would have involved analyzing only the air flowing through the underhood region, assessing the cooling package performance, and identifying hotspots. Over the years, with the increase in computational resources, OEMs continually want to increase the complexity level without adding to the project time.
Generating a Vehicle Thermal Management (VTM) model for a full vehicle consists of the following steps:
- Gather the latest 3D CAD, which could comprise up to 5,000+ parts, and organize it into the relevant groups
- Prepare the surfaces (both on the fluid and solid sides) for computational mesh generation
- Generate a suitable computational mesh, including the correct connections between the fluid and solid sides
- Assign the material properties, necessary flow, and thermal boundary conditions (there could be hundreds of potential boundaries)
The steps listed above can take up to two months with multiple engineers working in parallel to simply generate a computational model ready to run. Of course, that does not include the analysis and post-processing, which can take an additional few weeks, depending on the analysis.
Even if the baseline model exists, several updates of the model will be required in order to assess variations in the heat protection design or to evaluate steady and transient effects.
Like a physical production line, an automated solution (robot) to carry out many of the standard repetitive tasks can free up time for engineers to focus on where they really add value – in results analysis. With this solution, the engineer completes an Excel spreadsheet with required information for the analysis. This is read by the tool, which uses the data to gather the CAD and generate the appropriate computational model. The use of this automated workflow has proven to decrease the generation of a new model from around two months to approximately one week, a savings of over 80% in project/engineering time.
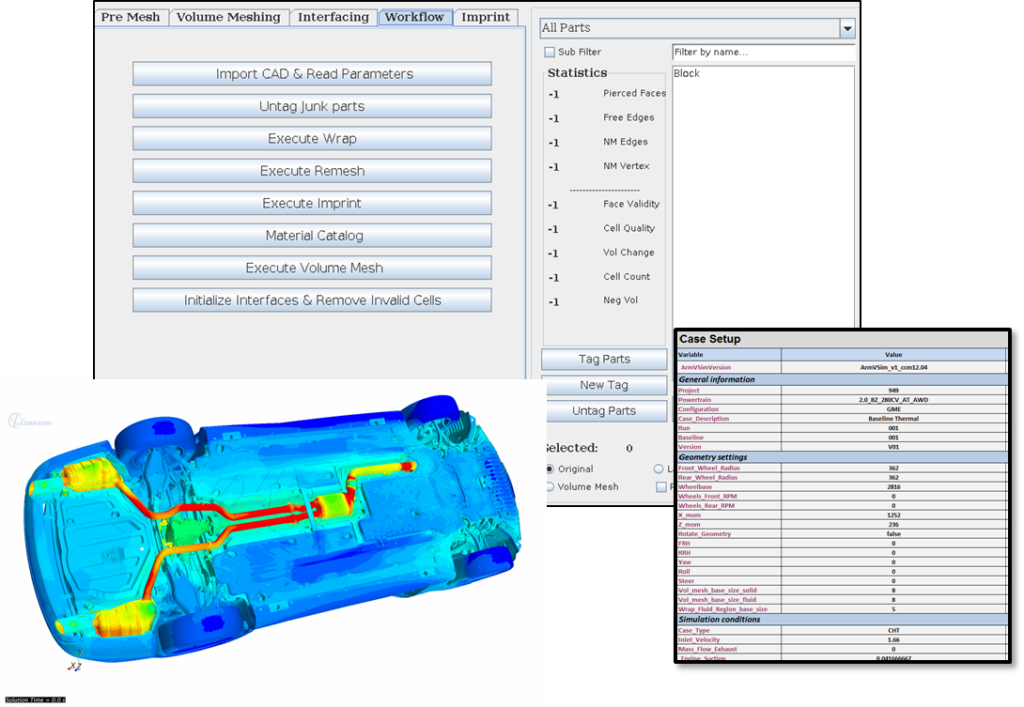
However, the work is not over once model generation is complete. Many companies still struggle with determining an efficient computational solution. Siemens has worked with customers to use loosely coupled simulations for the fluid and solid to take advantage of the differing thermal time scales that exist. Tools have been developed to efficiently manage these transient solutions, as well as the post-processing.
The result is a process that can be used by non-expert engineers to generate consistent results, eliminating manual input errors that occur when such a large number of boundaries and settings need to be dealt with.
Example two: Process automation in consumer products packaging
The second example we will discuss is the consumer product sector, where simulation is not mature and large internal simulation teams do not exist. However, the production processes in this industry consist of many complex fluid dynamic problems that would benefit greatly from automation to eliminate issues and increase overall efficiency.
One example relates to the pouring of liquid detergents and the amount of residue left on the bottle cap after use. While this may sound insignificant, a report by Allied Market Research titled “Liquid Detergent Market, by Nature, Application, Sales Channel, and End User: Global Opportunity Analysis and Industry Forecast, 2018 – 2025,” (https://www.alliedmarketresearch.com/press-release/liquid-detergent-market.html) found that the global liquid detergent market, valued at $27,405 million in 2017, is expected to reach $40 million by 2025. While sustainability and hygiene are the main drivers of this growth, customer experience also plays a significant role. If the consumer has a bad experience with a large amount of residue building up on the cap and going to waste, it may lead to the consumer choosing another brand. If this cycle continues, it could lead to a significant loss of market share and thus should be ignored at the manufacturer’s own risk.
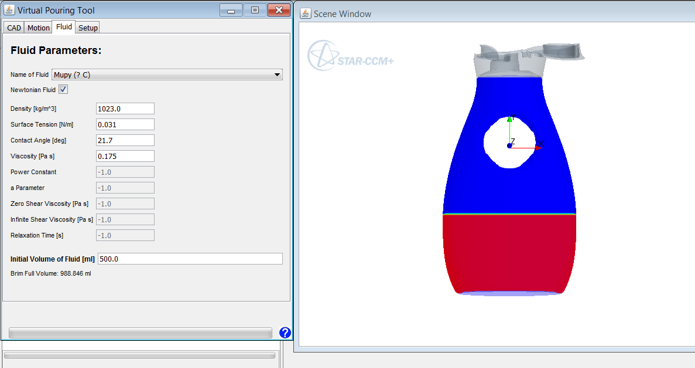
It is common to use rapid prototyping to generate physical test samples which can then be experimented with. The testing can range from subjective feedback by volunteers using the pack of several days or to a more controlled experiment. Either way, there are limitless variations in the way people use different packs. Thus, the first step in resolving residue issues is to define a consistent, repeatable test. Once this is complete, manufacturers need a quantitative way of measuring the amount of residue and its footprint in the bottle cap to compare designs, which is not done easily or accurately with experiments.
Like the automotive industry, simulation can provide the answer to this challenge. A virtual test rig can be generated that allows the definition of the 3D CAD, pack fill level, liquid properties, and pouring dynamics. This provides a robust, repeatable way to analyze different pack designs and the resulting residue in the cap. Many designs can then be automatically compared in parallel within a few days, removing much of the time to generate and test the prototypes. There are additional savings in the material used to generate the test pieces, product wasted during physical tests, and the cost associated with late tooling changes when problems are identified late into the project.
Companies often see the benefit of this approach but believe that they do not have the engineers and skill sets required to generate and carry out the simulations. I would challenge this belief. By applying the automation techniques discussed, the simulation and best practices can in fact be enclosed in a “black box” with a simple user interface that shows only those parameters that the engineers are accustomed to, such as fill level, liquid properties, etc. The result is a tool that can be used by non-experienced simulation engineers, opening the possibility to explore and eliminate bad customer experiences while decreasing the time to market for a given product.
A prime example of this technology being adopted is at Unilever. In this example, the use of an automated virtual test rig and parallel high performance computing resulted in development time being reduced from 20 weeks to just two weeks.
To learn how Simcenter Engineering and Consulting Services can help you develop automated processes like the ones discussed in this blog, email us at engineeringservices.sisw@siemens.com.